Contributing editor
- FMA
- The Fabricator
- FABTECH
- Canadian Metalworking
Categories
- Additive Manufacturing
- Aluminum Welding
- Arc Welding
- Assembly and Joining
- Automation and Robotics
- Bending and Forming
- Consumables
- Cutting and Weld Prep
- Electric Vehicles
- En Español
- Finishing
- Hydroforming
- Laser Cutting
- Laser Welding
- Machining
- Manufacturing Software
- Materials Handling
- Metals/Materials
- Oxyfuel Cutting
- Plasma Cutting
- Power Tools
- Punching and Other Holemaking
- Roll Forming
- Safety
- Sawing
- Shearing
- Shop Management
- Testing and Measuring
- Tube and Pipe Fabrication
- Tube and Pipe Production
- Waterjet Cutting
Industry Directory
Webcasts
Podcasts
FAB 40
Advertise
Subscribe
Account Login
Search
Auto industry shift makes for odd bedfellows
From “too big to fail” to “too big to solve alone”
- By Kate Bachman
- September 26, 2019
The upcoming transition in the automotive industry from internal combustion engine (ICE) vehicles to electric and other autonomous, connected, electric, and shared (ACES) vehicles has knitted many a brow. The task of realigning the design and engineering, sourcing, production, sales, aftermarket, infrastructure—everything— from the combustion propulsion system to a new (yes, also old) electric propulsion system is an enormous challenge, especially the autonomous aspect.
Grace Under Pressure
During what has been referred to as “a sea change for the auto industry,” automakers and their suppliers face the high costs of R&D and seemingly insurmountable problems with everything from forming high-tensile-strength steel and aluminum to achieving lightweighting and a changing vehicle architecture and infrastructure.
Shortages and challenges often prompt people and companies to become more secretive and more possessive. Sometimes, out of desperation, they even commit theft and other crimes.
Occasionally, though, when faced with challenges of magnitude, people and enterprises do the opposite—and caravan together. Arm ‘round arm, they shoulder each other up the hill.
Odd Bedfellows
If politics makes for strange bedfellows, these technological challenges surely do too. One of the most surprising upshots of the ICE-to-ACES vehicles challenge has been the pairing of archrivals. The steep costs of developing electric, and especially autonomous, vehicles are prompting automakers to form alliances with competitors.
One remarkable alliance most intriguing to me is the pairing of Ford and Volkswagen. The two automakers are accessing each other’s strengths to augment their own, thereby reducing their R&D investments substantially. Volkswagen has invested in Ford’s Argo AI, and Ford will use Volkswagen’s modular electric toolkit, known as MEB, to design an all-new battery-electric vehicle for its European operations.
Ford CEO Jim Hackett and VW CEO Herbert Diess project that the wide-ranging cooperation on electric and autonomous vehicles has the promise of saving each company hundreds of millions of dollars/euros in future development costs.
The European AffordabLe LIghtweight Automobiles Alliance (ALLIANCE), is another example. Daimler AG coordinated an alliance of six European automakers (Daimler, Volkswagen, Volvo, Opel, TME, and Centro Ricerche Fiat) to research optimal lightweighting materials and manufacturing processes.
Prof. Dr.-Ing. Sama Mbang, Daimler Mercedes-Benz, headed up a three-year research project for the ALLIANCE that just concluded. Presenting at the recent GALM conference, Mbang said the research objectives were threefold: weight reduction, emissions reduction, and affordability.
The latter goal may seem surprising considering that Mercedes-Benz is generally not considered a cost-conscious brand. Why? The alliance identified the high cost of lightweighting innovation as the major bottleneck.
“Affordability is very important—for the OEMs, because of the cost of materials and cost of production--and also to make these new lightweight material technologies affordable for customers,” Mbang explained. The research project exceeded its goals. The final results were a 33 percent weight reduction, 25 percent emissions reduction, and cost savings of 3 euros/kilograms.
From Handouts to Handshakes
It was not so long ago in 2008 that, facing the worst economy since the Great Depression, the U.S. auto industry appealed to Washington for $80 billion in megaloans to keep the fires burning. There was talk of auto OEMs being “too big to fail.”
Today, facing the major technological challenges and costs of the ACES transition, automakers are reaching out to each other and to their suppliers for help. Instead of being “too big to fail,” the industry is admitting that the mountain is too big for one company to climb alone. “Both EVs and AVs are big costs for investment,” Ford’s Hackett was quoted as saying in Advanced Manufacturing. “It’s my opinion, you can’t do this alone.”
This collaborative approach takes enormous courage and a monumental amount of self-awareness. It seems a more prudent way to balance the P&L sheet than other alternatives.
Got thoughts? kateb@thefabricator.com
subscribe now
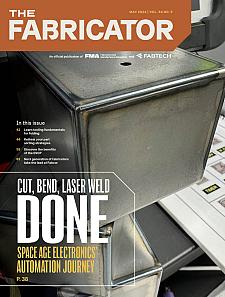
The Fabricator is North America's leading magazine for the metal forming and fabricating industry. The magazine delivers the news, technical articles, and case histories that enable fabricators to do their jobs more efficiently. The Fabricator has served the industry since 1970.
start your free subscriptionAbout the Author
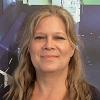
Kate Bachman
815-381-1302
Kate Bachman is a contributing editor for The FABRICATOR editor. Bachman has more than 20 years of experience as a writer and editor in the manufacturing and other industries.
- Stay connected from anywhere
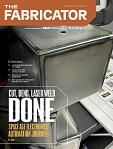
Easily access valuable industry resources now with full access to the digital edition of The Fabricator.
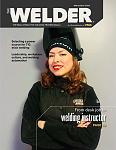
Easily access valuable industry resources now with full access to the digital edition of The Welder.
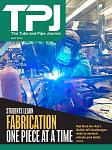
Easily access valuable industry resources now with full access to the digital edition of The Tube and Pipe Journal.
- Podcasting
- Podcast:
- The Fabricator Podcast
- Published:
- 04/16/2024
- Running Time:
- 63:29
In this episode of The Fabricator Podcast, Caleb Chamberlain, co-founder and CEO of OSH Cut, discusses his company’s...
- Trending Articles
Capturing, recording equipment inspection data for FMEA
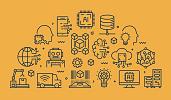
Tips for creating sheet metal tubes with perforations
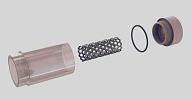
Are two heads better than one in fiber laser cutting?
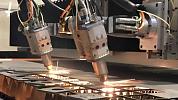
Supporting the metal fabricating industry through FMA
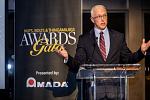
Omco Solar opens second Alabama manufacturing facility
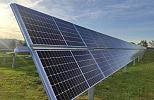
- Industry Events
16th Annual Safety Conference
- April 30 - May 1, 2024
- Elgin,
Pipe and Tube Conference
- May 21 - 22, 2024
- Omaha, NE
World-Class Roll Forming Workshop
- June 5 - 6, 2024
- Louisville, KY
Advanced Laser Application Workshop
- June 25 - 27, 2024
- Novi, MI