- FMA
- The Fabricator
- FABTECH
- Canadian Metalworking
Categories
- Additive Manufacturing
- Aluminum Welding
- Arc Welding
- Assembly and Joining
- Automation and Robotics
- Bending and Forming
- Consumables
- Cutting and Weld Prep
- Electric Vehicles
- En Español
- Finishing
- Hydroforming
- Laser Cutting
- Laser Welding
- Machining
- Manufacturing Software
- Materials Handling
- Metals/Materials
- Oxyfuel Cutting
- Plasma Cutting
- Power Tools
- Punching and Other Holemaking
- Roll Forming
- Safety
- Sawing
- Shearing
- Shop Management
- Testing and Measuring
- Tube and Pipe Fabrication
- Tube and Pipe Production
- Waterjet Cutting
Industry Directory
Webcasts
Podcasts
FAB 40
Advertise
Subscribe
Account Login
Search
Giving the nod
Wearing a welding helmet doesnt have to be a pain in the neck
- By Tom Sommers
- September 11, 2007
- Article
- Safety
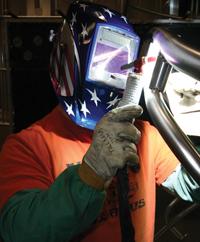
Even when not darkened, the lens of the helmet protects against ultraviolet and infrared light emissions.
Autodarkening helmets have high-speed phototransistors that detect the light from a welding arc, and then quickly darken the helmet lens to allow the welder to view the arc safely. Autodarkening lenses use liquid crystal display (LCD) technology, similar to that found in flat-panel televisions and cell phones. The time it takes the sensors to register the light from the arc to the time the lens darkens is between 0.05 and 0.28 millisecond (depending on the helmet), which is up to 2,500 times faster than it takes to blink your eye (the average blink lasts 100 to 150 milliseconds).
Additionally, multiple sensors located around the perimeter of the lens are important to ensuring protection in certain applications, such as low-amperage gas tungsten arc welding (GTAW) and out-of-position welding in which one sensor may be obstructed.
Vision Concerns
All autodarkening helmets must meet the safety protection specifications of the American National Standards Institute (ANSI) and its international equivalents. Even when not darkened, the windows provide protection from ultraviolet and infrared light emissions, the two most dangerous elements of a welding arc and the cause of arc flash. Even if a helmet fails to darken when the arc is struck, the operator is still protected from the harmful effects of the light.
Most helmets need to be turned on to operate and will turn themselves off after a certain period of inactivity. If a welder forgets to turn the helmet on, he will be protected from harmful spectrums of light, but the experience is still uncomfortable. Because of this, some manufacturers offer an auto-on feature with their helmets, in which the helmet is in a constant on-mode and darkens no matter how long it is idle.
However, not all autodarkening helmets are appropriate for all applications.
Fixed shade lenses, which darken to shade 10 in most cases, usually react anywhere from 1/2,000 second to 1/3,600 second and are not recommended for frequent tack welds, GTAW, and other industrial applications. For applications such as GTAW or those that require frequent tack welds, a lens that adjusts between shades 9 and 13 and darkens in the range of 1/10,000 second is recommended.
Repetitive Stress Injury
A welder who uses a traditional helmet keeps the helmet in an up position until he is ready to strike an arc. He then jerks his head down in a nodding motion to bring the helmet into position. This repeated motion may lead to long-term repetitive stress injury and lowered productivity.
Ed Forbes, vice president of operations for Engineering Metals & Composites Inc. (EM&C) in West Columbia, S.C., said his company has never even allowed a traditional welding helmet into its plant. EM&C, a designer and manufacturer of aluminum components for small boats and yachts, is known for its high-volume, high-productivity GTAW fabrication skills.
"We knew that repetitive stress injuries can and do occur as a result of using traditional welding helmets, so we standardized all 105 of our welders on autodarkening helmets right from the start," Forbes said.
"Because autodarkening helmets are all we use, we've been able to reduce our workers' compensation insurance rates and had fewer trips to the emergency room from arc-flashed eyes than companies that use traditional helmets."
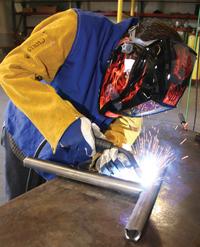
Nodding the helmet into ready position can actually cause the gun, torch, or electrode to shift out of position.
The weight of traditional helmets, up to 2 pounds in some cases, is also a source of neck strain. Autodarkening helmets can weigh up to 50 percent less and are increasingly designed with more ergonomic comfort in mind than previous helmet models.
Robert Lantrip, owner of Ourco Welding and Industrial Supplies, a Houston-area mobile welding distributor, occasionally performs his own fabrication work. After finishing the first of three fixtures he was welding, his autodarkening helmet was blown out of the bed of his delivery truck and he had to resort to using a traditional helmet.
"There was a lot of fitting and short 2- to 3-inch welds," Lantrip explained.
"I was able to weld 14 pieces an hour for the first job. On the second go-round, after my hood blew out the back and I had to use a regular hood, eight pieces an hour was the absolute best I could do, and that was pushing it."
Welding with these helmets can mean more time for welding. If a welder doesn't have to raise and lower his helmet when he's tack welding, he can save time going from piece to piece without moving the helmet at all.
The autodarkening helmet can reduce fatigue and frustration as well. A welder can get fatigued snapping his head to drop the hood down for each weld of the day. When using a traditional helmet, the welder positions his gun, torch, or electrode, and then nods the helmet into position before striking the arc. This can cause the gun, torch, or electrode to shift out of position, resulting in a dislocated start that requires reworking. Autodarkening helmets allow the welder to keep his head steady before striking the arc, greatly increasing the ability to achieve accurate starts.
"We're confident that our plant operates with much higher overall efficiency than it would if we were using traditional helmets," Forbes said.
More Than Just a Fashion statement
Not all autodarkening helmets are created equal. They don't all look the same, either. Graphics on an autodarkening helmet can allow a welder to express his personality, much like a custom paint job on a vehicle.
An often overlooked benefit of a helmet is that it's a way to express individuality, and many welders receive the helmet's safety and productivity benefits almost as an afterthought. In this way, the graphics on autodarkening helmets actually serve to increase both safety and productivity.
About the Author
Tom Sommers
1635 W. Spencer St. P.O. Box 1079
Appleton, WI 54912
800-426-4553
About the Publication
subscribe now
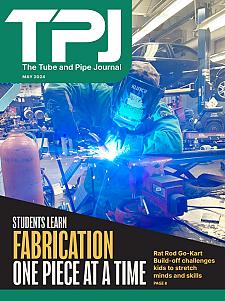
The Tube and Pipe Journal became the first magazine dedicated to serving the metal tube and pipe industry in 1990. Today, it remains the only North American publication devoted to this industry, and it has become the most trusted source of information for tube and pipe professionals.
start your free subscription- Stay connected from anywhere
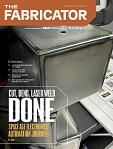
Easily access valuable industry resources now with full access to the digital edition of The Fabricator.
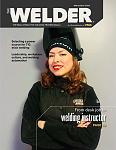
Easily access valuable industry resources now with full access to the digital edition of The Welder.
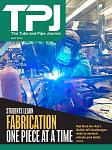
Easily access valuable industry resources now with full access to the digital edition of The Tube and Pipe Journal.
- Podcasting
- Podcast:
- The Fabricator Podcast
- Published:
- 04/30/2024
- Running Time:
- 53:00
Seth Feldman of Iowa-based Wertzbaugher Services joins The Fabricator Podcast to offer his take as a Gen Zer...
- Trending Articles
Zekelman Industries to invest $120 million in Arkansas expansion
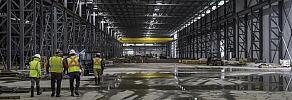
3D laser tube cutting system available in 3, 4, or 5 kW
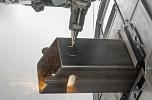
Corrosion-inhibiting coating can be peeled off after use
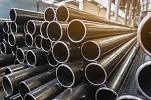
Brushless copper tubing cutter adjusts to ODs up to 2-1/8 in.
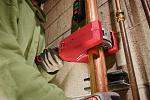
HGG Profiling Equipment names area sales manager
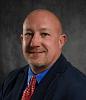
- Industry Events
Pipe and Tube Conference
- May 21 - 22, 2024
- Omaha, NE
World-Class Roll Forming Workshop
- June 5 - 6, 2024
- Louisville, KY
Advanced Laser Application Workshop
- June 25 - 27, 2024
- Novi, MI
Precision Press Brake Certificate Course
- July 31 - August 1, 2024
- Elgin,