Contributing Writer
- FMA
- The Fabricator
- FABTECH
- Canadian Metalworking
Categories
- Additive Manufacturing
- Aluminum Welding
- Arc Welding
- Assembly and Joining
- Automation and Robotics
- Bending and Forming
- Consumables
- Cutting and Weld Prep
- Electric Vehicles
- En Español
- Finishing
- Hydroforming
- Laser Cutting
- Laser Welding
- Machining
- Manufacturing Software
- Materials Handling
- Metals/Materials
- Oxyfuel Cutting
- Plasma Cutting
- Power Tools
- Punching and Other Holemaking
- Roll Forming
- Safety
- Sawing
- Shearing
- Shop Management
- Testing and Measuring
- Tube and Pipe Fabrication
- Tube and Pipe Production
- Waterjet Cutting
Industry Directory
Webcasts
Podcasts
FAB 40
Advertise
Subscribe
Account Login
Search
Hydroforming provides Rx for medical pumps
Fabriator adds economy to other benefits of titanium
- By T.R. Balmer
- January 10, 2002
- Article
- Hydroforming
![]() |
Figure 1: The pump housings Hudson produces for the three Arrow models are made of fully contoured and circular titanium to provide smooth, sloping edges between surfaces. |
Arrow International wanted strong housings for its implantable pumps. The answer had to be in titanium, with high quality that could be produced quickly.
"Titanium has proven to be the metal of choice for medical implantable devices," said Daniel Krebs, operations manager for Arrow International Inc., Walpole, Mass. "The material's strength, weight, and inertness to body fluids make it ideal for devices such as blood pumps and pacemakers — devices that will remain in people's bodies for the rest of their lives. However, titanium is difficult to work with when producing the intricate parts needed for these devices."
Arrow found its answer in a hydroformed product at Hudson Tool & Die Company Inc. The Ormond Beach, Fla.-based company produces closures and other precision parts made of titanium, stainless steel, and other exotic metals.
"Our initial contact with Hudson was twofold," Krebs said. "First, we needed a supplier who could produce the pump housings quickly to meet product introduction schedules. We also wanted to improve the housing economics while maintaining close tolerances and high quality."
Diagnosis: Use Hydroforming
Arrow International, through its Implantable Drug Delivery System Division, produces the model 3000 series constant-flow implantable infusion pumps. The pump infuses drugs and safe bolus-dose — a very large dose — injections into patients requiring chemotherapy for colorectal cancer that has spread to the liver, for chronic-pain management, and for the treatment of spasticity.
The pumps are available in three reservoir sizes (16 ml, 30 ml, and 50 ml) and have three flow ranges (low, medium, and high). Which pump is needed depends on each patient's needs, which include variables such as the type of medication and the frequency it's dispensed, the patient's size, and the time interval desired between refills.
The pumps have a fully contoured, circular titanium housing that provides smooth, sloping edges between surfaces (see Figure 1). The housing has a palpable, raised septum with a large target area that is easy to locate and access. The single septum access makes reservoir refill and bolus injections simply a matter of changing needles rather than searching for injection ports.
Jim Wagner, an engineer at Hudson, said, "When Arrow approached us to produce the part, we quickly realized that our hydroforming process was the ideal solution. We have had our hydroforming machine for nearly 10 years, and within the last two we have made some significant advances to improve the process.
"Hydroforming uses a punch and urethane bladder to form the shape. By changing the pressures on the punch, we change the shape and dimensions of the part. Also, hydroforming eliminates one side of the tooling, significantly reducing cost."
![]() |
Figure 2: The upper cover on the Arrow pumps has a palpable, raised silicone septum in the center that is 10.2 mm in diameter. |
Krebs said, "We were impressed with Hudson's dedicated plant-within-a-plant for medical parts. In the medical industry, we are always concerned with quality and contamination issues."
In its turn, Hudson had prepared to address these concerns.
"Several years ago we committed ourselves to producing medical parts by creating the dedicated plant," Wagner said. "Other improvements included a new $1.2 million toolroom and a $625,000 vacuum annealing furnace. To maintain the integrity of the furnace, we use it only for stainless steel and titanium parts.
"For the Arrow application, we developed special baskets to hold the parts during the heat-treating process to ensure that the parts were uniformly treated. Also, the baskets are used only for titanium parts, eliminating the possibility of contamination."
Pump Housing
The Arrow pump housings comprise two parts — the can, or bottom body, and the top, or upper cover. The can ranges from 61.2 mm to 86.4 mm in diameter and 19.7 mm to 27.4 mm in height, depending on pump capacity.
The can also has four small suture loops attached. The upper cover ranges in height from 12.3 mm to 10.0 mm; the smaller-diameter can is matched with a higher upper cover. A small recess along the top lip of the can ensures a tight seal with the upper cover. The upper cover has a palpable, raised silicone septum in the center that is 10.2 mm in diameter on all models (see Figure 2).
The raised septum design provides a large target area that simplifies the process for refilling the reservoir. For a bolus injection, a special needle is used that has a side hole to allow the medication to bypass the drug reservoir and flow into the patient's system (see Figure 3).
![]() |
Figure 3 |
Hydroforming
To create these minute mechanisms, Hudson replaced conventional matched die forming with a draw ring (blank holder) and a male punch hydroforming system that gives it the flexibility to produce either low-volume or irregularly contoured parts cost-effectively.
Hydroforming molds a metal blank into the desired shape using hydraulic pressure. Basic components include a lower die, guides, a rubber diaphragm, and an upper ram or punch.
The metal blank is placed in the lower die and held in place by the guides. The rubber diaphragm is placed on top of the blank, and the punch compresses the diaphragm against the metal blank. The metal blank flows into the lower die, forming the desired shape.
Altering hydraulic pressures during the hydroforming process allows Hudson to form extreme profiles that were not economically achievable with conventional forming methods. Hudson produces housings in wall thicknesses from 0.010 to 0.020 in. with 0.0001-in. tolerances, which result in size and weight reductions.
"Hydroforming allows us to produce highly precise parts typically needed for medical applications in a more economical and cleaner operation," Wagner said.
T.R. Balmer is a freelance writer based in Galloway, N.J. He can be reached at trbalmer@msn.com.
Hudson Medical Products (HMP), 1327 Highway U.S. 1, Ormond Beach, FL 32174, phone 904-672-2000, fax 904-672-0388, Web site www.hudsontool.com. HMP, a business unit of Hudson Tool & Die Company Inc., designs and constructs cases for implantable cardiac pacemakers and defibrillators.
About the Author
About the Publication
subscribe now
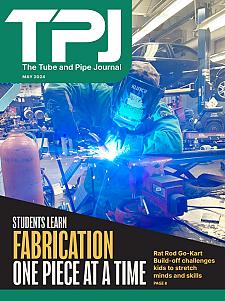
The Tube and Pipe Journal became the first magazine dedicated to serving the metal tube and pipe industry in 1990. Today, it remains the only North American publication devoted to this industry, and it has become the most trusted source of information for tube and pipe professionals.
start your free subscription- Stay connected from anywhere
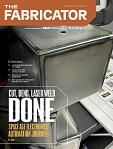
Easily access valuable industry resources now with full access to the digital edition of The Fabricator.
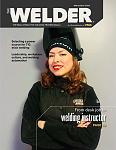
Easily access valuable industry resources now with full access to the digital edition of The Welder.
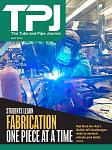
Easily access valuable industry resources now with full access to the digital edition of The Tube and Pipe Journal.
- Podcasting
- Podcast:
- The Fabricator Podcast
- Published:
- 04/30/2024
- Running Time:
- 53:00
Seth Feldman of Iowa-based Wertzbaugher Services joins The Fabricator Podcast to offer his take as a Gen Zer...
- Trending Articles
Team Industries names director of advanced technology and manufacturing
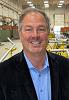
Orbital tube welding webinar to be held April 23
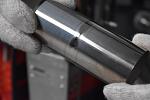
Zekelman Industries to invest $120 million in Arkansas expansion
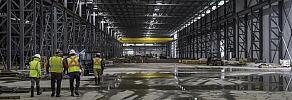
3D laser tube cutting system available in 3, 4, or 5 kW
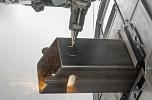
Corrosion-inhibiting coating can be peeled off after use
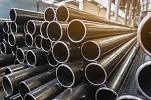
- Industry Events
16th Annual Safety Conference
- April 30 - May 1, 2024
- Elgin,
Pipe and Tube Conference
- May 21 - 22, 2024
- Omaha, NE
World-Class Roll Forming Workshop
- June 5 - 6, 2024
- Louisville, KY
Advanced Laser Application Workshop
- June 25 - 27, 2024
- Novi, MI