- FMA
- The Fabricator
- FABTECH
- Canadian Metalworking
Categories
- Additive Manufacturing
- Aluminum Welding
- Arc Welding
- Assembly and Joining
- Automation and Robotics
- Bending and Forming
- Consumables
- Cutting and Weld Prep
- Electric Vehicles
- En Español
- Finishing
- Hydroforming
- Laser Cutting
- Laser Welding
- Machining
- Manufacturing Software
- Materials Handling
- Metals/Materials
- Oxyfuel Cutting
- Plasma Cutting
- Power Tools
- Punching and Other Holemaking
- Roll Forming
- Safety
- Sawing
- Shearing
- Shop Management
- Testing and Measuring
- Tube and Pipe Fabrication
- Tube and Pipe Production
- Waterjet Cutting
Industry Directory
Webcasts
Podcasts
FAB 40
Advertise
Subscribe
Account Login
Search
Reaping rewards with precision laser cutting
Ag equipment manufacturer uses laser technology to reduce material handling, expand design options
- By Eric Lundin
- April 8, 2015
- Article
- Laser Cutting
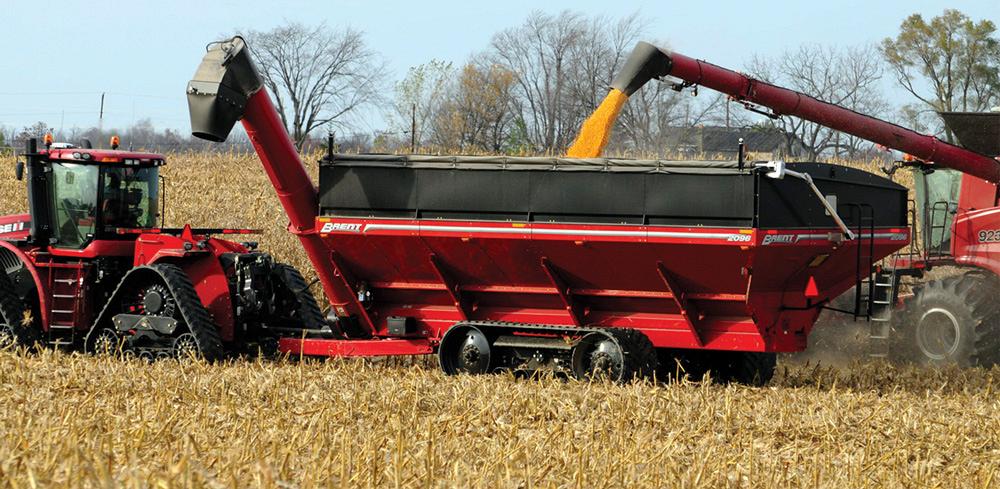
Avalanche model 2096, which has a 2,000-bushel capacity, is the largest grain cart in the Brent product line. Manufactured at Unverferth’s facility in Shell Rock, Iowa, it consists of large steel components that pose substantial manufacturing and material handling challenges. Laser cutting equipment for sheet and tube has improved the manufacturing processes, reducing material handling, and resulted in a better product.
Drive through the countryside of any Midwestern state in the middle of August and the scenery doesn’t change much. Mile after mile after mile, you’re likely to see nothing but fields of corn, soybeans, hay, and more corn. The Midwest doesn’t have the majestic views of the Rocky Mountains or the soothing calm of the oceans, and it certainly doesn’t inspire flocks of camera-toting tourists like Niagara Falls, the Grand Canyon, and a hundred other places throughout the U.S. The fields of the Midwest just aren’t much to look at.
Unless you’re looking at a balance sheet.
In 2013 Iowa alone produced $10 billion in corn—that’s “billion” with a “b”—and another $5 billion (the “b” word again) in soybeans. The state’s 200,000 dairy cattle added another $1 billion in milk production. Farmers’ fields don’t look too exciting until you start adding it all up.
A successful farm runs on good business sense as much as good weather, and these days farmers are more business-savvy than ever before. Every independent farmer does the things all entrepreneurs do: They hire people, buy raw materials, sell their products, pore over the books, use accumulated revenue to expand the operations, and, you guessed it, invest in new equipment.
The equipment is something to behold. Tractors have benefited from many of the technologies that have improved passenger cars over the years, and some tractors actually have more advanced functions than you can find in a modern luxury car. Enclosed cabs and climate control provide a lot of comfort, while GPS units, computers, and automatic steering systems eliminate overlapping passes in the field to prevent wasting fuel, seed, and fertilizer.
Likewise, the many implements farmers use—cultivators, seeders, fertilizer spreaders, harvesters, threshers, reapers, hay balers, combines, and so on—are improved more or less continuously by their manufacturers. The Brent product line, manufactured by Unverferth® Manufacturing Co., Shell Rock, Iowa, is a case in point. The products have been improving since former full-time farmer and part-time fabricator Mike Van Mill designed and built a high-capacity gravity wagon for a neighboring farmer in the early 1970s.
That grain cart led to another idea, a way of making a combine harvester more productive. The combine concept itself was a minor miracle when it was introduced in that this machine combined three grain-processing steps—harvesting, threshing, and winnowing—and carried them out as one continuous operation. The holdup was stopping to unload it. Van Mill came up with a double-auger grain cart to unload the combine while in motion, allowing it to work without interruption.
Now the operations manager of the company’s Shell Rock plant, Van Mill is part of a team that continues to design and manufacture safer, more productive implements for harvesting a variety of crops.
More Productivity in the Field and in the Shop
The Unverferth staff runs the Shell Rock facility the way a progressive farmer runs a farm, always on the lookout for a way to make things run a little more quickly, a little more smoothly, or a little more safely. For example, in 2004 the company invested in a laser to improve its sheet cutting capability. It was a sudden and substantial productivity improvement. The software imports part drawings quickly and provides nesting automatically; the laser cuts any shape imaginable without hard tooling; the machine stands in place of a shear, drill, punch press, and machining center; and the parts don’t need deburring, but a less intensive process, air sanding. Carrying out all of these operations on one machine eliminates most of the material handling, so the laser cuts out most of the non-value-added time and labor from the production process. In Van Mill’s eyes, these were the icing but not the cake.
“The real benefit to a sheet laser is the accuracy,” Van Mill said. Better accuracy at the laser means better part fit-up downstream, providing benefits in welding and the integrity of the finished component.
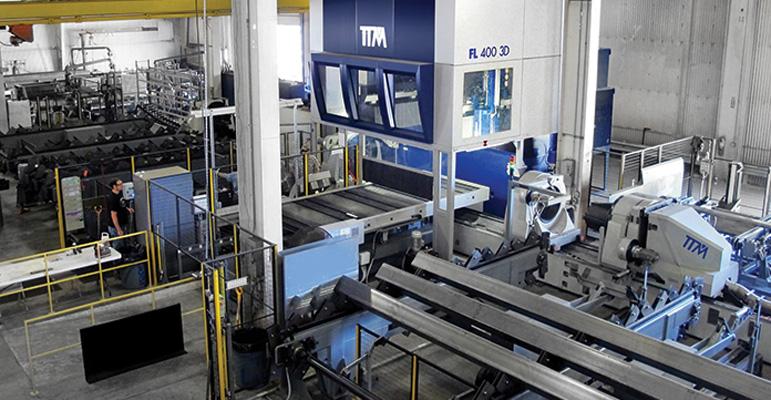
Figure 1
When Mike Van Mill and his team researched laser machines, they looked for one that could be customized to fit into an existing space
and work with the established part flow. TTM builds machines that can be fed from either side and provides customized infeed and
outfeed systems.
More recently Van Mill and his team gave some thought to a tube laser. They knew the company would derive many of the same benefits as when they invested in the sheet laser, but a tube is not a sheet, so some of the motivations were different. Storage, material handling, and fabricating considerations for sheet metal and tube are more different than they are alike. Tubes take up a lot more space, and they have different storage requirements because they don’t stack well.
“The main reason for a tube laser was to reduce work-in-process,” Van Mill said.
The larger the tube, the greater the amount of WIP, and the agriculture equipment industry uses really large tube. At Unverferth, a single stick of raw material can weigh 21⁄2 tons. The biggest pieces are 20-in.-OD round tubes, 5⁄8-in. wall thickness, and 40 ft. long. Of course, the company works with many other sizes and shapes of tube, but even a small tube in the ag industry—2 in. dia., 0.125-in. wall thickness, 40 ft. long—is substantial. Another factor in the amount of WIP is the nature of the business. The company relies very little on outside vendors, so it’s a high-mix shop.
“We make hundreds of parts,” Van Mill said.
Also, because its laser investment was not a greenfield project, the company needed a machine that would fit into the existing space and not disrupt the established part flow. To handle these challenges, the company chose an FL400 laser tube cutting machine, manufactured by TTM Laser. The machine handles most of the tube and pipe used at the Shell Rock facility, up to 16 in. OD in round and 12 in. OD in square, 5⁄8 in. wall thickness (at 12 in. OD, material that weighs 94 lbs. per ft.). TTM builds machines with the infeed on either the right or left side and customized material handling systems. The standard infeed and outfeed systems handle 46-ft. lengths, but these were customized to suit the company’s production, so the infeed side handles 41-ft. lengths and the outfeed handles 31-ft. lengths (see Figure 1). Another consideration was having a bundle loader and a chain loader on the machine. Conventional designs offer one or the other. Small-capacity machines usually load a bundle at a time, whereas machines that handle large, heavy workpieces usually load just one piece at a time. TTM offers both on one machine, so that when cutting small diameters, Unverferth doesn’t tie up a crane loading one small tube at a time.
Perhaps the most outstanding feature is the machine’s ability to multitask. It has four chucks, two for infeeding and two for outfeeding. When incoming material is on the infeeding chucks, the laser cuts features on the front half of the tube; the workpiece then gets transferred to the outfeeding chucks and the laser works on the back half of the tube. While this is going on, chucks 1 and 2 retrieve the next piece of material, which provides a big improvement in beam-on time.
It sounds complicated, but the software takes quite a bit of the burden off of the operators.
“There’s a learning curve, but it doesn’t take too long before it becomes second nature,” Van Mill said. “You could train anyone who runs a band saw to run a laser. The best combination of feed, speed, and wattage for a particular cut is a well-known science, so that’s built into the software. It automatically selects the best parameters for the job, and that goes a long way toward optimizing the laser’s efficiency,” he said.
The laser is a benefit when processing simple parts, but as the parts become more complex, the benefits are greater.
“Some parts are simple, but others have quite a few features,” he said. “The laser has taken many man-hours out of chamfering and other such features.
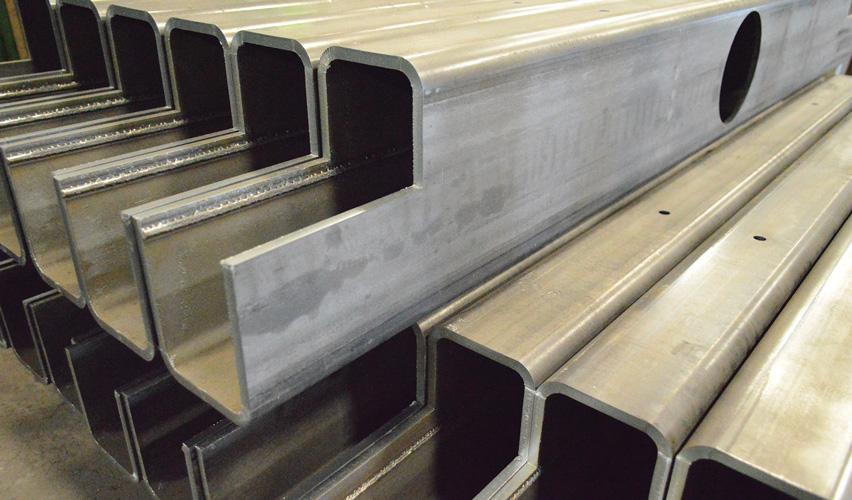
Figure 2
A stack of rectangular components hints at the laser’s versatility. Round holes of any size and end cuts don’t need hard tooling, and the
ability to do many types of features on one machine greatly reduces material handling time and labor.
“The laser also allows us to reduce fixturing,” Van Mill said. “We can use tabs and slots for parts that require welding, eliminating the fixture that would normally be used to hold the parts in position.”
However, some of the biggest benefits show up in the farmer’s field rather than on the factory floor. Because the laser doesn’t rely on hard tooling, the company’s engineers are more or less free to experiment with new features or entirely new designs. The engineering staff doesn’t incur the time or expense associated with designing, ordering, and waiting for tooling (see Figure 2).
“We’re freed up to do more complex designs,” Van Mill said. “We can do more robust designs and develop products that have fewer components.
“For example, when designing sound structures, it’s better to pass a cross member through the wall of a tube than weld it to the wall of the tube,” he said. It’s a stronger construction and it’s faster to produce because it eliminates welding.
“We end up making a more durable product,” he said.
About the Author
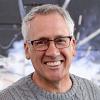
Eric Lundin
2135 Point Blvd
Elgin, IL 60123
815-227-8262
Eric Lundin worked on The Tube & Pipe Journal from 2000 to 2022.
About the Publication
subscribe now
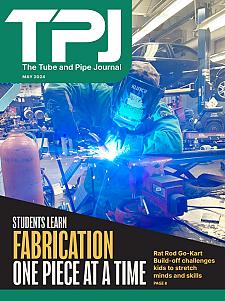
The Tube and Pipe Journal became the first magazine dedicated to serving the metal tube and pipe industry in 1990. Today, it remains the only North American publication devoted to this industry, and it has become the most trusted source of information for tube and pipe professionals.
start your free subscription- Stay connected from anywhere
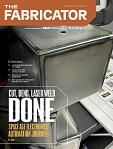
Easily access valuable industry resources now with full access to the digital edition of The Fabricator.
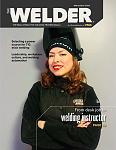
Easily access valuable industry resources now with full access to the digital edition of The Welder.
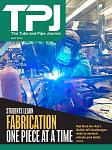
Easily access valuable industry resources now with full access to the digital edition of The Tube and Pipe Journal.
- Podcasting
- Podcast:
- The Fabricator Podcast
- Published:
- 04/30/2024
- Running Time:
- 53:00
Seth Feldman of Iowa-based Wertzbaugher Services joins The Fabricator Podcast to offer his take as a Gen Zer...
- Trending Articles
Zekelman Industries to invest $120 million in Arkansas expansion
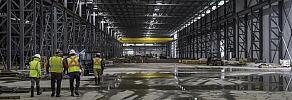
3D laser tube cutting system available in 3, 4, or 5 kW
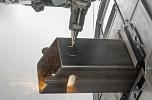
Corrosion-inhibiting coating can be peeled off after use
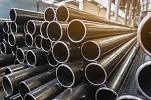
Brushless copper tubing cutter adjusts to ODs up to 2-1/8 in.
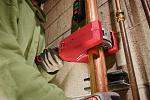
HGG Profiling Equipment names area sales manager
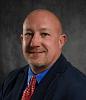
- Industry Events
Pipe and Tube Conference
- May 21 - 22, 2024
- Omaha, NE
World-Class Roll Forming Workshop
- June 5 - 6, 2024
- Louisville, KY
Advanced Laser Application Workshop
- June 25 - 27, 2024
- Novi, MI
Precision Press Brake Certificate Course
- July 31 - August 1, 2024
- Elgin,