Technical Liaison Manager
- FMA
- The Fabricator
- FABTECH
- Canadian Metalworking
Categories
- Additive Manufacturing
- Aluminum Welding
- Arc Welding
- Assembly and Joining
- Automation and Robotics
- Bending and Forming
- Consumables
- Cutting and Weld Prep
- Electric Vehicles
- En Español
- Finishing
- Hydroforming
- Laser Cutting
- Laser Welding
- Machining
- Manufacturing Software
- Materials Handling
- Metals/Materials
- Oxyfuel Cutting
- Plasma Cutting
- Power Tools
- Punching and Other Holemaking
- Roll Forming
- Safety
- Sawing
- Shearing
- Shop Management
- Testing and Measuring
- Tube and Pipe Fabrication
- Tube and Pipe Production
- Waterjet Cutting
Industry Directory
Webcasts
Podcasts
FAB 40
Advertise
Subscribe
Account Login
Search
Selecting shielding gas for GMAW and FCAW
Why choosing appropriate shielding gas is critical for obtaining sound welds
- By David Meyer and Rob Koltz
- December 11, 2023
Q: In my welding shop, we use a variety of GMAW and FCAW wires to make fillet and butt welds in all positions. Can you help us select the appropriate shielding gas for these different wires and applications?
A: Selecting an appropriate shielding gas is critical for obtaining sound welds, but it can be a challenge. Always remember that some basic principles can make gas selection a little easier.
The first thing to consider in shielding gas selection is the material being welded. When welding aluminum, copper, and nickel-based alloys, use a fully inert gas such as argon (Ar), helium (He), or an argon/helium blend. When welding ferrous alloys, the gas will, in most cases, have an oxidizing component (oxygen or CO2), although straight argon is sometimes used for welding stainless steel.
With GMAW, the transfer mode used must be considered when welding ferrous alloys. To obtain spray transfer, the gas must contain less than 18% CO2 or 8% oxygen. However, combining the high arc energy of spray transfer with a highly oxidizing gas blend, such as 82% Ar/18% CO2 and 92% Ar/8% oxygen, causes a thick oxide layer to form on the weld bead. You can achieve better results with less oxidation by using gas blends that contain no more than 10% CO2 or 5% oxygen. For stainless steel, use a gas blend with minimal oxidizing components—no more than 3% oxygen or 3% CO2.
Pulsed welding is normally done with a gas that is used for spray welding.
Welding carbon and low-alloy steel using GMAW with short-circuiting transfer is normally done with either 100% CO2 or 75% Ar/25% CO2. You also can use other Ar/CO2 blends that contain more than 18% CO2 in some applications. When welding low-alloy steels that require oxidization to be kept to a minimum, use a He/Ar/CO2 tri-mix that contains less than 5% CO2. This type of tri-mix also is used when welding stainless steel with short-circuiting transfer.
Another thing to consider is the cleanliness of the material. If there is heavy mill scale or rust, utilize a gas blend with more CO2 to help clean the weld metal and minimize porosity. For materials that are relatively clean, a less-oxidizing gas can reduce spatter and fumes.
When welding with flux-cored wires, you should only use the shielding gas or gases recommended by the wire manufacturer. Using a flux-cored wire with a gas that is not recommended by the manufacturer can result in weld defects, including porosity and cracking, and also can result in a weld with inadequate mechanical properties.
subscribe now
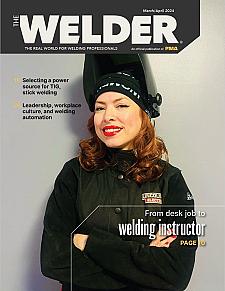
The Welder, formerly known as Practical Welding Today, is a showcase of the real people who make the products we use and work with every day. This magazine has served the welding community in North America well for more than 20 years.
start your free subscriptionAbout the Authors
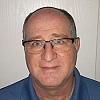
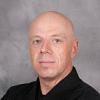
Rob Koltz
Application Engineer
411 S. Ebenezer Rd.
Florence, 29501
636-485-2253
About the Publication
Related Companies
- Stay connected from anywhere
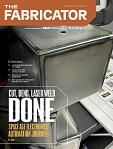
Easily access valuable industry resources now with full access to the digital edition of The Fabricator.
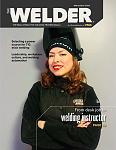
Easily access valuable industry resources now with full access to the digital edition of The Welder.
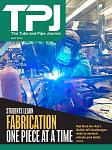
Easily access valuable industry resources now with full access to the digital edition of The Tube and Pipe Journal.
- Podcasting
- Podcast:
- The Fabricator Podcast
- Published:
- 04/16/2024
- Running Time:
- 63:29
In this episode of The Fabricator Podcast, Caleb Chamberlain, co-founder and CEO of OSH Cut, discusses his company’s...
- Trending Articles
Sheffield Forgemasters makes global leap in welding technology
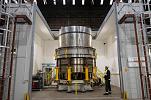
ESAB unveils Texas facility renovation
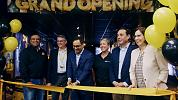
Engine-driven welding machines include integrated air compressors
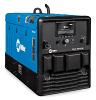
The impact of sine and square waves in aluminum AC welding, Part I
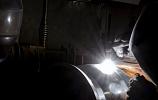
How welders can stay safe during grinding
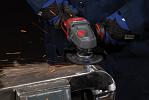
- Industry Events
16th Annual Safety Conference
- April 30 - May 1, 2024
- Elgin,
Pipe and Tube Conference
- May 21 - 22, 2024
- Omaha, NE
World-Class Roll Forming Workshop
- June 5 - 6, 2024
- Louisville, KY
Advanced Laser Application Workshop
- June 25 - 27, 2024
- Novi, MI