General Manager, Americas
- FMA
- The Fabricator
- FABTECH
- Canadian Metalworking
Categories
- Additive Manufacturing
- Aluminum Welding
- Arc Welding
- Assembly and Joining
- Automation and Robotics
- Bending and Forming
- Consumables
- Cutting and Weld Prep
- Electric Vehicles
- En Español
- Finishing
- Hydroforming
- Laser Cutting
- Laser Welding
- Machining
- Manufacturing Software
- Materials Handling
- Metals/Materials
- Oxyfuel Cutting
- Plasma Cutting
- Power Tools
- Punching and Other Holemaking
- Roll Forming
- Safety
- Sawing
- Shearing
- Shop Management
- Testing and Measuring
- Tube and Pipe Fabrication
- Tube and Pipe Production
- Waterjet Cutting
Industry Directory
Webcasts
Podcasts
FAB 40
Advertise
Subscribe
Account Login
Search
A la caza de esqueletos
Cómo anidar para un flujo óptimo
- By Doug Wood
- October 20, 2020
- Article
- Laser Cutting
El anidamiento estratégico es un acto de equilibrio entre la fabricación de chapas y placas. Desea un rendimiento de material óptimo y una estabilidad del proceso de corte, pero también debe considerar las operaciones posteriores.
Aun cuando los fabricantes entienden que el anidado es fundamental para una eficiencia óptima, con frecuencia aprenden de la peor manera que implementar tecnología no reemplaza la necesidad de tener un panorama completo de cómo los procesos de anidado afectan el flujo de las piezas de trabajo. Leer las claves que va dejando el esqueleto puede ayudar a tener un panorama más preciso del proceso de anidado y servir como la base de lanzamiento para una estrategia para lograr los resultados que se buscan.
Después de ver los “huesos” de su proceso de anidado, es posible que usted descubriera que podría estar generando nidos más eficientes. Sin embargo, sepa que vale la pena considerar si los resultados que está buscando son resultados que realmente obtendrá si hace un cambio. Sí, el esqueleto puede decir qué tan bien se está maximizando el material y qué tan eficientemente está cortando la máquina, pero saber qué hacer con esa información puede ser complicado. El anidado es un paso de un proceso de producción con muchas partes móviles, por lo que se requiere equilibrar los beneficios de un mayor rendimiento del material con el flujo del trabajo en todo el taller.
Si usted trabaja en un taller grande que procesa cantidades significativas de material o si trabaja frecuentemente con material caro, incluso cambios menores en la utilización de la chapa pueden dar resultados impresionantes. Los talleres de tamaño mediano a pequeño también podrían tener ganancias significativas con nidos más eficientes.
Independientemente de sus ahorros potenciales, el reto es encontrar el equilibrio correcto entre un mayor rendimiento del material y la mínima cantidad de piezas en proceso (WIP, por sus siglas en inglés). Si las partes se mueven sin problemas corriente abajo, la pregunta real es si se pueden enviar más partes corriente abajo sin que el barco se tambalee ni se hunda.
Consideraciones de la mezcla de partes
Aun cuando expandir la mezcla de partes podría aumentar la eficiencia del anidado, también podría aumentar el tiempo que gastan los operadores corriente abajo en configuraciones de máquina, considerando cambios frecuentes de material y herramental. Además de demorar las operaciones secundarias, una mezcla mayor de partes en un nido podría mantener al departamento de soldadura esperando la última parte en el ensamble antes de continuar con un trabajo, o mantener la línea de pintura esperando el último componente antes de un cambio de color.
Al considerar todo el flujo de trabajo de un taller, hay que asegurarse de investigar cuánto tiempo realmente tarda cargar y cambiar herramientas entre trabajos, cambiar el gas de corte en un láser, o cargar programas NC diferentes en un controlador. Además, ¿el sistema CAM permite editar un nido generado automáticamente?
También ayuda a entender cuánto tiempo y esfuerzo se invierten en manejar y rastrear partes desanidadas, especialmente si los operadores de láser o punzón se la pasan pensando en maneras creativas de apilar las partes alrededor de una máquina.
Cambiar los procesos de anidado puede brindar enormes beneficios si se considera cuidadosamente la travesía de las partes corriente abajo. Las eficiencias pueden mejorar incluso si se agregan maquinaria y personal en respuesta a una mayor demanda. Independientemente de su situación, investigar cuidadosamente las necesidades reales de un taller es el punto correcto para empezar.
No todos los nidos se crean iguales
El anidado dinámico típicamente es la manera más rápida y más fácil de lidiar con una variedad de partes. El anidado dinámico de forma real considera las formas únicas de varias partes y las anida en chapas. Si, por ejemplo, se tiene una parte formada como un marco de ventana, puede anidarse otra parte dentro de la primera para utilizar la chapa por completo. Es muy probable que no se vea una cantidad significativa de material que se queda en el esqueleto con el anidado dinámico, debido a que está diseñado para utilizar automáticamente todo el material que se pueda.
Uno de los avances de anidado más recientes es el anidado por lotes, el cual conlleva el anidado a través de varias chapas a la vez para la mejor utilización global de material. Esto prepara el camino para un mejor rendimiento debido a que puede anidarse una gama más amplia de partes de manera eficiente a través no sólo de una sino de varias chapas.
Este nido muestra el potencial de alta utilización de material, estabilidad de las partes y facilidad de clasificación.
El anidado estático se usa típicamente cuando un taller hace con frecuencia el mismo trabajo, por lo que los anidados estáticos pueden reusarse cuando sea necesario. Dependiendo de las fortalezas de su CAM o sistema de anidado, el tiempo que se requiere para hacer un cambio a un trabajo existente puede mermar más los ahorros que se obtuvieron al aumentar el rendimiento del material.
Aplicar corte de línea común puede ayudar a obtener eficiencia en el corte, especialmente en ciertos arreglos de nido. Sin embargo, en algunos casos es poco probable crear ganancias importantes en tiempo, rendimiento del material o mano de obra.
Dicho lo anterior, cuando se trata de maximizar materiales, el uso del tamaño de chapa ideal podría también ser un factor. Esto no necesariamente significa que se necesite tener varios tamaños de chapa a la mano, pero es buena idea hacer algunos ensayos o corridas de prueba mientras se deja que el software de anidado considere diversos tamaños de chapa y haga la elección correcta con base en la mezcla de partes.
Analice el esqueleto y observe la integridad de las partes y la estabilidad
La cuestión aquí no es si se tiene o no un esqueleto en el closet. Usted sabe que tiene un esqueleto, pero éste está en la planta de producción, contándole todos sus secretos de producción a quien quiera escucharlos. ¿Ese esqueleto está en buena forma, o indica que sus procesos podrían usar una pequeña modificación? ¿Ha llegado usted tan lejos en el anidado de partes que la chapa se consumió en la máquina, o ésta sufrió una tremenda colisión? ¿Cuánto material quedó?
A pesar del arduo trabajo en la lectura de todas las claves disponibles, hay veces en que nuestros mejores planes en teoría simplemente no funcionan cuando se llevan a la práctica. Por ejemplo, puede lograr una utilización de material increíblemente alta generando diligentemente los mejores nidos posibles, y sin embargo toda su operación empieza a fallar cuando corta realmente esos nidos.
Para que los nidos funcionen en la práctica, el software de anidado tiene que ser compatible con la máquina, pues el nido sólo puede ser cortado para la mejor de las capacidades de la máquina. La manera más rápida de apilar un esqueleto bajo la punzonadora, o posiblemente botar la cabeza láser, es generar una mala trayectoria de corte.
Para generar nidos exitosos, consulte a su esqueleto y mantenga en mente estos consejos:
- Aleje las partes pequeñas del borde de sujeción para mantener la integridad del esqueleto. Esto le dará a su esqueleto la estructura que necesita para brindar un marco fuerte a sus partes.
- Evite la acumulación de calor para exactitud de las partes y prevención de colisiones. En una máquina láser o plasma, cortar varios agujeros o partes pequeñas en un área concentrada puede torcer el material. En una punzonadora o láser, una parte puede soltarse de las orejas que la sujetan.
- Aumente el rendimiento del material anidando entre las sujeciones. Haga corte de línea común sin desestabilizar la chapa, y use tamaños máximos de grupos de partes para crear sub-nidos que sean cortados con línea común.
Manejo de los sobrantes
Aprovechar al máximo los sobrantes puede ser clave para aumentar las ganancias. Para asegurar resultados consistentes con el tiempo, guarde sus ajustes de sobrantes ideales en una base de datos de manufactura. Podría decidir recortar sobrantes para simplificar el manejo del material que queda. Sin embargo, la precaución aquí es que crear demasiados sobrantes únicos puede volver difícil su localización y su manejo.
Una excelente opción es usar los anchos de sobrantes ideales para que sean fáciles de colectar cuando se recuperan del almacén, y se puede limitar el número de tamaños de sobrantes con los que los operadores tienen que tratar, creando una pesadilla de almacenamiento. Si se recorta la chapa justo después de la última parte en el nido, típicamente se acaba con un tamaño único -48 por 33.625 pulgadas por ejemplo. Usando los anchos ideales, al redondear los recortes de chapa a incrementos de 6 o 10 pulgadas, se pueden crear tamaños estándar de sobrantes. Se sacrificará un poco de material pero se ganará en simplificar la logística—como en el ejemplo anterior, lo que resulta en un sobrante de 48 por 36 pulgadas.
Signos de retos de desanidado
Más allá de leer el esqueleto para la utilización de la chapa, los huesos que quedan después del anidado pueden hablarle sobre los retos del desanidado y la calidad de las partes relacionados con la separación del entramado, uso excesivo de orejas y malas ubicaciones de las orejas. Rastrear estos resultados es clave para evaluar la cantidad y la calidad de salida. Con estos resultados, se puede construir una base de datos que será útil para descubrir las mejores prácticas.
A las piezas descargadas automáticamente se les pone un código de colores en el software para ayudar a optimizar la clasificación de partes.
Desarrollar los procesos ideales de anidado para su flujo de trabajo, maquinaria y software CAM podría requerir cierto proceso de prueba y error, pero el esfuerzo reducirá el desperdicio y mejorará los procesos a largo plazo. Su base de datos debe incluir las mejores prácticas para el éxito, incluyendo tipo y espesor de material, tipo o estilo de orejas, y preferencia para la localización y el tamaño de las orejas.
Cuando funciona el acto de equilibrio
Cuando los procesos de anidado son optimizados verdaderamente, éstos deben aplicarse de manera consistente para aprovechar al máximo el material de un modo que se ajuste a las demandas de su taller. Se pueden hacer cambios al flujo global de trabajo y prepararse para una posible afluencia de una variedad de partes, pero considere el panorama completo antes de lanzar un problema potencial a los trabajos.
Para optimizar el anidado, las circunstancias ideales incluirían un sistema de ejecución de manufactura (MES), planeación de recursos de la empresa (ERP), o una plataforma similar integrada con su software CAM. Con dicha integración su software de negocio puede decirle qué partes necesita cortar y cuándo, con lo que pueden moverse fácilmente partes “justo a tiempo” corriente abajo para operaciones secundarias, sin forzar a su operador a gastar mucho tiempo manejando pilas de partes. Una configuración ideal podría incluir la automatización de la remoción y el apilado de partes, lo cual podría reducir el error y darle al operador más tiempo para otras tareas.
Todo aquello que sea fácil de leer y entender a un vistazo es un beneficio en la planta de producción. La identificación estratégica de partes, como por ejemplo reportes de nido con código de colores, puede simplificar y hacer que la clasificación sea a prueba y error. Y agregar la identificación de partes durante el proceso de anidado, como por ejemplo grabar números de parte o imprimir etiquetas que puedan aplicarse de manera manual o automática, identifica las partes incluso antes de que salgan del nido.
Aun cuando no todos los talleres tengan los recursos necesarios para lograr inmediatamente la configuración ideal, en especial sin perturbar procesos que generalmente funcionan bien, se pueden hacer cambios graduales con el tiempo. Después de todo, la meta no necesariamente es ser el taller perfecto, sino ser el taller que es perfecto para las condiciones bajo las cuales usted ya trabaja.
Doug Wood es gerente general, Radan Americas, Hexagon Manufacturing Intelligence Production Software, 25 N. Lake St., Suite 220, Forest Lake, MN 55025, 800-875-7232, www.radan.com.
About the Author
About the Publication
Compañías Relacionadas
subscribe now
FMA Communications ha introducido al mercado la edición en Español de la revista The Fabricator. Esta versión consiste del mismo tipo de artículos técnicos y sección de lanzamientos de nuevos productos que actualmente presentan el personal de primera categoría de Fabricator en Inglés.
start your free subscription- Podcasting
- Podcast:
- The Fabricator Podcast
- Published:
- 05/14/2024
- Running Time:
- 62:12
Cameron Adams of Laser Precision, a contract metal fabricator in the Chicago area, joins the podcast to talk...
- Trending Articles
Anidado para la estabilidad del corte láser
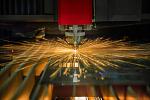
Seguridad en la soldadura desde el inicio
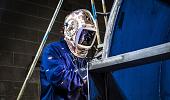
El software guía a los soldadores a través de instrucciones de trabajo
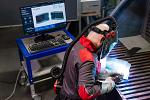
La rueda reduce las fuerzas de empuje/tracción hasta en un 50%

Gafas protectoras diseñadas para trabajadores que necesitan lentes correctivos
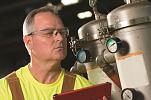
- Industry Events
Laser Welding Certificate Course
- May 7 - August 6, 2024
- Farmington Hills, IL
World-Class Roll Forming Workshop
- June 5 - 6, 2024
- Louisville, KY
Advanced Laser Application Workshop
- June 25 - 27, 2024
- Novi, MI
Precision Press Brake Certificate Course
- July 31 - August 1, 2024
- Elgin,