- FMA
- The Fabricator
- FABTECH
- Canadian Metalworking
Our Publications
Categories
- Additive Manufacturing
- Aluminum Welding
- Arc Welding
- Assembly and Joining
- Automation and Robotics
- Bending and Forming
- Consumables
- Cutting and Weld Prep
- Electric Vehicles
- En Español
- Finishing
- Hydroforming
- Laser Cutting
- Laser Welding
- Machining
- Manufacturing Software
- Materials Handling
- Metals/Materials
- Oxyfuel Cutting
- Plasma Cutting
- Power Tools
- Punching and Other Holemaking
- Roll Forming
- Safety
- Sawing
- Shearing
- Shop Management
- Testing and Measuring
- Tube and Pipe Fabrication
- Tube and Pipe Production
- Waterjet Cutting
Industry Directory
Webcasts
Podcasts
FAB 40
Advertise
Subscribe
Account Login
Search
A new way to fabricate a heat exchanger
Ultrasonic additive manufacturing expands design options
- By Sue Roberts
- August 16, 2018
- Article
- Additive Manufacturing
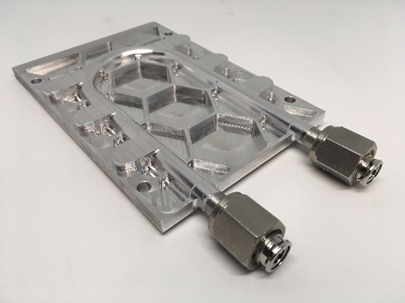
Figure 1. This heat exchanger built out of 6061 aluminum includes integrated channels for thermal management.. Photos courtesy of Fabrisonic LLC.
Thermal management devices are designed to monitor and protect products, equipment, and people from excessive heat. These heat exchangers wick heat away to keep things cool in diverse industries, such as electronics, aerospace, and chemical manufacturing. They come in all shapes and sizes, varying levels of complexity, and are built from an ever-expanding array of materials.
Before additive manufacturing (AM) was an accepted process, engineers relied on two common methods of producing heat exchangers—both still in use today. The first process, and possibly the simplest, calls for drilling cross channels in a thin structure and using screws to block channels and direct the coolant, creating the desired flow paths. The second process, which allows for more design flexibility, involves milling and brazing. The milling cuts channels in multiple parts, at times as many as six or seven, to create the flow path; then the parts are brazed together to complete the component.
Mark Norfolk, president of Fabrisonic LLC, said with AM as the production process, engineers have more design freedom because heat exchanges can be fabricated as a single part (see Figure 1). It also offers the ability to embed things like sensors in any location.
Many of the AM processes can deliver more design freedom when it comes to heat exchangers, but ultrasonic additive manufacturing (UAM) stands out because it’s a low temperature process (see Figure 2), according to Norfolk. When milling is added to the design mix, an engineer has even more design variables at his fingertips.
Fabrisonic’s SonicLayer™ hybrid machines combine UAM with CNC 3-axis precision milling to perform additive and subtractive processes in one setup (see Figure 3). Norfolk said that this combination makes it possible to create deep slots, hollows, lattices, honeycombs, and other complex structures with a milled finish on both internal and external surfaces. When producing heat exchangers, smooth surfaces on the channel walls help the coolant flow easily to provide consistent cooling.
“About half of our business is producing thermal management devices—from little microchannels up to panels over 5 feet long and 3 feet wide. Some of the very small devices are for cooling electronics. Some of the large panels are designed to cool aerospace vehicles. AM allows for the manufacture of very complex exchangers that incorporate features like a channel that begins with a ½-inch diameter and narrows down to a microthin passage,” Norfolk said.
“And the channels can be built so the flow goes exactly where cooling is needed. If you have electronics packages at positions X and Y, for example, the cooling can be directed exactly to those areas. You don’t have to push coolant sideways or in front or in back of the positions to get the cooling close to where it is needed.”
Layering Foils, Smoothing Surfaces
During the UAM process, metal foils from 0.005- to 0.010-in. thick are layered and ultrasonically welded together to achieve a solid metal part. The deposition temperature is below 250 degrees F.
Creating the UAM bond involves three steps that are performed while under constant force. First, surface oxides are broken up by the ultrasonic motion. Second, localized asperities yield and collapse, smoothing the surface. Third, heat and pressure promote diffusion and recrystallization at the interface of the two surfaces to complete a high-strength, solid bond built in a near net shape. Then the tool changer swaps the printing head for the appropriate end mill and CNC milling takes over to produce specified features and finish the surfaces.
“For most heat exchangers, you want smooth cooling passages. Using our hybrid equipment, both the internal and external passages are touched by the CNC mill. We print just a little extra material and mill it to assure that the tolerances and surface finishes of the heat exchanger are exactly what the engineers are looking for,” Norfolk said.
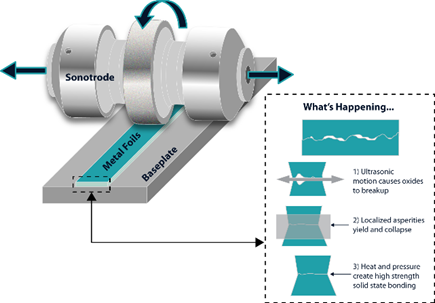
Figure 2. During the UAM process, a welding head rolls over foil feedstock while vibrating left to right about 30 microns. The scrubbing action breaks up oxides and collapses local asperities creating a solid-state weld.
Printing some complex geometries can be a challenge, but those challenges lead to further technology developments.
“Underhangs in an internal geometry have been the most difficult feature to print because when we weld the layers we push down with a little force and we need something to push back. Our answer to the problem was to develop a water-soluble support material. We fill the gaps with that material, weld over it while building up the part, and then flush the component with water. That material goes away leaving the specified metal characteristic,” Norfolk said.
Mixing Metals and Embedding Materials
The low temperature of the UAM process allows for bonding of dissimilar materials and embedding sensitive items within the metal. Materials like nickel, aluminum, copper, and steel can be securely joined, giving engineers the option of specifying different metals within a single part to accommodate specific needs.
“An area of copper can be used to draw heat away from a header or device, and the rest of the structure can be aluminum to reduce weight. Or we may print an aluminum part, add layers of tantalum (which is a great neutron absorber) and then add layers of titanium to catch some other radiation frequencies,” Norfolk said.
Most sensors, wires, and fibers survive being embedded in the metal because of the low process temperatures.
“We do a lot of work that involves embedding thermal couples and fiber-optic sensors. We can embed a single fiber-optic cable that is several feet long throughout a part to collect strain or temperature data from anywhere along the fiber. That can turn the entire part into a sensor,” Norfolk said.
“Thermal sensors were planted in components that were placed about 0.02 in. from an internal mixing chamber for a chemical mixing company. That gave them the ability to monitor the exact temperature of the chamber so they had a finer control over the process. The end result was that they were able to speed up the mixing process and gain about 10 percent efficiency.”
Much of the company’s current research involves embedding of nonmetallic materials within the layers of metal to create specific material characteristics.
“A big portion of research right now involves adding ceramic fibers to the layers of metal: Think about rebar in concrete. We are embedding ceramics in aluminum, copper, or steel to get higher performance out of the component. There is one ceramic that is about five times stronger than aluminum, so we mix ceramic fibers—up to 5 to 10 percent of the component’s weight—to give a strength and fatigue advantage.”
Working with NASA
Overseeing heat exchangers that monitor and protect sensitive, on-board electronics from the temperature extremes of space is one of the tasks of NASA’s Jet Propulsion Laboratory (JPL). The devices can be as small as 3 by 3 in. or as large as 3 by 3 ft. For many years, tubes that were bent and epoxied along the outside of the vehicles acted as the heat exchangers.
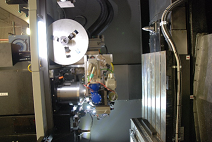
Figure 3. Adding an ultrasonic weld head as a tool in a traditional CNC mill’s tool changer transforms the machine with additive and subtractive capabilities. The SonicLayer 4000 completes parts up to 48 by 24 in.
During a four-year-long program, Fabrisonic and its affiliate EWI worked with JPL to develop heat exchangers to position the loops that hold the pumped coolant within the structures being cooled.
“We made upwards of 100 parts throughout the program,” Norfolks said. “At the end, we had developed a series of parts that went through qualification test runs including thermal cycling, helium leak checks, and vibration and abrasion tests. The launch loads from a Saturn V rocket were recreated for these test procedures. The heat exchanger weight was reduced, performance was better than previous exchangers, and the UAM exchangers themselves were manufactured faster.
“Now, we are starting to talk about production parts. UAM is still a new technology, which can be viewed as a risk, but we are taking the right steps to mitigate those risks. When there is a question, we try to answer it. We are starting to open some eyes at NASA.”
A full-size, functioning heat exchanger prototype (see Figure 4)has been produced in preparation for the Mars 2020 rover mission.
Combining Functions
A design engineer has to be a little creative to take full advantage of using AM for heat exchanger production. That means looking beyond cooling.
“The biggest bang for your buck is when you can combine functionalities. We built a part for a satellite that had three distinct functions. It was carrying a load, so it was structural. It had some heavy metals—things like tantalums and titaniums—for radiation shielding. And it had cooling passages integrated into it so it was a thermal device,” Norfolk said.
“Previously there were three separate parts. Using the additive process, all functions could be built into one component. There were efficiencies in reduced weight and higher overall performance,” he continued. “It’s when designs build in functions beyond cooling that we see the heat exchanger home runs.”
About the Author
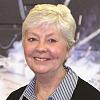
About the Publication
- Podcasting
- Podcast:
- The Fabricator Podcast
- Published:
- 04/16/2024
- Running Time:
- 63:29
In this episode of The Fabricator Podcast, Caleb Chamberlain, co-founder and CEO of OSH Cut, discusses his company’s...
- Trending Articles
- Industry Events
16th Annual Safety Conference
- April 30 - May 1, 2024
- Elgin,
Pipe and Tube Conference
- May 21 - 22, 2024
- Omaha, NE
World-Class Roll Forming Workshop
- June 5 - 6, 2024
- Louisville, KY
Advanced Laser Application Workshop
- June 25 - 27, 2024
- Novi, MI