Contributing Writer
- FMA
- The Fabricator
- FABTECH
- Canadian Metalworking
Categories
- Additive Manufacturing
- Aluminum Welding
- Arc Welding
- Assembly and Joining
- Automation and Robotics
- Bending and Forming
- Consumables
- Cutting and Weld Prep
- Electric Vehicles
- En Español
- Finishing
- Hydroforming
- Laser Cutting
- Laser Welding
- Machining
- Manufacturing Software
- Materials Handling
- Metals/Materials
- Oxyfuel Cutting
- Plasma Cutting
- Power Tools
- Punching and Other Holemaking
- Roll Forming
- Safety
- Sawing
- Shearing
- Shop Management
- Testing and Measuring
- Tube and Pipe Fabrication
- Tube and Pipe Production
- Waterjet Cutting
Industry Directory
Webcasts
Podcasts
FAB 40
Advertise
Subscribe
Account Login
Search
Pulse welding: What is it?
Cost-effective, portable, high-deposition joining of thick materials made possible
- By Rhonda Zatezalo and Ryan Kondrat
- Updated March 1, 2024
- December 10, 2018
- Article
- Arc Welding
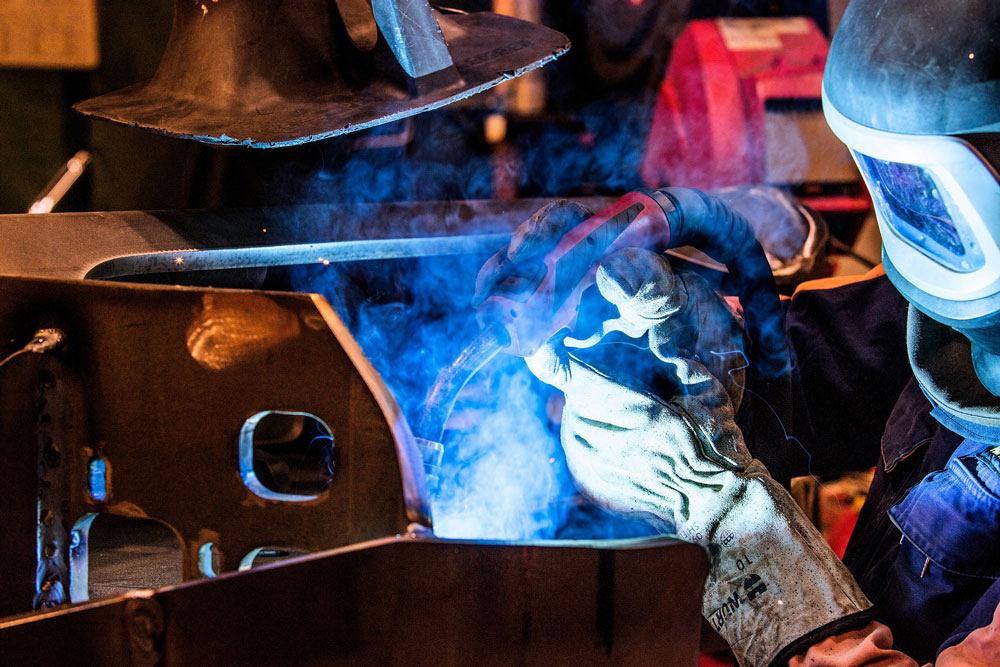
In applications that require high deposition rates, pulse welding reduces heat input, even with cored wires. Because the arc current is pulsed, the total average current is lower than with a conventional spray arc.
Welding thick metals with large joints commonly found in heavy industry and equipment manufacturing often requires a process that can produce high deposition rates. Two of the most common processes are spray-arc gas metal arc welding (GMAW) and submerged arc welding (SAW). While both processes have many advantages, they share one disadvantage—they are limited to welding in the flat and horizontal positions.
In the real world, life isn’t flat. Joints are located out of position and hard to reach, or it isn’t plausible to rotate the large parts and subassemblies this type of fabrication requires. Pulse welding can provide a solid option for these situations, and it is the best option in others. Why? And how do you determine which method is best for your application?
What Is Submerged Arc Welding?
During SAW, a layer of flux covers the arc and weld joint. While the process provides a smooth, finished weld without spatter, and with little or no smoke covering, it’s the flux covering that makes it feasible on flat or horizontal joints only. Additional drawbacks include expensive and large equipment, and the flux and slag can be messy.
The covered arc reduces the chance of arc flash, making it a safer option for employees’ eyesight, but it also limits the operator’s view of the finished piece and removes the immediate opportunity to adjust the arc midprocess. After a few inches the slag will break off, exposing the weld, and the operator can make adjustments as needed.
This type of welding may be the best choice for some applications, but in confined spaces, the size of the equipment and need to maneuver parts may not allow for access to the weld joint.
What Is Spray-Arc Welding?
Spray-arc welding has the same position limitations as SAW but for different reasons. In spray-arc, the droplet application happens just as it sounds—through a spray action. The arc produces a constant stream of tiny droplets, resulting in a more fluid weld pool. Gravity assists the process in a flat and horizontal position, but in any other position the puddle can shift before the weld pool solidifies. In the horizontal or flat position, spray-arc has great penetration profiles, can lay down a lot of material, and allows for high travel speeds. Using a flux-core wire can assist with holding the weld pool in place but requires postweld cleaning to remove the slag.
Cored wires are another option for high-deposition welding, but they are more expensive than solid wire. Many fabricators use flux-cored or metal-cored wires because of their ability to weld “dirtier” steels—those with higher levels of mill scale, rust, or oil. One problem with using cored wires is the amount of fumes they produce. Studies show that welding fumes such as manganese, iron oxide, and hexavalent chromium may cause significant health problems, requiring expensive fume removal systems or welding outside where fumes can disperse. Switching to solid wire will reduce the fume generation, but welding with pulse lowers fume generation significantly.
What Is Pulse Welding?
Pulse welding is a modification of the spray-arc process that varies the electrical output of the power source to form and detach a single droplet at a time. Once the droplet is formed in the higher peak current, the output decreases and the droplet is detached, pushing the molten metal into the weld puddle. The precise increase and decrease reduces heat input and spatter without sacrificing proper penetration. Based on the waveform, or synergic line, this process can occur as many as 400 times per second.
Pros to Pulse. GMAW with pulse has become the standard for low-heat-input, low-spatter welding for many applications. The new adaptable power supplies can be less expensive than a SAW machine and often can integrate pulse capability into machines that weld with standard spray arc. Modern power sources that offer pulse capability can be as compact as a small suitcase, eliminating the need for a bulky sub arc system, while maintaining high travel speed ability. Pulse welding is a precision process without messy flux slag that produces little spatter and low fumes.
Pulse welding for heavy deposition reduces the overall heat, even with cored wires. Because the arc current is pulsed, the total average current is lower than with a conventional spray arc, providing less heat input. In most applications, pulse has excellent penetration profiles, but some require specialized processes for the best possible weld.
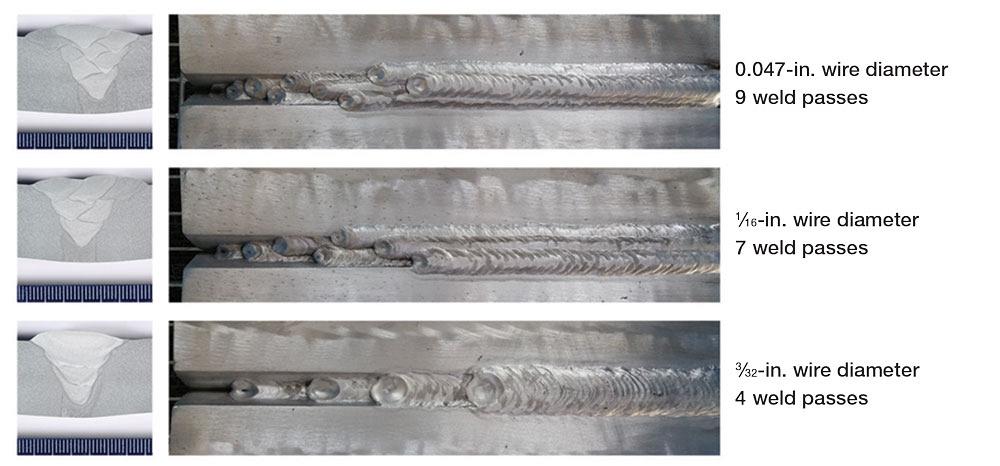
When performing heavy-deposition aluminum welding, consider using pulse welding with large-diameter wires. The increased weld volume from the 3⁄32-in. wire reduces the number of weld passes necessary, increasing welding speeds by up to 20 percent. Photo courtesy of Safra S.p.A.
So why aren’t more fabricators and manufacturers using solid wire with pulse welding for high-deposition jobs? The answer is simple: There isn’t a lot of information available about the process for heavy fabrication. Many assume it requires specialized equipment or that it’s difficult to set up, requiring experienced welding professionals. With modern-day welding inverters, this isn’t the case. In fact, several options on the market allow for multiple processes to be used and offer synergic functionality for easy parameter adjustment.
Sometimes pulse isn’t the best answer. When the application requires flux-core wire, the benefits of pulse are negligible. With the exception of T-5 flux-core wires, most do not improve welding performance using a pulsed arc. With solid-steel wires greater than 5⁄64 in., the peak current necessary to create the droplet becomes extremely high, so a standard spray-arc process is required. But most of the time it’s clean, fast, cost-efficient, and can use equipment shops may already have on hand.
Advanced Pulse Processes and Other Options. New advanced processes modify pulse even further to provide consistently better penetration with less undercutting. These processes stabilize penetration and arc length, adding controls that stop the change in current automatically when the contact-tip-to-workpiece distance changes. By stabilizing the current through changes in distance, operators can eliminate problems such as lack of fusion and burn-through. Some machines actively adjust the voltage and current through wire movement during welding to stabilize the arc and penetration profile, making minute changes through the application to provide consistently solid welds.
Modern pulse machines provide high deposition during welding in several ways. When using pulse welding with solid wire, operators can extend the stick-out to get higher deposition with less heat input. Instead of welding with a stick-out of 5⁄8 inch, they can use 1 in. or 11⁄8 in. A higher stick-out drops the average current to increase the wire speed, using the same current as the shorter stick-out for higher deposition with the same heat input.
When performing heavy-deposition aluminum welding, operators should consider using pulse welding with large-diameter wires, which provides benefits in both time and cost savings. The increased weld volume from large-diameter wire reduces the number of weld passes necessary, increasing welding speeds by up to 20 percent.
Increased Deposition Rate With Dual Wire
Another alternative to consider for increased deposition rates is twin wire or dual wire. Twin-wire welding uses two arcs simultaneously. The pulses are offset 180 degrees to maximize the process stability. Also, one arc can pulse while the other is operating in standard constant voltage or spray. This process offers many benefits for high-deposition welding, including increased travel speed.
The Pulse Welding Learning Curve
Since pulse welding is no longer difficult to set up, most welders can use it regardless of their experience level. They can eliminate long hours under the hood to learn how to make more difficult welds because those welds are no longer as troublesome. The more experienced welders now have time to focus on challenging weld scenarios while the novices build their confidence and skills.
Equipment Versatility Is Key
The versatility of modern welding equipment is a boon to the heavy equipment manufacturing industry. In addition to advanced pulse processes, the welding machines also can perform spray and standard pulse. Synergic lines are configured to use all types of wires—including cored wires—with the pulse process.
Ryan Kondrat is senior application engineer of heavy fabrication at Fronius USA LLC, 6797 Fronius Drive, Portage, IN 46368, 219-734-5500, www.fronius.us.
Rhonda Zatezalo is a freelance writer for Crearies Marketing Design LLC, 248-783-6085, www.crearies.com.
About the Authors
Ryan Kondrat
Senior Application Engineer of Heavy Fabrication
219-734-5500
About the Publication
subscribe now
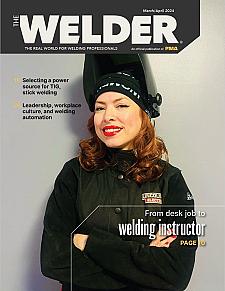
The Welder, formerly known as Practical Welding Today, is a showcase of the real people who make the products we use and work with every day. This magazine has served the welding community in North America well for more than 20 years.
start your free subscription- Stay connected from anywhere
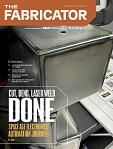
Easily access valuable industry resources now with full access to the digital edition of The Fabricator.
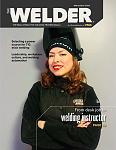
Easily access valuable industry resources now with full access to the digital edition of The Welder.
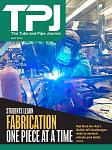
Easily access valuable industry resources now with full access to the digital edition of The Tube and Pipe Journal.
- Podcasting
- Podcast:
- The Fabricator Podcast
- Published:
- 04/16/2024
- Running Time:
- 63:29
In this episode of The Fabricator Podcast, Caleb Chamberlain, co-founder and CEO of OSH Cut, discusses his company’s...
- Trending Articles
Sheffield Forgemasters makes global leap in welding technology
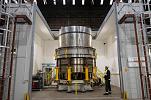
ESAB unveils Texas facility renovation
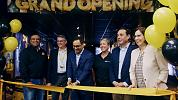
Engine-driven welding machines include integrated air compressors
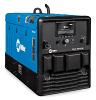
The impact of sine and square waves in aluminum AC welding, Part I
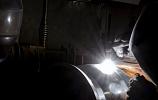
How welders can stay safe during grinding
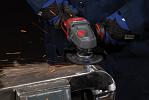
- Industry Events
16th Annual Safety Conference
- April 30 - May 1, 2024
- Elgin,
Pipe and Tube Conference
- May 21 - 22, 2024
- Omaha, NE
World-Class Roll Forming Workshop
- June 5 - 6, 2024
- Louisville, KY
Advanced Laser Application Workshop
- June 25 - 27, 2024
- Novi, MI