Contributing Writer
- FMA
- The Fabricator
- FABTECH
- Canadian Metalworking
Categories
- Additive Manufacturing
- Aluminum Welding
- Arc Welding
- Assembly and Joining
- Automation and Robotics
- Bending and Forming
- Consumables
- Cutting and Weld Prep
- Electric Vehicles
- En Español
- Finishing
- Hydroforming
- Laser Cutting
- Laser Welding
- Machining
- Manufacturing Software
- Materials Handling
- Metals/Materials
- Oxyfuel Cutting
- Plasma Cutting
- Power Tools
- Punching and Other Holemaking
- Roll Forming
- Safety
- Sawing
- Shearing
- Shop Management
- Testing and Measuring
- Tube and Pipe Fabrication
- Tube and Pipe Production
- Waterjet Cutting
Industry Directory
Webcasts
Podcasts
FAB 40
Advertise
Subscribe
Account Login
Search
Pipelines to China
Tube China draws an international crowd
- By Scot Stevens
- December 7, 2004
- Article
- Shop Management
![]() |
Joe Shooshani was smoking a cigarette outside Hall 4 at the Shanghai New International Expo Center (SNIEC). He had traveled from Los Angeles where he owns Bobco Metals, a metals service center offering a range of services, including forming, bending, welding, and fabricating. Shooshani was in search of a small tube mill for his L.A. facility and he ended up halfway around the world.
"We are going to have to work a lot harder and a lot smarter," he mused, shaking his head and summing up what he'd seen in the aisles of the first Tube China 2004 — China International Tube & Pipe Trade Fair, held in September in Shanghai.
Coupled with wire China (devoted to wire and cable technologies), the two events comprised 683 exhibitors and occupied 280,000 square feet of exhibit space. The tube and pipe event comprised 177 exhibitors and covered 81,000 sq. ft. of space. Packed into that space was a tiny snapshot of the global impact of China's continuing industrialization. By the time it was over, 23,477 visitors from 70 countries had seen what Shooshani had seen. Many had come to the same conclusion about working harder and smarter.
China's emerging tube producers and equipment suppliers were well-represented, but exhibitors also came from Austria, France, Germany, Italy, North America, and the U.K. Many were following their customers into the Chinese market. Some were lured by the massive amount of tube- and pipe-related infrastructure that is springing up across China. The country's fledgling automotive industry, which has attracted significant investment from the world's biggest automakers, also was a top draw.
Many were taken aback by the international makeup of attendees and exhibitors.
![]() |
Fein is targeting pipeline construction, repair and maintenance, sewer construction, water treatment plants, and other infrastructure projects in China. This pipe milling machine for straight and profile cuts on pipes, tanks, and bins with diameters from 250 to 3,000 mm features pneumatic and three-phase motors and is available with two different feed and cutting speed rates. |
"How do I make this part?"
"Totally unexpected by us was the number of visitors from outside China and Asia," said Savio Dominici, managing director, Emmedi S.p.A.
"The number of international visitors is astounding," concurred Graham Wood, export sales director, AddisonMckee. "We have seen people from Iceland, Greece, Europe, Japan, the Philippines, Australia, the U.S.—all looking toward the same market, all coming to see what's going on in China. There are people coming to our booth with projects and drawings in hand, asking us, "How do I make this part?'"
Both attendees and exhibitors alike, however, noted a conspicuous shortage of Americans.
"There were not many people from our country," Shooshani said. "People in our industry missed a great opportunity to at least see what they are dealing with. We cannot put our heads in the sand and then ask what happened to our markets and our jobs. We should go and capture the market they have to offer. The Europeans have embraced this approach."
"Most of the big international players are here," observed Mick Nallen, president, Thermatool Corp. "Most stateside companies are not here, but they should be."
From Threat to Opportunity. Conventional wisdom regarding the manufacturing boom in China is evolving from threat-oriented characterizations to an acknowledgment of the opportunities presented, no matter how challenging those opportunities may be.
In the international tube and pipe markets, reality has sunk its teeth in. The U.S. and Europe are stagnant. The experience of one lawn mower producer in the southeastern U.S. symbolizes the changes transforming business. At one time it had a tube mill, bending technology, and a powder coating operation that produced finished lawn mower handles. Today bent and coated handles come from China.
Asia, on the other hand, is flourishing. In Tian Bao, the largest Thermatool welder ever built is about to enter operation in what is said to be the first 24-inch API pipe mill operating in China.
"And there are three more large welders on big pipe mills right behind it, being installed to support the oil and gas infrastructure that is being built across the country," said Nallen. "You have to be there."
![]() |
This four-axis CNC rotary head tube bender from Taiwanese manufacturer Ying Lin Machine Industrial Co. Ltd. (YLM) is being positioned for products such as exercise equipment, tubular furniture, exhaust pipe systems, and transportation-related applications. |
Nallen also cited strong potential for H beams to support the burgeoning construction market that has ignited a hotbed of activity in multifamily housing and condominium development.
"Currently we are not targeting the U.S. tube and pipe market," noted Heinz Kasparet, international sales manager, Linsinger Maschi-nenbau GmbH, an Austrian producer of tube cutoff, strip edge milling, and plate edge milling equipment. "There are few investments in
that market, no new mills being installed, and an aging installed base of equipment.
"We have been in China for 10 years, and it is our most important worldwide market at the moment. There are very high levels of investment in the Chinese tube industry, with companies investing in both new mills and replacement equipment," Kasparet said.
Modern Infrastructure, Rising Standards of Living. "Every city in China is building infrastructure," added Kenneth Ma of Luda Development, a Hong Kong supplier of flanges and fittings. He has visited many Chinese tube mills to buy the pipe necessary for the company's products.
"The standard of living is rising," Ma continued. "Real estate development is under way. People are buying cars and housing right now, in anticipation of continued future price increases. Every factory is operating at high utilization rates."
"Automotive here is clearly expanding exponentially, and the requirement for higher levels of technology is expanding along with it. That means our business is increasing here," said AddisonMckee's Wood. "By 2010 China is expected to overtake Japan in the volume of cars produced. Consequently, our activities must increase in this market. We see all our global partners steadily investing more and more in China. Where they go, we go."
According to Wood, the market is embracing the company's all-electric bending technology for automotive exhaust systems. "We've put three of these systems in the market in the last two years," he said. "The only reason the customers invested in them was to meet quality demands of the car manufacturers setting up in China. Ford and Volkswagen want the same quality in China as they have in the U.S. and Europe."
![]() |
Dongsheng, a manufacturer in China's Guangdong Province, produces 3,000 of these and similar units annually. According to the company, it is exporting few if any of its machines because of the strong demand in local markets. Dongsheng has a cooperative alliance with the Dutch saw blade manufacturer Kinkelder. |
Boiling Over
Production for tube bending supplier Schwarze-Robitec, as of late September 2004, was fully booked through May 2005, according to Sales Manager Erik de Wijs.
"In fact, because of the growth in China, and some in Russia, we have not had a problem getting through the market downturns in the U.S. and Europe," de Wijs said.
The company's main end-use market in China is the industrial boiler segment. "China needs a lot of power plants, a lot of tubes, and a lot of large industrial boilers," according to de Wijs. "We are also targeting the shipyard and automotive markets."
He sees a growing opportunity as hydroforming in automotive applications continues to spread throughout the world. "It requires more sophisticated bending technologies that can hold increasingly tighter tolerances," he explained. "It started in Europe, with BMW in 1991, followed by Volvo and Porsche. It then moved to the U.S. and Japan. We are now seeing it in places like Korea, where we have three fully automated lines that will be used in hydroforming applications involving engine cradles and rear suspension assemblies.
"These technologies will end up in the emerging automotive industries in both China and India," he predicted.
Mannesmann sold its first pipe production line in China 100 years ago. The company first entered the boiler segment 50 years ago.
"We have a lot of boiler expertise and rock-solid relationships here in China, reinforced by the presence of Valtimet [another subsidiary of Vallourec Group], which produces locally stainless and titanium welded tubes for condensers," said Dominique Richardot, director, sales and marketing, Energy Department, Vallourec & Mannesmann Tubes.
"China is importing 500,000 tons of tube and pipe per year," added Rainer Lenzen, director, sales and marketing, Industry Department.
"They are exporting line pipe and commodity grades. They import the niche products and grades, related to size and material composition."
The company is focused in China on the more sophisticated, specialized grades and alloys required by the boiler industry, where domestic producers in China have a way to go yet. "They have limited know-how and capability in these types of products," said Richardot.
"They will acquire the capacity and the know-how," he added. "It is only a question of time. If their consumption decreases, we could face stiffer competition because they have massive capacity, unless they close their older and obsolete tube mills. However, currently we are considering a project to manufacture in China some higher-grade, higher-quality tubes in order to better serve the needs of Chinese boiler companies."
Working Harder, Smarter
![]() |
This rotary ultrasonic wall thickness measurement system from Houston-based Tuboscope-Mill/NDT Systems identifies wall variations by utilizing ultrasonic sound waves coupled to the material surface with water. The machine rotates several ultrasonic inspection arrays around the outside surface of linearly conveyed tubes. |
As China's industrial base advances, the pace is breathtaking. Car dealerships, in short supply in the late 1990s, now dot the streets of Shanghai alongside McDonald's, Pizza Hut, and Kentucky Fried Chicken restaurants. Roadways are wallpapered with billboards advertising housing projects and luxury condominium developments. In the tube and pipe markets, international companies are up against domestic suppliers in a competition that intensifies daily.
"Chinese companies are now producing equipment that competes against ours," said Antonio Rodriquez, sales manager, GH Electrotermia S.A., a supplier of heat-treating and welding systems based in Spain. "More foreign competitors have also entered the market. In the beginning we were practically alone. But today everyone believes China is the future."
The company has more than 100 installations in China, where it has been competing since 1991. "In 1991 we could manufacture in Spain," Rodriquez explained. "But since that time the competition from Chinese companies has increased, competitors from Europe have come, and this is pressuring our margins."
"There is a lot of noncompetitive capacity in China," observed Thermatool's Nallen. "What's going to happen once it is exposed to
the world's most competitive companies?"
Nallen fully expects a closing of the current gap in welding and cutting technologies in Chinese tube and pipe mills, which are significantly slower than their counterparts in the U.S. International demands will motivate improvements.
"They will have to get better," he said. "That's why we're here."
"Chinese manufacturing quality is improving every day," Luda Development's Ma said. "Within 10 years our Chinese competitors will be able to compete on an international scale."
Dominici of Emmedi made similar observations. The company has installed two bright annealing systems for stainless steel tubes during its 18-month-old efforts in China. And while demand for Emmedi's specialized equipment continues to increase, Dominici conceded, "China is a tough market. It is difficult to convince people of the value of your technology. They are very sensitive to price, and they want references from installed systems in China, not Europe or the U.S. The market is growing, but it's also highly competitive. A lot of competitors from Europe and the U.S. are now competing along with Chinese competitors that make a lower-level product for a very low price. But even they are rapidly improving their quality and technology.
![]() |
ITP-Axel's horizontal arm CMM and tube inspection software are used to measure manipulated tubes, wire, or hose and fixtures. It automatically generates a measuring sequence and 3-D graphic after the operator enters nominal tube data. |
"Therefore," he said, "our No. 1 priority is technological innovation, which is the only way to stay ahead of the marketplace. Our No. 2 priority is to reduce cost."
"There is no doubt the Chinese market is rapidly becoming more sophisticated," AddisonMckee's Wood agreed. "They are starting to focus on things like taking cost out of their processes, process management, and higher quality demands, all compatible with our level of product. The requirements for world-class quality coming from the automotive side are forcing the Asian manufacturers to improve the quality and sophistication of their products, which, in turn, challenges us to stay a step ahead."
Stefano Dellacqua, sales manager, SOMO S.p.A., has been confronting the challenges of the Chinese marketplace since 2001. "In the conventional and medium-sized press brakes and shears," he explained, "there is too much price competition from domestic Chinese producers. In the larger-size technologies, 6,000-ton press brakes, for example, the domestic producers are not so competitive."
Nonetheless, Dellacqua said, the fully automatic technologies he is positioning for larger tube and lighting pole applications are a tough sell. "The customer here says having one operator versus 10 is not an issue. We must convince them that the automation means consistent, repeatable quality that cannot be achieved with manual labor. As China's exports to the West increase, their export customers will demand these levels of quality."
Sailing the Trade Routes
Joe Shooshani emigrated to America from Europe some 30 years ago. He recalled the comparisons made back then. "We used to compare my old third-world country, or for that matter, all of Europe, to the United States," he remembered. "We would say the United States is the most sophisticated, most modern place on Earth.
"During this trip to Shanghai, when I saw all the brand-new buildings and the tremendous growth, for the first time I felt we have to work much harder and much smarter."
"We are here to do business in China, not take business out," Nallen said. "We have long-term business relationships established here. We do business in the local language and currency using local suppliers and support services.
"If you come in with short-term thinking, you'll fight hard," he warned. "If you think long-term, you have to be doing business where your customers are. If Americans come to China, they will find out that the Chinese need their expertise and technology."
Indeed, one Thermatool customer, a shock absorber producer, was experiencing weld failures and couldn't figure out the problem. "It turned out to be process-related issues," Nallen said, "fundamental mistakes they didn't know they were making. It was an older tube mill, and when new orders came in calling for higher-carbon-content materials, there was a negative impact on weld quality.
"This is nothing new," Nallen said of the transformation being driven by China's industrialization. "It's been going on for centuries. Some will be adventurous, get on the ships and sail the trade routes. Others will not."
Today there's no such thing as a slow boat to China. Just ask Joe Shooshani.
About the Author
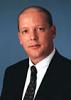
About the Publication
subscribe now
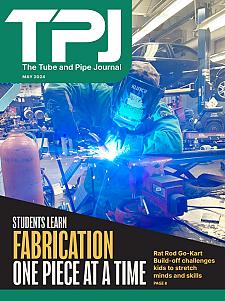
The Tube and Pipe Journal became the first magazine dedicated to serving the metal tube and pipe industry in 1990. Today, it remains the only North American publication devoted to this industry, and it has become the most trusted source of information for tube and pipe professionals.
start your free subscription- Stay connected from anywhere
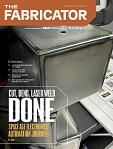
Easily access valuable industry resources now with full access to the digital edition of The Fabricator.
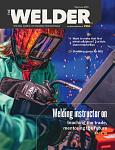
Easily access valuable industry resources now with full access to the digital edition of The Welder.
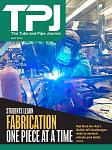
Easily access valuable industry resources now with full access to the digital edition of The Tube and Pipe Journal.
- Podcasting
- Podcast:
- The Fabricator Podcast
- Published:
- 05/07/2024
- Running Time:
- 67:38
Patrick Brunken, VP of Addison Machine Engineering, joins The Fabricator Podcast to talk about the tube and pipe...
- Trending Articles
Zekelman Industries to invest $120 million in Arkansas expansion
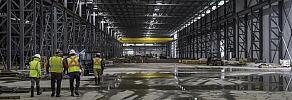
Making the move from hard automation to robotic welding
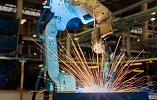
Brushless copper tubing cutter adjusts to ODs up to 2-1/8 in.
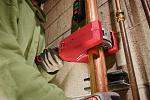
HGG Profiling Equipment names area sales manager
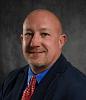
Miscellaneous metals fabricator increases productivity and opportunity with plasma cutting
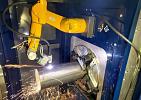
- Industry Events
Laser Welding Certificate Course
- May 7 - August 6, 2024
- Farmington Hills, IL
World-Class Roll Forming Workshop
- June 5 - 6, 2024
- Louisville, KY
Advanced Laser Application Workshop
- June 25 - 27, 2024
- Novi, MI
Precision Press Brake Certificate Course
- July 31 - August 1, 2024
- Elgin,