- FMA
- The Fabricator
- FABTECH
- Canadian Metalworking
Categories
- Additive Manufacturing
- Aluminum Welding
- Arc Welding
- Assembly and Joining
- Automation and Robotics
- Bending and Forming
- Consumables
- Cutting and Weld Prep
- Electric Vehicles
- En Español
- Finishing
- Hydroforming
- Laser Cutting
- Laser Welding
- Machining
- Manufacturing Software
- Materials Handling
- Metals/Materials
- Oxyfuel Cutting
- Plasma Cutting
- Power Tools
- Punching and Other Holemaking
- Roll Forming
- Safety
- Sawing
- Shearing
- Shop Management
- Testing and Measuring
- Tube and Pipe Fabrication
- Tube and Pipe Production
- Waterjet Cutting
Industry Directory
Webcasts
Podcasts
FAB 40
Advertise
Subscribe
Account Login
Search
Ask the Stamping Expert: Fixing die shortcomings
- By Thomas Vacca
- April 14, 2015
- Article
- Bending and Forming
Q: We have a large stamping tool running in a 300-ton press. A changeover tool makes a left part and a right part, each of which is about 0.1 in. thick and shaped like a peanut. One-half of the part (lengthwise) is coined offset one material thickness in depth in addition to a number of other strengthening embosses and assembly holes.
The tool is old and we are having many problems: The parts are dimensionally inconsistent; scrap is excessive; service intervals vary greatly, with many runs cut short because of chipped or sheared punches and dies; changeovers from one part to the other never go flawlessly; excessive tweaking is required to get the part to meet print specification; and the list goes on. We have allocated funds for a new tool but are hesitant to base it on the current design. Any advice?
A: Our design team talked to the reader further to understand the current state of the tool design. Following are problems we identified and the actions we recommended. They fall into two categories: robustness and design changes.
1. Robustness: Part variation is caused by the tool flexing and poor guidance. The press has no bed holes for scrap. The die is on parallels, which are small and spaced out over the 6-ft. tool length. The die shoe, at 3 in. thick, is flexing. The parallels need to cover the entire surface of the bottom of the tool, except the very minimal areas where scrap needs to fall through. Four 3-in.-dia. down stops are placed at the corners. The three-plate design uses four stripper guide pins at the outer corners of the strippers.
We recommended the following changes:
- Add several parallels, some up to 6 in. wide, under the forming stations in the tool.
- Increase the die shoe thickness from 3 to 5 in.
- Add four more evenly spaced down stops and increase their size to 3- by 4-in. rectangles where possible. Make sure the ram is stopped at dead bottom of the stroke in exactly the same spot every cycle.
- Increase the number of stripper guide pins to eight, evenly spaced, and change the design from ball cages to roller cages, which will offer 10 times more rigidity in guidance. Apply this advice to the die shoe as well. Increase the diameter of all guide pins by 1.0 in., to 4 in. When proper guidance is achieved, you could almost remove the press guides and still run the tool.
- Add a hardened steel backup plate sufficiently thick so that the die inserts can sit on it, rather than directly on the die shoe.
2. Design Changes: Variation inherent in the stripper clamping is causing inconsistent forming of the blank. The biggest design issue is in the offset station in the tool. The part must be bent up into the stripper plate. The form insert is 0.1 in. higher than the die chase. As the tool closes and the stripper clamps the material, the bend goes into the stripper plate forming punch cavity, essentially bending the part with the stripper force. As the tool continues to close and the stripper continues to collapse, at some point the forming punch contacts the material to be formed and rebends the part offset. This bending and rebending is a fundamental flaw that leads to variation.
Following are the actions we recommended:
- Add slug darts to hold down scrap.
- Add lifters and some additional pilots to keep the strip level.
- Make sure the forming punch is spring-loaded to a point flush with the stripper face when the tool is open. Add a nitrogen spring pack loaded behind the punch with enough force to bend the part and prevent the punch from backing up. This way, when the stripper contacts the material, the forming punch will prevent the material from bending into the stripper form punch cavity. As the stripper compresses, the part is formed and hits home on the backup plate at dead bottom.
After all these changes were made, the new tool is now up and running flawlessly. Changeovers require no tool tweaking. Service intervals are repeatable and predictable. Scrap has been eliminated. The toolroom maintains to the CAD prints, with no tweaking or shimming.
About the Author
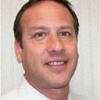
Thomas Vacca
Micro Co.
Has a shop floor stamping or tool and die question stumped you? If so, send your questions to kateb@thefabricator.com to be answered by Thomas Vacca, director of engineering at Micro Co.
Related Companies
subscribe now
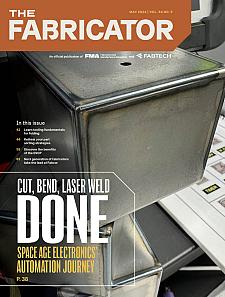
The Fabricator is North America's leading magazine for the metal forming and fabricating industry. The magazine delivers the news, technical articles, and case histories that enable fabricators to do their jobs more efficiently. The Fabricator has served the industry since 1970.
start your free subscription- Stay connected from anywhere
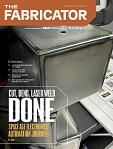
Easily access valuable industry resources now with full access to the digital edition of The Fabricator.
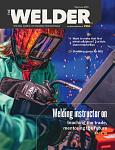
Easily access valuable industry resources now with full access to the digital edition of The Welder.
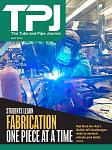
Easily access valuable industry resources now with full access to the digital edition of The Tube and Pipe Journal.
- Podcasting
- Podcast:
- The Fabricator Podcast
- Published:
- 05/07/2024
- Running Time:
- 67:38
Patrick Brunken, VP of Addison Machine Engineering, joins The Fabricator Podcast to talk about the tube and pipe...
- Trending Articles
White House considers China tariff increases on materials
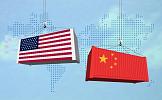
A deep dive into a bleeding-edge automation strategy in metal fabrication
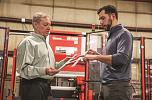
A visit to Automate 2024 reveals the future might be now
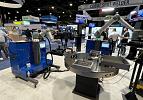
Majestic Steel Arkansas fully operational
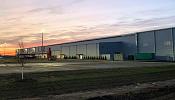
Rivian to expand Illinois facility to manufacture midsized SUV
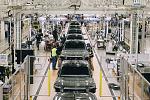
- Industry Events
Laser Welding Certificate Course
- May 7 - August 6, 2024
- Farmington Hills, IL
World-Class Roll Forming Workshop
- June 5 - 6, 2024
- Louisville, KY
Advanced Laser Application Workshop
- June 25 - 27, 2024
- Novi, MI
Precision Press Brake Certificate Course
- July 31 - August 1, 2024
- Elgin,