Contributing Writer
- FMA
- The Fabricator
- FABTECH
- Canadian Metalworking
Categories
- Additive Manufacturing
- Aluminum Welding
- Arc Welding
- Assembly and Joining
- Automation and Robotics
- Bending and Forming
- Consumables
- Cutting and Weld Prep
- Electric Vehicles
- En Español
- Finishing
- Hydroforming
- Laser Cutting
- Laser Welding
- Machining
- Manufacturing Software
- Materials Handling
- Metals/Materials
- Oxyfuel Cutting
- Plasma Cutting
- Power Tools
- Punching and Other Holemaking
- Roll Forming
- Safety
- Sawing
- Shearing
- Shop Management
- Testing and Measuring
- Tube and Pipe Fabrication
- Tube and Pipe Production
- Waterjet Cutting
Industry Directory
Webcasts
Podcasts
FAB 40
Advertise
Subscribe
Account Login
Search
Die Basics 101: Common causes of slug pulling
- By Art Hedrick
- Updated July 18, 2018
- December 12, 2006
- Article
- Bending and Forming
Slug pulling is a serious problem in a stamping operation. Addressing the issue requires first understanding why the slugs are pulling.
What Is Slug Pulling?
When a pierce punch creates a hole, it also produces scrap, usually referred to as a slug. Slug pulling occurs when the slug sticks to the punch face upon withdrawal and comes out of the button, or lower matrix.
If a slug falls off the punch and onto the strip or part, it can damage the part and die. Keeping the slug down in the matrix or, better yet, completely pushing it out of the die is the desired scenario.
What Causes Slug Pulling?
Many factors contribute to slug pulling. Among them are trapped air; large cutting clearances; extremely fast piercing operations; sticky lubricants; improperly demagnetized punches; and fatigued or insufficient spring ejectors.
1. Trapped air/ vacuum pockets. The slug generated during the piercing process has some curvature. The curved, void areas where air is trapped, creating a vacuum action. During the perforating process, a tight seal is maintained around the punch perimeter. When the punch is withdrawn, this seal prevents the slug from coming off the punch (Figure 1a). Keep inmind that the only portion of the piercing punch that makes contact with the metal is a localized zone around the punch's outside diameter. Even punches with angularity make only localized contact with the metal (Figure 1b).
Trapped air must be allowed to escape to reduce the amount of vacuum. This is done by creating a small air vent in the center of the pierce punch, which allows the otherwise trapped air to exhaust itself from the vent hole and reduce the suction. Losing suction breaks the seal between the slug and the pierce punch and allows the slug to fall (Figure 2a).
When piercing punches that are too small to vent are used, other means of addressing slug pulling most likely will be necessary. Also keep in mind that addressing the trapped air probably won't solve the slug pulling issue completely, but it will certainly help.
2. Larger cutting clearances. Although using engineered or larger cutting clearances can result in much greater punch and matrix life, there is one drawback to doing so. As the clearance gets larger, compression on the slug decreases, which increases the chances of slug pulling.
When smaller cutting clearances are used during the perforating process, both the slug and metal outside the slug are forced into compression. After the slug is cut free, it decompresses and remains in the matrix. This is because the decompressed slug now has an interference or press fit into the matrix.
In simple terms, when greater cutting clearances are used, the slug will be slightly smaller than the hole in the matrix, which means it may be pulled from the matrix by the punch, resulting in slug pulling. Reducing the cutting clearance certainly can help this problem, but it also can shorten punch life and increase sharpening frequency. Rather than reducing the cutting clearance, it isrecommended stampers try a few methods that will be discussed in the next part of this series (Figure 2b).
3. Oil / lubricant problems. Using heavy, thick, highly viscous oils and deep-drawing lubricants only adds to slug pulling problems. Unfortunately, these compounds often are necessary for forming dies to perform correctly.
Over time heavy oils and compounds can become coagulated and sticky. Thick, sticky compounds can cause slugs to stick to punches. Periodically cleaning the cutting components can help to resolve this sticky residue problem. Other methods to resolbe this problem will be discussed in Part XII.
4. Magnetized punches. Punches and die sections often are sharpened with a surface grinder. Most surface grinders secure the sections and punches to be ground by a high-power electro- or conventional magnet (Figure 3). Any ferrous metal that comes in contact with this magnet becomes slightly magnetized.
After the die components have been ground, they then must be demagnetized fully. This process is accomplished by using a commercially available demagnetizing unit. Magnetized pierce punches and die sections can cause slugs and other magnetic debris to be picked up and carried through the tool.
5. Weak or fatigued spring ejectors. Spring ejectors often are used in piercing and cutting punches. These small, spring-loaded pins push the slug from the punch face after cutting has taken place. If the spring behind the punch fails or fatigues, slug pulling can occur. Periodically inspecting and replacing springs is a necessary part of a good die maintenance program(Figure 4).
Slug pulling can have disastrous consequences. A single slug carried through a progressive die can damage every tool in the station. The next part in this series will discuss methods for resolving slug pulling problems.
Editor's Note:
Part I provides an introduction to stamping.
Part II covers various forming operations.
Part III discusses several production methods used to make stamped parts.
Part IV and Part V cover common stamping die components.
Part VI explains specialty die components.
Part VII provides an overview of metals used in stamping, and Part VIII continues this discussion.
Part IX covers the mechanical properties as well as behavioral characteristics of metals.
Part X begins an in-depth look at the metal cutting process.
Part XI defines slug pulling and common causes.
Part XII describes methods for resolving slug-pulling problems.
Part XIII discusses various specialty metal cutting methods used in stamping operations.
Part XIV explains fineblanking and GRIPflow®.
Part XV describes several bending methods—wipe, coin relief, pivot, and V bending.
Part XVI continues the discussion of bending in stamping operations, focusing on rotary and reverse U bending. It also addresses the advantages and disadvantages of rotary bending.
Part XVII discusses the fundamentals of drawing and stretching.
About the Author
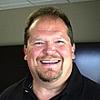
Art Hedrick
10855 Simpson Drive West Private
Greenville, MI 48838
616-894-6855
Related Companies
subscribe now
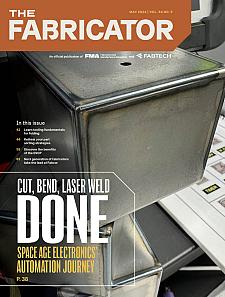
The Fabricator is North America's leading magazine for the metal forming and fabricating industry. The magazine delivers the news, technical articles, and case histories that enable fabricators to do their jobs more efficiently. The Fabricator has served the industry since 1970.
start your free subscription- Stay connected from anywhere
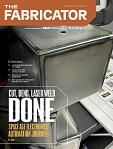
Easily access valuable industry resources now with full access to the digital edition of The Fabricator.
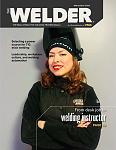
Easily access valuable industry resources now with full access to the digital edition of The Welder.
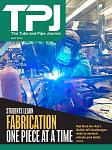
Easily access valuable industry resources now with full access to the digital edition of The Tube and Pipe Journal.
- Podcasting
- Podcast:
- The Fabricator Podcast
- Published:
- 04/16/2024
- Running Time:
- 63:29
In this episode of The Fabricator Podcast, Caleb Chamberlain, co-founder and CEO of OSH Cut, discusses his company’s...
- Trending Articles
Capturing, recording equipment inspection data for FMEA
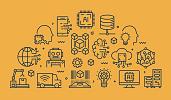
Tips for creating sheet metal tubes with perforations
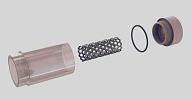
Are two heads better than one in fiber laser cutting?
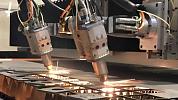
Supporting the metal fabricating industry through FMA
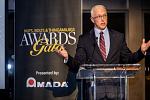
Omco Solar opens second Alabama manufacturing facility
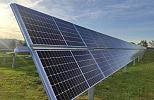
- Industry Events
16th Annual Safety Conference
- April 30 - May 1, 2024
- Elgin,
Pipe and Tube Conference
- May 21 - 22, 2024
- Omaha, NE
World-Class Roll Forming Workshop
- June 5 - 6, 2024
- Louisville, KY
Advanced Laser Application Workshop
- June 25 - 27, 2024
- Novi, MI