- FMA
- The Fabricator
- FABTECH
- Canadian Metalworking
Categories
- Additive Manufacturing
- Aluminum Welding
- Arc Welding
- Assembly and Joining
- Automation and Robotics
- Bending and Forming
- Consumables
- Cutting and Weld Prep
- Electric Vehicles
- En Español
- Finishing
- Hydroforming
- Laser Cutting
- Laser Welding
- Machining
- Manufacturing Software
- Materials Handling
- Metals/Materials
- Oxyfuel Cutting
- Plasma Cutting
- Power Tools
- Punching and Other Holemaking
- Roll Forming
- Safety
- Sawing
- Shearing
- Shop Management
- Testing and Measuring
- Tube and Pipe Fabrication
- Tube and Pipe Production
- Waterjet Cutting
Industry Directory
Webcasts
Podcasts
FAB 40
Advertise
Subscribe
Account Login
Search
Magnetohydrodynamic galvanizing modernizes corrosion prevention for steel applications
Process applies zinc in uniform, controlled thickness on tube, pipe IDs and ODs
- By Eric Lundin
- May 23, 2019
- Article
- Finishing
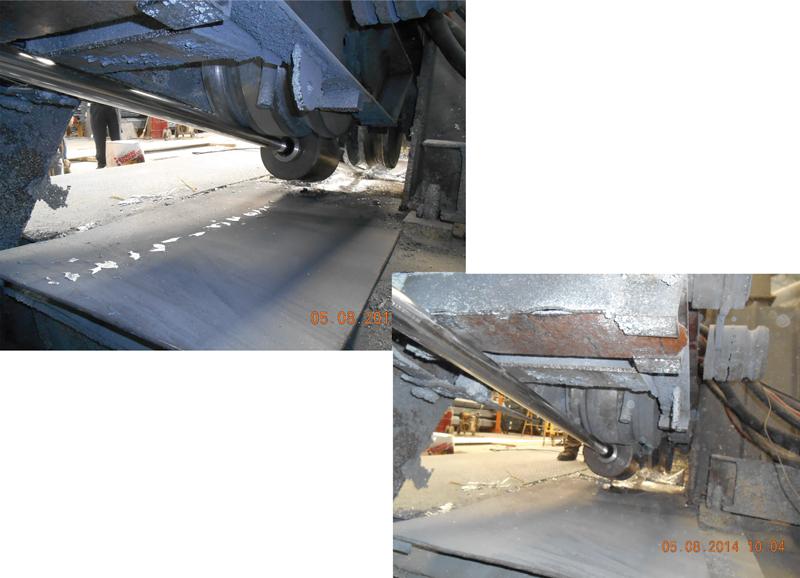
A magnetohydrodynamic galvanizing setup, when turned off, demonstrates a common problem in galvanizing: excess zinc runoff (top left). When the ID wiper is turned on, the system runs efficiently, eliminating excess zinc consumption (bottom right).
Once in a while, a researcher announces a strange discovery that gets the members of the scientific community all fired up while leaving the rest of us mildly befuddled. For example, the concept that time is relative seems a bit strange: A clock that moves faster than a reference clock runs slower than the reference clock. Another is the immense gravity of black holes, which is so great that nothing escapes, not even light. This isn’t easy to prove, in that a black hole isn’t much to look at, but the evidence that they exist has been piling up for decades.
A third concerns magnetism. While it’s usually considered an attractive force, magnetism repels some elements and compounds, including bismuth, copper, lead, silver, mercury, zinc, and water.
When they are announced, such discoveries generally are little more than scientific curiosities, and for most of us, that’s the end of it. It’s unlikely that any of us really care about the relativity of time or a gravitational field so strong it can’t be measured, but the third one, known as diamagnetism, has practical applications.
Suspension in a Coil
The key to applying a new or unusual concept in physics to solve a real-world problem is to find the right equipment to make it work. Diamagnetism isn’t a strong force, so it needs a powerful magnetic field to turn it into a useable force.
A specific electromagnet, the Bitter solenoid, is very powerful. Invented in 1933 by Francis Bitter, this type of solenoid creates extremely strong continuous magnetic fields. Because its shape is a coil, it exerts a magnetic force focused in the center of the windings. A diamagnetic item, such as a length of copper wire, placed in the center of an energized Bitter solenoid will be repulsed from all directions around the solenoid’s circumference, essentially trapping it.
A Bitter solenoid’s magnetic field is more than strong enough to capture and contain a quantity of water, holding it in suspension. The staff at the Nijmegen High Field Magnet Laboratory, Nijmegen, Netherlands, demonstrated this property—and their collective sense of humor—by levitating a frog in a Bitter solenoid. Frogs are mostly water, and water is diamagnetic, and one thing led to another.
For a practical application, the team at SunWyre Inc. created a system that captures and contains molten zinc in the same way. It went on to develop the necessary equipment and a process to apply the zinc to the surface of steel objects that pass through the suspended zinc. Galvanizing is nothing new, but this process, termed magnetohydrodynamic (MHD) galvanizing, provides an updated way to apply the zinc and control its thickness. MHD was developed nearly 30 years ago, so it’s not a new technology, but it is new to the tube and pipe industry.
“SunWyre developed the technology in 1996 for galvanizing rod and wire,” said President Victor Dorsten. “In 1995 I traveled to France to see MHD in action on rebar, and in 1996 the company developed a system for galvanizing wire rod.” The wire rod application wasn’t substantially different from the original application, but the wire rod system was developed to handle diameters from 7⁄32 to ½ inch, and the rebar system is or larger sizes..
“The system uncoils the wire rod, prepares the surface, galvanizes it, and recoils the wire rod so it’s ready for shipment or further processing,” he said.
The company installed systems throughout the Americas and in the Middle East, continuing to expand the technology’s worldwide presence.
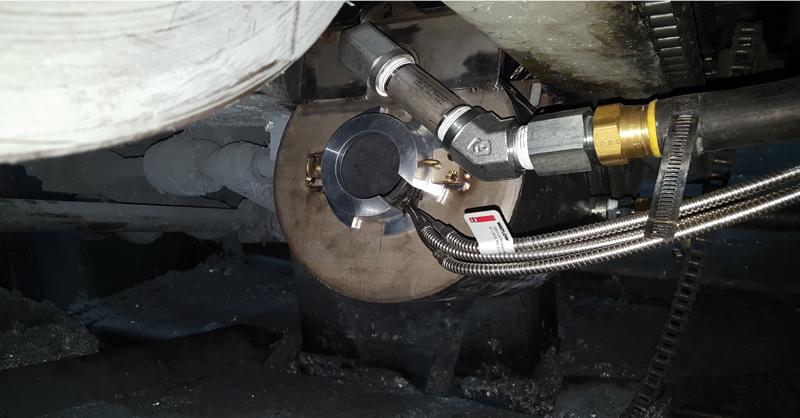
A Sweet coil, devised by SunWyre for the magnetohydrodynamic galvanizing process, effectively wipes excess zinc from the tube’s OD.
Moving on to Tube and Pipe Applications
Several years later a tube producer inquired about the technology.
“In 2007, a tube producer in Australia asked about continuous galvanizing for its products,” Dorsten said. “The application called for galvanizing round tube, then reshaping it to be rectangular or square.” SunWyre developed a system for this application, and after entering the tube market, it was just matter of time before finding other tube and pipe applications.
“A common galvanized product in the automotive industry is Galfan®,” Dorsten said. Developed in the 1980s and named for galvanizing with fantastic properties, the process uses about 95 percent zinc, 5 percent aluminum, and some rare-earth metals to provide a coating that is more durable and corrosion resistant than 100 percent zinc, according to industry literature. Applied at the same coating thickness as zinc, Galfan provides longer-lasting protection; alternatively, the Galfan thickness can be reduced to achieve protection similar to that of straight zinc.
“For many automotive applications, the coating thickness is 9 or 10 microns,” Dorsten said. “Some of the automotive suppliers wanted a thicker coating, and it took us about a year to perfect it, but we got it up to 24 microns in a consistent application,” he said. A thicker coating leads to a longer life cycle, so the new product has been nicknamed Super-Galfan, Dorsten said. Subsequent applications include structural steel, conduit, and rebar.
Rebar is galvanized in either of two ways. The most common involves low-carbon steel billets, 41⁄4 by 41⁄2 in., which are hot-rolled to reduce the size to 0.375 to 2 in. diameter. The hot-rolling processes also imparts the rib pattern. Sizes from 3⁄8 to ½ in. dia. can be galvanized by uncoiling, galvanizing, and recoiling it. Larger diameters are galvanized in straight lengths.
Less common is a process in which 3⁄8- to ½-in.-dia. wire rod made from low-carbon steel is galvanized coil-to-coil and subsequently cold-rolled through indenting rollers to create the rib pattern.
The equipment setup for MHD includes an induction heater to bring the workpiece up to the necessary temperature, 850 degrees F; a furnace equipped with a kettle that stores the zinc; and a Sweet coil, a device developed by SunWyre, which wipes the tube’s OD, keeping any excess galvanizing compound in the galvanizing chamber. Because induction heating is fast, bringing a common tube sizes up to the galvanizing temperature in just a half second or so, line speeds up to 300 feet per minute are possible.
While continuous processing lines exist, they’re rare in tube and pipe applications. For the most part, MHD lines for tubular products handle cut lengths.Process Efficiency
Beyond the ability to apply the corrosion- prevention compound in a consistent thickness to solids and hollows, MHD technology has four variables that allow the user to vary the application thickness, Dorsten said.
The first one is a matter of equipment setup: The size of the bore through which the tube or pipe passes. The others are operational parameters—the current supplied to the solenoid, the line speed, and the zinc temperature. To increase the coating thickness, the user can increase the chamber bore, decrease the current supplied to the solenoid, decrease the line speed, or decrease the zinc compound’s temperature.
While MHD does produce some waste, which accumulates in the form of dross, or mousse, Dorsten said that the process reduces the waste by nearly 90 percent.
“They have to skim the pots, but usually just once a shift rather than once per hour,” Dorsten said.
Also, while the process uses nitrogen, it consumes about 5 percent of the nitrogen that traditional galvanizing uses.
For automotive tube applications, which typically have diameters from 3⁄16 to 7⁄8 in. and wall thicknesses from 0.024 to 0.065 in., MHD can deposit 13.9 grams per square foot (GSF) of zinc onto the surface, or 150 grams per square meter (GSM), when running at 400 feet per minute (FPM). For structural tube, from 1 to 1.75 in. dia. and 0.039 to 0.118 in. wall thickness, the deposition rate is 28 GSF (305 GSM) for line speeds up to 328 FPM. Cut lengths of pipe, in diameters from ½ to 1½ in. and wall thicknesses from 0.098 to 0.127 in., the deposition rate is 28 GSF (305 GSM) for line speeds from 90 to 200 FPM.
The company’s current work concerns cut lengths in diameters from 2 to 6 in. and wall thicknesses from 0.135 to 0.252, and a deposition rate of 28 GSF (305 GSM). According to Dorsten, the target line speeds are 60 to 90 FPM.
SunWyre, www.sunwyre.com
About the Author
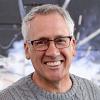
Eric Lundin
2135 Point Blvd
Elgin, IL 60123
815-227-8262
Eric Lundin worked on The Tube & Pipe Journal from 2000 to 2022.
About the Publication
Related Companies
subscribe now
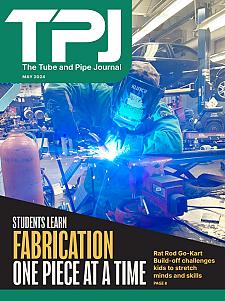
The Tube and Pipe Journal became the first magazine dedicated to serving the metal tube and pipe industry in 1990. Today, it remains the only North American publication devoted to this industry, and it has become the most trusted source of information for tube and pipe professionals.
start your free subscription- Stay connected from anywhere
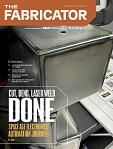
Easily access valuable industry resources now with full access to the digital edition of The Fabricator.
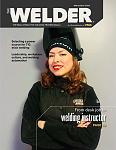
Easily access valuable industry resources now with full access to the digital edition of The Welder.
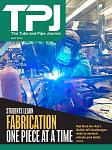
Easily access valuable industry resources now with full access to the digital edition of The Tube and Pipe Journal.
- Podcasting
- Podcast:
- The Fabricator Podcast
- Published:
- 04/30/2024
- Running Time:
- 53:00
Seth Feldman of Iowa-based Wertzbaugher Services joins The Fabricator Podcast to offer his take as a Gen Zer...
- Trending Articles
Zekelman Industries to invest $120 million in Arkansas expansion
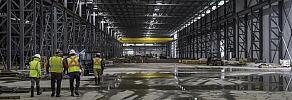
3D laser tube cutting system available in 3, 4, or 5 kW
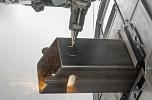
Corrosion-inhibiting coating can be peeled off after use
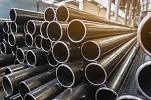
Brushless copper tubing cutter adjusts to ODs up to 2-1/8 in.
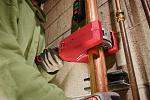
HGG Profiling Equipment names area sales manager
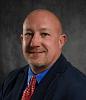
- Industry Events
Pipe and Tube Conference
- May 21 - 22, 2024
- Omaha, NE
World-Class Roll Forming Workshop
- June 5 - 6, 2024
- Louisville, KY
Advanced Laser Application Workshop
- June 25 - 27, 2024
- Novi, MI
Precision Press Brake Certificate Course
- July 31 - August 1, 2024
- Elgin,