- FMA
- The Fabricator
- FABTECH
- Canadian Metalworking
Categories
- Additive Manufacturing
- Aluminum Welding
- Arc Welding
- Assembly and Joining
- Automation and Robotics
- Bending and Forming
- Consumables
- Cutting and Weld Prep
- Electric Vehicles
- En Español
- Finishing
- Hydroforming
- Laser Cutting
- Laser Welding
- Machining
- Manufacturing Software
- Materials Handling
- Metals/Materials
- Oxyfuel Cutting
- Plasma Cutting
- Power Tools
- Punching and Other Holemaking
- Roll Forming
- Safety
- Sawing
- Shearing
- Shop Management
- Testing and Measuring
- Tube and Pipe Fabrication
- Tube and Pipe Production
- Waterjet Cutting
Industry Directory
Webcasts
Podcasts
FAB 40
Advertise
Subscribe
Account Login
Search
Building in the frozen tundra
Southern Spear Ironworks designs, fabricates, and erects metal buildings from Chattanooga to the Antarctic
- By Sue Roberts
- January 29, 2019
- Article
- Shop Management
Becoming an established business, like erecting a building, requires the right tools … and time. Most of the time. Founding a recognized, full-service construction firm with steel fabricating capabilities in less than three years is a bit unusual.
Sean Compton, president of Southern Spear Ironworks in Chattanooga, Tenn., fast-forwarded through the typical timeframe to go from a small-time erection company run from his home to a structural steel shop that handles its own steel fabricating and pre-engineered metal building sales and erection (see Figure 1). Since February 2016 nearly 60 in-house employees and numerous subcontractors have joined the entrepreneur to make the company one of the largest steel contracting firms between Knoxville and Atlanta.
Add to that brisk pace the success of winning a five- to six-year design/build government contract to construct a research station, basically a small city, in a locale few people visit, much less call a workplace: Antarctica.
A former football fullback and tight-end player for Florida State University, where he played for Bobby Bowden and Jimbo Fisher while he was the offensive coordinator coach-in-waiting, Compton relates the company culture to a solid mix of philosophies that fall somewhere between those of the New England Patriots team and Google®. “Ironwork is one of the most dangerous, most difficult, most scrutinized, stressful businesses in the world. Moving forward and success for everyone involved requires give and take between the employer and employee [see Figure 2]. So, I try to run my company with a mixture of the vision of Steve Jobs, the tenacity of Andrew Carnegie, and the compassion and leadership of Bobby Bowden.
“When people love who they work with and are compensated correctly, the resulting product is cleaner, safer, and a better quality. At many companies in our industry, many of the employees have barely met the owner and don’t have the chance to directly communicate with upper management. Ninety percent of our employees have my personal cell number and call, text, or Facebook me regularly.
“I like passionate people and try to make the work fun like Google and competitive like football. I want people to do their jobs not because they are scared of losing them, but because they believe in the company and want us all to succeed.”
Building the Business
Compton used his personal savings, credit cards, and previous general contracting experience to start the company. After working through his first contract, he decided that a warehouse or shop was needed because he kept getting requests to also provide materials and fabrication.
“My love of structures, particularly the steel portions, pushed me to go on my own. When fabrication was added to the capabilities offered, that part of the business immediately took off. Clients were glad we were doing everything in-house.
“The first shop was rented from a retiring steel fabricator local to Chattanooga. Built in the 1950s, it had maybe 13,000 square feet and some old 1950s equipment—literally leather belt-driven. We didn’t use those machines much. We outgrew that facility in about two months.”
A search for more production space landed Southern Spear in its new location about 2 miles down the road. The company moved into the vintage 1916 brick, wood, and steel factory building in September 2018. Compton drew from one of his company’s areas of expertise—renovating old buildings—to redesign the interior and update the 60,000 sq. ft. and three stories of the former textile mill (see Figures 3 and 4).
“Everybody is going downtown in their communities and repurposing old factories for fixed or multiuse purposes. Not every contractor likes to do these jobs, but it is my love,” said Compton. “An old building will become a development that houses retail, offices, apartments, or once in a while an industrial enterprise like ours.”
Shop layout is based on lean principles. Each employee has a workstation. Tools are arranged on shadow pegboards to keep everything identified, accessible, in its place, and within a hand’s reach. Production flow is laid out to keep materials and assemblies moving. Cranes are in place and used as needed, but conveyors quickly move components from one station to another whenever possible.
Design, engineering, and fabrication processes are nearly 100 percent paperless until delivered to the construction site. The latest project revision or request for information can be accessed instantly by employees using large iPad®s with cell service that links to the cloud server storing project plans.
Time clocks in the field are based on biometrics for individual identification and cellphone apps.
Adding the Best
Compton’s business philosophy includes having control of every possible aspect of fabricating and building erection (see Figure 5). That includes either buying a supplier or incorporating various services into his own company. For example, he was unhappy with the costs and delays that can be part of transportation, so the company now owns a fleet of trucks, semis, and trailers to handle its own shipping. Similarly, he hired three crane operators and purchased a 40-ton National-Manitowoc boom truck to gain control of on-site crane costs and scheduling.
The equipment roster for efficient fabrication is continually expanding. Building components are produced on a Hyd-Mech fully automated saw, a 200-ton Niagara press brake, a Cleveland Steel Tool punch, and a 300-amp burn table using Hypertherm’s True Hole® technology.
A new Lincoln Electric PythonX was added in late September (see Figure 6). The robotic structural fabricating system fits with the company’s lean attitude by handling material transfers; accommodating a variety of structural configurations and sizes; and producing accurate features from bolt holes and copes to markings, bevels, and slots in one pass.
“We closed on financing in mid-September, and two weeks later the Python and installers arrived so it could be installed ASAP,” said Compton. Its own metal structure was built around the system after it was in place.
“We also use only Hilti power tools. The tools are guaranteed for a year, so if something breaks, we get a replacement overnight. Finding good vendors can be the difference between winning and losing.”
The company is structured to get—and retain—good people. “We recruit employees based on intelligence, drive, creativity, and, of course, skills. It’s not necessarily about experience. We’ll take the flexible, ambitious, tenacious people with two or three years of experience and who want to grow, and we’ll teach them the right way to do the job.
“We offer things that other companies don’t. Pay is more than what our competitors offer, health insurance is good, and our 401(k) match and vesting schedule is to the max. People want to stay, and we get a lot of employee referrals. We have a team mentality where everyone is working towards the same goal. Based on my football days, I always emphasize finishing strong and, when you get tired, pay attention to the details and technique.”
Engineers are hired based on each specific project. “Drawing from a group of engineers can be like pulling the right club from a golf bag to make a play. The right engineer for a new high-rise development might not be the same guy who is best at redesigning a 100-year-old building. We’re not at the company size where we can have a whole bag of golf clubs.”
Heading Way South
For the next five to six years the essential company goal will be completing the design-and-build project that shelters the Antarctic’s largest research facility. McMurdo Station is located on an island close to New Zealand, part of the least habitable continent on earth. The National Science Foundation (NSF) manages the station and research that occurs there through the U.S. Antarctic Program (USAP).
Compton said that during the summer months, October to April, when the temperature can reach up to 35 degrees F, the McMurdo population can climb to 1,000. According to the NSF, in the winter months, the sea literally is impassable, and temperatures can drop to -58 degrees F. Then the population drops to about 180.
A committee was commissioned by the NSF and the government’s Office of Science to assess the USAP logistics support system in 2011. Part of the committee’s determination was that the McMurdo Station, with its current structures built in the late 1950s, needed significant infrastructure modernization to continue efficiently supporting the research teams.
The resulting project was named the Antarctic Infrastructure Modernization for Science (AIMS), and it’s the largest construction project that has been undertaken on the continent. Four goals of the infrastructure modernization, as listed in the government’s AIMS description, are:
1. Redevelopment of the core facilities into smaller, more energy- and operationally efficient spaces optimized for support of local and field science.
2. Replacement of major service and logistics facilities, including administration, dining, warehousing, trades shops, and field science support.
3. Establishment of a continuity-of-operations wing with modernized fire, medical, and personnel support capabilities.
4. Environmental and safety upgrades to all facilities for fuel containment, utilities distribution, and fire protection.
These directives are to be accomplished while work at the station continues within the current buildings. The cycle will be to demolish multiple small buildings, rebuild one larger replacement that is more efficient, and repeat. All materials resulting from the demolition will be shipped off of the continent.
Southern Spear Ironworks bid on and won the first phase of the project and was then awarded the other 90 percent of the design-and-build contract. The company is helping determine what materials will be used. Logistics have been laid out, and component fabrication is in its initial stages.
“The government wanted to find a company that was comfortable with adventurous projects, had the capacity to basically do everything in-house, and had multiskilled people. It’s a huge deal if you can take a compact group of people who can do different trades because of the travel and housing costs. The logistics and costs of getting to Antarctica are ridiculous, so fewer people represent significant cost savings,” said Compton.
Running that project requires extreme advanced planning. Each year there will be only one opportunity to ship materials to the southern island.
“When we are done with the fabrication in Chattanooga, the components for that year’s construction will be transported via our trucks to Port Hueneme, a naval base in Ventura County, Calif. We’ll have about a month beginning in October to send materials because the ship will be docked at the port for about 30 days. Everything we will need has to be included in that shipment that will leave in November—structure components, welding wire and rods, gases, power tools, batteries—everything for about four months of continuous building. We won’t see those items again until the end of January, which is the middle of the summer there and when our personnel will arrive.
“Back home, the shop will have a good amount of time to handle other steel erection and fabrication projects until it starts fabrication for the next year’s AIMS building cycle.”
Keeping Things Tight
More than 3,000 tons of steel will be involved in the project. Buildings of structural steel, corrugated stainless steel wall panels, and roofing will be constructed on concrete footers that float on the ice surface. Galvanized steel subcolumns that come out of the ice are part of the floating footers. All structural steel, including that in the floors, will be covered by 12 inches of structural insulated panel (SIP) systems and thermal break material to help stop the conduction of cold from the ice to the building. When completed, each building of the complex will have an R-70 insulation rating.
Compton said, “The panels will be made of wood because metal panels only have up to an R-30 rating, and they are more expensive. The panels for this project will be constructed from two pieces of OSB [oriented strand board] with 12 in. of foam insulation between them. The SIPs are being custom-built by Todd Bell and his team at Premier SIPs in Puyallup, Wash.
“Each building will essentially sit off the earth. Soffits underneath that get the same insulation as the walls will complete the tight seal of each building. They will be very efficient and built to withstand the extreme weather. It’s hard to design a new building for a severe climate when you’re drawing from modern building materials that have not been tested in that type of environment.”
Manning the Job
Compton and most members of the senior management team will travel to Antarctica. Several of the employees from the shop and erection crews also are ready to spend time in the 24-hour sun.
Crews will include certified crane operators, who will use cranes already on-site for the first season of the project. In 2020, when the project is estimated to use 600 tons of steel, the company’s 65- and 100-ton cranes will be shipped to Antarctica for use throughout the remaining five years.
“It’s kind of a reward for some of our guys, because it will be at a higher pay rate and it’s a once-in-a-lifetime opportunity. Since there is 24 hours of sunlight every day, we’ll have three foremen running three shifts. Some of the people on-site will phase in and out, and some will stay from January through April when we come back,” said Compton.
“Most of our guys are multifaceted, and that’s what we’ve built this program on. We have people who started as steel framers and are now our best certified welders. They know how to read plans and how structures go together, so they will be able to complete tasks typically assigned to several different tradesmen.
“Since it is a design-and-build project, we have a good heads-up and can schedule production out nicely. We’ll always have something going on.”
When asked what he does when he’s not working 12- to 14-hour days seven days a week, Compton said he thinks about working … and occasionally watches FSU Seminole football games with his fiancé while working from his laptop. Work is his passion.
Southern Spear Ironworks, www.thesouthernspear.com
About the Author
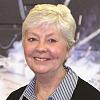
subscribe now
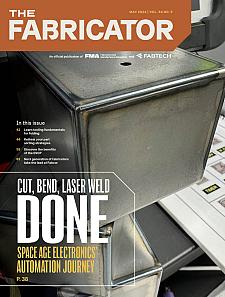
The Fabricator is North America's leading magazine for the metal forming and fabricating industry. The magazine delivers the news, technical articles, and case histories that enable fabricators to do their jobs more efficiently. The Fabricator has served the industry since 1970.
start your free subscription- Stay connected from anywhere
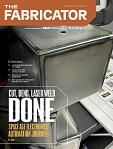
Easily access valuable industry resources now with full access to the digital edition of The Fabricator.
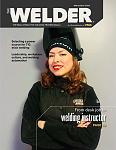
Easily access valuable industry resources now with full access to the digital edition of The Welder.
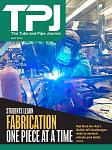
Easily access valuable industry resources now with full access to the digital edition of The Tube and Pipe Journal.
- Podcasting
- Podcast:
- The Fabricator Podcast
- Published:
- 04/16/2024
- Running Time:
- 63:29
In this episode of The Fabricator Podcast, Caleb Chamberlain, co-founder and CEO of OSH Cut, discusses his company’s...
- Trending Articles
Capturing, recording equipment inspection data for FMEA
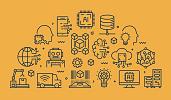
Tips for creating sheet metal tubes with perforations
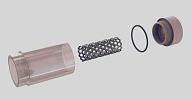
Are two heads better than one in fiber laser cutting?
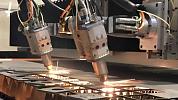
Supporting the metal fabricating industry through FMA
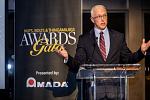
Omco Solar opens second Alabama manufacturing facility
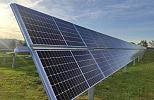
- Industry Events
16th Annual Safety Conference
- April 30 - May 1, 2024
- Elgin,
Pipe and Tube Conference
- May 21 - 22, 2024
- Omaha, NE
World-Class Roll Forming Workshop
- June 5 - 6, 2024
- Louisville, KY
Advanced Laser Application Workshop
- June 25 - 27, 2024
- Novi, MI