Editor-in-Chief
- FMA
- The Fabricator
- FABTECH
- Canadian Metalworking
Categories
- Additive Manufacturing
- Aluminum Welding
- Arc Welding
- Assembly and Joining
- Automation and Robotics
- Bending and Forming
- Consumables
- Cutting and Weld Prep
- Electric Vehicles
- En Español
- Finishing
- Hydroforming
- Laser Cutting
- Laser Welding
- Machining
- Manufacturing Software
- Materials Handling
- Metals/Materials
- Oxyfuel Cutting
- Plasma Cutting
- Power Tools
- Punching and Other Holemaking
- Roll Forming
- Safety
- Sawing
- Shearing
- Shop Management
- Testing and Measuring
- Tube and Pipe Fabrication
- Tube and Pipe Production
- Waterjet Cutting
Industry Directory
Webcasts
Podcasts
FAB 40
Advertise
Subscribe
Account Login
Search
Managing the multigenerational workforce
Metal fabricators offer their advice on how to make the most of an age-diverse labor pool
- By Dan Davis
- November 16, 2018
- Article
- Shop Management
The media that covers labor and hiring trends finds the current mix of generations in the workforce endlessly fascinating. Some have called it a special time because you have distinctly labeled generations in the same labor market.
For those interested in such things, these generations, as defined by the Pew Research Center, are the baby boomers (born 1946 to 1964), Generation X (born 1965 to 1980), the millennials (born 1981 to 1996), and Generation Z or the post-millennials (born 1997 and later). The boomers have been in the news lately as they are currently retiring in great numbers; some estimates have pegged the trend at 10,000 exits per day for these veterans of the work world. Manufacturers have been especially aware of this as they have tried to anticipate the departure of these longtime employees.
Of course, leave it to metal fabricators to cut through the hype and get down to what matters. What seems like a hot topic for trade journal columnists and TV pundits is just another aspect of running a manufacturing business.
“We’ve always had multigenerational work environments. That’s nothing new,” said Jeff Stapel, human resources and safety manager, Shickel Corp., in Bridgewater, Va.
So the situation is not so special, but the reality of the mixed-generational workforce is pretty important. All manufacturers are looking to get the most out of their employees. That’s why we’ve asked some metal fabricators just what they are doing to maintain a productive employee base, even as they face a robust manufacturing environment and a dearth of qualified candidates willing to tackle current job openings.
Forget the Stereotypes
A comedian once commented that stereotypes are great because they save time. You don’t need to develop an opinion about the person; you just fall back on the stereotype and move on.
That might be cause for a giggle, but it’s a lame approach to managing individuals. The truth is that people can surprise you, if you give them the chance.
Al Carlson, vice president of human resources, talent management, and leadership development, BTD Mfg., in Detroit Lakes, Minn., said his company is working aggressively to replace the baby boomers who are retiring. The company has roughly 1,250 employees spread over four plants, so management has made recruiting and talent development key areas of focus as they face the potential loss of vast amounts of institutional knowledge leaving with impending retirements.
Carlson said BTD has targeted two-year tool and die, welding, and other vocational school students, but acknowledges that the competition is great for those individuals. That leaves a company needing to think creatively about who might be a suitable candidate for a career at a metal fabrication shop.
Is a 22-year-old certified nursing assistant a good candidate? Surprisingly, yes, according to Carlson. She had started as a welder in early October, and early feedback was that she was loving the daily challenge of building something from nothing.
“I’ve been asking some of our younger people why metal fabrication, and they just like the variety,” Carlson said. “They like the challenge. They like the fact that they’re building for a world-class brand.”
The stereotype suggests people of that age don’t want to work. The truth is that they don’t want to be bored.
“There has never been a person in my 35-year working career that told me that they were bored here,” said Jean Pitzo, CEO, Ace Metal Crafts Co., in Bensenville, Ill.
If variety is the spice of a metal fabricating shop, then values are the base of any company culture. Pitzo said, by not focusing on age and stereotypes, you can find the right mix of people for your company.
“It doesn’t matter how old you are because it’s really about values,” she said. “Two of our big values are trust and respect. They kind of go hand-in-hand. It also fuels one of the behaviors that we collectively decided to foster: sharing knowledge. That’s one of the biggest things manufacturers have to work on.”
When that is the goal, stereotypes can’t get in the way of executing the plan. You can’t assume that just because someone is older that they are poised to excel at a mentoring role. When it comes to introducing inexperienced workers to CNC programming or shop management software, you don’t want to mistakenly conclude that younger people catch on faster than their older colleagues. In reality, stereotypes can lead to awkward work situations that might leave a negative impression on someone the company is trying to win over.
Try to Be Flexible
Here’s an irrefutable fact: Older adults are staying in the workforce longer than they used to. The Pew Research Center reports that the share of adults 65 and older who are employed has risen steadily over the decades, from 12 percent in 1980 to 19 percent in 2015. The Great Recession likely bolstered this trend.
Now here’s something that we hear repeatedly from metal fabricators: They can’t find the right skilled candidates for their job openings.
This has led metal fabricators to become a bit more flexible with work schedules than maybe they were in the past. While Shickel Corp. doesn’t have an official policy, it does try to remain open-minded, particularly as older workers have to adjust to life changes, such a caring for aging parents, or just want to slow down a bit and not deal with the rigors of a 40-hour week.
“What’s the alternative? To say ‘no?’” Stapel said. “You have all of that experience and knowledge, and they can share that with others. Why not work to accommodate that?”
Carlson said work schedule flexibility really plays a part in an area such as the tool and die department, where finding skilled replacements for the knowledgeable, long-term workers is particularly daunting. That’s why they have some of their older workers “ratcheting down” before officially retiring, he said. That might mean a standing request to work no overtime or the shifting of a schedule to 20 or 30 hours.
“We need to be flexible with our older workers. We want to have them stay longer, especially when they want to stay longer,” Carlson said.
Sometimes the flexibility isn’t limited to creative scheduling. It also may be required in career path adjustments.
The variety of work crossing a fab shop’s floor is no secret. That mix makes fabricating attractive for some workers because no two days are alike. It also presents opportunities for someone to learn multiple jobs, even if they happen to be really good at one of them.
Pitzo discovered this recently when a welder indicated he wanted to become a machinist. That’s a request that Ace Metal Crafts normally wouldn’t have a problem with, but he happened to be a good welder and the shop needed all of the welders it could get to keep up with orders. The timing was not the most ideal.
“It really takes a gut check and a lot of patience,” Pitzo said. But management worked with the young man, getting him registered for machining classes even if the job did not line up right away.
Engage the Employees
Carlson said that as part of its commitment to develop its workforce to take on more opportunities in the future, BTD is not only trying to bring in new blood, but also identify career paths for those already in the organization. The thought is that even the most impatient of employees can feel reassured that they won’t be stuck in the same job for an undefined future because they can identify steps to take within the BTD organization to get to the job they desire.
“We’ve got these nice business cards that have three questions on them,” Carlson said. “Where are you now? Where do you want to go? What does the future look like? We try to have that conversation with each of our employees and focus on those questions.”
Some people take note of such conversations. Carlson said a 20-something person had indicated an interest in ultimately becoming a director of one of BTD’s plants. He had demonstrated traits that management had identified as important to being a leader, but he really needed more exposure to interacting with customers. Carlson said that management arranged for the young man to join a BTD sales representative in weekly meetings with one of the company’s largest customers. The meetings covered new jobs heading to BTD facilities and engineering revisions for existing jobs, but they allowed the young man to see what the salespeople did.
“Uncovering the needs of our people is probably one of our biggest challenges. We have to keep asking them what’s next for them,” Carlson said.
Not all shops have formal leadership training programs, but that doesn’t mean they can’t be aware of employees’ career goals. For some metal fabricators, simply offering additional training opportunities is the way to go. It helps to cross-train employees, which provides more flexibility on the shop floor and allows employees to add skills.
Pitzo said that shops should be aware that some “train-the-trainer” classes might be needed for more experienced employees deemed to be perfect mentor candidates to trainees. Some people are better fabricators than communicators, so additional guidance on how to demonstrate procedures or offer constructive criticism can help.
Carlson added that not all people have a desire to step into leadership roles, and fab shops should be cognizant of that. These folks want to show up, be compensated fairly for a day’s work, and head home at the end of their shift.
“We have to be respectful of those people as well, because we need a lot of those people too,” he said.
Communication Channels Need Updating
You don’t have to be an anthropologist to know that society consumes information differently than it did just 15 years ago. For example, most people don’t read newspapers anymore. Their heads are buried in mobile phones consuming the day’s headlines, gossip, and memes as they stand, walk, and even drive their cars.
Stapel said that trend has led Shickel Corp. to rethink the way they are communicating with their employees, particularly the younger ones who have grown up in a digital world. The company has put up more monitors on the shop floor, while still using bulletin boards. It makes sense as people become more used to real-time information being delivered electronically instead of in a memo.
He added that he has had to investigate new methods of employee recruiting as well. He’s done some Facebook mining recently, whereas five years ago, Stapel said he never would have considered that a viable path for finding job candidates.
“We have to realize that things have changed in the ways people communicate, especially for some portions of the population,” Stapel said.
What About the Next Generation?
Who’s after Generation Z? Demographers may not have gotten around to identifying a nickname for this upcoming workforce, being that the oldest of them are probably more interested in fighting acne than finding a job, but metal fabricators should take note. If you want the best and the brightest to consider a career in manufacturing, you have to reach them as early as possible.
Developing relationships with local community colleges and high schools is nice, but by that time, most students have made up their mind as to what they want to do with their lives. If a metal fabricator wants to make a mark on an open mind, it needs to be involved in the middle school ranks at the very least. That’s where students are tasked with more rigorous classes and juggling multiple assignments. It’s where they start to develop an idea about what they like and what they are good at.
“To excite and attract people to what we do—if we want to do that, we need to plant the seeds early on,” Stapel said.
Ace Metal Crafts Co., www.acemetal.com
BTD Mfg., www.btdmfg.com
Shickel Corp., www.shickel.com
About the Author
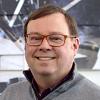
Dan Davis
2135 Point Blvd.
Elgin, IL 60123
815-227-8281
Dan Davis is editor-in-chief of The Fabricator, the industry's most widely circulated metal fabricating magazine, and its sister publications, The Tube & Pipe Journal and The Welder. He has been with the publications since April 2002.
subscribe now
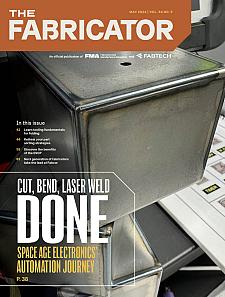
The Fabricator is North America's leading magazine for the metal forming and fabricating industry. The magazine delivers the news, technical articles, and case histories that enable fabricators to do their jobs more efficiently. The Fabricator has served the industry since 1970.
start your free subscription- Stay connected from anywhere
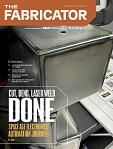
Easily access valuable industry resources now with full access to the digital edition of The Fabricator.
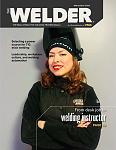
Easily access valuable industry resources now with full access to the digital edition of The Welder.
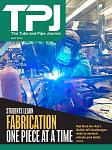
Easily access valuable industry resources now with full access to the digital edition of The Tube and Pipe Journal.
- Podcasting
- Podcast:
- The Fabricator Podcast
- Published:
- 04/16/2024
- Running Time:
- 63:29
In this episode of The Fabricator Podcast, Caleb Chamberlain, co-founder and CEO of OSH Cut, discusses his company’s...
- Industry Events
16th Annual Safety Conference
- April 30 - May 1, 2024
- Elgin,
Pipe and Tube Conference
- May 21 - 22, 2024
- Omaha, NE
World-Class Roll Forming Workshop
- June 5 - 6, 2024
- Louisville, KY
Advanced Laser Application Workshop
- June 25 - 27, 2024
- Novi, MI