Sales and Applications Manager
- FMA
- The Fabricator
- FABTECH
- Canadian Metalworking
Categories
- Additive Manufacturing
- Aluminum Welding
- Arc Welding
- Assembly and Joining
- Automation and Robotics
- Bending and Forming
- Consumables
- Cutting and Weld Prep
- Electric Vehicles
- En Español
- Finishing
- Hydroforming
- Laser Cutting
- Laser Welding
- Machining
- Manufacturing Software
- Materials Handling
- Metals/Materials
- Oxyfuel Cutting
- Plasma Cutting
- Power Tools
- Punching and Other Holemaking
- Roll Forming
- Safety
- Sawing
- Shearing
- Shop Management
- Testing and Measuring
- Tube and Pipe Fabrication
- Tube and Pipe Production
- Waterjet Cutting
Industry Directory
Webcasts
Podcasts
FAB 40
Advertise
Subscribe
Account Login
Search
How to weld 300 series pipe without back purge welding
Reduce setup time, purge time, and gas use
- By Jim Byrne
- Updated December 7, 2023
- May 23, 2019
- Article
- Arc Welding
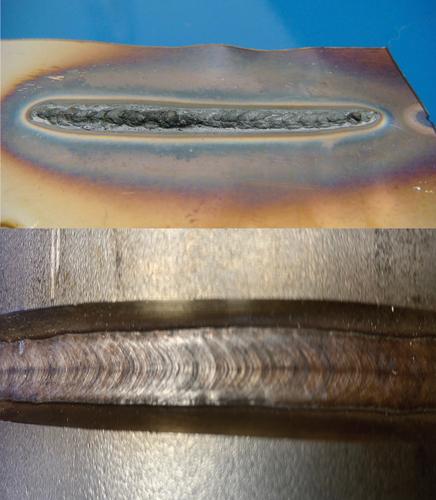
When welding 300 series stainless steels, contractors can eliminate back purging in open-root pipe welding and still achieve high weld quality.
Favored for their corrosion resistance and strength, stainless steel alloys are used for many pipe and tube applications, including oil and gas, petrochemical, and biofuels. While gas tungsten arc welding (GTAW) traditionally is used for many stainless steel applications, it has some drawbacks.
First, as the skilled welder shortage continues, finding workers knowledgeable in GTAW is an ongoing challenge. Second, GTAW isn’t the fastest welding process, which hinders companies that want to increase productivity to meet customer demand. Third, it requires a time-consuming and costly back purge on stainless steel tubes and pipes.
Back purging with argon gas is needed with shielded metal arc welding (SMAW) as well as GTAW, and the cost of the gas and the setup time for the purging process can be significant, especially as the pipe diameters and lengths increase.
When welding 300 series stainless steels, contractors can eliminate back purging in open-root pipe welding and still achieve high weld quality, retain the material’s corrosion resistance, and meet welding procedure specification (WPS) requirements by switching from traditional GTAW or SMAW to a modified short-circuit gas metal arc welding (GMAW) process. A modified short-circuit GMAW process also delivers additional benefits for productivity, efficiency, and ease of use that can help improve the bottom line.
What Is Back Purge Welding?
Purging is the introduction of a gas to remove contaminants and provide backing during welding. Back purging shields the back side of the weld, preventing the formation of heavy oxides that occur in the presence of oxygen.
When the back side isn’t protected during open-root pipe welding, it can result in a breakdown of the base material. This breakdown is known as sugaring, named because it results in a surface appearance much like sugar on the inside of the weld. To prevent sugaring, welders insert a gas hose into one end of the pipe and then block the ends of the pipe with purge dams. They also create a vent hole on the opposite end of the pipe. They usually tape around the joint opening, too. After they have purged the pipe, they peel back a section of the tape around the joint and begin to weld, repeating the process of peeling and welding until the root pass is complete.
Eliminating the Back Purge
Back purging can cost an operation substantial time and money, in some cases adding thousands of dollars to a project. Transitioning to a modified short-circuit GMAW process allows companies to complete root passes without a back purge in many stainless steel applications. Welding applications on 300 series stainless steels are good candidates for this, while welding applications for high-purity duplex stainless steel currently require GTAW for the root pass.
Keeping the heat input as low as possible helps to retain the corrosion resistance of the workpiece. Reducing the number of weld passes is one way to reduce heat input. A modified short-circuit GMAW process, such as Regulated Metal Deposition (RMD®), uses precisely controlled metal transfer to provide uniform droplet deposition. This makes it easier for the welder to control the weld puddle and, therefore, control heat input and welding speeds. A lower heat input allows the weld puddle to freeze faster.
With controlled metal transfer and faster puddle freezing, the welding puddle is less turbulent and the shielding gas exits the GMAW gun relatively undisturbed. This allows the shielding gas to push through the open root, displacing the atmosphere and preventing sugaring or oxidation on the back side of the weld. That gas coverage is needed only for a short time because the puddle freezes so quickly.
Testing shows that a modified short-circuit GMAW process meets weld quality standards while retaining the corrosion resistance of stainless steel just as well as when the root pass is welded with GTAW.
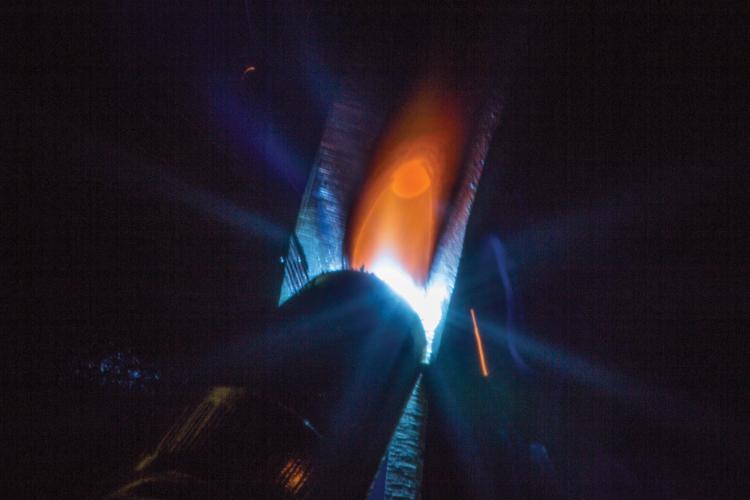
Using a modified short-circuit GMAW process for open-root pipe welding delivers other benefits for productivity, efficiency and welder training.
A change to the welding process does require a company to requalify its WPS, but the switch can offer tremendous payback in time and cost savings—both for new fabrication and repair work.
Using a modified short-circuit GMAW process for open-root pipe welding delivers other benefits for productivity, efficiency and welder training. These include:
- Travel speeds that are two to three times faster than traditional GTAW and SMAW processes.
The potential to eliminate the hot pass, a result of the ability to deposit more metal for increased root pass thickness.
Exceptional tolerance for high-low misalignment between pipe sections. Because of the smooth metal transfer, the process can easily bridge gaps of up to 3⁄16 inch.
Consistent arc length regardless of electrode stickout, which compensates for operators who struggle to hold a consistent stickout length. The easier-to-control weld puddle and consistent metal transfer can reduce training time for new welders.
Minimal cleanup time because the process leaves behind no slag and little spatter, if any.
Reduced downtime for process changeover. The same wire and shielding gas can be used for root, fill, and cap passes. A pulsed GMAW process can be used, provided that a shielding gas of at least 80 percent argon is used for the fill and cap passes.
Five Tips for Success When Switching to Short-Circuit MIG Welding
For operations that want to eliminate back purging in stainless steel applications, it’s important to follow five key tips for success when switching to a modified short-circuit GMAW process.
- Ensure a minimum root gap of 1⁄8 in. This allows the shielding gas to flow through and protect the back side of the weld from oxidation.
Clean the inside and outside of the pipe to remove any contaminants. Use a wire brush designed for stainless steel to clean at least 1 in. back from the edge of the joint.
Use a stainless steel filler metal with a high silicon content, such as a 316LSi or 308LSi. Higher silicon content helps the weld puddle wet out and acts as a deoxidizer.
For best performance, use a shielding gas mix that is formulated specifically to the process, such as 90 percent helium, 7.5 percent argon, and 2.5 percent carbon dioxide. Another option is 98 percent argon and 2 percent carbon dioxide. Welding gas suppliers might have other recommendations.
For best results, use a tapered tip and nozzle for the root pass to localize gas coverage. Tapered nozzles with built-in gas diffusers provide excellent coverage.
Note that using a modified short-circuit GMAW process without a backing gas does produce a small amount of oxide scale on the back side of the weld. This typically flakes off as the weld cools and is within the quality standards for oil, power plant, and petrochemical applications.
Jim Byrne is sales and applications manager with Miller Electric Mfg. LLC, 1635 W. Spencer St., Appleton, WI 54912, 920-734-9821, www.millerwelds.com.
About the Author
About the Publication
Related Companies
subscribe now
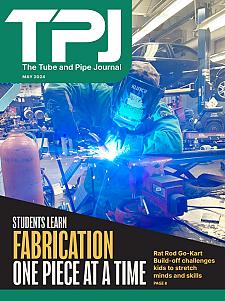
The Tube and Pipe Journal became the first magazine dedicated to serving the metal tube and pipe industry in 1990. Today, it remains the only North American publication devoted to this industry, and it has become the most trusted source of information for tube and pipe professionals.
start your free subscription- Stay connected from anywhere
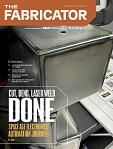
Easily access valuable industry resources now with full access to the digital edition of The Fabricator.
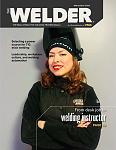
Easily access valuable industry resources now with full access to the digital edition of The Welder.
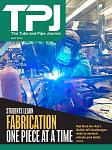
Easily access valuable industry resources now with full access to the digital edition of The Tube and Pipe Journal.
- Podcasting
- Podcast:
- The Fabricator Podcast
- Published:
- 04/16/2024
- Running Time:
- 63:29
In this episode of The Fabricator Podcast, Caleb Chamberlain, co-founder and CEO of OSH Cut, discusses his company’s...
- Trending Articles
Zekelman Industries to invest $120 million in Arkansas expansion
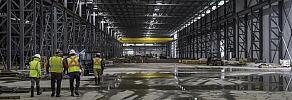
3D laser tube cutting system available in 3, 4, or 5 kW
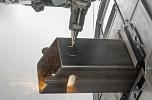
Corrosion-inhibiting coating can be peeled off after use
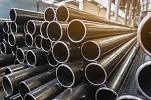
Brushless copper tubing cutter adjusts to ODs up to 2-1/8 in.
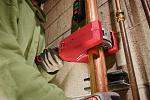
HGG Profiling Equipment names area sales manager
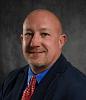
- Industry Events
16th Annual Safety Conference
- April 30 - May 1, 2024
- Elgin,
Pipe and Tube Conference
- May 21 - 22, 2024
- Omaha, NE
World-Class Roll Forming Workshop
- June 5 - 6, 2024
- Louisville, KY
Advanced Laser Application Workshop
- June 25 - 27, 2024
- Novi, MI