Product Manager, Saws and Hand Tools
- FMA
- The Fabricator
- FABTECH
- Canadian Metalworking
Categories
- Additive Manufacturing
- Aluminum Welding
- Arc Welding
- Assembly and Joining
- Automation and Robotics
- Bending and Forming
- Consumables
- Cutting and Weld Prep
- Electric Vehicles
- En Español
- Finishing
- Hydroforming
- Laser Cutting
- Laser Welding
- Machining
- Manufacturing Software
- Materials Handling
- Metals/Materials
- Oxyfuel Cutting
- Plasma Cutting
- Power Tools
- Punching and Other Holemaking
- Roll Forming
- Safety
- Sawing
- Shearing
- Shop Management
- Testing and Measuring
- Tube and Pipe Fabrication
- Tube and Pipe Production
- Waterjet Cutting
Industry Directory
Webcasts
Podcasts
FAB 40
Advertise
Subscribe
Account Login
Search
Using a reciprocating saw for cutting pipe and tube
Safety, versatility, ease of use make reciprocating process a good alternative to conventional cutoff
- By Jordan Schimel
- Updated January 23, 2023
- June 8, 2021
- Article
- Cutting and Weld Prep
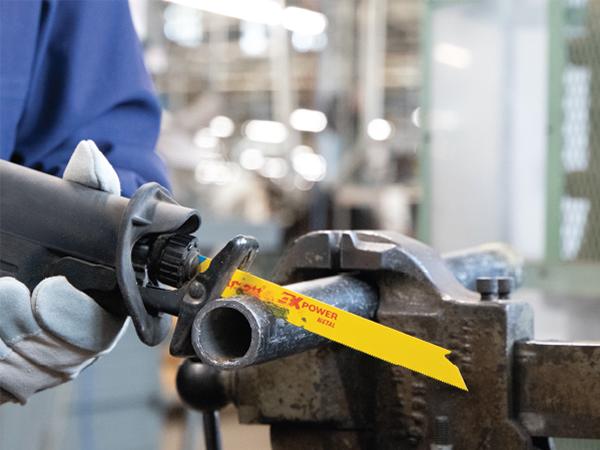
A grinder with a cutoff wheel is the go-to tool for many tube and pipe shops, but this isn’t the only choice. A reciprocating saw offers advantages in safety and cutting speed, and when outfitted with a premium blade, it can offer substantial cost savings. Images: Starrett
Grinders have more than a niche in metal fabrication, favored for use in both finishing operations and cutoff. The tools and cutoff blades are reliable, and they make quick work of all sorts of metals.
While they do an excellent job of cutoff, they do have some inherent risks. The cutoff blades rotate at high speeds (often exceeding 10,000 RPM), and the sparks and dust they generate travel quite a distance. That said, for fabricators who use rotary cutoff regularly and manage the hazards successfully, this process is productive and capable—no question about that.
However, rotary cutting with a grinder isn’t the only option for fast, convenient cutoff. A reciprocating saw can provide a quick and clean cutting method that handles a variety of thicknesses and tube or pipe diameters and contributes to workplace safety. Because the reciprocating action is fundamentally different from the rotary action, and the saw design likewise is different, a reciprocating tool provides a completely different cutting experience from that of a rotary tool.
Safety When Cutting Metal With a Reciprocating Saw
The reciprocating action is a milling process that makes chips. Although the saw can cut quickly, the blade’s action and speed don’t impart a lot of energy into the chips it makes. It doesn’t generate a lot of thermal energy; the temperature stays low in both the substrate and the cutting tool. Likewise, the process doesn’t transfer much kinetic energy to the chips. Cleanup is easy because the swarf falls out of the tooth gullets and is deposited onto the floor in a localized area.
A rotary tool with a 4-1/2-in. cutoff wheel rotating at 13,500 RPM generates a motion that equates to 16,000 surface feet per minute. It hurls sparks up to 30 ft. At 1,800 degrees, these metal shards have the potential to cause injury if any red-hot metal were to hit an unprotected worker. They also have the potential to cause extensive property damage if they land near anything flammable or explosive. Using one takes great care and often requires a hot work permit.
Rotary cutting also generates no small amount of dust, both abrasive dust from the cutting wheel and metal dust from the workpiece, so workers in the area need personal protective equipment to prevent inhaling airborne particulates.
Ergonomics is another factor. Reciprocating blades tend to cut faster than abrasive tools, so less time cutting means less time subjected to vibrations from the process. Also, reciprocating blades generate less noise, operating about 15 dB quieter than rotary blades. Finally, because reciprocating blades are made from metal, they can flex. Cutoff wheels are brittle and can shatter, sending debris throughout the workplace.
Versatility in Using a Reciprocating Saw to Cut Metal
Because the blade of a reciprocating saw extends straight out from the end of the tool, and because the tool doesn’t have guarding, the blade can get into tight spaces. Noteworthy too is that reciprocating blades come in a few standard lengths, so cutting a variety of pipe diameters doesn’t mean using a variety of blade lengths. For the most part, one size fits all.
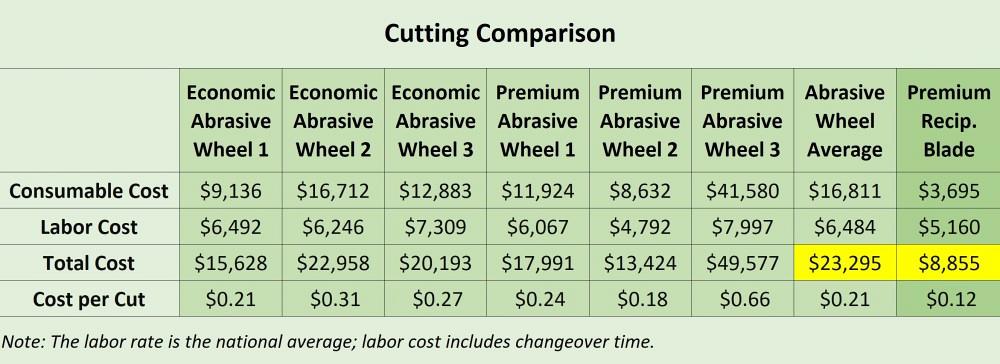
The average cost to make 74,750 cuts on 1-½ Sch. 40 steel pipe with rotary cutoff is $23,295. For a reciprocating tool with a premium blade, the annual cost is $8,855, a savings of $14,440.
When using a using a grinder with a cutoff wheel, it might be tempting to remove the guard to get into a tight spot. Bad idea. When a wheel breaks, the result is catastrophic, and it’s even worse if the guard isn’t in place to capture some of the debris. All the energy that was supposed to go into the cutting process sends pieces of broken wheel in every direction, putting the operator and others in the area at risk.
Efficiencies and Economic Considerations When Cutting Tube and Pipe
In terms of wear, reciprocating blades hold a constant size and therefore cut at a constant rate. Because the number of surface feet per minute doesn’t change, the cutting efficiency doesn’t change much from the first cut to the last cut. An abrasive cutoff wheel doesn’t cut at a constant rate. As the cutting wheel wears, its diameter (and circumference) shrink, but the speed remains the same. As the wheel shrinks, the number of surface feet per minute shrinks, increasing the time needed for each cut.
Blade selection is critical. A longer-lasting blade might cost more, but depending on the blade’s construction and tooth design, it might more than pay for itself in durability and less frequent work stoppages to replace the blade.
A cutting test comparing a premium 6-in. reciprocating blade with a variety of 4.5-in. abrasive cutoff wheels yielded an average annual savings advantage of more than $14,000 (see Figure 1).
The test was based on an annual workload of 74,750 cuts in Schedule 40 steel pipe, typical for three operators in a small to midsized shop earning the national average labor rate. The consumption is one box of abrasives (25 wheels per box) per worker per week versus six reciprocating blades per operator per week, or 75 rotary wheels versus 18 blades per week.
Selecting the Right Reciprocating Saw to Cut Metal
Manufacturers typically offer two shapes, one with parallel edges and one with a tapered profile (see Figure 2 and Figure 3). The style with parallel edges is for harder cuts, especially when the tip needs to be forced. The tapered profile is for straighter cuts and is better for hard-to-reach places.
The number of teeth per inch (TPI) usually determines the type of material the blade can cut. For example, as the metal thickness decreases, the TPI should increase. As the TPI increases, so does the cutting time; the advantage is that more TPI results in a cleaner cut.
Some reciprocating blades are marked to identify the application, but after just a few minutes of use, the marking has worn off, making it difficult to tell one blade from another. Some manufacturers offer color coding on the shank so it won’t wear off. This provides a fast, easy way to determine a blade’s application even after several uses.
About the Author
About the Publication
Related Companies
subscribe now
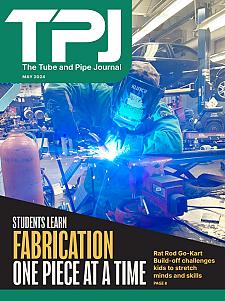
The Tube and Pipe Journal became the first magazine dedicated to serving the metal tube and pipe industry in 1990. Today, it remains the only North American publication devoted to this industry, and it has become the most trusted source of information for tube and pipe professionals.
start your free subscription- Stay connected from anywhere
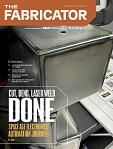
Easily access valuable industry resources now with full access to the digital edition of The Fabricator.
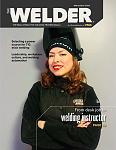
Easily access valuable industry resources now with full access to the digital edition of The Welder.
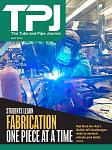
Easily access valuable industry resources now with full access to the digital edition of The Tube and Pipe Journal.
- Podcasting
- Podcast:
- The Fabricator Podcast
- Published:
- 04/16/2024
- Running Time:
- 63:29
In this episode of The Fabricator Podcast, Caleb Chamberlain, co-founder and CEO of OSH Cut, discusses his company’s...
- Trending Articles
Zekelman Industries to invest $120 million in Arkansas expansion
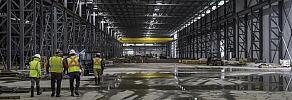
3D laser tube cutting system available in 3, 4, or 5 kW
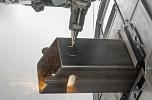
Corrosion-inhibiting coating can be peeled off after use
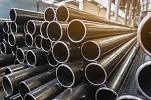
Brushless copper tubing cutter adjusts to ODs up to 2-1/8 in.
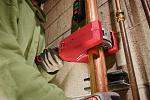
HGG Profiling Equipment names area sales manager
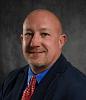
- Industry Events
16th Annual Safety Conference
- April 30 - May 1, 2024
- Elgin,
Pipe and Tube Conference
- May 21 - 22, 2024
- Omaha, NE
World-Class Roll Forming Workshop
- June 5 - 6, 2024
- Louisville, KY
Advanced Laser Application Workshop
- June 25 - 27, 2024
- Novi, MI