Contributing Writer
- FMA
- The Fabricator
- FABTECH
- Canadian Metalworking
Categories
- Additive Manufacturing
- Aluminum Welding
- Arc Welding
- Assembly and Joining
- Automation and Robotics
- Bending and Forming
- Consumables
- Cutting and Weld Prep
- Electric Vehicles
- En Español
- Finishing
- Hydroforming
- Laser Cutting
- Laser Welding
- Machining
- Manufacturing Software
- Materials Handling
- Metals/Materials
- Oxyfuel Cutting
- Plasma Cutting
- Power Tools
- Punching and Other Holemaking
- Roll Forming
- Safety
- Sawing
- Shearing
- Shop Management
- Testing and Measuring
- Tube and Pipe Fabrication
- Tube and Pipe Production
- Waterjet Cutting
Industry Directory
Webcasts
Podcasts
FAB 40
Advertise
Subscribe
Account Login
Search
Properties of structural aluminum
Aluminum stands tall as a structural metal
- By Randy Kissell
- Updated September 6, 2023
- November 7, 2002
- Article
- Aluminum Welding
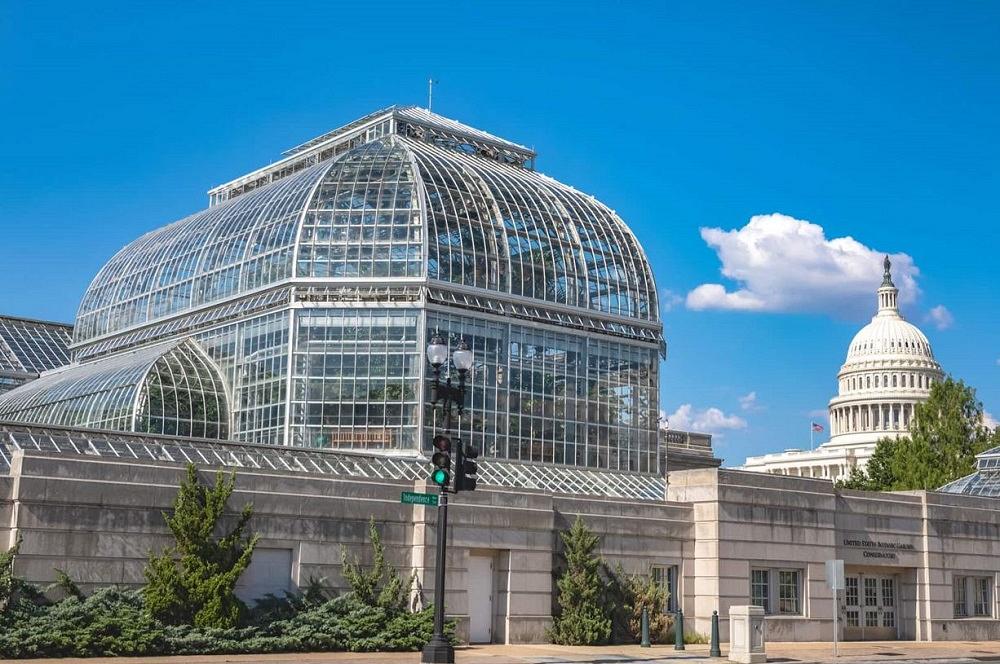
The whole Palm House roof had to be fabricated off-site, then lifted and set on the support structure, so it had to fit perfectly. The accuracy of the measurement and fabrication of all of those aluminum members in the roof was critical. The new roof was transported to Washington, D.C., where it was reassembled, mounted, and attached to the rest of the structure.
In appearance, aluminum sometimes is difficult to distinguish from other rust-free structural metals such as stainless steel, magnesium, and even galvanized steel. However, its properties are very different. Even different aluminum alloys can have dissimilar characteristics.
Aluminum is a popular choice in construction applications, found in everything from cryogenic vessels and piping to bridge guardrails and curtain walls used to clad office buildings. Because the material is more costly than carbon steel, however, it’s important to understand aluminum's structural properties and efficient aluminum structural design.
Aluminum History 101
After oxygen and silicon, aluminum is the most plentiful element in the earth's crust and the most common metal. Even so, aluminum was discovered much later than most other metals, including iron and copper, because in its natural state it is so tightly bonded to other elements.
In 1807, the English chemist Sir Humphry Davy named it aluminum after alumine, the metal of clay whose existence was theorized by the Romans. While Davy successfully isolated other previously undiscovered elements such as potassium, it wasn't until 1825 that the Danish chemist Hans Oersted became the first to isolate aluminum.
Aluminum was still a precious metal when American Charles Hall and French chemist Paul Heroult independently discovered an electrolytic process for producing aluminum in 1886. Both received patents for this method, which required large amounts of power but was much less costly than earlier chemical reduction techniques. Through this discovery and improvements in the production of aluminum oxide from aluminum-bearing ore, the modern aluminum industry was born in the 1890s.
Structural Aluminum—It's Not Just One Thing
The early metallurgists found aluminum to be very light in its pure state—0.1 lb. /in.3, about one-third the weight of an equal volume of steel. It also was formable and corrosion-resistant because its oxide was very hard and blocked further oxidation once it formed on the metal's surface. However, it was not as strong as steel, only about 10,000 PSI. Perhaps even more significant, aluminum’s modulus of elasticity—a measure of its stiffness and buckling strength when compressed—was also about one-third that of steel.
To counter some of these shortcomings in the decades following the discovery of the Hall-Heroult process, metallurgists alloyed aluminum with small quantities of other elements (usually less than 5% by weight) to produce aluminum alloys with much improved strengths.
Around 1910, it was discovered that adding small amounts of copper to aluminum produced alloys with strengths greater than steel. These alloys, called duralumin, were used by the Germans in the Zeppelin airship frames. Unfortunately, the name duralumin turned out to be a bit of an overstatement because these alloys proved to be the least corrosion-resistant of the aluminum alloys. By the 1920s, aluminum-magnesium and aluminum-magnesium-silicide alloys were developed; while they provided slightly less strength than the aluminum-copper alloys, they suffered much less loss of corrosion resistance compared to pure aluminum than duralumin.
In 1954, The Aluminum Association, an industry association of U.S. aluminum producers, adopted a naming system for the numerous aluminum alloys that had been developed (see Figure 1). This designation system has been accepted by most aluminum-producing nations of the world.
Strengthening Aluminum by Cold-Working
Aluminum, like other metals, also can be strengthened by cold-working, although this comes at the cost of ductility. Around the time metallurgists began alloying aluminum, they also found that some aluminum alloys could be strengthened by various heat treatments. The combination of alloying, cold-working, and heat treatment produces the various aluminum alloys and tempers used today. The temper designation (also developed by The Aluminum Association) is used as a suffix after the alloy designation and reveals how the metal has been cold-worked or heat-treated (see Figure 2).
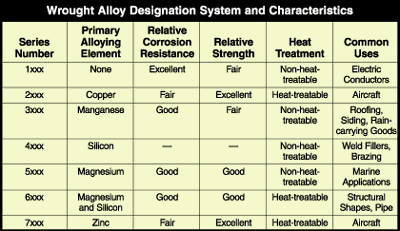
FIGURE 1. In 1954, The Aluminum Association, an industry association of U.S. aluminum producers, adopted a naming system for the numerous aluminum alloys that had been developed.
Properties of all the common aluminum products can be found in the Aluminum Association's “Aluminum Standards and Data.”
Extrusions May Eliminate Need for Other Operations
As with other metals, aluminum is sold in many different product forms, including castings, forgings, wire, rod, and bar. For construction applications, however, more than 90% of the aluminum materials used are flat-rolled sheet and plate and extrusions.
While flat-rolled material may be familiar to most metal fabricators, extrusions may not. Aluminum can be heated and pushed through an opening, with the same outline as the cross-sectional shape of the product. The resulting form is called an extrusion. While some other metals can be extruded, aluminum can be extruded in the greatest variety of shapes and alloys of any metal. Even hollow aluminum shapes can be extruded.
Even though aluminum's light weight and corrosion resistance often are cited, extrudability is the most important reason aluminum is used in construction applications. Extrusions may eliminate the need for many cost-intensive fabrication operations, such as welding and machining, that are required to make prismatic members with complex cross sections in other materials.
There are limitations, of course. Extrusions usually are limited in size to those shapes that fit within a circle of the diameter of the press that pushes the metal. Presses available for construction applications are limited to 18 in. dia., and extrusions made on smaller presses usually are less expensive.
Extrusion shapes can be custom-designed, or a shape can be produced from an open die (one that's available for anyone's use). Extruders provide catalogs of open die shapes, which include channels, angles, I beams, rectangular and round tubes, Ts, and Zs. Custom-designed shapes are limited to those shapes that are practical to extrude. This means that in addition to fitting within the extrusion press diameter, the shape must not contain abrupt transitions in geometry, such as very thin parts connected to thick parts. A rule of thumb is to limit the ratio of thickness of thick-to-thin parts to 2-to-1.
Welding Aluminum
Welding aluminum is tricky for several reasons. First, the tenacious aluminum oxide layer that rapidly forms on aluminum products has a much higher melting point than the base metal and must be carefully removed before welding. Welders who are more familiar with steel or who are in a hurry sometimes overlook this and get poor results.
The antidote for such problems is to weld in accordance with an established welding code, such as the American Welding Society's D1.2, “Structural Welding Code—Aluminum.”
Second, many aluminum products rely on cold-working or heat treatments for their strength. The heat that is created during welding reverses these effects, reducing the metal to its annealed (and weakest) condition. Only aluminum alloys that principally derive their strength from their alloying elements (such as the 5xxx series) can avoid this fate. Designers must account for the weakened metal at the weld, called the heat-affected zone (HAZ).
Case Study: The U.S. Botanic Garden Conservatory
While aluminum is considered by some to be lightweight, suitable for structures no more robust than beverage cans, it is used successfully in many significant structures.
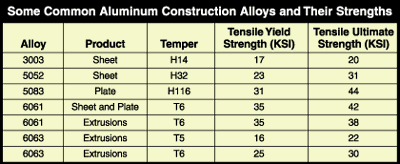
FIGURE 2. The temper designation developed by The Aluminum Association is used as a suffix after the alloy designation and reveals how the metal has been cold-worked or heat-treated.
One of the first uses of aluminum in a building application was in the U.S. Botanic Garden Conservatory, built in the early 1930s in Washington, D.C. The conservatory was built from the new (at that time) aluminum-copper alloy duralumin. Even though the copper comprised only a few percent of the alloy, it increased the alloy’s strength roughly fourfold.
At the center of the garden, rolled aluminum structural shapes were riveted together to form a great glass-clad structure called the Palm House, rising 78 ft. above the conservatory floor and enclosing a footprint approximately 90 ft. long by 90 ft. wide.
In addition, aluminum was used to frame adjacent conservatories called low houses. The inside environment was humid, while the framing outside was subjected to all the variations of the local weather, including snow.
By the early 1990s, the conservatory and adjacent buildings were in poor repair. Six decades of service and exposure had deteriorated the aluminum. In fact, duralumin had proven to be the least durable of the aluminum alloys. By the 1940s, other, more durable aluminum alloys were in use instead.
The design challenge was to build the new aluminum conservatory with modern methods, but to make it look like the original structure using some of the same construction types that had been used in the 1930s. When the architect began the rehabilitation project in 1999, he called for aluminum to be used again in the conservatory framing. At first, he planned to salvage some of the original members, but later decided to replace them all instead because the original beams had deteriorated.
Not only was the original alloy no longer used in building applications, but riveting had been replaced by welding and bolting.
Aluminum alloys such as aluminum-magnesium that get their strength from the alloying elements do not lose their strength when heated during welding. However, the 6061-T6 alloy that the conservatory architect specified gets its strength from a heat-treatment process. Welding weakens the HAZ, reducing the strength by 40%. So the engineer had to consider the length limitations of aluminum beams and columns (typically 25 ft. from a warehouse and 40 ft. from a mill) to position the welds so that the member still was relatively efficient despite the strength reduction in the HAZ.
In the 78-ft. tall Palm House, some members are longer than 25 ft., so they had to be fabricated from two pieces shop-welded near the center. Welding at midheight is much more critical, because doing so weakens columns more than at the ends. Where there was a weld at midheight, or farther than 5% of the length of the beam from the end, the member had to be designed as if it were all-welded material at that lower strength.
For example, the original construction had included the frequent use of back-to-back angles to support the columns to a horizontal member. To compensate for the weakened state of the aluminum in the HAZ, the angles had to be larger or deeper than they would have been without welds in the member. Instead of using a 1/4-in.-thick, 4- by 4-in. angle, a 3/8-in.-thick, 4- by 6-in. angle might have been used.
Forming the Structural Members. The original aluminum members in the conservatory were hot-rolled, a process in which a hot, almost molten rectangular bar is pressed by a series of rolls into shapes such as an I beam or channel. Steel structural shapes traditionally have been formed by hot rolling. That same process had been used for aluminum also until after World War II, when a method called extruding was developed.
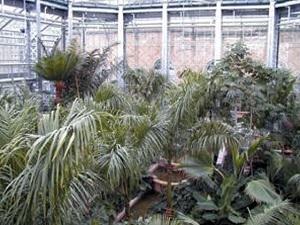
The Palm House, a great glass-clad structure rising 78 feet above the conservatory floor, houses exotic plants from around the world. The inside environment is humid, while outside the framing is subjected to all the variations of the local weather, including snow.
With extrusions, metal is formed similarly to the way toothpaste is squeezed out of a tube. Aluminum's formability makes it especially suitable for extrusion. Today, aluminum structural shapes, including I beams, channels, and angles, primarily are formed by extruding. In appearance, they are indistinguishable from shapes formed by roll forming but are more cost-effective for aluminum applications. Most of the new members in the conservatory are extruded shapes.
One notable exception was the use of roll forming for the aluminum columns that curve to meet the roof. That was a delicate process because the members had to be curved to the correct radius to join horizontal members at the top. In addition, the columns are very visible, so care had to be taken to make sure the columns were not scored or marred as they went through the rolling mills.
Reassembling the Buildings. Although almost all of the aluminum members were replaced, the corner steel columns were salvaged. Mating the new aluminum roof structure with the old steel column structure was difficult.
The whole Palm House roof had to be fabricated off-site, then lifted and set on the support structure, so it had to fit perfectly. The accuracy of the measurement and fabrication of all those aluminum members in the roof was critical.
The old roof was measured, then refabricated. The new roof had to be measured several different ways to be sure that it was square across its base and that the various accumulated tolerances on all the parts or some possible misfabrications had not altered the dimensions. Then it had to be disassembled; put on trucks; and transported to Washington, D.C., where it was reassembled, mounted, and attached to the rest of the structure.
The corners of the curved pieces were fastened together with austenitic stainless steel bolts. The bolt metal had to be chosen wisely because the use of dissimilar metals can create problems with galvanic corrosion caused by differences in the electrical potential of different metals. Austenitic stainless steel is fairly strong and compatible with aluminum.
Axial Tension and Compression, Bending. Structural members in the new conservatory include members of virtually every type. Truss bottom chords in the top of the Palm House are in axial tension under snow loads; aluminum columns around the perimeter are in compression; and purlins between the roof trusses and throughout the conservatory act as beams, subjected to bending and shear.
Trusses expand across the center Palm House, slanting top chords on either side, with a triangulated latticing in between the top chord and the bottom chord. The bottom chord goes straight across the base of the roof.
The aluminum columns for the Palm House also were required to support bending loads as they were angled to horizontal, connecting to the top of vertical steel columns around the Palm House perimeter. The bending loads also can cause buckling because they cause compression in half of the member cross section and tension in the other. For each half, the design is similar to that for members in pure axial tension and axial compression.
In the low houses that surround the Palm House, purlins are pitched to form the roof. If snow accumulates, it puts those purlins in bending, because the snow effectively is a load that is transverse to the length of the purlin.
For prismatic members such as the bottom chord members of the Palm House trusses, if the load surpasses the capacity, rupture will occur first at bolted connections at the ends of the members, since the bolt holes reduce the cross section there, making a weak point.
This problem had to be accounted for in the design by referencing that reduced area as the cross-section member in question. For the 6061-T6 alloy, the minimum specified tensile strength is 38,000 PSI. The area of the cross section reduced by the hole was multiplied by 38,000 PSI to calculate how many pounds the member could support.
About the Author
Randy Kissell
TGB Partnership
1325 Farmview Road
Hillsborough, NC 27278
919-644-8250
subscribe now
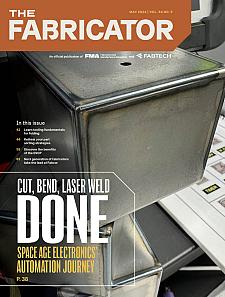
The Fabricator is North America's leading magazine for the metal forming and fabricating industry. The magazine delivers the news, technical articles, and case histories that enable fabricators to do their jobs more efficiently. The Fabricator has served the industry since 1970.
start your free subscription- Stay connected from anywhere
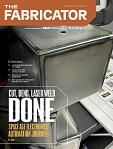
Easily access valuable industry resources now with full access to the digital edition of The Fabricator.
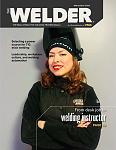
Easily access valuable industry resources now with full access to the digital edition of The Welder.
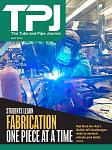
Easily access valuable industry resources now with full access to the digital edition of The Tube and Pipe Journal.
- Podcasting
- Podcast:
- The Fabricator Podcast
- Published:
- 04/16/2024
- Running Time:
- 63:29
In this episode of The Fabricator Podcast, Caleb Chamberlain, co-founder and CEO of OSH Cut, discusses his company’s...
- Industry Events
16th Annual Safety Conference
- April 30 - May 1, 2024
- Elgin,
Pipe and Tube Conference
- May 21 - 22, 2024
- Omaha, NE
World-Class Roll Forming Workshop
- June 5 - 6, 2024
- Louisville, KY
Advanced Laser Application Workshop
- June 25 - 27, 2024
- Novi, MI