Editor-in-Chief
- FMA
- The Fabricator
- FABTECH
- Canadian Metalworking
Our Publications
Categories
- Additive Manufacturing
- Aluminum Welding
- Arc Welding
- Assembly and Joining
- Automation and Robotics
- Bending and Forming
- Consumables
- Cutting and Weld Prep
- Electric Vehicles
- En Español
- Finishing
- Hydroforming
- Laser Cutting
- Laser Welding
- Machining
- Manufacturing Software
- Materials Handling
- Metals/Materials
- Oxyfuel Cutting
- Plasma Cutting
- Power Tools
- Punching and Other Holemaking
- Roll Forming
- Safety
- Sawing
- Shearing
- Shop Management
- Testing and Measuring
- Tube and Pipe Fabrication
- Tube and Pipe Production
- Waterjet Cutting
Industry Directory
Webcasts
Podcasts
FAB 40
Advertise
Subscribe
Account Login
Search
Complexity isn’t always free in 3D printing
Why complex AM parts cost more than simple parts
- By Don Nelson
- February 3, 2020
During a recent interview with the business development manager of Lincoln Electric’s Additive Solutions division, Mark Douglass, I didn’t expect him to debunk one of my long-held beliefs about additive manufacturing. But he did.
Like many in manufacturing, I accepted the adage that when it comes to designing 3D-printed parts, “the complexity is free.” I offhandedly uttered that phrase toward the end of our interview. He responded, “I know people like to say that. Maybe it’s free to the design group, but it’s not free. In order to manufacture that complexity takes some doing.”
I followed up with Douglass and asked him to elaborate. He said all that’s needed to 3D-print a part, theoretically, is a printer and a CAD file. If the designer alters a file by adding complexity to the design, then, in theory, the printer’s motion-control system would adjust to the programming changes and seamlessly build the latest iteration.
“However, the machine and the slicing/path planning software have to be able to handle the added complexity, which very well may require adaptations to both in order to print the newly designed part,” explained Douglass. He described 3D-printing a simple cylinder to illustrate his point. All that’s required is a turntable and a printhead, and that one of the two devices have some vertical-motion capability. But if the shape is a cylinder that transitions to another cylinder—such as a 90-degree elbow—or multiple cylinders positioned at different angles to each other, then both the software and hardware would need to be more sophisticated to accommodate the more complex design.
“That added sophistication incurs added expense,” said Douglass.
A fair amount of material can be found online that supports his contention. Among them is a study conducted at Loughborough University in 2017 by Patrick Pradel and three others. Study results show that shape complexity directly relates to increased build time and material consumption.
The U.K. researchers set out to empirically disprove studies that claim a 3D-printed part’s complexity has no influence on its manufacturing cost. They used a Stratasys FDM-style printer to make a series of load-cell holders that differed from one another in terms of design complexity.
The foursome also developed a Shape Complexity Index (SCI) to determine the geometrical complexity of each design variation. The results show shape complexity directly relates to increased build time and material consumption. “In fact,” wrote the researchers, “the building time of the component with the highest SCI was generally twice the building time of the component with the lowest SCI.”
The conversation with Douglass and the online studies that refute the “complexity is free” claim of AM-technology promoters everywhere brings to mind another adage: “There is no free lunch.”
About the Author
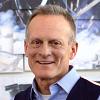
Don Nelson
2135 Point Blvd.
Elgin, IL 60123
(815)-227-8248
About the Publication
- Podcasting
- Podcast:
- The Fabricator Podcast
- Published:
- 04/16/2024
- Running Time:
- 63:29
In this episode of The Fabricator Podcast, Caleb Chamberlain, co-founder and CEO of OSH Cut, discusses his company’s...
- Trending Articles
- Industry Events
16th Annual Safety Conference
- April 30 - May 1, 2024
- Elgin,
Pipe and Tube Conference
- May 21 - 22, 2024
- Omaha, NE
World-Class Roll Forming Workshop
- June 5 - 6, 2024
- Louisville, KY
Advanced Laser Application Workshop
- June 25 - 27, 2024
- Novi, MI