Senior Editor
- FMA
- The Fabricator
- FABTECH
- Canadian Metalworking
Categories
- Additive Manufacturing
- Aluminum Welding
- Arc Welding
- Assembly and Joining
- Automation and Robotics
- Bending and Forming
- Consumables
- Cutting and Weld Prep
- Electric Vehicles
- En Español
- Finishing
- Hydroforming
- Laser Cutting
- Laser Welding
- Machining
- Manufacturing Software
- Materials Handling
- Metals/Materials
- Oxyfuel Cutting
- Plasma Cutting
- Power Tools
- Punching and Other Holemaking
- Roll Forming
- Safety
- Sawing
- Shearing
- Shop Management
- Testing and Measuring
- Tube and Pipe Fabrication
- Tube and Pipe Production
- Waterjet Cutting
Industry Directory
Webcasts
Podcasts
FAB 40
Advertise
Subscribe
Account Login
Search
How vibratory weld conditioning can help weld distortion
The technology can increase throughput and make the welder’s life easier
- By Tim Heston
- Updated December 8, 2023
- March 10, 2021
- Article
- Arc Welding
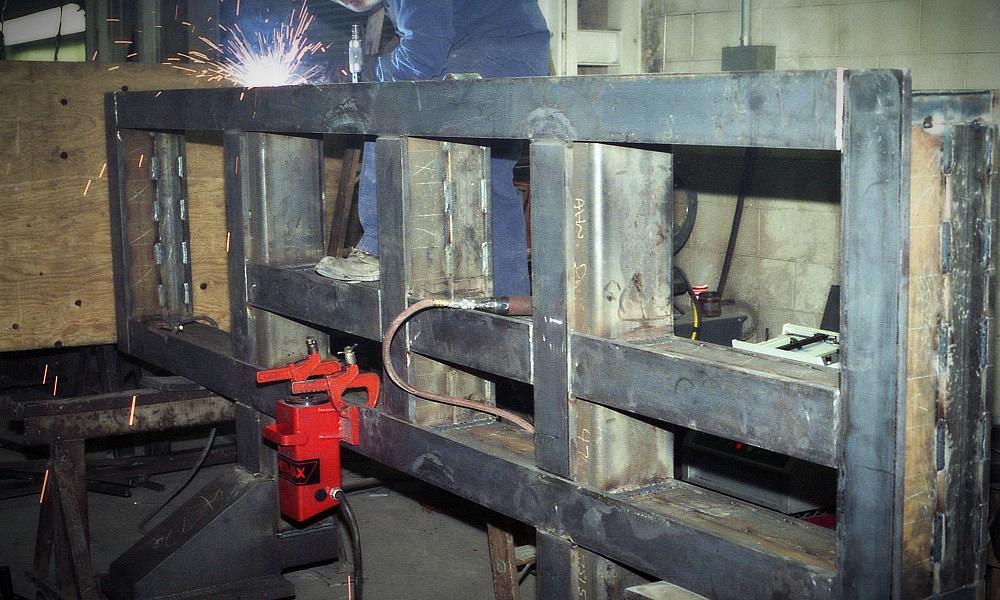
This automotive check fixture—16 by 5.5 ft. and consisting primarily of 2- by 4-in. tubing—previously required an elaborate straightening procedure after welding. Vibratory weld conditioning reportedly prevented 85% of the normal distortion and eliminated the need for straightening.
Imagine a welder completes one side of a large workpiece, then flips the thing over and welds the other side, then flips it back to continue welding. A nonwelder looking on might think the welder’s just creating work for himself. But he isn’t. He’s fighting weld distortion.
What Is Weld Distortion?
Weld distortion occurs as the weld and base metals expand and contract during welding. It can include a change in the weld joint size (shrinkage) or angle, as well as bucking of the weld.
Not only can the distortion affect the appearance of a weld, but it can cause difficulty in part assembly and even prevent an end product from performing its intended purpose.
Is Heat a Factor?
Welders have a love-hate relationship with heat. Arc welding couldn’t occur without it, but left uncontrolled, heat in many cases also can destroy a weld and create a lot of headaches. The welder performing a seemingly quixotic weld procedure—welding one side and then the other—is really just working to counteract how the weld distorts the final part geometry.
Heat is a contributing factor, but Tom Hebel, president of Bonal Technologies, Royal Oak, Mich., doesn’t see heat—or, specifically, quick changes in temperature—as a direct cause of weld distortion and potential cracking.
“We feel that the [direct causes] of weld distortion are dominated by the shrinkage of the weld metal,” he said. “Yes, the sharp temperature drop causes thermal stress,” which can be particularly problematic in chrome-moly and other material grades that tend to dissipate heat very quickly. “That thermal stress will remain in the weldment as residual stress after cooling. But that doesn’t necessarily cause permanent distortion. The weld shrinkage does. And to control that, you need to figure out how to influence exactly how the weld metal solidifies. Essentially you want to [prolong] the time it takes for the face to solidify. The longer it takes for the face to solidify, the less distortion will result.”
Vibratory Weld Conditioning
Mild vibration, as it turns out, is a way to keep metal molten a little longer before the weld face solidifies and, hence, nip weld distortion in the bud.
Hebel and others at Bonal have studied vibration’s effect on welding for years and, in doing so, have patented what they call the Meta-Lax process, which induces subharmonic vibrations.
The technology has two applications. One is vibratory stress relief, which is applied after a metal workpiece has been worked in some way, such as welding or machining. It relieves stresses in the workpiece, which can minimize or eliminate subsequent cracking and distortion, but it cannot straighten a workpiece that’s already distorted. “After all, once you experience weld distortion, it’s too late,” Hebel said. “Applying vibratory stress relief isn’t going to straighten your part.”
The other application is vibratory weld conditioning. Here, a vibration-inducing unit is affixed to the workpiece during welding, usually halfway along the weld length (or for very long joints, halfway along a 15-ft. length of weld). The unit applies a low subharmonic frequency, usually lower than the frequencies used for vibratory stress relief.
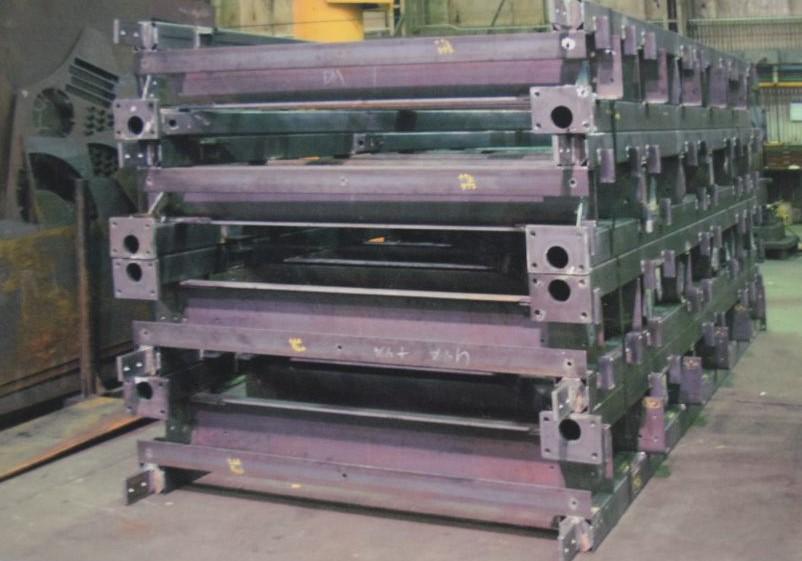
Kanawha Manufacturing fabricated these box-tube assemblies, the structural component of battery backup systems used in the power industry. The use of vibratory weld conditioning eliminated considerable distortion problems.
To understand how this all works, it helps to know exactly how weld distortion takes place in a conventional setup. Once filler metal becomes molten and spreads across the joint, the weld begins to solidify. The molten metal near the base metal solidifies first. Next comes the solidification of the weld face (top of the weld), which is affected by the air temperature. Once the metal solidifies completely across the face, shrinkage begins to occur. Unfortunately, the weld metal underneath, still in its liquid state, offers no resistance to the distortion that occurs as the weld face continues to shrink.
Adding the right amount of vibrational energy while welding changes the situation. Mild, subharmonic vibrations added to the base weldment gently excite the weld pool. Solidification, particularly at the face, is delayed a few seconds.
“This delay is very important,” Hebel explained, “in that it gives time for the inside area of the weld bead to solidify from the root, then gradually out to the face.”
The weld face is the last, or nearly the last, area of the weld joint to solidify. And when the weld face does finally solidify, it does so over weld metal that’s already solidified, no longer in its liquid state. This helps keep the dimensional shape of the weld joint, which helps prevent most weld distortion. “The amount of weld distortion that can be prevented is in the order of 50 to 90%,” Hebel said.
Vibratory weld conditioning is roughly similar to welding process iterations that spin, oscillate, or otherwise alter how the wire feeds into the pool. The resulting “stirring” of the weld pool delays solidification. “The vibratory weld conditioning we do has a similar result,” Hebel said. “But instead of stirring and vibrating the weld pool directly, we’re vibrating the base material.”
A Complementary Process
In certain cases, vibratory weld conditioning can minimize or eliminate the need for low-temperature preheating, usually at or less than 250 or 300 degrees F. Hebel added that some torch preheating might be necessary to evaporate moisture on and around the joint. To improve weld quality, particularly on crack-sensitive material, some choose to maintain the same preheat (say, 250 or 300 degrees F) and simply add vibratory weld conditioning to the existing weld procedure.
Still, vibratory weld conditioning cannot replace high-temperature preheating. “If a material needs 600 degrees F of preheat, or even more than 1,000 degrees F, the [vibratory conditioning] process isn’t going to replace that,” Hebel said.
High levels of preheating compensate for significant mismatches in coefficients of expansion between different metals, and vibratory conditioning really can’t compensate for the difference. In other words, simply vibrating the base metal won’t magically make the heated metals involved react and interact in a dramatically different way. In these cases, vibratory weld conditioning might make the existing weld procedure more consistent and efficient, but it really can’t replace high levels of preheating entirely.
“Some materials you really need to preheat no matter what,” said Carl Smith, a CWI and welding consultant who, during his time at Charleston, W.Va.-based Kanawha Manufacturing, used vibratory weld conditioning on a variety of challenging projects. “It was an extremely useful tool, but of course it wasn’t a cure-all. For instance, if you don’t preheat materials like chrome-moly, there’s no question you’ll end up with weld cracking.”
Even so, the weld conditioning process can change the way welders approach their work. For instance, if to mitigate distortion a welder previously sequenced his welds in different areas of the workpiece, with weld conditioning the welder might be able to weld consistently from one end of the part to the other—no part flipping, repositioning, or walking back and forth required.
Hebel added that vibratory weld conditioning can eliminate the need for postweld heat treating (PWHT) in some cases. It really depends on what the PWHT aims to accomplish. If the goal is to relieve stress, then yes, vibratory weld conditioning could eliminate the need for PWHT. “With vibratory weld conditioning, the thermal stress never has a chance to negatively influence the part in terms of distortion or premature cracking.”
However, if the purpose of PWHT is to change the material properties in some way, such as softening hard spots left by the heat-affected zone in welding, then vibratory weld conditioning really cannot reduce or replace PWHT.
The Welder’s Experience
Smith recalled using vibratory weld conditioning on a massive project involving 2205 duplex stainless steel. “That material is extremely susceptible to distortion, and the customer didn’t want any discoloration. So we couldn’t preheat, and we had to be very careful about heat input.”
The welding team used the vibratory weld conditioning unit on workpieces that were 20 ft. wide and 40 ft. long. He added that welding still had to occur intermittently to control heat and keep the temperature within the specified range. “But with the weld conditioner, we could weld farther without stopping.”
In this case, Smith used weld conditioning in conjunction with an oscillating, mechanized weld head that could lay down enough weld metal to complete the large joint in just one pass. Welding manually would have required three passes. Beyond taking more time, additional passes would have introduced more heat, which of course isn’t a good thing on heat-sensitive duplex stainless steel.
“The [vibratory weld conditioning] process does require some additional welder training,” Smith added, recalling that one operator at Kanawha “knew it inside and out.”
The learning curve requires the welder to, well, learn to read the curve—specifically, the harmonic curve. The welder affixes the vibration inducer near the midpoint of the weld length (or in the middle of a weld segment for very long welds). He turns on the system and sees the harmonic, bell-shaped curve that can change with the material and application. In fact, every welding setup has a unique harmonic signature. But whatever that signature’s shape, the welder zeros in on the area where the curve just starts ascending toward its peak. That represents a material’s optimal subharmonic weld conditioning frequency. He then begins to weld.
The curve’s frequency location isn’t set in stone but instead changes with the material properties, which the act of welding can change. So on large workpieces especially, the curve’s frequency location can change as the weld progresses. In these cases, the welder adjusts the system from time to time to compensate. Alternatively, computer-controlled weld conditioners change the vibration frequency automatically as needed.
With vibratory weld conditioning turned on, the welder is likely to notice several changes. “First, the weld tends to want to run hotter,” Hebel explained, adding that “a welder has a choice. He can crank up the amps, which will produce a higher-quality weld and allow him to weld faster. Alternatively, he could reduce the amps and maintain the same weld quality and travel speed, which would be best in preventing weld distortion from occurring.”
Under vibration, the weld also tends to “settle in” more. “It’s almost as if it’s magnetized,” Hebel explained, adding that the effect can make welding vertical-up, vertical-down, and overhead a little easier.
Another noticeable difference is the solidification pattern. An operator viewing a weld usually sees an upside-down U shape as the weld is deposited and flows into the joint as the welding arc travels forward. Increase the travel speed and you get a narrower U (almost a V) shape as the metal flows quickly around the arc. “But with vibratory weld conditioning, you can tell that the molten metal takes just a little longer to solidify. When you view the solidification pattern, you see a more pronounced U taking shape.”
A Tool, Not a Panacea
Both Hebel and Smith emphasized that vibratory weld conditioning isn’t a panacea. It can’t make unweldable material weldable, nor can it eliminate the need for preheat or PWHT in all materials and in all circumstances. As Smith explained, in many cases, vibratory weld conditioning helped reduce time- consuming distortion-preventing practices like intermittent welding and repositioning, but it didn’t eliminate them entirely. As with any other technology, results really depended on the application.
That said, vibratory weld conditioning is still a useful, and often overlooked, tool that in the right situation can help minimize or eliminate the most time-consuming aspect of challenging welding jobs: the heating, workpiece maneuvering, and intermittent welding (like stitch welding and welding alternately in different areas). Moving from one area of the weldment to the other, taking breaks to allow the weld to cool, flipping the workpiece: Considering all this, a welder can spend surprisingly little of his day actually welding. With the right tools applied in the right way, it doesn’t have to be this way.
About the Author
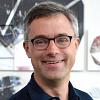
Tim Heston
2135 Point Blvd
Elgin, IL 60123
815-381-1314
Tim Heston, The Fabricator's senior editor, has covered the metal fabrication industry since 1998, starting his career at the American Welding Society's Welding Journal. Since then he has covered the full range of metal fabrication processes, from stamping, bending, and cutting to grinding and polishing. He joined The Fabricator's staff in October 2007.
subscribe now
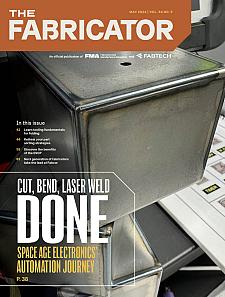
The Fabricator is North America's leading magazine for the metal forming and fabricating industry. The magazine delivers the news, technical articles, and case histories that enable fabricators to do their jobs more efficiently. The Fabricator has served the industry since 1970.
start your free subscription- Stay connected from anywhere
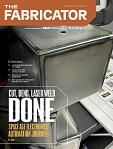
Easily access valuable industry resources now with full access to the digital edition of The Fabricator.
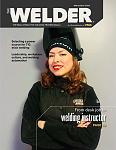
Easily access valuable industry resources now with full access to the digital edition of The Welder.
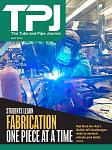
Easily access valuable industry resources now with full access to the digital edition of The Tube and Pipe Journal.
- Podcasting
- Podcast:
- The Fabricator Podcast
- Published:
- 04/16/2024
- Running Time:
- 63:29
In this episode of The Fabricator Podcast, Caleb Chamberlain, co-founder and CEO of OSH Cut, discusses his company’s...
- Industry Events
16th Annual Safety Conference
- April 30 - May 1, 2024
- Elgin,
Pipe and Tube Conference
- May 21 - 22, 2024
- Omaha, NE
World-Class Roll Forming Workshop
- June 5 - 6, 2024
- Louisville, KY
Advanced Laser Application Workshop
- June 25 - 27, 2024
- Novi, MI