Contributing editor
- FMA
- The Fabricator
- FABTECH
- Canadian Metalworking
Categories
- Additive Manufacturing
- Aluminum Welding
- Arc Welding
- Assembly and Joining
- Automation and Robotics
- Bending and Forming
- Consumables
- Cutting and Weld Prep
- Electric Vehicles
- En Español
- Finishing
- Hydroforming
- Laser Cutting
- Laser Welding
- Machining
- Manufacturing Software
- Materials Handling
- Metals/Materials
- Oxyfuel Cutting
- Plasma Cutting
- Power Tools
- Punching and Other Holemaking
- Roll Forming
- Safety
- Sawing
- Shearing
- Shop Management
- Testing and Measuring
- Tube and Pipe Fabrication
- Tube and Pipe Production
- Waterjet Cutting
Industry Directory
Webcasts
Podcasts
FAB 40
Advertise
Subscribe
Account Login
Search
Clever racking design boosts lifelong powder coating coverage
Recreational products fabricator Lifetime meets high-volume, high-quality demand
- By Kate Bachman
- August 6, 2019
- Article
- Finishing
Lifetime Products, Clearfield, Utah, manufactures sturdy, durable metal and blow-molded plastic basketball sets, picnic and utility tables, chairs, sheds, swing sets, coolers, and playsets. “All of our backyard playsets are simple to set up and built to last,” the company promises.
Demand for the products is tremendous. The company manufactures and powder-coats more than 100,000 metal parts a day. It makes up to 13,500 folding chairs alone per day. Trying to meet that volume demand while achieving the quality standards required to make recreational products that are simple to set up and last a lifetime is no picnic.
“The volume of parts we have going through—that would be our biggest challenge for sure,” said Ryan Miller, powder coating manager for Lifetime. “All of our lines run at 14 to 18 feet a minute. Trying to keep up with the output is difficult.”
Meeting that challenge takes innovative engineering and a well-planned and well-executed powder coating process.
Challenge: Good Coverage, Fast
Lifetime categorizes its products into three separate systems, manufactured mainly in three buildings. Miller oversees operations of all three systems. “Each building houses what we call a family of product. A basketball set is made in one building, tables and chairs are made in another building, and in our third building we run playground and shed parts.”
The manufacturer organizes its production for kitting, performing subassembly and packaging each product unit at the end of an automated conveyor line for consumer final assembly.
Process. The parts are positioned on racks on the conveyors, which go through the mostly automated powder coat line. The conveyor system feeds the parts on the racks through a pretreatment system, a dryer oven, and then into powder booths.
The powder coat booth line is equipped with automated guns and two manual sprayers. The manual sprayers reinforce the part areas that are hard for the automated sprayers to reach. The conveyor moves the parts through continuous curing ovens, and finally into the assembly area, where personnel take the parts off and partially assemble and then package them.
Order. “In designing the production order, we usually start with the packaging design and work backwards,” said Brad McAllister, manufacturing engineer. “We look at how those parts are going to be placed in the package. We design unique racking so that when the parts come down the line, our assemblers can take a whole unit off of one rack in an orderly fashion, assemble them quickly, and box them ready to ship.”
One of the biggest engineering challenges has been designing the racking systems so that the automatic and manual powder coat sprayers can coat the parts thoroughly but also quickly. The metal parts are tubular, stamped, roll formed, and laser-cut. Each model, with different shapes, bends, and curves, must be sprayed at the same time.
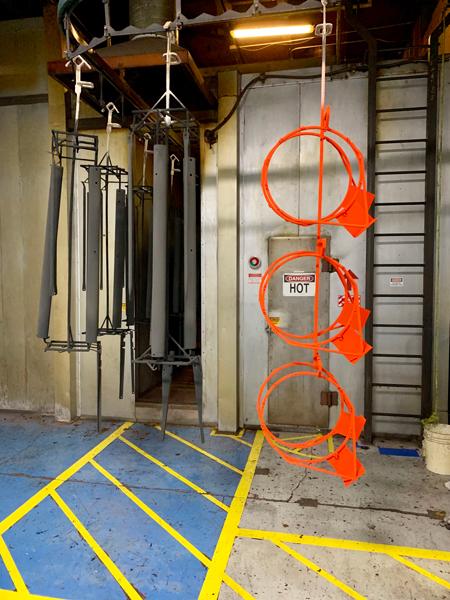
Parts getting different colors travel on one line, then are separated to proceed into their respective color booths, then are rejoined for curing and packaging.
What makes a part section difficult to spray? Bends with 90-degree or tighter angles. The interior of a long flange. The area of a part where the hook blocks the spray.
“Our technicians adjust the automated spray guns to try to get the appropriate spray patterns and deliver the correct air-to-powder ratio so the part gets adequate coverage. Then manual sprayers reinforce the remaining hard-to-reach areas,” Miller said.
Mils. “It’s important to get powder down into those blind spots so that there is adequate powder coverage. A too-light coating could propagate or promote rust in those areas. We have to make sure everything is covered, to have appropriate mils on it, so that we present a good product,” said Mike Seegmiller, powder coating technician.
Seegmiller said the mil thickness goal is 21/2 to 4 mils. “That middle range of 21/2 to 4 is very good. It’s where we can hit that requirement for the range of the product and still not be wastefully throwing powder out the door.”
Racking Line Speed
The engineers calculate the racking positions as methodically as FedEx calculates its delivery routes.
“How we present a part to the auto guns makes a big difference,” said Keith Maw, manufacturing engineer.
The density of the racking directly determines the throughput, so obviously they are positioned as densely as possible without overwhelming the manual powder coaters and assemblers. “It’s all about being able to put as many parts as we can on a rack as efficiently as possible, yet not overwhelm the powder coating booth’s ability to coat them and the employee’s ability to keep up with that,” Maw said. “It’s a balancing act; when we spread those racks further apart, we reduce the capacity of that line and it slows production down.
“You’d have a hard time walking through the line, but we have gapped out the individual racks so that the employees can keep up,” Maw continued. “As engineers, when we get a new product, we design how we’re going to hang it and what speed we’re going to deliver it to all the employees who are adding value to the product.
“We do a prototype of those racks and we put the parts on them. We do a mil check on them to make sure they’re getting the proper mil powder coverage on them. We also see how the employees can handle the spacing. If they can’t keep up with it, then we go back to the drawing board,” Maw said.
Some of the adjustments the engineers have made are to optimize the racking and parts so the automatic guns reach the maximum and for optimal ergonomic positioning for the employees.
McAllister added, “We try to face the difficult-to-reach areas toward the auto guns so that they can cover them. Instead of presenting them perpendicular to the guns, we turn the parts on an angle to allow the powder to flow through the rack and wrap around the parts.
“If parts are too high for shorter employees, we’ll bring them down lower on the rack where they can reach them,” he continued. “Parts that are long, we’ll put them up higher because the smaller or shorter employees can reach the lower area of that part, and take it off the rack to dissemble it. Parts that are heavy, we’ll usually put on racks by themselves so that an employee can handle them one at a time.”
Innate Ingenuity
Lifetime is no stranger to ingenuity. In fact, the company was born 33 years ago from the founder’s reinvention, called Quick Adjust®, of how a basketball set could be assembled and adjusted so that his kids could play with it. Lifetime’s founder Barry Mower devised a basketball unit that could be height-adjusted with a broomstick because his kids couldn’t reach the hoop. He also came up with the breakaway rim and a three-piece pole so that the whole unit could be packaged in one box.
Color Changes
Most of the parts are powder-coated in blocks of 500 to 1,000 units on a line. After those are coated, there is a small gap as the line is readied for the next block of models.
Offering a broad range of products makes multiple color changes a necessity. Lifetime is equipped with Nordson and Gema powder spray guns on its lines. “On our shed line we have a Nordson ColorMax® quick-changeover system that allows quick color changes. Before that we had a spray-to-waste booth,” said Seegmiller. “All of one powder color had to be emptied before another color could be added. It actually took six manual sprayers to coat our product on that line. Since we were able to switch to that, now we have only two.”
It is a flexible line, meaning different products’ parts, such as for tables and chairs, are run together simultaneously through the same color booths.
The company actually can run four colors at the same time on one main line, as for playgrounds, Miller said. The system works similar to a train spur. The parts split off from the main line and go through different booths for different color applications and then come together back on the main line.
“The hooks are fashioned so that one line grabs a part and it goes through a separate line of a different color and then transfers the part back onto the main line and through the cure oven. It’s pretty innovative. For visitors who look at the system, it’s kind of a jaw-dropper,” Miller said.
PCI 4000 Certification
The manufacturer sought the Powder Coating Institute’s PCI 4000 certification as both a goal and a knowledge resource, according to Miller. “The biggest reason we reached out for that was to make more resources available for us … and to be part of the powder coating community.” Seegmiller said that having the PCI auditor come out to the plant to provide some of his insights was especially helpful. The auditor individually audited each one of the lines, looking at the processes and how the company handles quality control.
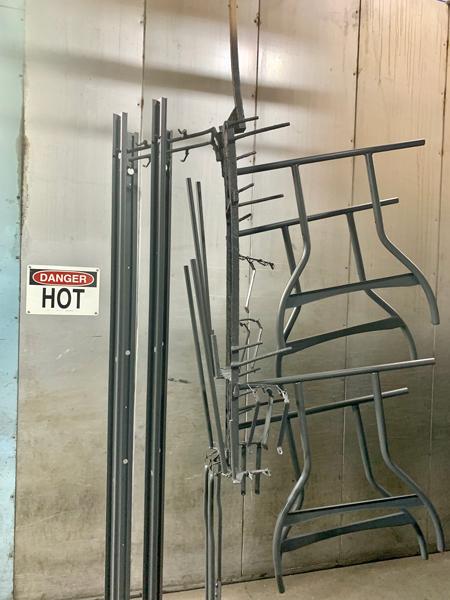
All parts are kitted so that they can be subassembled and packaged immediately at the end of the line, ready for the consumer. Can you tell which product these metal parts comprise?
“Some of the things he looked at were whether we had consistency in our process; mil consistency; how we store, use, and then track our powder. We have that all climate-controlled. He looked at how we do our PMs [preventive maintenance] on our equipment,” Seegmiller said.
Now others seeking the PCI 4000 have reached out to them to ask questions, he added. “It just opened up doors for us in that aspect.”
The company qualifies all of its powders before they are put into production. Test samples undergo 15 different tests, such as a 500-hour salt spray test. The salt spray test is performed in a lab to eliminate all other variables.
Endgame: Longevity and Dependable Strength
The finishing group relayed some funny stories from customers about alternative uses they’ve discovered for Lifetime’s products that demonstrate their strength and durability. One customer sent a photo of a swordfish he displayed on a Lifetime table. Another customer sent a photo of herself sledding on a folding table. Another customer used the basketball set as an engine hoist. “Some people send videos of themselves using our tables as surfboards and snow shovels. And we fed our cooler to a grizzly bear to see how it would fare,” Miller said.
Which won? The bear or the cooler? “The cooler, actually. We show a video on YouTube of a bear trying to get into a can of sardines in that cooler. He fought for quite awhile, but he couldn’t get it open. It’s certified bear-proof,” McAllister said. “Your food is safe in our coolers,” Maw added.
Photos courtesy of Lifetime Products
About the Author
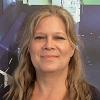
Kate Bachman
815-381-1302
Kate Bachman is a contributing editor for The FABRICATOR editor. Bachman has more than 20 years of experience as a writer and editor in the manufacturing and other industries.
Related Companies
subscribe now
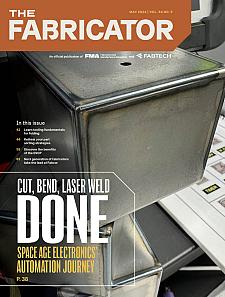
The Fabricator is North America's leading magazine for the metal forming and fabricating industry. The magazine delivers the news, technical articles, and case histories that enable fabricators to do their jobs more efficiently. The Fabricator has served the industry since 1970.
start your free subscription- Stay connected from anywhere
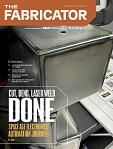
Easily access valuable industry resources now with full access to the digital edition of The Fabricator.
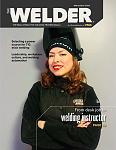
Easily access valuable industry resources now with full access to the digital edition of The Welder.
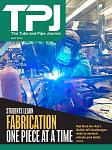
Easily access valuable industry resources now with full access to the digital edition of The Tube and Pipe Journal.
- Podcasting
- Podcast:
- The Fabricator Podcast
- Published:
- 04/16/2024
- Running Time:
- 63:29
In this episode of The Fabricator Podcast, Caleb Chamberlain, co-founder and CEO of OSH Cut, discusses his company’s...
- Trending Articles
Capturing, recording equipment inspection data for FMEA
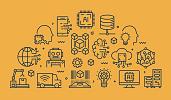
Tips for creating sheet metal tubes with perforations
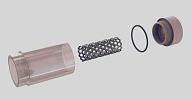
Are two heads better than one in fiber laser cutting?
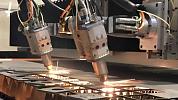
Supporting the metal fabricating industry through FMA
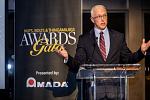
Omco Solar opens second Alabama manufacturing facility
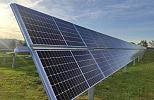
- Industry Events
16th Annual Safety Conference
- April 30 - May 1, 2024
- Elgin,
Pipe and Tube Conference
- May 21 - 22, 2024
- Omaha, NE
World-Class Roll Forming Workshop
- June 5 - 6, 2024
- Louisville, KY
Advanced Laser Application Workshop
- June 25 - 27, 2024
- Novi, MI