- FMA
- The Fabricator
- FABTECH
- Canadian Metalworking
Our Publications
Categories
- Additive Manufacturing
- Aluminum Welding
- Arc Welding
- Assembly and Joining
- Automation and Robotics
- Bending and Forming
- Consumables
- Cutting and Weld Prep
- Electric Vehicles
- En Español
- Finishing
- Hydroforming
- Laser Cutting
- Laser Welding
- Machining
- Manufacturing Software
- Materials Handling
- Metals/Materials
- Oxyfuel Cutting
- Plasma Cutting
- Power Tools
- Punching and Other Holemaking
- Roll Forming
- Safety
- Sawing
- Shearing
- Shop Management
- Testing and Measuring
- Tube and Pipe Fabrication
- Tube and Pipe Production
- Waterjet Cutting
Industry Directory
Webcasts
Podcasts
FAB 40
Advertise
Subscribe
Account Login
Search
Additive technologies developed for space are being adopted for Earth
- June 7, 2021
- News Release
- Additive Manufacturing
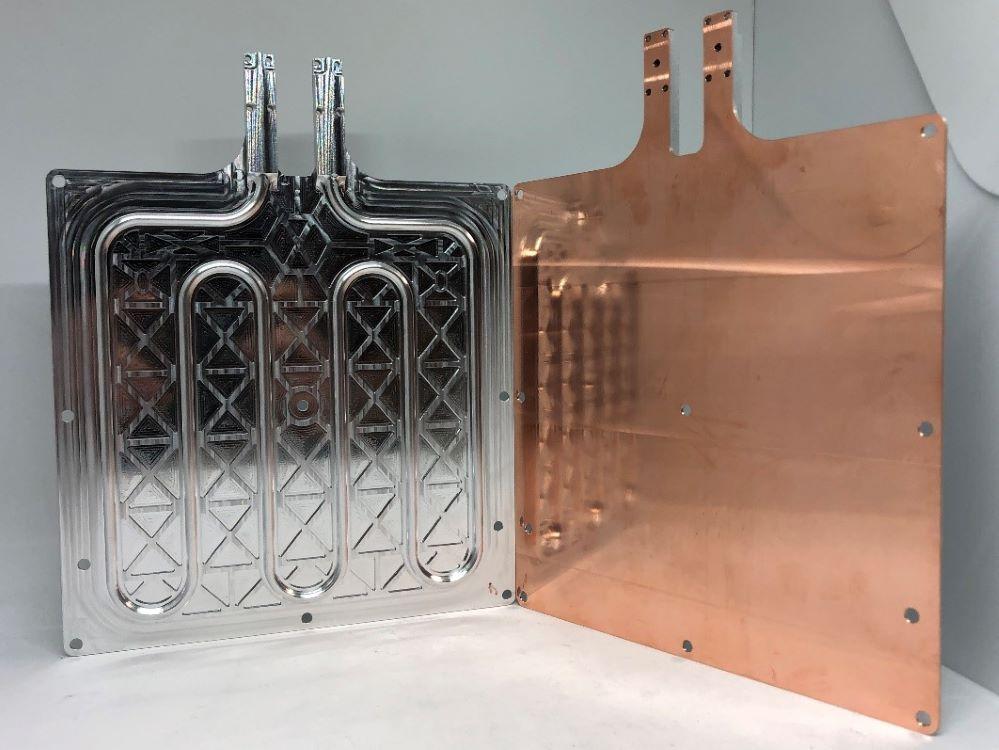
This 3D-printed radiator for a CubeSat miniature satellite combines aluminum and a small bit of copper to allow heat to spread more evenly across the face. Fabrisonic was able to combine the metals using additive manufacturing techniques that employ ultrasonic welding. Fabrisonic
The following is a lightly edited excerpt from an article titled Ultrasonic Welding Makes Parts for NASA Missions, Commercial Industry. It appears on the NASA/Jet Propulsion Laboratory website. The author is Margo Pierce, of NASA’s Goddard Space Flight Center, Greenbelt, Md.
A burst water main is always expensive and messy, but a pipe that fails in space can be mission-ending. That’s why NASA technologists work hard to make hardware as reliable as possible. Sometimes that means scrapping the old way of doing things and experimenting with a brand-new material—or fabrication process.
This challenge spurred Scott Roberts, a technologist at NASA’s Jet Propulsion Laboratory (JPL) in Southern California, to try a type of welding technology found in 3D printing. Called ultrasonic additive manufacturing (UAM), it’s already used by the private sector.
With some additional innovation, Roberts thought it could be used to improve reliability in heat exchangers, a crucial component of any spacecraft. Improvements one company made to its UAM process to help Roberts build better spacecraft are now beginning to pay off in industries from aeronautics to oil drilling.
“The problems I’m working on don’t solve one problem for one mission,” said Roberts. “They’re going to solve a class of problems for both NASA and industry.”
Dealing with temperature extremes in space
Temperature is particularly problematic in space, where extremes can vary by hundreds of degrees. Heat exchangers help maintain a steady temperature inside a spacecraft by removing excess heat or drawing in more. Traditionally, these devices include a long, snaking pipe attached to a metal plate with brackets and epoxy. Although effective, they consist of many interconnected parts, introducing many potential points of failure.
With ultrasonic additive manufacturing, however, the entire device can be crafted as a single piece. Small Business Innovation Research (SBIR) funding provided by JPL made it possible for Roberts to work with Columbus, Ohio-based Fabrisonic LLC on a new heat exchanger design.
As a subcontractor for Sheridan Solutions LLC, Fabrisonic started with an existing process that builds up multiple thin layers of metal by fusing them together with high-frequency vibrations. To create the heat exchanger, a curved channel is carved into the layered metal and then enclosed under additional layers.
The new design replaces dozens of small parts and joints that could fail during a long-term mission or under extreme conditions on Earth.
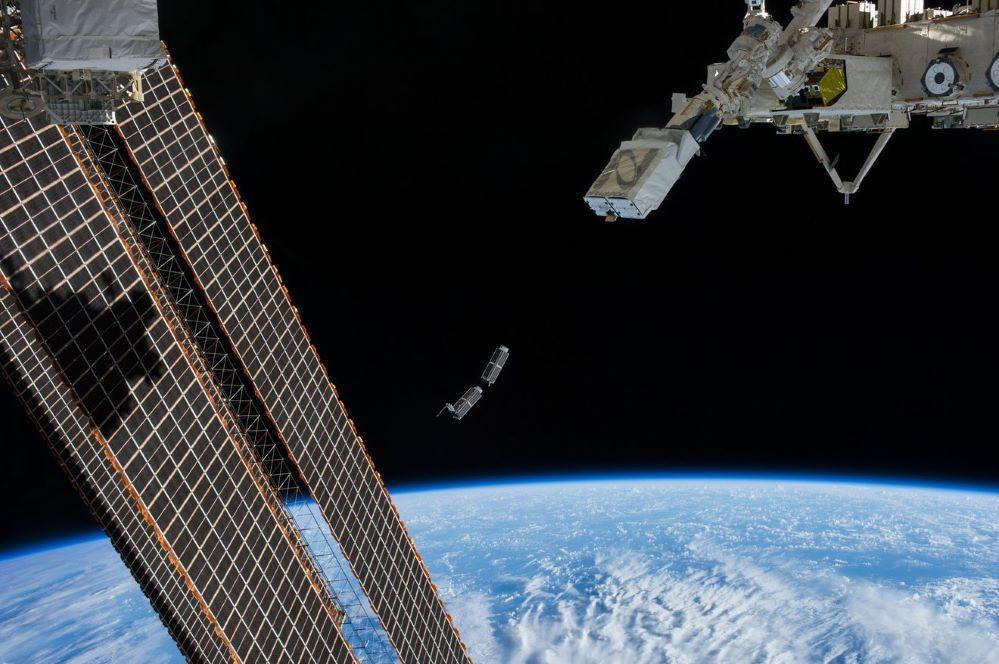
CubeSats can be used for a variety of tasks, but their small size makes it a challenge to fit all the parts as well as the shielding needed to manage the extreme temperatures of space. NASA is interested in manufacturing techniques that enable more efficient use of materials. NASA
How can vibrations fuse metal?
Ultrasonic welding uses sound and friction to create a solid-state bond between layers of metal. It begins with a thin foil pressed onto another metal component, such as a base plate. Constant pressure and ultrasonic vibrations cause friction between the facing sides, creating a shearing motion that raises temperatures and removes surface oxides, allowing direct contact of pure metal to pure metal. The result is a solid-state, atomic bond that welds layers of metal together.
Even layers of different metal can be bonded into a single piece. Relatively little heat is required because the bonding temperature for metals is significantly below their melting temperature.
Fabrisonic can piece together layers as large as six feet square, making it possible to create a part with a complex geometry in a matter of days instead of the months required by traditional fabrication practices.
Why combine different metals?
Protecting electronic components from intense space radiation that can destroy them is challenging when everything on a spacecraft needs to be lightweight. It’s one problem Roberts is trying to solve using novel materials. Additional SBIR funding provided by NASA’s Langley Research Center in Hampton, Va., paid for Fabrisonic to add layers of the radiation-resistant metal tantalum in the middle of aluminum spacecraft parts.
Unlike other forms of welding, UAM won’t cause the different metals to liquefy and mix together. Engineers can rely on the properties of each metal to remain constant and perform as expected, said Mark Norfolk, president of Fabrisonic. This quality demonstrated that NASA could realize its goal of combining the aluminum with tantalum.
The ability to meld layers of different metals also has advantages for customers in the oil and gas industry that rely on various Fabrisonic parts for drilling, Norfolk noted. One is a well drill pipe—a hollow, thin-walled tube that combines dissimilar materials and incorporates embedded sensors.
To read the entire article, click here.
Working with the private sector
NASA has a long history of transferring technology to the private sector. The agency’s Spinoff publication profiles NASA technologies that have been transformed into commercial products and services, demonstrating the broader benefits of America’s investment in its space program. For more information on how NASA brings space technology down to Earth, click here.
- Podcasting
- Podcast:
- The Fabricator Podcast
- Published:
- 04/16/2024
- Running Time:
- 63:29
In this episode of The Fabricator Podcast, Caleb Chamberlain, co-founder and CEO of OSH Cut, discusses his company’s...
- Trending Articles
- Industry Events
16th Annual Safety Conference
- April 30 - May 1, 2024
- Elgin,
Pipe and Tube Conference
- May 21 - 22, 2024
- Omaha, NE
World-Class Roll Forming Workshop
- June 5 - 6, 2024
- Louisville, KY
Advanced Laser Application Workshop
- June 25 - 27, 2024
- Novi, MI