Senior Editor
- FMA
- The Fabricator
- FABTECH
- Canadian Metalworking
Categories
- Additive Manufacturing
- Aluminum Welding
- Arc Welding
- Assembly and Joining
- Automation and Robotics
- Bending and Forming
- Consumables
- Cutting and Weld Prep
- Electric Vehicles
- En Español
- Finishing
- Hydroforming
- Laser Cutting
- Laser Welding
- Machining
- Manufacturing Software
- Materials Handling
- Metals/Materials
- Oxyfuel Cutting
- Plasma Cutting
- Power Tools
- Punching and Other Holemaking
- Roll Forming
- Safety
- Sawing
- Shearing
- Shop Management
- Testing and Measuring
- Tube and Pipe Fabrication
- Tube and Pipe Production
- Waterjet Cutting
Industry Directory
Webcasts
Podcasts
FAB 40
Advertise
Subscribe
Account Login
Search
Anidado para la estabilidad del corte láser
Cómo considerar levantamientos de partes para que el láser siga cortando
- By Tim Heston
- April 29, 2024
- Article
- Laser Cutting
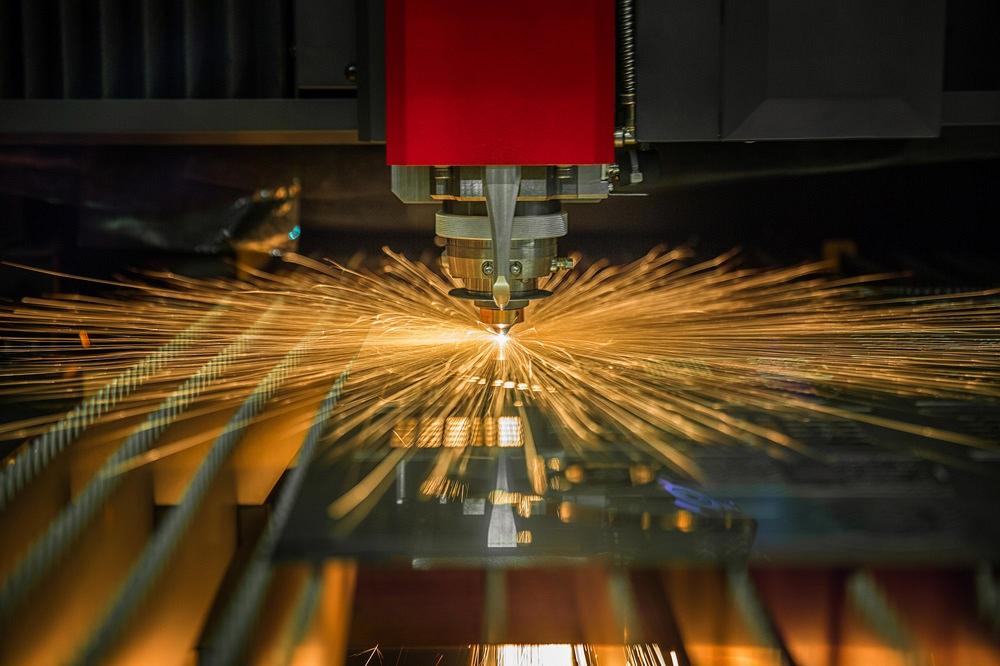
La ubicación y condición de las tablillas que soportan la chapa afecta la manera en que se soportan las partes y se evacúan los sobrantes. NeoPhoto/iStock/Getty Images Plus
El láser de fibra ha hecho extraordinariamente productiva la operación de corte principal en la mayoría de los fabricantes de metal– hasta que una parte se levanta y hace que la cabeza se detenga o colisione. Para evitar esto hay que empezar por conocer algunos fundamentos de anidado y, lo más importante, cómo las decisiones en el anidado y la programación láser afectan todos los pasos de manufactura que siguen.
¿Qué hace que las partes se levanten y se arqueen?
Hace años, muchos proveedores de máquinas y vendedores de software se enfocaban en cambiar operadores de las punzonadoras a los láseres de óptica volante. Debido a que el punzón mueve la chapa, todo necesita mantenerse unido con lengüetas, a menos hasta que sea evacuado a una lanzadera o levantado por ventosas en un sistema de remoción automatizada de partes. De lo contrario, las partes no caen de un nido a menos que los operadores las quiten haciéndolas saltar o sacudiéndolas. Cuando los talleres cambiaron a los láseres de fibra óptica, las chapas ya no se movían, y muchas partes que eran punzonadas con micro-lengüetas ya no las necesitaban. Por supuesto, el láser introdujo a la matriz una nueva variable: la posición de las tablillas.
Como lo expresó Mike Boggs, vicepresidente de ventas y mercadeo de Striker Systems, la capacitación empieza con los fundamentos, especialmente ahora que se está retirando tanta gente experimentada. “Volviendo a los fundamentos, la principal causa de levantamiento es el tamaño y la forma de la parte con relación a su posición en las tablillas de soporte”.
“Al final de cuentas, la posición de estas partes en el nido y dónde están las partes con relación a las tablillas en la máquina realmente importa”, dijo Doug Wood, director de ventas, Metal Solutions North America en Hexagon, creador del software Radan.
Las partes generalmente se colocan con 2 o 3 pulgadas de separación, dependiendo del modelo de la máquina. Entonces, si una parte (o sobrante de una forma interna) tiene al menos una dimensión menor a 6 pulgadas, tiene el potencial de levantarse. Imagine una parte rectangular de 5 pulgadas. Si el nido tiene esa pieza colocada de forma que se asienta sólo en una tablilla, esa pieza justo podría levantarse después de que el láser corta su perfil.
Es aquí donde pueden ayudar secuencias de destrucción de sobrantes. ¿Por qué arriesgarse a que un sobrante se atasque y se levante cuando puede ser cortado en piezas pequeñas y caer de manera segura? “Cuando se hacen partes con formas cortadas más grandes, las cuales tienen el potencial de levantarse, destruir ese sobrante y hacer que caiga entre las tablillas puede ser benéfico”, dijo Wood.
La mayoría de las tablillas constan de puntas o “dientes” que soportan la pieza de trabajo. Ciertas geometrías de parte podrían acabar levantándose en la “V” de la tablilla. La condición de la tablilla tiene un efecto aquí también. Si una tablilla no se ha limpiado, la hoja de hecho puede situarse más alta en ciertos dientes de la tablilla que en otros, lo que abre la posibilidad de más inestabilidad del proceso.
Las partes más pequeñas pueden levantarse, pero las partes más grandes – especialmente aquéllas largas y delgadas – pueden arquearse hacia arriba y causar estragos en la estabilidad del proceso – material publicitado como “plano para láser” idealmente tendría esfuerzos equilibrados de forma que, cuando una parte se corta de la manera óptima (para controlar los efectos del calor, por ejemplo), no se arquea – incluso partes largas y angostas que son especialmente susceptibles a distorsión. El que esto ocurra o no, depende del material en la cama del corte láser. Si el nivel de distorsión se desconoce, muchos programadores optan por sujetar partes angostas con lengüetas.
Los efectos de onda de la incorporación de lengüetas
Actualmente, el software puede detectar automáticamente y rotar partes para que la dimensión más larga quede orientada de forma perpendicular a las tablillas. Los programadores también pueden establecer diferentes estrategias de incorporación de lengüetas para diferentes tamaños de parte; una parte muy pequeña podría requerir sólo una lengüeta, mientras que partes más grandes hasta cierta dimensión requieren progresivamente más. Más allá de cierta dimensión, el software no pone lengüetas.
“Estas reglas sólo establecen una jerarquía inteligente con base en la posición de la parte en la mesa con relación a las tablillas de soporte”, dijo Boggs.
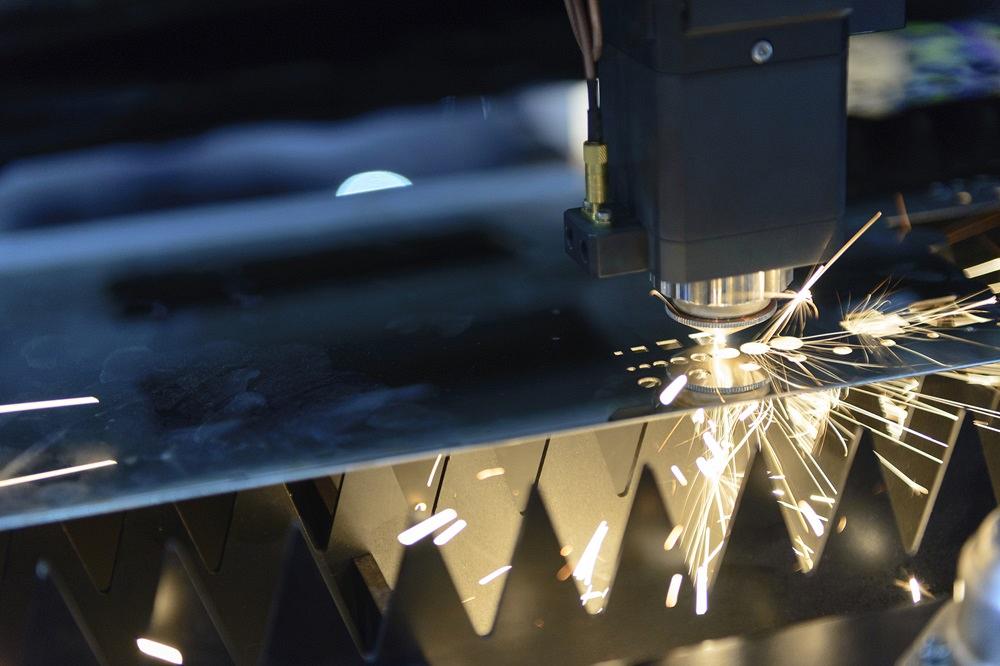
Las partes pueden levantarse de diversas maneras dependiendo del diseño de tablilla, o rejilla, que esté soportando la chapa. Las tablillas generalmente están puestas con varias pulgadas de separación. Las partes se pueden levantar ya sea cayendo entre las tablillas o (para piezas muy pequeñas), cayendo entre los dientes de una tablilla. Phuchit/iStock/Getty Images Plus
“La colocación de lengüetas puede depender también de cuestiones estéticas”, agregó Wood. “Con todo esto, se puede hacer que el software incorpore lengüetas automáticamente con base en las dimensiones X y Y del componente, pero se puede forzar la colocación de ciertas lengüetas cuando surja la necesidad”.
El tamaño de esas lengüetas puede ser controlado para diversos materiales así como diferentes escenarios en torno al gas auxiliar – particularmente cuando se trata de gas auxiliar nitrógeno a alta presión, cuya turbulencia puede hacer que las partes cortadas se levanten y se mueven mucho más que cuando se corta con oxígeno”. “La turbulencia de un corte con nitrógeno a alta presión puede significar que un taller necesitará lengüetas, ya sea más grandes o en mayor número, con base en el tamaño de la parte”, dijo Boggs.
La colocación de lengüetas puede variar dependiendo de los requerimientos del trabajo y de las mejores prácticas en una compañía en particular, dijo Boggs. Por ejemplo, algunas operaciones podrían optar por incorporar lengüetas a las partes directamente en las esquinas, mientras que otras prefieren lengüetas en los bordes rectos y, si una esquina necesita algo para estabilidad, ponen una lengüeta a varias milésimas de pulgada de la esquina real. Todo depende de lo que beneficie a las operaciones corriente abajo, y del acomodo y función final de la parte.
La geometría de la lengüeta puede cambiar dependiendo del espesor y del grado del material, por supuesto, pero también puede cambiar con base en qué operaciones sufrirá una pieza corriente abajo. Esas geometrías de lengüeta afectan la manera en que las lengüetas se separan de la parte.
En el área de descarga del láser, los operadores podrían sacudir las partes para separarlas de un nido antes de hacerlas pasar por una máquina de desbarbado de parte plana. Las micro-lengüetas típicamente dejan una rebaba en la parte y un hueco en el esqueleto. Esto supone que un fabricante deseará desbarbar la pieza para crear un borde perfectamente plano.
Sin embargo, ¿todas las partes necesitan un borde perfectamente plano? ¿Qué pasa con los bordes que estarán ocultos en un ensamble o cubiertos por una soldadura? En estos casos, los talleres podrían optar por saltar el desbarbado y enviar las piezas al formado. Desafortunadamente, debido a que la rebaba sobresale ligeramente, cuando el operador de prensa calibra la parte para el doblez, ésta mueve muy ligeramente el dedo del tope trasero. Eso causa una desalineación de la línea de doblez que, en un taller que fabrica a tolerancias estrictas, puede crecer a muchos otros problemas.
En este caso, dijo Boggs, un programador podría optar por crear lo que él llama una “lengüeta libre de rebaba”, con una geometría que se rompe de manera diferente, creando un hueco muy ligero en el borde de la parte. “El programador puede controlar la profundidad de este hueco”, dijo Boggs, “y éste puede tener sólo unas cuantas milésimas de profundidad, por lo que no hará una diferencia en el acomodo y función final de la parte”. Agregó que la utilidad de esto dependerá de los requerimientos de la parte. Puede funcionar en bordes no expuestos, y puede ayudar a crear un borde libre de rebabas para formado y otras operaciones corriente abajo.
Efectos de la automatización de la remoción de partes
Considere sistemas robóticos y cartesianos que usan sujetadores con ventosas para quitar y apilar partes. “Algunas partes son tan pequeñas”, dijo Boggs, “que no pueden ser levantadas de un nido de manera individual. Podríamos crear dentro de un nido una especie de mini-nido de un grupo de partes unidas con lengüetas”.
Los sistemas que mueven chapas cortadas a torres o a otra automatización introducen otras consideraciones. Los nidos cortados que son transportados de regreso a los estantes de torre podrían requerir más lengüetas para asegurar la estabilidad de las partes cuando la chapa es movida por todo el sistema. Boggs dio otro ejemplo de sistemas de horquillas que quitaban nidos con lengüetas de partes muy grandes en los cuales más micro-lengüetas eran necesarias alrededor del perímetro de la parte, sólo para evitar que las piezas largas o grandes se hundieran y quedaran atrapadas entre dientes individuales de la horquilla.
Destrucción del esqueleto
El uso de horquillas o sistemas de remoción de partes similares aporta otra estrategia de anidado que puede ayudar a simplificar el desanidado y aumenta la confiabilidad del proceso en general: secuencias de destrucción del esqueleto.
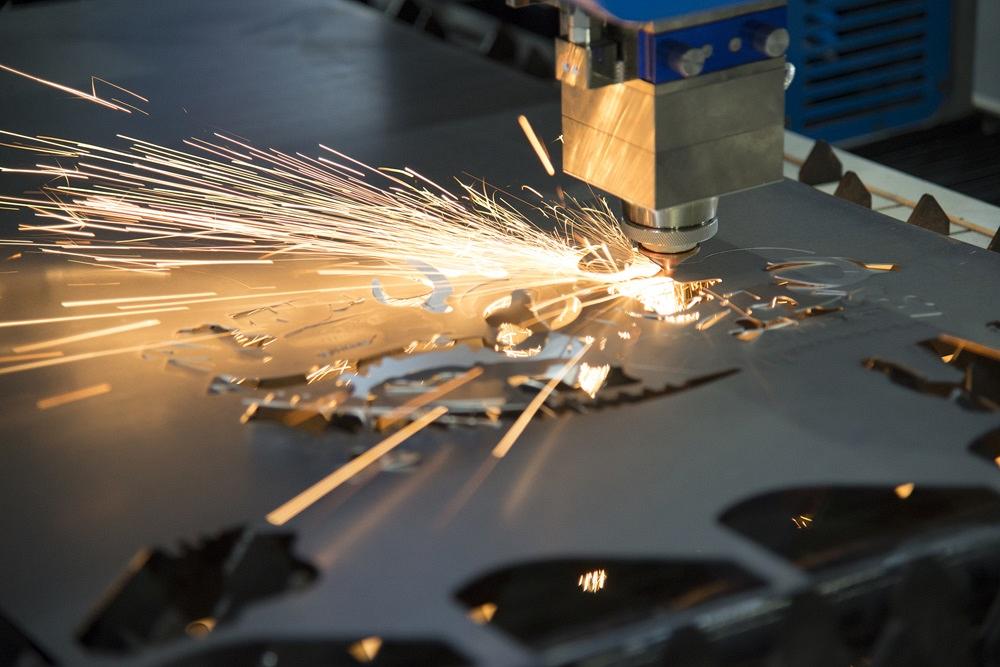
Las partes previamente cortadas y sobrantes (a la izquierda) se levantan. Ésta es la razón de que la cabeza se aleje de esas piezas previamente cortadas o, de ser necesario, se levante para hacer “cobertura aérea”, manteniendo una distancia segura de esas partes levantadas. Phuchit/iStock/Getty Images Plus
“Ésta se configura para considerar la máquina específica que usa un fabricante”, dijo Boggs. Por ejemplo, si la cabeza debe viajar lejos del borde de una hoja para destruir el esqueleto, los sensores de altura de la cabeza de corte necesitan deshabilitarse, para evitar que la cabeza de corte se mueva hacia abajo para buscar una superficie de corte que no está ahí. Sin embargo, enfatizó que los pasos necesarios varían con la máquina que se esté usando.
Si se programan adecuadamente, las secuencias de destrucción de esqueleto pueden aportar cierta eficiencia significativa corriente abajo. Imagine el mismo escenario de remoción por horquilla para ese nido de partes grandes, pero esta vez, en lugar de incorporar lengüetas alrededor del perímetro de las partes para evitar que se hundan, el programador le indica al láser que destruya el esqueleto, cortándolo en piezas pequeñas que pueden caer abajo de las tablillas. Las horquillas entonces levantan esas partes grandes y ponen todo el grupo en una banda transportadora o en otro dispositivo de descarga. Las piezas salen del láser con bordes intachables libres de lengüetas – sin requerir desbarbado u otro procesamiento secundario.
Las fuentes enfatizaron que cuándo y dónde es útil el uso de secuencias de destrucción de esqueletos depende de cómo se muevan las hojas por un sistema láser, incluida la estrategia de descarga de partes. Algunos escenarios podrían beneficiarse de la destrucción de esqueletos, mientras que otros podrían necesitar la estabilidad de un esqueleto con partes aseguradas con lengüetas.
Estrategia de trayectoria de corte
Existe cierto nivel de riesgo siempre que una cabeza de corte necesita atravesar sobre material previamente cortado. Teóricamente, incluso si ocurren levantamientos de partes descontrolados en todo un nido, la cabeza de corte no colisionará si nunca pasa sobre partes previamente cortadas.
“Necesita basarse su inicio y final de la parte, de forma que estén en la ubicación optima en términos de velocidades de corte y viaje de la máquina, pero también en términos de logística”, dijo Wood. “Se trata de asegurarse de no estar atravesando sobre componentes una vez que han sido cortados. También puede usarse una ‘cobertura aérea’ con propiedad de evasión. Si el láser está en un área de la cual no puede salir sin atravesar sobre partes previamente cortadas, la cabeza puede levantarse y atravesar de manera segura a la siguiente ubicación”.
Digamos que una cabeza de corte va del final de una parte inmediatamente hacia el inicio más cercano de la siguiente parte. Eso suena lógico y eficiente, pero ¿qué pasa si este movimiento del final de una parte al inicio de una parte siguiente requiere que la cabeza cruce sobre la parte que acaba de cortar o sobre otros perfiles o formas de parte previamente cortadas, especialmente si éstas no están unidas por lengüetas? Esto podría generar el riesgo de una colisión de la cabeza.
En estos casos, dijo Boggs, los programadores que usan optimización de la trayectoria de herramienta pueden cambian la ubicación del inicio para asegurar que la cabeza atraviese rápido sobre la menor cantidad posible de geometrías de parte previamente cortadas (e idealmente sobre ninguna). Por supuesto, algunos podrían optar por no usar esta optimización de trayectoria de herramienta, dijo Boggs, para cumplir los requerimientos de un trabajo específico. Cambiar el inicio de parte también cambia la ubicación de la primera micro-lengüeta, quizás forzándola a una ubicación que se volverá un borde expuesto o estéticamente crítico de alguna otra manera.
Sin embargo, hacer que esa cabeza se aleje de los perfiles que acaba de cortar es una buena práctica que además puede aumentar la confiabilidad de otras estrategias de anidado, incluido el corte de línea común. “Siempre que corte un grupo de partes que tienen corte común en el nido”, dijo Boggs, “deseará que la cabeza salga de la secuencia alejándose de esas partes”.
Agregó que el ajuste fino en dichas estrategias podría ayudar a un fabricante a aumentar el uso del corte común en general. Hacer que dos partes compartan la misma línea de corte no sólo ahorra material sino que además reduce el tiempo de procesamiento y con frecuencia simplifica el desanidado. Puede ser de uso particular para nidos de una sola parte que implican formas de parte sencillas, como rectángulos o cuadrados. Para nidos más complicados, hacer corte común con cada parte posible “puede volverse muy peligroso desde el punto de vista del levantamiento de parte”, dijo Boggs.
Wood agregó que hacer el corte común confiable para grupos de partes “requiere una secuencia de corte estricta, como por ejemplo hacer primero destrucción de sobrantes internos, y luego hacer los cortes de perímetro de una manera estricta de forma que nunca tenga que trazar sobre áreas que ya han sido cortadas”.
“Además, al trabajar con láseres de fibra de alta velocidad, el corte común puede tener retornos decrecientes”, agregó Wood. “Si está trabajando con un nido único, esto podría no valer la pena, mientras que si tiene un nido repetido, entonces el tiempo invertido ajustando el proceso puede valer la pena”.
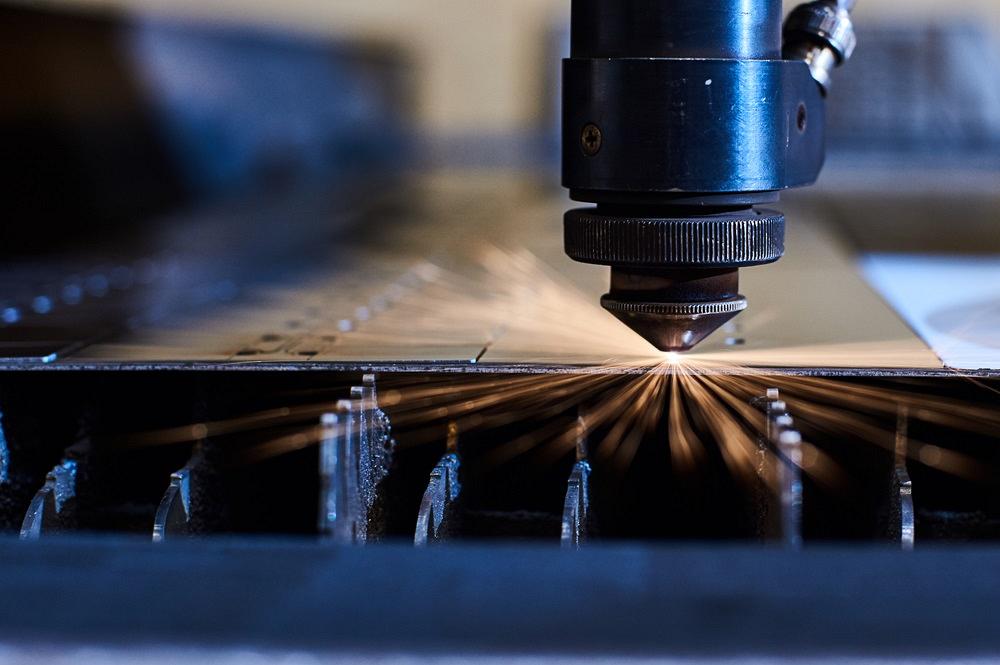
Una cabeza láser corta cerca del borde de una chapa. Si la cabeza debe cortar al borde – ya sea al usar el borde de chapa como el borde de parte o al llevar a cabo una secuencia de destrucción de esqueleto – entran a escena algunas consideraciones especiales. Dependiendo de la máquina, los sensores de altura de una cabeza necesitan desactivarse temporalmente. sandsun/iStock/Getty Images Plus
Las fuentes agregaron que esto no significa que un programador deba evitar el corte común por completo. Todo depende de qué tan rápida y confiablemente puedan generarse los programas de corte común, y de qué tan estables sean las secuencias de corte. Identificar grupos específicos de partes que funcionan bien bajo circunstancias específicas – colocación en un nido (con relación a las tablillas), con una estrategia de trayectoria de corte inteligente – puede ayudar a hacer uso del corte común y al mismo tiempo seguir manteniendo la estabilidad del proceso.
El papel del calor
El calor hace que el material se mueva, a veces de maneras no deseadas, y la manera en que el calor se disipa puede hacer la diferencia en la confiabilidad del proceso de corte. El corte concentrado en un área pequeña puede dar lugar a movimientos de parte inesperados, que incluyen levantamientos.
Como lo explicó Wood, “si está cortando un grupo de partes más pequeñas, ¿hay opciones de disipación del calor que podría usar, que podrían ayudar al proceso y reducir el levantamiento? Una opción es pre-perforar todo el nido antes de cortar los perímetros de las partes, para limitar la acumulación de calor”. Tener un paso de pre-perforación separa del proceso de corte el proceso de perforación de calor intensivo. Esto permite que el calor se disipe y, a fin de cuentas, que las partes cortadas permanezcan estables dentro del nido.
Perfeccionamiento del nido
Las estrategias de anidado son específicas para el taller y para la aplicación. El software podría usar por defecto ciertas reglas cuando se trata de ancho de entramado, geometría de micro-pestañas y grados y espesores de material más específicos. Algunas aplicaciones podrían tener restricciones de grano, lo que significa que una pieza debe colocarse de una manera específica para que el grano del material vaya en cierta orientación, ya sea por razones de estética o para asegurar la exactitud en el formado.
También entran en la ecuación los requerimientos de productividad. “Mucho del corte láser se basa en reglas”, agregó Wood. Los estilos del inicio, los estilos y tamaños de las lengüetas, la dirección de corte, la secuencia de corte, uso de cobertura aérea para evasión de una parte, asegurarse de no golpear un componente levantado. En algunos casos, las simulaciones pueden ayudar también. Sin embargo, por otra parte, no hay mucho tiempo para que un programador le siga el ritmo a un láser de fibra de alta velocidad. La meta es integrar lógica en las preferencias de manufactura de un software de anidado, para hacer el proceso lo más automático posible”.
La situación ideal implica el anidado automático, ajustado finamente con reglas que creen nidos confiables, una y otra vez. Habrá excepciones, por supuesto, las cuales requerirán pequeños ajustes manuales.
Lo ideal, dijeron las fuentes, es mantener una comunicación constante entre la programación y la planta de producción, con el propósito de impulsar el rendimiento general para todos – en el anidado, pasando por corte láser, y más allá. Y cualquiera que sea la estrategia específica que adopte el departamento de programación de un taller, todo empieza por asegurar la estabilidad del proceso de corte. Después de todo, un proceso de corte poco confiable puede crear serios dolores de cabeza virtualmente en cualquier otro lado de la planta de producción.
About the Author
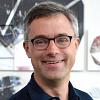
Tim Heston
2135 Point Blvd
Elgin, IL 60123
815-381-1314
Tim Heston, The Fabricator's senior editor, has covered the metal fabrication industry since 1998, starting his career at the American Welding Society's Welding Journal. Since then he has covered the full range of metal fabrication processes, from stamping, bending, and cutting to grinding and polishing. He joined The Fabricator's staff in October 2007.
About the Publication
Compañías Relacionadas
subscribe now
FMA Communications ha introducido al mercado la edición en Español de la revista The Fabricator. Esta versión consiste del mismo tipo de artículos técnicos y sección de lanzamientos de nuevos productos que actualmente presentan el personal de primera categoría de Fabricator en Inglés.
start your free subscription- Podcasting
- Podcast:
- The Fabricator Podcast
- Published:
- 05/14/2024
- Running Time:
- 62:12
Cameron Adams of Laser Precision, a contract metal fabricator in the Chicago area, joins the podcast to talk...
- Trending Articles
Anidado para la estabilidad del corte láser
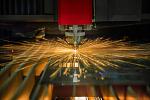
Seguridad en la soldadura desde el inicio
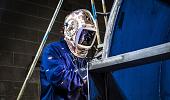
El software guía a los soldadores a través de instrucciones de trabajo
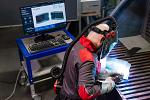
La rueda reduce las fuerzas de empuje/tracción hasta en un 50%

Gafas protectoras diseñadas para trabajadores que necesitan lentes correctivos
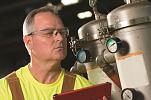
- Industry Events
Laser Welding Certificate Course
- May 7 - August 6, 2024
- Farmington Hills, IL
World-Class Roll Forming Workshop
- June 5 - 6, 2024
- Louisville, KY
Advanced Laser Application Workshop
- June 25 - 27, 2024
- Novi, MI
Precision Press Brake Certificate Course
- July 31 - August 1, 2024
- Elgin,