- FMA
- The Fabricator
- FABTECH
- Canadian Metalworking
Categories
- Additive Manufacturing
- Aluminum Welding
- Arc Welding
- Assembly and Joining
- Automation and Robotics
- Bending and Forming
- Consumables
- Cutting and Weld Prep
- Electric Vehicles
- En Español
- Finishing
- Hydroforming
- Laser Cutting
- Laser Welding
- Machining
- Manufacturing Software
- Materials Handling
- Metals/Materials
- Oxyfuel Cutting
- Plasma Cutting
- Power Tools
- Punching and Other Holemaking
- Roll Forming
- Safety
- Sawing
- Shearing
- Shop Management
- Testing and Measuring
- Tube and Pipe Fabrication
- Tube and Pipe Production
- Waterjet Cutting
Industry Directory
Webcasts
Podcasts
FAB 40
Advertise
Subscribe
Account Login
Search
Tube 2018 expo to take place amid global economic expansion
Timing couldn’t be better for biennial gathering in Düsseldorf
- By Eric Lundin
- March 14, 2018
- Article
- Shop Management
The time is drawing near for the largest biennial gathering of tube and pipe producers, equipment vendors, and fabricators, and Messe Düsseldorf, the organizer of Tube® 2018, is expecting its largest-ever turnout: 1,200 exhibitors and 31,000 visitors. The timing couldn’t be better. Hundreds of economies throughout the world are growing simultaneously, and this trend is expected to last for the foreseeable future.
According to the latest World Economic Outlook, which is published by the International Monetary Fund (IMF) and most recently updated on Jan. 22:
The cyclical upswing underway since mid-2016 has continued to strengthen. Some 120 economies, accounting for three quarters of world GDP, have seen a pickup in growth in year-on-year terms in 2017, the broadest synchronized global growth upsurge since 2010.
The projection from the IMF’s Regional Economic Outlook, published in November 2017, reveals a solid forecast for Europe:
The European recovery is strengthening and broadening appreciably. Real GDP growth is projected at 2.4 percent in 2017, up from 1.7 percent in 2016, before easing to 2.1 percent in 2018. The European recovery is spilling over to the rest of the world, contributing significantly to global growth. Most emerging European economies are now seeing robust wage growth.
FocusEconomics provides a forecast similar to that of the IMF, expecting to see the Eurozone growing a robust 2.2 percent next year. Growth dynamics include accommodative monetary policy, an improving labor market, and high sentiment. In 2019, growth is expected to slow slightly to 1.9 percent.
A key ingredient in this expansion is its resilience. Despite substantial uncertainties over the last few years, Europe’s economies have continued to grow. A massive influx of immigrants that started in 2014, terrorist attacks in France (2015) and Britain (2017), Britain’s referendum vote to exit the European Union (2016), a coup attempt in Turkey (2016), and the Catalan independence referendum in Spain (2017) haven’t prevented the economies from gathering steam.
Tube, Pipe, and More
One broad-based indicator that tells quite a bit about economic activity, and one that supports the metals industry—especially tube and pipe—is the volume of automobile sales. The number of passenger cars produced throughout the world nearly doubled in the last decade, increasing from 50 million in 2009, according to data provided by the International Organization of Motor Vehicle Manufacturers, to an anticipated 99 million in 2018, according to data aggregator Statista. In addition to being a gauge of transportation requirements and a predictor of gasoline consumption, this trend indicates rising living standards as more people throughout the world move into the middle class. It doesn’t stand alone; an automobile is just one of many durable goods people buy as their purchasing power grows.
Other telling factors concern crude oil. Although the spot price for a barrel of West Texas Intermediate isn’t anywhere near the lofty heights of the 2011-2014 timeframe, when it hovered around $100, it has recovered from the recent low, $26.19 (early 2016). Selling for less than $50 per barrel as recently as September 2017, it was trading for more than $60 per barrel in January.
Rising prices encourage additional exploration, drilling, and refining activity, which leads to hiring more workers to run the rigs, buying more components to maintain them, and ultimately consuming more steel to build new ones. Indeed, the international rig count increased by 13 over 11 months (from
December 2016 to November 2017), then increased by 12 more in a single month (December 2017).
In the U.S., tube and pipe producers that deal in the oil and gas industry got a recent break when the U.S. International Trade Commission (ITC) lowered the boom on several Korean companies that make energy-oriented tube and pipe products.
“Every complaint filed with the ITC bounced off Korean producers until recently,” said Donald Gibeaut, tubular products manager for Ajax Tocco Magnathermic Corp., a manufacturer of welding power sources and a variety of heating equipment, including heaters, furnaces, and ovens. The recent ruling provided substantial relief for domestic producers, considering that Korean manufacturers had 30 to 40 percent of the import market for some products, Gibeaut said. This has shaken up the industry quite a bit, he added, as many small finishing companies—some of which were based solely on imports from Korea—were forced to close up shop.
It didn’t take long for several Korean firms to take a different tack.
“Some Korean companies are buying U.S. facilities or investing in partnerships,” Gibeaut said. It’s a strategy that works. When a high tariff makes exporting to the U.S. nearly unprofitable, companies with deep pockets set up shop in the U.S. to capture or maintain U.S. market share.
AjaxTocco doesn’t make mills, but it makes many of the systems that most tube or pipe production facilities need, such as electric resistance welding (ERW) power sources for seam welding and induction heating lines to heat-treat, quench, and temper tubular products, as well as systems for seam annealing and bright annealing. Rising oil prices and the Korean shakeup have boosted quoting activity for the company.
“We were very busy in the fourth quarter and we’re busy now,” Gibeaut said.
Carlos Thagard, director of sales for tube and pipe mill manufacturer FD Equipment, also said that business was good in recent months.
“The expanding economy is a big factor,” he said. “Many manufacturers are doing well now, and requests for quote are up, especially from companies that use a lot of tube. We’re getting inquiries from companies that haven’t made tube in the past but want to make their own now.”
Many inquires are coming in for mills to make tube for the automotive market and to make structural components, Thagard said. The activity is both for upgrades to replace existing mills and for new mills to accommodate growth. Of course, mill manufacturers have to compete with equipment available on the used market, but Thagard sees this source as drying up lately. That bodes well to help the entire industry move forward. He’s confident that anyone using an old mill as a benchmark will be pleasantly surprised by today’s technology.
“Some manufacturers are still using mills built in the 1940s,” he said. “They don’t compare to the designs of new mills,” he said.
Doing More with Less
How are metal fabricators and durable goods manufacturers dealing with this upswing in business activity? Many are following the traditional mantra, “Do more with less.” According to several Tube exhibitors interviewed for this article, this means substituting automation for tasks that traditionally have been performed manually. While workers are favored for adaptability and versatility, automated systems usually do better than workers in productivity, quality, and consistency.
Jurgen Jost, president and CEO of ASMAG USA Inc., summed up the rationale for integrating automation: “Automation is necessary to increase productivity without increasing costs.”
Combined with Seuthe, the company manufactures complete mill systems for making tube, pipe, and profiles; equipment for extruding and drawing, including related processes such as pointing and straightening; and material handling systems. The ASMAG Group recently teamed up with Ingenia, which makes fully automated galvanizing lines and galvanizing plants.
“Many think that drawing starts with pointing, but the process starts further upstream,” Jost said. “It starts with the tube’s pretreatment.” Ingenia’s forte is setting up entire plants that move material from station to station throughout the galvanizing process without manual labor.
“It’s a hands-free operation,” he said. Because the company also makes material handling machinery, its equipment covers all the steps. Furthermore, the companies in the ASMAG Group make as many of the components as possible, which they see as critical in maintaining control over quality and lead times, Jost said.
Jost cites Seuthe’s flexible cold forming (FCF®) technology as another way to enhance productivity by replacing labor with automation. Using a cage concept, this tube mill design has automated tooling exchange, eliminating lengthy manual changeovers.
Cutting equipment manufacturer HGG, which manufactures machines for oxyfuel and plasma cutting, likewise benefits from the trend to substitute automated machines for labor. Focused on 3-D profiling, the company’s machines are designed and built for cutting and end preparation of heavy-wall beams, tubes, and profiles and are used for fabricating large-diameter or heavy-duty components for steel construction, process piping, offshore and onshore applications, crane construction, and shipbuilding.
“The company has more than 30 years of experience in developing machines for the shipbuilding industry,” said Jack Kistemaker, the company’s chief technology officer. “We have manufactured machines for the world’s largest shipbuilders, such as Hyundai and Damen,” he said. Shipyards have relied on automation for decades.
“For forty years, the biggest shipyards have used robotic cutting lines,” Kistemaker said. “For small fabrication shops, moving to automation is just a matter of time.” The company will bring its extensive experience in shipbuilding equipment to the Tube 2018 audience in the form of its latest machine developed for the shipbuilding industry, Ship Profiler 450.
“This machine doesn’t have the entire capacity of our large machines,” Kistemaker said. Compared to one of the company’s high-end machines, it has about 70 percent of the processing speed at 40 percent of the cost. “It has enough capacity for small and medium-size shipyards,” he explained.
A critical element in the machine’s productivity is that it doesn’t need much in the way of programming. The software does this on the user’s behalf.
“About 30 percent of HGG’s workforce are software engineers,” said
Wiebe Wiersma, sales manager for HGG. Their goal is to eliminate machine programming.
“The software provides the interface between the CAD drawing and the machine,” Kistemaker said. “It’s intended for the most inexperienced user. It’s as simple as using an iPhone.” In addition to handling the programming, the software compensates for imperfect workpieces. Most profiles aren’t straight, and the dimensions often are slightly off specification; a laser measures the workpiece so the operator doesn’t have to compensate for the deviations.
Kistemaker compared automated processes to manual processes for making a typical pressure vessel, which requires a substantial amount of prep work in marking, cutting, and grinding, estimating that 40 hours of manual labor can be compressed down to one hour of machine time.
Machine tool and industrial laser manufacturer TRUMPF facilitates doing more with less by integrating formerly downstream process steps into its TruLaser tube machines. It will demonstrate machines in its 5000 series, which handle workpieces up to 6 in. in dia., and its 7000 series, which handle diameters up to 10 in. Most TruLaser machines have threading capability in the form of tapping for heavy-wall tube and the flow-drill process for thin-wall tube, and machines in the 7000 series eliminate downstream cleaning by integrating a catcher device that reduces spatter.
The 5000 series machines are available with either a CO2 or solid-state resonator. The company stresses that each has clear advantages—the CO2 version is built on an open platform and modular design, while the other has RapidCut mode, which uses the full cutting speed of the solid-state technology.
As for the prevailing business conditions, the company is seeing a broad-based demand for its tube fabricating machines.
“We see strong demand in all relevant sectors, especially in furniture, mostly business and office furniture, and agricultural machines and equipment, and fitness equipment,” said Head of Product Management Tube Cutting Karl Schmid.
“Do more with less” also has found its way into the design of welding power sources. AjaxTocco introduced such a power source at FABTECH® in 2017 and will display it at Tube 2018. A key component used in solid-state, high-frequency induction ERW power supplies went through a transformation about five years ago, Gibeaut said, and the company updated its power supplies accordingly.
This amplifying component, the metal-oxide semiconductor field effect transistor (MOSFET), typically uses silicon for the substrate, Gibeaut said. However, the new MOSFET uses silicon carbide for a substrate. The current-carrying capacity of the new variety is much greater, so the new power supply—marketed under the Emmedi brand, model name MosWeld SiC—uses fewer of these components.
“A conventional design for a 500-kilowatt power supply had 320 MOSFETs, but the new design has just 20,” Gibeaut said. “It develops the same amount of power, but it’s more efficient and more reliable because we reduced the part count.” he said. The company has installed this model in Europe and in the U.S., Gibeaut said.
Visiting Tube
Expo visitors can meet these exhibitors at the expo locations listed below. For the most up-to-date information, see the exhibitor list at www.tube.de.
Eric Lundin can be reached at ericl@thefabricator.com.
Ajax Tocco Magnethermic Corp., www.ajaxtocco.com — Hall 6, booth A17
ASMAG Group, www.asmag.at — Hall 6, booth A01
FD Machinery, www.fdmachinery.com — Hall 6, booth G12
HGG Group, www.hgg-group.com — Hall 6, booth E04
TRUMPF, www.trumpf.com — Hall 6, booths A09 and E22
Tube & Pipe Journal®, www.thefabricator.com — Hall 6, booth C10-05
A Guide to Tube
Visitors who have never attended a trade show in Germany will probably find that getting there and getting around isn’t too difficult. English is spoken widely in Germany, especially in service sectors that cater to international clientele, and transportation is convenient and punctual. Getting a passport (allow at least six weeks of processing time), making transportation arrangements, and setting up a hotel reservation are the three key components (the organizer recommends making reservations through TTI Travel Inc., www.traveltradeint.com) for planning a trip to the expo.
Location, Dates, Times, and Costs
Messe Düsseldorf/Messeplatz
Stockumer Kirchstrasse 61
Düsseldorf, Germany 40474
April 16-19: 9:00 a.m. - 6:00 p.m.
April 20: 9:00 a.m. - 4:30 p.m.
One-day Ticket
Online, before the expo starts: EUR 40.00
On-site: EUR 58.00
Season Ticket
Online, before the expo starts: EUR 80.00
On-site: EUR 98.00
Getting There and Getting Around
Düsseldorf Airport (DUS) is less than two miles from the exhibition center and has direct links from 200 destinations in 50 countries on four continents. Trains run from the exhibition center directly to several stations throughout Düsseldorf, including the main train station.
Transportation to and from Messe Düsseldorf
All admission tickets entitle the bearer to travel, at no cost, to and from the exhibition grounds on the day of the visit on all public transportation in the VRR system. Look for this symbol:
Exhibitor Product Categories
- Raw materials, tube, pipe, and accessories
- Tube and pipe manufacturing machinery and ancillary
- Tube and pipe fabricating machinery and related equipment
- Control system hardware and software
- Measurement and testing technology
- Material handling equipment and systems
Visitor Industries
- Iron, steel, and nonferrous metals producers
- Tube and pipe producers
- Automotive industry
- Chemical processors
- Energy, oil, gas, and water supply systems builders
- Construction industry
- Electrical industry
- Appliance manufacturers
- Measuring and control technology
- Maintenance, repair, and operations
- Skilled tradespeople and technical specialists
Service & Contact
Messe Düsseldorf GmbH
Visitor service telephone number: 49-211-4560-7616
Web: www.messe-duesseldorf.de
About the Author
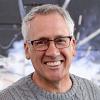
Eric Lundin
2135 Point Blvd
Elgin, IL 60123
815-227-8262
Eric Lundin worked on The Tube & Pipe Journal from 2000 to 2022.
About the Publication
Related Companies
subscribe now
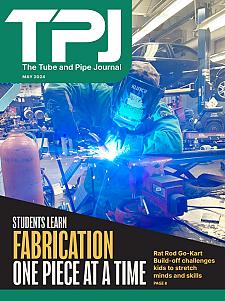
The Tube and Pipe Journal became the first magazine dedicated to serving the metal tube and pipe industry in 1990. Today, it remains the only North American publication devoted to this industry, and it has become the most trusted source of information for tube and pipe professionals.
start your free subscription- Stay connected from anywhere
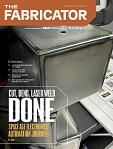
Easily access valuable industry resources now with full access to the digital edition of The Fabricator.
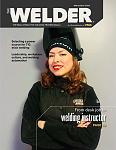
Easily access valuable industry resources now with full access to the digital edition of The Welder.
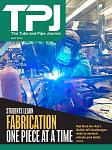
Easily access valuable industry resources now with full access to the digital edition of The Tube and Pipe Journal.
- Podcasting
- Podcast:
- The Fabricator Podcast
- Published:
- 04/30/2024
- Running Time:
- 53:00
Seth Feldman of Iowa-based Wertzbaugher Services joins The Fabricator Podcast to offer his take as a Gen Zer...
- Trending Articles
Team Industries names director of advanced technology and manufacturing
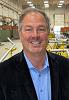
Zekelman Industries to invest $120 million in Arkansas expansion
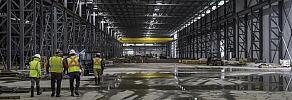
3D laser tube cutting system available in 3, 4, or 5 kW
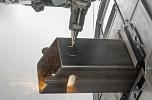
Corrosion-inhibiting coating can be peeled off after use
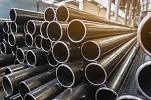
Brushless copper tubing cutter adjusts to ODs up to 2-1/8 in.
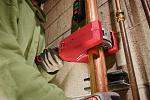
- Industry Events
Pipe and Tube Conference
- May 21 - 22, 2024
- Omaha, NE
World-Class Roll Forming Workshop
- June 5 - 6, 2024
- Louisville, KY
Advanced Laser Application Workshop
- June 25 - 27, 2024
- Novi, MI
Precision Press Brake Certificate Course
- July 31 - August 1, 2024
- Elgin,