Editor-in-Chief
- FMA
- The Fabricator
- FABTECH
- Canadian Metalworking
Categories
- Additive Manufacturing
- Aluminum Welding
- Arc Welding
- Assembly and Joining
- Automation and Robotics
- Bending and Forming
- Consumables
- Cutting and Weld Prep
- Electric Vehicles
- En Español
- Finishing
- Hydroforming
- Laser Cutting
- Laser Welding
- Machining
- Manufacturing Software
- Materials Handling
- Metals/Materials
- Oxyfuel Cutting
- Plasma Cutting
- Power Tools
- Punching and Other Holemaking
- Roll Forming
- Safety
- Sawing
- Shearing
- Shop Management
- Testing and Measuring
- Tube and Pipe Fabrication
- Tube and Pipe Production
- Waterjet Cutting
Industry Directory
Webcasts
Podcasts
FAB 40
Advertise
Subscribe
Account Login
Search
How fab shops can pay for capital equipment purchases with tax savings
Fabricators who design or develop processes to manufacture parts may qualify for an R&D tax credit
- By Dan Davis
- May 18, 2022
- Article
- Shop Management
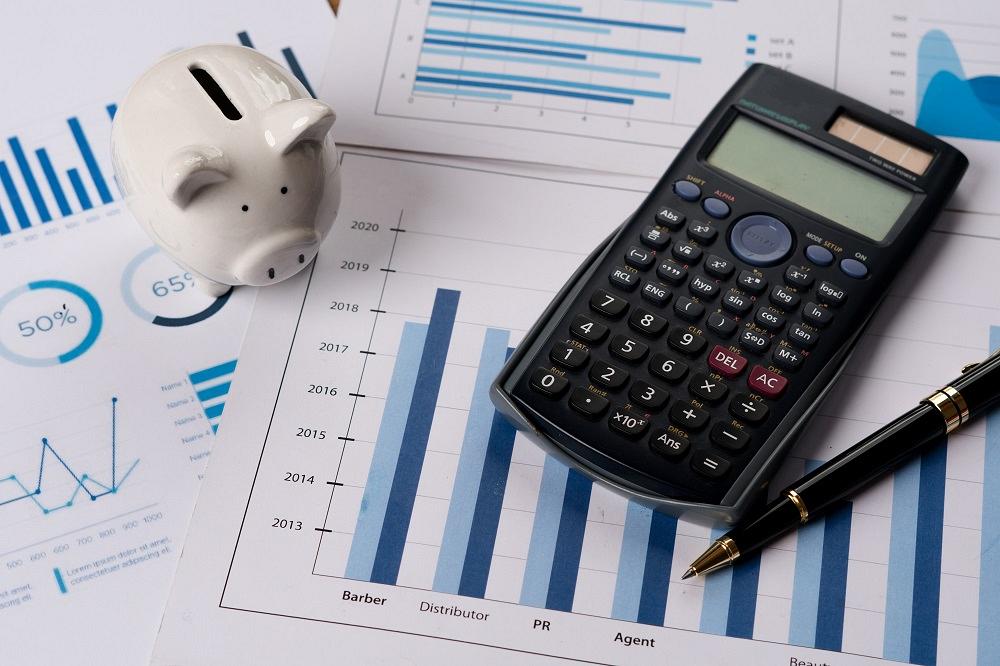
John Madsen, vice president/manufacturing practice leader for Black Line Group, says that many of the activities involved in preparing for a new job to hit the shop floor can qualify for the R&D tax credit. Perawit Boonchu/Getty Images
The R&D tax credit is a tool that many manufacturers and metal fabricators might have heard about but, frankly, rarely use. The thinking is logical: “We don’t have an R&D department.” But that thinking is flawed.
The tax credit, also known as the Research and Experimentation tax credit in some circles, acknowledges that companies involved in the development, design, or improvement of products, processes, formulas, or software are worthy of deducting the expenses associated with these activities in their tax returns. Plenty of manufacturers use this tax credit because they produce an end product. On the other hand, many metal fabricators and contract manufacturers think because they don’t have a product line that they are excluded from pursuing these potential cost savings. John Madsen, vice president and manufacturing practice leader for Black Line Group, argues that this isn’t necessarily the case. He states that almost any preparation work done for a new job hitting the shop floor could qualify for the R&D tax credit.
Madsen has direct knowledge of high-mix/low-volume manufacturing because he once ran a contract manufacturing company before moving on to his current role. It’s also one of the reasons that he is the chair of the Minnesota Precision Manufacturers Association’s board of directors. He’s taken that experience and now tries to convince other fab shops and contract manufacturers that their work is a perfect candidate for this particular type of tax savings.
This discussion is timely because the R&D tax credit is no longer a temporary benefit. As part of the Protecting Americans from Tax Hikes Act of 2015, the tax credit was permanently extended. Before this law was passed, Congress had to take action each year to extend it another tax season.
The FABRICATOR chatted with Madsen to find out why many metal fabricating companies don’t take advantage of this tax credit and what they can do to make a solid case for the tax savings and that will stand up to Internal Revenue Service scrutiny.
The FABRICATOR: So, can any aspect of product design and prototype development be applied to the R&D tax credit?
Madsen: Yes. And if you look at it at a superhigh level, it can even be sales.
I’m not talking about a salesperson taking a call from someone ordering item B on page 238 of the company catalog. Of course, there’s no R&D in that. However, if a well-educated salesperson is out there and he’s telling a customer that a part doesn’t have to be thick because a rib can be a part of the design or that welding is not necessary because it can be formed on a press brake, that’s important because the company will include that salesperson’s idea to lower the cost or make it easier to manufacture along with the quote to print the job as is.
If you’ve got the salesperson out there encouraging, wearing their fit-form-and-function hat on, and helping that customer understand what’s possible, you can find elements that apply to the R&D tax credit even in that.
FAB: What about quoting activities?
Madsen:The government doesn’t like the word quoting, so we’ve kind of shifted away from that a little bit. But what are you really doing? You’re designing a process in order to put a price to it.
You have to decide which machine to use, how long the work will take, what the tolerances are, and what the volume is, for example. These engineers are involved in trying to answer the quote, and that’s part of the process of developing a price.
You’re also engineering a process to make that part. So whether or not you get that job, those are qualifying activities.
FAB: Can you describe those steps that might be a part of “engineering the process”?
Madsen: Certainly. From the engineer’s point of view, you have to lay out your flat blank and program the laser or the turret. Someone has to figure out how the brake will be set up and then work through one to three parts to get the bending sequence down. That's all part of it.
Let’s take it to quality. Writing up the PPAP [production part approval process] can be a qualifying activity. Let’s face it. You can’t ship the part out the door unless it’s been qualified and you meet the requirements.
FAB: Does all this hold up when IRS accountants start looking at the paperwork?
Madsen: Yes, it will. We’ve been doing this for 20 years, and only 1.3% of all the clients we’ve helped have ever been challenged by the IRS.
We defend everything that is submitted to the IRS, and we actually give audit insurance to the client as part of our fee.
We follow the tax law. We understand the tax law. We don’t claim more than we’re allowed, and we try not to claim less than we’re allowed.
FAB: Do all tax accounting firms consider these types of manufacturing activities to be items that can be claimed under the R&D tax credit?
Madsen: I worked with a client last week who asked me, “How come you quoted me $230,000 in R&D tax credits and my CPA quoted me $30,000? Who do I believe?” I said, “Let me just take a wild guess. Your CPA only took your engineers.” That was the case.
The CPA didn’t claim the quality personnel or the estimators. He was just taking the supersafe approach, not fully understanding the manufacturing world.
So, Mr. Manufacturer, who’s never taken the R&D tax credit before, is doing cartwheels at $30,000, but not realizing he left thousands of dollars on the table.
FAB: How do you instruct a job shop or a contract manufacturer to begin collecting the information they need to claim more activities against the R&D tax credit?
Madsen: Typically, the smaller shops are not as well organized or might not have all of the details in an ERP system or something similar. That’s OK because the IRS will allow you another form of collecting this information, which is basically interviewing the employees.
You can have a tooling manager speak for all the toolmakers in the shop, for example. He might say that Hank is the best toolmaker and he gets all the work because he is so good. He’s developing tooling. The manager might point out that Tony over there is an apprentice and he’s just sharpening tools. Hank might spend 80% of his day doing R&D, whereas Tony just sharpens tools or does die repair. Those are the things that you need to vet out and make sure that what we are claiming as an industry is sustainable, if it is challenged.
FAB: Is it hard to get owners and managers to take full advantage of the R&D tax credit, especially when they are under pressure to get parts out, not necessarily spending a ton of time dealing with taxes?
Madsen: You know, my daddy always said, “If it sounds too good to be true …”
But let me offer you a great example. Somebody here in the Twin Cities makes custom clean rooms. I love the word custom. The company has about $13 million in annual revenue.
I called him and said, “Hey, you’re on my way home. I saw your website. I think I can help you.” And he replied, “You know, I’ve had three firms in here in the past that my CPA recommended. They all told me that I don’t do R&D.”
I continued by saying, “Would you mind if I stop by? I really believe you do.” It was a moment when you can literally hear his eyes roll over the phone. But he told me to stop by.
Like most manufacturers, the best parts they make are out in the lobby or in the conference room. They’re showing off their skills. I walked in and saw a custom window, about 12 by 12 in., wrapped in sheet metal in the lobby. I picked it up, and he walked into the lobby. I should have said hello first, but I said, “You’re forming this against the edge of the sheet metal, burr down. If you did it burr up and folded it in, that burr would be gone. You wouldn’t have to spend 15 minutes grinding this window.” His mouth kind of dropped open. He said, “You’re no ordinary CPA, are you?” I replied, “I never claimed to be a CPA.”
Fast-forward, and we found him $1.3 million in tax savings. He ended up buying a turret punch press, a laser, and a brake. That just did my heart good.
FAB: Do you think that this can be construed as bending the rules to be able to claim the tax savings associated with the R&D tax credit?
Madsen: I don’t think so. If you’re in this industry, you’re fighting to keep employees, and you’re adjusting wages for your good people. Health care is kicking your butt, and now you have to worry about trying to find material and probably overpaying for material. With these owners just dishing out the cash for all of these areas, how do they reinvest in the business when they’re only making maybe 4 cents out of every sales dollar that comes in the front door? That’s tough, when you want to lay a million down for a new piece of equipment.
The R&D tax credit can be that vehicle to help these people reinvest.
FAB: What type of average return can a job shop or contract manufacturer expect if it pursues these potential tax savings?
Madsen: I would rather talk to them or somebody before talking about a figure because it’s about people and activities. If a majority of your work is repeat, unless there’s a revision or you’ve improved the product or the process, the R&D is gone. It all depends on the mix in your business.
If you’re seeing 80% of your business being new each and every year and you're growing, not losing money, and you’re about $6 million in revenue with maybe 40 employees, you could see somewhere in the neighborhood of maybe $80,000. That just a hypothetical example, of course.
In R&D tax credits, it’s a real opportunity, but you have to be profitable and paying taxes. If you’ve got net operating losses, you can still apply for the R&D tax credit and roll those credits forward up to 20 years. But, as somebody that ran a business, why would I pay someone like me to put credits in the bank when I need that money to run my business?
So, for those clients, I often advise them to look at the employee retention credit. There are a lot of opportunities around that as well.
FAB: Do your manufacturing clients continue their R&D tax credit efforts after the first year?
Madsen: Once a manufacturer gets a taste of this, there’s no turning back. They want to keep up with it.
Ninety-four percent of our clients repeat every year. The majority of the other 6% were either acquired by another company, they’re doing it on their own, or they had net operating losses that year.
FAB: We’ve talked about the activities involved in developing a product design and proving out a manufacturing process that can be applied toward the R&D tax credit. Can a company claim the development of software or some sort of information technology investment as an R&D tax credit?
Madsen: It could. I’ll try and simplify it just a little bit. If a company owner is buying two seats of SolidWorks, can he claim R&D on the software? No. Why? Because he’s buying a canned package. The manufacturing company is only training on how to use SolidWorks, and that is not a qualifying activity.
Now, if you have SolidWorks in your shop and you want to connect it to your accounting software so that you can keep track of raw materials and you bring in a third party or do it internally, that could qualify for R&D tax credits.
FAB: What specifically is being looked at within a company’s operations that could qualify for the R&D tax credit?
Madsen: Within the R&D tax credit, there are three main areas to get qualifying costs. Wages are one. That is probably 90% or greater of the R&D tax credit. And it’s just basically the people within your organization that are involved in part and process development.
The other area is supplies. An example here might be paying for a new type of sheet metal that’s slightly cheaper than what you normally use. So you buy $500 worth and find out that it’s junk. Well, that $500 could go right back into your R&D tax credit under qualified cost because you were intending to develop or improve your product or process.
Often the R&D tax credit reduces your risk to try something different or maybe expand your manufacturing footprint. Maybe it doesn’t work out That’s OK. Try again. That’s the whole point.
The other area is contractor research. Say you can’t get the paint booth to paint a single part, so you hire somebody to straighten it all out. That could be a contractor. Or perhaps you have some sheet metal back there and the certs are gone. So you nip a piece off and send it to the metallurgist. He comes back and provides the correct material makeup. That also could be a third party. So, even though it’s a small part, it’s something else that qualifies.
FAB: Do you feel like you are making the IRS a little more informed about manufacturing as you prepare these cases?
Madsen: God, I hope so. You know, this industry has been so good to me that instead of retiring, this is what I chose to do to give back to the industry.
Looking for Additional Tax Savings?
Madsen believes the R&D tax credit is a great way for job shops and contract manufacturers to find funds to reinvest in the company. He also believes the employee retention credit (ERC) often can help smaller manufacturers—if they qualify—more than the R&D tax credit.
Unfortunately, the ERC is misunderstood, particularly coming out of the pandemic. As a result, for many manufacturers across the country, ERC money remains unclaimed. Madsen offered three misconceptions about the ERC in an effort to make it clear that manufacturers shouldn’t be ignoring this opportunity:
- Misconception No. 1—“We are a manufacturer and were deemed an essential business during the pandemic. We remained open and were never fully or even partially suspended. Therefore, we do not qualify.” That’s what you hear from small companies, but they should know that they are misunderstanding the IRS definition of fully or partially suspended, according to Madsen.
- Misconception No. 2—“We received a Paycheck Protection Program loan. I know you can’t double-dip on the PPP and ERC, so there are no eligible wages left. Therefore, we don’t qualify.” Madsen said that line of thinking is incorrect. PPP wages are calculated on 10 weeks of payroll, and the eligibility period to use the funds is up to 24 weeks. This leaves eligible wages to qualify for the ERC, and typically the impact of PPP on the eligible ERC amount is relatively minor.
- Misconception No. 3—“We have been told we don’t qualify because our revenue did not drop enough.” That’s false, Madsen said. For companies with 100 or fewer employees in 2019, just because their revenue didn’t drop by more than 50% in Q2, Q3, or Q4 2020 compared to the same quarter in 2019 doesn’t mean they don’t qualify. For companies with 500 or fewer employees in 2019, just because their revenue didn’t drop by more than 20% in Q1, Q2, or Q3 2020 compared to the same quarter in 2019 doesn’t mean they don’t qualify.
“Most manufacturers do qualify based on a qualitative argument showing how their business was “partially suspended” due to COVID-19 governmental restrictions at the national, state, or local level. This is where the governmental restrictions have had at least a nominal impact on business operations,” Madsen said. A nominal impact is defined as being a 10% or more change in revenue, productivity, or some other metric from a similar period before the pandemic, he added.
The governmental restrictions that could have had made an impact on manufacturing business come in one of three forms, Madsen said. Only one is required for qualification. Examples include:
- Productivity impact. Because of governmental orders related to social distancing, cleaning, or 10-day quarantine restrictions, the productivity of a given department was affected by more than a nominal amount compared with the same quarter in 2019.
- Supply chain impact. Key suppliers might have been experienced significant delays in the delivery of parts and supplies because of governmental orders. This is proven out by comparing order-to-delivery times of suppliers to the same quarter in 2019.
- Market segment impact. Customers in industries such as automotive, aerospace, and medical have been nominally impacted by governmental orders, according to Madsen. This is analyzed by comparing revenue by market segment to the same quarter in 2019.
“Simply put, if you have experienced even a slight reduction in gross revenue in any calendar quarter from Q2 2020 through Q3 2021, you stand a very good chance of qualifying,” Madsen said.
For those interested in learning more about the ERC, Madsen will be a part of the conference agenda at FABTECH, Nov. 8-10, at Georgia World Congress Center in Atlanta.
About the Author
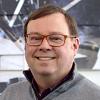
Dan Davis
2135 Point Blvd.
Elgin, IL 60123
815-227-8281
Dan Davis is editor-in-chief of The Fabricator, the industry's most widely circulated metal fabricating magazine, and its sister publications, The Tube & Pipe Journal and The Welder. He has been with the publications since April 2002.
subscribe now
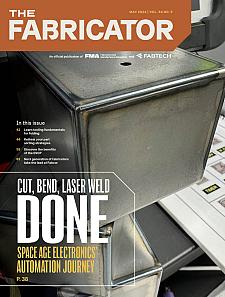
The Fabricator is North America's leading magazine for the metal forming and fabricating industry. The magazine delivers the news, technical articles, and case histories that enable fabricators to do their jobs more efficiently. The Fabricator has served the industry since 1970.
start your free subscription- Stay connected from anywhere
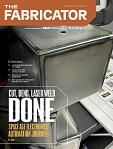
Easily access valuable industry resources now with full access to the digital edition of The Fabricator.
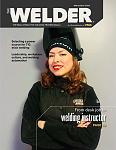
Easily access valuable industry resources now with full access to the digital edition of The Welder.
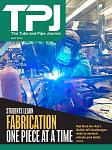
Easily access valuable industry resources now with full access to the digital edition of The Tube and Pipe Journal.
- Podcasting
- Podcast:
- The Fabricator Podcast
- Published:
- 04/16/2024
- Running Time:
- 63:29
In this episode of The Fabricator Podcast, Caleb Chamberlain, co-founder and CEO of OSH Cut, discusses his company’s...
- Industry Events
16th Annual Safety Conference
- April 30 - May 1, 2024
- Elgin,
Pipe and Tube Conference
- May 21 - 22, 2024
- Omaha, NE
World-Class Roll Forming Workshop
- June 5 - 6, 2024
- Louisville, KY
Advanced Laser Application Workshop
- June 25 - 27, 2024
- Novi, MI