Industrial Systems and Manufacturing Instructor
- FMA
- The Fabricator
- FABTECH
- Canadian Metalworking
Categories
- Additive Manufacturing
- Aluminum Welding
- Arc Welding
- Assembly and Joining
- Automation and Robotics
- Bending and Forming
- Consumables
- Cutting and Weld Prep
- Electric Vehicles
- En Español
- Finishing
- Hydroforming
- Laser Cutting
- Laser Welding
- Machining
- Manufacturing Software
- Materials Handling
- Metals/Materials
- Oxyfuel Cutting
- Plasma Cutting
- Power Tools
- Punching and Other Holemaking
- Roll Forming
- Safety
- Sawing
- Shearing
- Shop Management
- Testing and Measuring
- Tube and Pipe Fabrication
- Tube and Pipe Production
- Waterjet Cutting
Industry Directory
Webcasts
Podcasts
FAB 40
Advertise
Subscribe
Account Login
Search
Aluminum Etc.: Why hot cracking in aluminum welds is common
- By Gina Cutts
- Updated August 7, 2023
- October 6, 2021
- Article
- Aluminum Welding
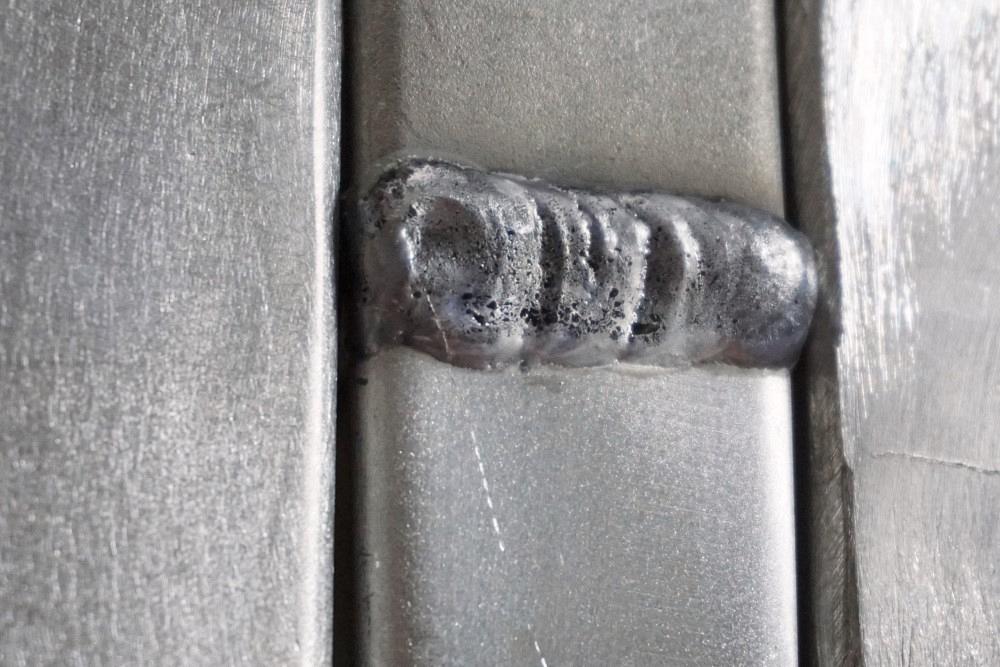
Hot cracking is an incredibly common form of weld defect found in aluminum welds. Aluminum Etc. columnist Gina Cutts explains why that is and shares a few tricks to help welders prevent it from happening. Getty Images
Almost all of the defects you may experience when welding aluminum are in the form of weld cracks. Why? Because we are not welding pure aluminum.
Pure aluminum is way too soft for commercial use, which is why it is alloyed with other elements like copper, silicon, magnesium, and magnesium silicide to make it workable. These different elements have different melting points—all but magnesium have a higher melting point than aluminum. (Aluminum melts at about 1,221 degrees F, which is pretty low!)
Hot cracking happens after the metal, which has been heated to liquid form, solidifies. For those interested, you can find a helpful chart online that breaks down weld sensitivity ranges. Basically, every aluminum alloy has a solidification cracking curve. For each possible alloying element added to aluminum, the chart shows what the probability of cracking is based on the percentage of that added alloy. This is referred to as the peak.
Silicon, magnesium, and magnesium silicide crack sensitivity peaks at around 1%. When copper is the alloying element, sensitivity peaks at about 3%.
Armed with this knowledge, you can start to develop a strategy for welding aluminum that will help you avoid cracking as much as possible.
Tips for Preventing Hot Cracking in Aluminum
First, look at the composition of your base metal. If the percentages of the alloying elements are lower than peak sensitivity, you should be OK. Just be sure to use a filler wire with a composition that doesn’t shift the overall mix toward the peak.
If, however, you weld parts with a composition that puts them close to peak sensitivity, you can use filler wire to your advantage. A wire with a composition that is very different from the parts you’re welding can shift the alloy percentages in the weld pool away from the peak.
Joint design can also be a factor in causing or minimizing hot cracking. For example, butt welding two square-edge pieces together won’t give you much area for adding filler. In this situation, you have little room for diluting the alloy percentages. However, giving the edges a generous bevel will enable you to add more filler. That filler will change the percentages of alloying elements in the weld pool, lowering peak sensitivity. This will help you to avoid hot cracking.
About the Author
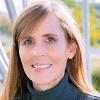
About the Publication
subscribe now
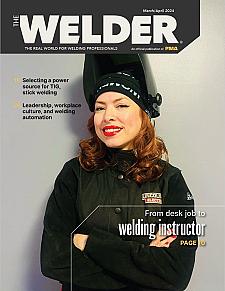
The Welder, formerly known as Practical Welding Today, is a showcase of the real people who make the products we use and work with every day. This magazine has served the welding community in North America well for more than 20 years.
start your free subscription- Stay connected from anywhere
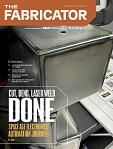
Easily access valuable industry resources now with full access to the digital edition of The Fabricator.
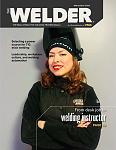
Easily access valuable industry resources now with full access to the digital edition of The Welder.
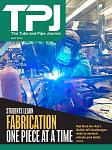
Easily access valuable industry resources now with full access to the digital edition of The Tube and Pipe Journal.
- Podcasting
- Podcast:
- The Fabricator Podcast
- Published:
- 04/16/2024
- Running Time:
- 63:29
In this episode of The Fabricator Podcast, Caleb Chamberlain, co-founder and CEO of OSH Cut, discusses his company’s...
- Industry Events
16th Annual Safety Conference
- April 30 - May 1, 2024
- Elgin,
Pipe and Tube Conference
- May 21 - 22, 2024
- Omaha, NE
World-Class Roll Forming Workshop
- June 5 - 6, 2024
- Louisville, KY
Advanced Laser Application Workshop
- June 25 - 27, 2024
- Novi, MI