Founder
- FMA
- The Fabricator
- FABTECH
- Canadian Metalworking
Categories
- Additive Manufacturing
- Aluminum Welding
- Arc Welding
- Assembly and Joining
- Automation and Robotics
- Bending and Forming
- Consumables
- Cutting and Weld Prep
- Electric Vehicles
- En Español
- Finishing
- Hydroforming
- Laser Cutting
- Laser Welding
- Machining
- Manufacturing Software
- Materials Handling
- Metals/Materials
- Oxyfuel Cutting
- Plasma Cutting
- Power Tools
- Punching and Other Holemaking
- Roll Forming
- Safety
- Sawing
- Shearing
- Shop Management
- Testing and Measuring
- Tube and Pipe Fabrication
- Tube and Pipe Production
- Waterjet Cutting
Industry Directory
Webcasts
Podcasts
FAB 40
Advertise
Subscribe
Account Login
Search
Safety tips learned the hard way from metal fabrication facility injury
Safety-oriented mindset can go a long way in preventing a mishap in any job shop
- By Jay Robinson
- August 20, 2019
- Article
- Safety
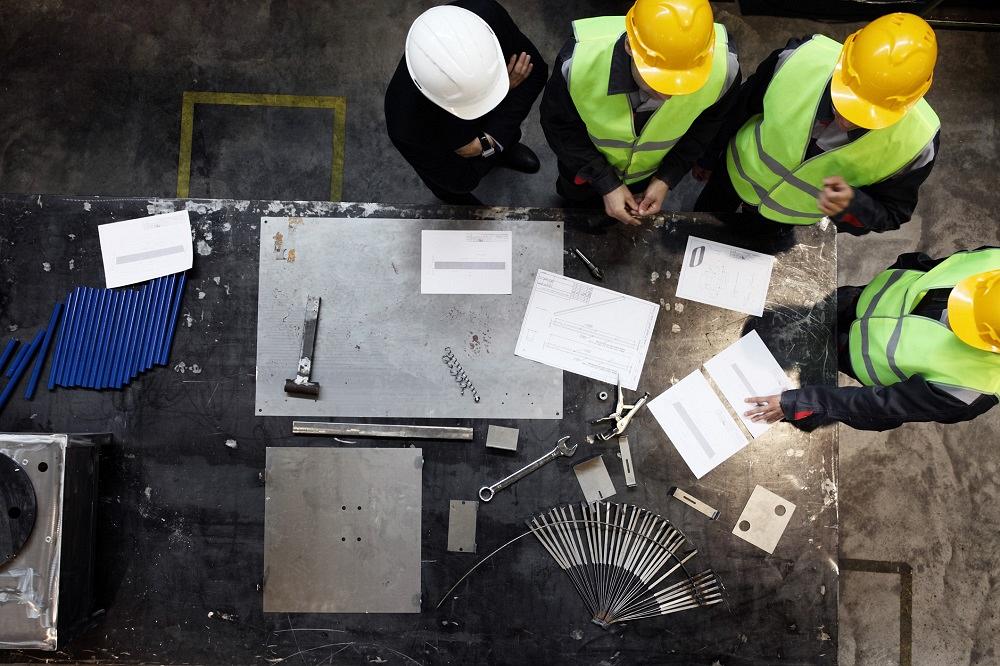
While working safely is ultimately the responsibility of the end user, fabricators don’t have to spend countless hours reading about the latest safety practices and devices. Companies that develop, produce, and market safety equipment usually have a deep reservoir of industry-specific safety expertise, so a safety audit from an equipment vendor can help to make the workplace safer while maintaining healthy production rates. Getty Images
Workplace safety is never to be taken lightly. Even a simple activity, such as climbing a ladder to change a light bulb, can go wrong. Whether it’s a matter of a specific task having specific safety protocols or a common task that just relies on common sense, a safety-oriented mindset can go a long way in preventing a mishap.
By the Numbers
As recorded and reported by the Occupational Safety and Health Administration (OSHA), industry has made substantial progress in reducing safety incidents over the last several decades. In 1994, private industry tallied 8.4 reportable incidents per 100 workers. It was higher in manufacturing, at 12.2, and higher still in fabricated metal products, at 16.4. In 2017, the most recent year for which data is available, the rates had fallen by more than half overall, to 3.1 incidents per 100 workers. The manufacturing sector made much more progress, cutting incident rates to about 25 percent of the numbers in 1994: the total was 3.5 per 100 workers in manufacturing and 4.1 per 100 in fabricated metal products.
Regrettably, things still go wrong, and when working around fabricating equipment, the outcome can be severe. An injury can result from contact with a hot surface, a laceration from a blade or other sharp surface, or entrapment between machine components driven by a large closing force.
The act of forming straight metal tubing into bent shapes requires huge amounts of force. For example, a pressure die powered by a 4-inch hydraulic cylinder and set to use 1,000 pounds per square inch (PSI) of hydraulic pressure will generate 12,560 lbs. of total clamping force against the tube. If any part of an equipment operator gets inside this clamping area, the machine will not even slow down.
An Injury Case Study
I recently received a phone call with terrible news. A fabrication shop employee was injured on the job. His hand had gotten caught in the clamps of one of the company’s tube benders, and the management team want to know if I could do some forensic work to help determine the cause.
Overall, everything was in order and up to date. The machine had several safety devices in place, including a properly working safety mat, emergency stops, overtravel devices, two-hand controls, and safety switches designed to stop the machine if an operator were to get trapped between the bend arm and body of the machine.
What was the failure that allowed the operator to be injured? In this instance there were several contributing factors. It’s hard to say if an injury would have occurred if the operator had violated just one or two safety guidelines, but in this case, a total of five factors came into play:
The part being run was very short: 20.9 in.
The carriage load position was set too far back for the part: 15 in.
The operator was standing in an area for loading that was not covered by the safety mat.
A footswitch was being used to start the cycle, freeing the operator’s hands.
The machine was set to start after a press of the footswitch.
Most CNC tubing benders allow the use of a footswitch so the operator can support a long tube if he is outside of the danger areas. In this case, he wasn’t supporting a long tube, but loading a short tube. Because the tube was so short, the operator was well within arm’s reach of the clamping areas.
Because the load position for the carriage position was so far back (15 in.) with a short tube, the operator had to stand close to the clamping area, or behind the bend head where there is no safety mat, and place his hands in the clamping area to load the part.
The part was set up to require only a single press of the footswitch. Immediately after the collet grasped the tube, the machine automatically moved to the first bending position and clamped the part.
The data logs from the machine control showed that the operator was not standing on the safety mat when he started the automatic cycle, and it was only after the clamps closed that the safety mat was engaged.
Prevention
What could have been done differently? The company had provided adequate safety devices to prevent injury, but the way the part was set up required operator actions that completely negated them.
Several steps can be taken to help to prevent this sort of accident:
Replace the safety mat with a floor scanner (or two). A properly installed, positioned, and programmed floor scanner can provide coverage over a larger area than most safety mats. Scanners also can be programmed to cover defined areas other than rectangles. In a case of bending tube, a scanner can cover the arc of a bend arm and run down the side of a machine. Although not impossible to defeat, it is much harder to work around the protective properties of a floor scanner than a safety mat. When programmed properly, the safety zone encompasses all hazardous areas.
Bolt the footswitch to the floor in a location that prevents the operator from using it while reaching into the clamping area. Doing this incorporates the footswitch into the safety regimen of the bender.
Planning a safety zone means replicating the machine’s location with as much integrity as possible. Because this machine would be placed near a column when installed at the customer’s location, this setup includes a column, at left. The blue tape on the floor represents the safety zone, which assists in programming the scanner.
Consider safety fencing with interlocked access doors for areas that cannot be adequately covered by a floor scanner. Safety fencing behind the bend head would have created a physical barrier, preventing the operator from being able to stand off of the mat to load the tube.
Provide operator training and set limits on how the machine can be set up for various parts and tube lengths.
Unfortunately, the person involved in the accident that prompted the phone call above lost three fingers. While that is bad enough, it could have been much worse. If you have tube benders, it’s imperative that you analyze your safety equipment and workplace practices, among both setup personnel and operators, to ensure that they understand the hazards and how to eliminate or avoid them.
Sending Workers Home Whole
Many companies make a sincere and wholehearted commitment to safety. Many of the largest firms make safety a priority over the day’s production, putting people before profit, and it’s fair to say that this shows up in the data. The improved injury rates over the last few decades speak for themselves. It’s hard to say how much of the improvement since 1994 is due to better safety devices and how much is due to better safety practices, but no matter—the reductions have been significant, and surely workplaces will continue to become safer still.
While working safely is ultimately the responsibility of the end user, fabricators don’t have to spend countless hours reading about the latest safety practices and devices. Companies that develop, produce, and market safety equipment usually have a deep reservoir of industry-specific safety expertise, so a safety audit from an equipment vendor can help to make the workplace safer while maintaining healthy production rates.
Jay Robinson is the founder of RbSA Industrial, 1401 McCalla Ave., Knoxville, TN 37915, 833-246-3747, info@rbsaindustrial.com rbsaindustrial.com.
About the Author
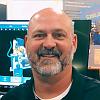
About the Publication
Related Companies
subscribe now
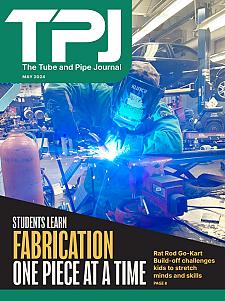
The Tube and Pipe Journal became the first magazine dedicated to serving the metal tube and pipe industry in 1990. Today, it remains the only North American publication devoted to this industry, and it has become the most trusted source of information for tube and pipe professionals.
start your free subscription- Stay connected from anywhere
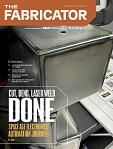
Easily access valuable industry resources now with full access to the digital edition of The Fabricator.
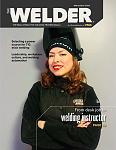
Easily access valuable industry resources now with full access to the digital edition of The Welder.
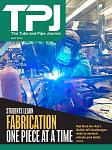
Easily access valuable industry resources now with full access to the digital edition of The Tube and Pipe Journal.
- Podcasting
- Podcast:
- The Fabricator Podcast
- Published:
- 04/30/2024
- Running Time:
- 53:00
Seth Feldman of Iowa-based Wertzbaugher Services joins The Fabricator Podcast to offer his take as a Gen Zer...
- Trending Articles
Zekelman Industries to invest $120 million in Arkansas expansion
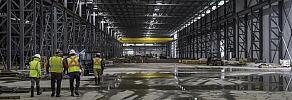
3D laser tube cutting system available in 3, 4, or 5 kW
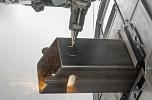
Corrosion-inhibiting coating can be peeled off after use
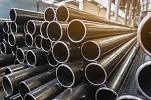
Brushless copper tubing cutter adjusts to ODs up to 2-1/8 in.
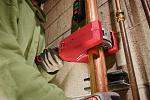
HGG Profiling Equipment names area sales manager
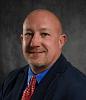
- Industry Events
Pipe and Tube Conference
- May 21 - 22, 2024
- Omaha, NE
World-Class Roll Forming Workshop
- June 5 - 6, 2024
- Louisville, KY
Advanced Laser Application Workshop
- June 25 - 27, 2024
- Novi, MI
Precision Press Brake Certificate Course
- July 31 - August 1, 2024
- Elgin,