- FMA
- The Fabricator
- FABTECH
- Canadian Metalworking
Categories
- Additive Manufacturing
- Aluminum Welding
- Arc Welding
- Assembly and Joining
- Automation and Robotics
- Bending and Forming
- Consumables
- Cutting and Weld Prep
- Electric Vehicles
- En Español
- Finishing
- Hydroforming
- Laser Cutting
- Laser Welding
- Machining
- Manufacturing Software
- Materials Handling
- Metals/Materials
- Oxyfuel Cutting
- Plasma Cutting
- Power Tools
- Punching and Other Holemaking
- Roll Forming
- Safety
- Sawing
- Shearing
- Shop Management
- Testing and Measuring
- Tube and Pipe Fabrication
- Tube and Pipe Production
- Waterjet Cutting
Industry Directory
Webcasts
Podcasts
FAB 40
Advertise
Subscribe
Account Login
Search
Falcon Steel builds vast tubular structures to support power industry expansions, upgrades, replacements
Fabricator’s towering expertise, business acumen cuts delivery time from months to days
- By Eric Lundin
- July 18, 2017
- Article
- Tube and Pipe Fabrication
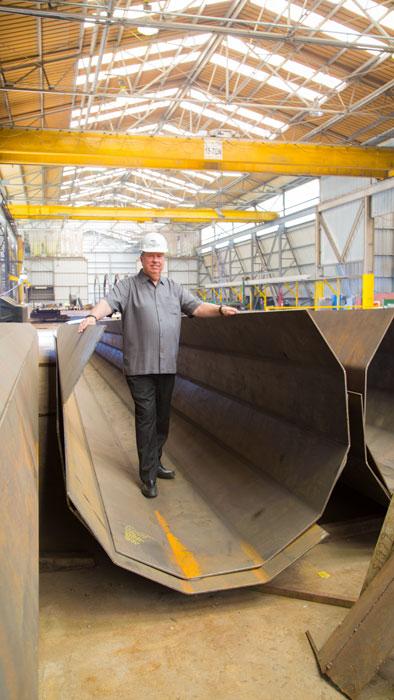
Falcon Steel America’s president and CEO, Jim Taylor, shows one of the company’s small products. The company makes tubular structures up to 121⁄2 feet in diameter.
You flip a switch, a light comes on, and you probably don’t give it much thought. If you were to dig into the details, you’d find that the electrical network in your home, mainly 120-volt circuits carrying a maximum of 15 amps of current, runs through 14-gauge wire. That wire typically comprises three solid strands of copper that measure 0.0641 inches in diameter. Not much to it.
However, the system that transfers that electricity from the generating station to your home is much more complex. Electrical current travels from the station to a step-up transformer, through a transmission network, then through a step-down transformer and through a distribution network before it finally gets to your house. The step-up transformer brings the initial voltage up to a transmission level, usually between 69,000 and 765,000 V. The heaviest wire in that section of the grid is 2,156 ga., comprising 84 strands of aluminum conductor surrounding 19 strands of steel cable for strength. The wire is rated to carry 1,623 amps of current and weighs 2,509 pounds per 1,000 feet.
What supports such heavy cables? Two types of structure: lattice tower and monopole. In some cases, towers are made from wood. Prone to deterioration from weather and insects—mainly moisture and termites—they tend to last 15 years or so, maybe a maximum of 20, and often they are replaced these days by steel structures. Steel structures have two main advantages. First, they last much longer than wood, occasionally exceeding 100 years. Second, because steel lends itself well to making structures that are stronger and taller than their wooden counterparts, power utilities can use a smaller number of structures over a given distance.
Falcon Steel America LLC, Haltom City, Texas, is the only company in the U.S. involved in designing and fabricating such lattice structures from steel. It recently has expanded its capacity in manufacturing transmission towers, forming large-diameter tubes from plate to make monopoles.
Growing Up in the Metroplex
When Falcon Steel America was founded in 1963, it catered to the construction market, and it was in the right place at the right time. Its home base, the Dallas-Ft. Worth area (DFW), had a population of 2 million residents. That location was an important hub even then, yet destined for much more growth. By 2015, it had become a vast metropolitan area, home to 7 million people and covering 9,000 square miles over 13 counties.
Construction accompanied the area’s growth. It wouldn’t be an understatement to say that Falcon played a big role in contributing to the structures that define the DFW skyline and the infrastructure that it relies on.
“When Falcon was founded in 1963, it made structural building components,” said President and CEO James Taylor. “This area has a large number of multilevel commercial buildings, and Falcon fabricated all of the components they typically need, from I-beams to handrails.”
Falcon’s growth wasn’t tied just to the local area. The U.S. population was 189.2 million in 1963 and as of 2017 it approached 325 million. The accompanying increase in infrastructure and utilities from coast to coast provided a rich growth opportunity for Falcon, which started to spread its wings shortly after it was founded.
The company started fabricating steel structures for power utilities in 1965, said Taylor. Its focus was on lattice towers which, despite their complex appearance, are less expensive to build than monopoles.
“They have many more components than a monopole, but they’re easier to fabricate,” said Corporate Business Development & Project Management Officer Cody Barry. “They’re put together with mechanical fasteners, whereas monopoles require quite a bit of welding and therefore weld testing. The drawback to a lattice tower is that it needs maintenance and upgrades, whereas a monopole doesn’t have additional costs.”
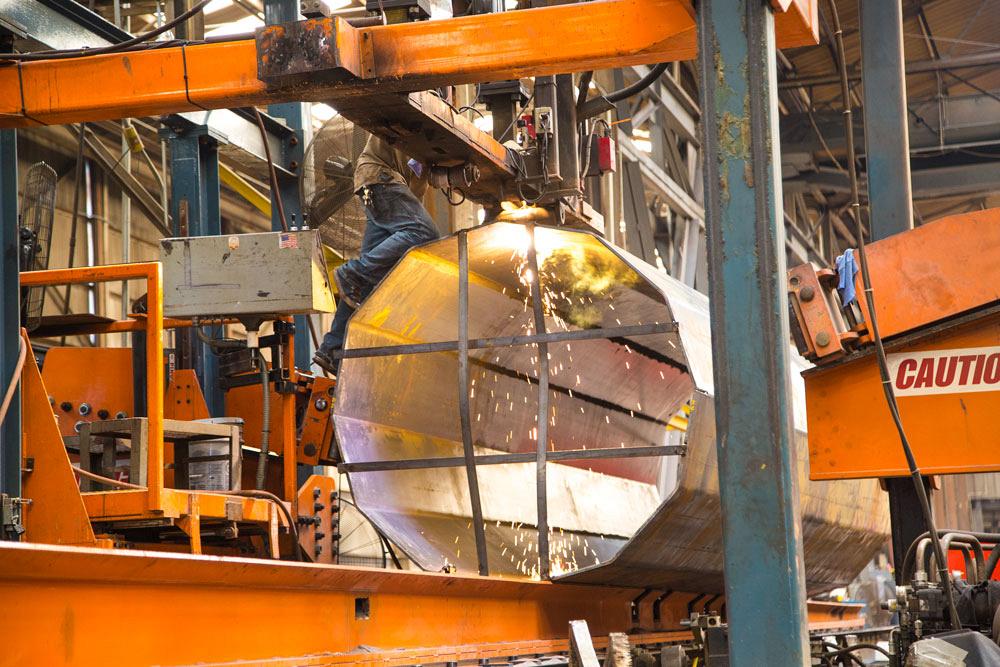
Figure 1
After putting two half-shells together, workers affix strapping to reinforce the tube for submerged arc welding.
Falcon was in a solid niche for many years. It wasn’t necessarily protected from competition, but the nature of the business drove many of its competitors out of the market. This cyclic business is characterized by upswings that often last three to five years, followed by downturns that usually last just as long, Taylor said. While others left the lattice tower market, Falcon endured and even thrived, because it has other product lines that run on other cycles. However, during late 2015 and early 2016, the company came under increasing price pressure from imported lattice towers, so it increased its capacity to support the monopole market.
Making a Monopole from Scratch
“We use A36 material, A572 grade 50, and A572 grade 65,” Barry said. For the poles, the material thickness is 3⁄16 to 1 in., widths run from 48 to 150 in., and lengths are up to 60 ft. Falcon makes big towers. It also makes big base plates, fabricated from steel up to 5 in. thick.
After pulling the material from inventory and leveling it, the Falcon staff cuts it on a plasma table. The shape isn’t rectangular but trapezoidal, because monopoles are wider at the base than at the top. Each piece then is moved to a 6,000-ton, 60-ft. press brake, which imparts five bends to form a six-sided half shell. After mating two half-shells, the company uses submerged arc welding to make two partial-penetration welds (see Figure 1). At this point the pole isn’t finished, but it has taken on the shape of a tower: a dodecagon. The diameter at the base of a small pole is around 48 in.; the large ones measure 150 in. across.
“You could drive a car through one of these poles,” Taylor said.
The pole end then gets fitted with additional features for hanging the wire and a male or female slip fitting so it can be joined to the next pole section (see Figure 2). The company uses a variety of weld inspection techniques—visual, dimensional, ultrasonic, and magnetic particle—to verify each weld’s integrity and prevent a weld failure in the field.
How Straight Is Straight Enough? Everyone who knows steel knows that it’s generally predictable, but its behavior isn’t certain. Even after the opposite sides of a symmetric structure are heated evenly, the resulting item can have a bit of distortion to it. Falcon uses a press to square up the ends and take out slight amounts of camber, but this isn’t always enough.
“If necessary, we’ll apply heat to straighten the pole,” Barry said. It’s a scientifically sound solution, but the application of heat isn’t an entirely scientific undertaking. Getting it right requires a thorough understanding of steel’s behavior, quite a bit of experience, and a blacksmith’s intuition.
“It’s an art,” Barry said, summing it up.
Straight, of course, doesn’t mean perfectly straight. Every industry allows some tolerance, and this one is no different. The amount of deflection is specified in percent over the entire structure, usually 1, 2, or 5 percent, Barry said. Then again, some applications need some deflection.
“Some structures support the cables at a change in direction, which can be up to 90 degrees,” Barry said. The choices are to make an extremely rigid pole with no camber, which isn’t really practical, or make a pole with some camber and leave it to the load to straighten it in place.
How Long Is Long Enough? The pole isn’t finished yet. Every structure has to last many, many decades, and the specific installation location makes a big difference in its life expectancy. A structure installed near Santa Fe, N.M., faces a much different weathering and corrosion environment than one located along the Gulf Coast Highway. On one hand, the dry desert air is essentially inert and does little to galvanized steel. It’s difficult to predict the life expectancy of a galvanized steel structure in such an environment. On the other hand, the salty, briny, humid air along the Gulf of Mexico is about as bad as it gets as far as inducing corrosion.
Regardless of the structure’s destination, a hot bath in a tub full of zinc is necessary. The company follows current best practices, adhering to application guidelines and testing procedures set forth by the American Galvanizers Association (AGA) and the American Society of Testing & Materials, so everything that goes out the door has a protection level that corresponds to the installation environment. For structures shipped to areas that are aggressively corrosive, Falcon steps up the galvanizing process to impart a thicker coating or it pretreats the steel, for example by sandblasting it, to give the zinc a rougher surface to bite into. For some of its other product lines, such as signposts that are embedded in soil when installed, Falcon specifies a coat of paint over the galvanized surface.
For parts that measure up to 4.5 by 5 by 42 ft., the company uses its own galvanizing line, which was designed for lattice tower components. For parts larger than that, the company outsources the galvanizing process.
Meeting More Regulatory Requirements and Industry Norms. Keeping up with certifications and regulations isn’t necessarily difficult, but a fabricator like Falcon has to pay close attention because it delivers products to be installed in all 50 states and outside the U.S. as well. Most of the compliance is standardized because it’s at the federal level, but nevertheless Falcon does have to comply with a variety of state and local regulations as well.
Regulatory compliance and building the documentation package start as soon as Falcon receives steel from the mill when it reviews the mill test reports. It then relies on the standards and guidelines crafted by the aforementioned AGA and two other organizations in how it goes about building its products.
“The American Institute of Steel Construction (AISC) is the primary source of our certifications. Falcon is certified in structures and bridge components,” Barry said, referring to AISC BU (building fabricator) and AISC CPT (certified bridge component manufacturer). The company’s welders go through an in-house training program and are certified to AWS D 1.1, structural steel, and D 1.5, bridges.
“The Department of Transportation and most state and local regulations cite AWS certification D 1.5 for any structure erected near a roadway,” Barry said. “That effectively raises the bar, but that’s to our advantage because we weld
everything to comply with D 1.5 anyway,” he said. No sense in having two sets of welding and nondestructive testing procedures and the mild logistical nightmare that would ensue from applying one set of procedures to some projects and another set to other projects.More than Surviving, Falcon Is Thriving
Two elements key to Falcon’s success are its careful choice of markets and its business model. The firm has been judicious in working complementary markets for many decades, so it has that down pat, but it has added two new aspects to its business model in the last two years.
Diversified Markets. In addition to poles, Falcon works in two other major markets: electrical substations and highway structures.
Electrical substations are integral to the electrical distribution system, and Falcon is well-versed in making the components to go into them—dead-end poles and all manner of supports, pedestals and stands for transformers, switchgear, bus bar, insulators, and arrestors. However, it makes more than just components. It delivers entire systems, so the contractor can get a substation in a package. The contractor doesn’t have to source components, have them galvanized, and ship them. Falcon delivers turnkey packages.
The company uses the same strategy in producing highway structures, assemblies that support lighting, signage, and intelligent transportation systems.
“Whether it’s a pole with a cantilevered lattice, a pole with a bent tube that holds a light fixture, or a high-mast pole, 120 ft. tall with a light fixture, it doesn’t matter—Falcon builds them all,” Barry said.
The next time you’re driving along a lonely stretch of highway on a moonless night and the highway is well illuminated, or you’re not sure if you’re running late and then you see an overhead sign displaying the estimated time to the next major interchange, you can thank the designers of the data-gathering system and a fabricator like Falcon for providing that additional bit of convenience to your trip. If you see one of these in Texas, you can thank Falcon, because most likely that unit originated in Haltom City.
Finally, the company pulls in an extra bit of revenue from commercial galvanizing. When it’s not using its galvanizing line, Falcon uses the line to coat products for other manufacturers that need steel galvanized.
Upgrading the Business Model. As far as the business model, this is where Falcon is taking steps to create a sea change in the industry.
“The current delivery schedule for a pole can be 20 or 25 weeks,” Taylor said. Construction projects rarely proceed on schedule anyway, mainly because a holdup in a delivery of any components or materials along the way, or bad weather, can throw a big project off the schedule. A lead time for an assembly that approaches six months doesn’t help construction crews stay on track. This isn’t to say that 20 weeks isn’t warranted, because indeed the build cycle for a pole order is lengthy. The fabricator has to procure the material, which can amount to enough for 100 poles; fabricate all the components; galvanize them; and truck them to the destination.
To reduce the delivery time, Falcon developed a material management program. It makes the structures and stores them until they are needed. Falcon’s goal is to stay ahead of construction schedules, and storing finished products gives the company more than enough flexibility to make a big difference in timing the deliveries.
“It cuts the delivery time down from 25 weeks to 10 days,” Barry said.
As it stands, all of the company’s storage yards are in Texas, but Falcon has plans to expand this program by leasing commercial space near project locations. This has the potential to cut lead times down to hours. It also means that Falcon can adjust the delivery time to match any delays in the schedule.
That might not mean much to a residential customer, unless the power is out, and Falcon has a plan for fulfilling urgent orders, too: It can run a secondary production line. The main one handles the day-to-day scheduled business, and the other is set up for urgent orders. The material management system takes a little bit of pressure off of the main
production line, which gives Falcon management some latitude in shifting labor over to the second production line when necessary. The Falcon staff puts all available hands to the task and, just as it does with scheduled orders, compresses the timeline for urgent orders remarkably.
“We had a recent case in which we delivered 11 towers in nine days,” Barry said.
Five Months Ahead of the Competition
This isn’t to say that it’s easy to stay ahead of the competition. In addition to domestic competition, the company noticed that imported lattice towers became much more prevalent near the end of 2016, and the prices are really low.
However, Falcon has a couple of longstanding advantages. The company is long on experience in this field, its customers don’t have to deal with any cultural or language barriers, and it’s easier to deal with a domestic company if an issue arises.
Finally, because Falcon can offer both lattice towers and monopoles, and it has its material management program, it can cut the delivery time from months to days.
Falcon Steel America LLC, 4201 Old Denton Rd., Haltom City, TX 76117, 817-581-9500, www.falconsteel.com
About the Author
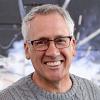
Eric Lundin
2135 Point Blvd
Elgin, IL 60123
815-227-8262
Eric Lundin worked on The Tube & Pipe Journal from 2000 to 2022.
About the Publication
subscribe now
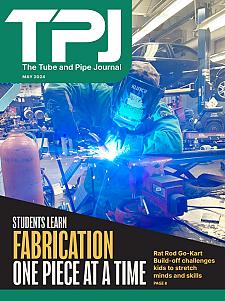
The Tube and Pipe Journal became the first magazine dedicated to serving the metal tube and pipe industry in 1990. Today, it remains the only North American publication devoted to this industry, and it has become the most trusted source of information for tube and pipe professionals.
start your free subscription- Stay connected from anywhere
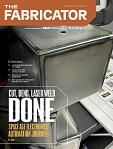
Easily access valuable industry resources now with full access to the digital edition of The Fabricator.
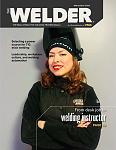
Easily access valuable industry resources now with full access to the digital edition of The Welder.
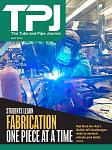
Easily access valuable industry resources now with full access to the digital edition of The Tube and Pipe Journal.
- Podcasting
- Podcast:
- The Fabricator Podcast
- Published:
- 04/30/2024
- Running Time:
- 53:00
Seth Feldman of Iowa-based Wertzbaugher Services joins The Fabricator Podcast to offer his take as a Gen Zer...
- Trending Articles
Team Industries names director of advanced technology and manufacturing
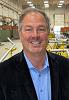
Zekelman Industries to invest $120 million in Arkansas expansion
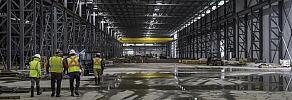
3D laser tube cutting system available in 3, 4, or 5 kW
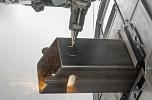
Corrosion-inhibiting coating can be peeled off after use
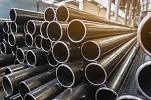
Brushless copper tubing cutter adjusts to ODs up to 2-1/8 in.
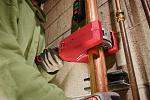
- Industry Events
Pipe and Tube Conference
- May 21 - 22, 2024
- Omaha, NE
World-Class Roll Forming Workshop
- June 5 - 6, 2024
- Louisville, KY
Advanced Laser Application Workshop
- June 25 - 27, 2024
- Novi, MI