- FMA
- The Fabricator
- FABTECH
- Canadian Metalworking
Our Publications
Categories
- Additive Manufacturing
- Aluminum Welding
- Arc Welding
- Assembly and Joining
- Automation and Robotics
- Bending and Forming
- Consumables
- Cutting and Weld Prep
- Electric Vehicles
- En Español
- Finishing
- Hydroforming
- Laser Cutting
- Laser Welding
- Machining
- Manufacturing Software
- Materials Handling
- Metals/Materials
- Oxyfuel Cutting
- Plasma Cutting
- Power Tools
- Punching and Other Holemaking
- Roll Forming
- Safety
- Sawing
- Shearing
- Shop Management
- Testing and Measuring
- Tube and Pipe Fabrication
- Tube and Pipe Production
- Waterjet Cutting
Industry Directory
Webcasts
Podcasts
FAB 40
Advertise
Subscribe
Account Login
Search
Hydroforming
Hydroforming - Hydroforming isn't as mysterious as it seems. This technology area is full of articles, including case studies, on hydroforming sheet metal and tubular sections.
-
- From The Fabricator
Jones Metal Products celebrates 100 years in business
- Feb 9, 2023
- News Release
Established in 1923 on the site of a former metal stamping and porcelain enameling company, Jones Metal Products is marking 100 years in business in West Lafayette, Ohio.
-
- From The Fabricator
Alternative hydroforming tech dispenses with bladder, achieves 60,000 PSI
- By Eric Lundin
- Aug 30, 2021
- Article
A technology related to hydroforming, named fluidforming, dispenses with bladders and diaphragms, achieving much greater pressures and more comprehensive metal forming capabilities.
-
- From The Fabricator
Quintus Flexform press eliminates need for matched male/female die sets
- Oct 26, 2019
- Product Release
The Quintus Flexform fluid cell press uses hydroforming technology, employing extremely high hydraulic pressure against a flexible rubber diaphragm to shape sheet material against a single tool half. The process enables the forming of a variety of geometric shapes out of sheet metal alloys from...
-
- From The Fabricator
Jones Metal changes ownership, chairman to retire
- Aug 23, 2019
- News Release
Jones Metal Products of West Lafayette, Ohio, has announced that chairman of the board and owner Marion Sutton will retire and has sold the metal forming company to President and CEO Dan Erb. Sutton is the third generation of her family to own Jones Metal, started in 1923 by her grandfather, Frank...
-
- From The Fabricator
Bilsing Automation relocates North American facility
- Jul 19, 2019
- News Release
Bilsing Automation North America, a supplier of automated tooling systems for stamping, fabrication, hydroforming, injection molding, and packaging, has moved to a new facility in Roseville, Mich., just down the street from its previous location. The new facility offers 15 percent more...
-
- From The Fabricator
Precision Aerospace completes recapitalization transaction
- Apr 24, 2019
- News Release
Phoenix-based Precision Aerospace LLC, a provider of complex metal assemblies for aerospace and industrial applications, has completed a recapitalization transaction led by investment firms Willcrest Partners and Curran Companies. Precision Aerospace produces prototypes and production-run metal...
-
- From The Fabricator
Gestamp opens new plant in Mexico
- Mar 20, 2019
- News Release
Gestamp, a multinational manufacturer of highly engineered metal components for the automotive industry, has inaugurated its new plant in San Luis Potosí, Mexico. The $86 million facility is the first Gestamp plant in Mexico for manufacturing chassis parts. Employing more than 300 people, it is...
Triform to manufacture fluid cell sheet hydroforming press for H&R Parts
- Apr 12, 2018
- News Release
Beckwood Press Co., a St. Louis-based manufacturer of custom hydraulic presses and automation systems, has been awarded a contract by H&R Parts Co. to manufacture a Triform model 24-5BD fluid cell sheet hydroforming press. With a 24-in.-dia. forming area and 5,000 PSI, the press will support...
Triumph achieves Elite Supplier status from Lockheed Martin RMS
- Mar 20, 2018
- News Release
Triumph Group Inc., Berwyn, Pa., has announced that its Triumph Fabrications company located in Hot Springs, Ark., has achieved Lockheed Martin Rotary and Mission Systems (RMS) Elite Supplier status for exceptional supplier performance in support of its Sikorsky Aircraft business. Triumph...
Sheet metal forming, hydroforming conferences to be held in Germany May 15-16
- Feb 2, 2018
- News Release
Forschungsgesellschaft Umformtechnik mbH and the Institut für Umformtechnik (IFU) have announced the upcoming international conferences New Developments in Sheet Metal Forming (NEBU) 2018 and New Developments in Hydroforming (NEHY) 2018, to be held May 15-16 in Fellbach, Germany. The conferences...
Hydroforming continues to pick up market share, enhance vehicle safety
- By Eric Lundin
- Jan 24, 2018
- Article
Redesigned for the 2016 model year, Nissan’s Titan won accolades from Cars.com and U.S. News & World Report. Tier-1 component supplier and designer Vari-Form developed an assembly that reduced part count, reduced vehicle weight, and helped it meet a new crash standard.
-
- From The Fabricator
Technology Spotlight: A new take on forming with fluids
If you know anything about hydroforming, you know that a bladder is necessary. Well, that bladder can prove troublesome in some metal forming applications. A new metal forming technology that uses water but does not require a bladder gives manufacturers something to think about as they seek to form intricate metal parts.
Beckwood supplies Triform equipment to international aerospace supplier
- Feb 14, 2017
- News Release
Beckwood, St. Louis, has supplied a Triform tray-style fluid cell sheet hydroforming press and an extrusion stretch-forming machine to an India-based aerospace supplier for fulfillment of several newly awarded contracts. With a 24- by 96-in. forming area and a dual shuttle system, the model...
Vari-Form provides rear suspension trailing arms to Volkswagen
- Feb 2, 2017
- News Release
Livonia, Mich.-based Vari-Form has announced that it is producing right and left trailing arms for the rear suspension system of the Volkswagen Golf A7 using pressure-sequence hydroforming technology. The trailing arms, hydroformed from closed-section tube, maintain inherent strength while...
Vari-Form load beam assembly meets requirements for 2017 Chrysler Pacifica
- Nov 3, 2016
- News Release
Livonia, Mich.-based Vari-Form has designed and manufactured the front-end load beam assembly for the 2017 Chrysler Pacifica®, a minivan re-engineered from the ground up and built on a new platform. “Very tight packaging was one of the challenges we faced on this technically advanced van,”...
subscribe now
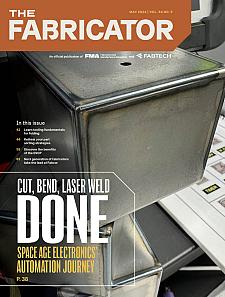
The Fabricator is North America's leading magazine for the metal forming and fabricating industry. The magazine delivers the news, technical articles, and case histories that enable fabricators to do their jobs more efficiently. The Fabricator has served the industry since 1970.
start your free subscription- Podcasting
- Podcast:
- The Fabricator Podcast
- Published:
- 04/16/2024
- Running Time:
- 63:29
In this episode of The Fabricator Podcast, Caleb Chamberlain, co-founder and CEO of OSH Cut, discusses his company’s...
- Trending Articles
Capturing, recording equipment inspection data for FMEA
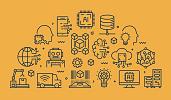
Tips for creating sheet metal tubes with perforations
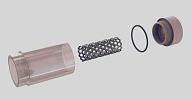
Are two heads better than one in fiber laser cutting?
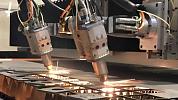
Supporting the metal fabricating industry through FMA
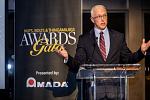
Zekelman Industries to invest $120 million in Arkansas expansion
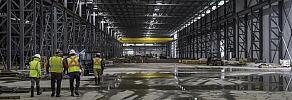
- Industry Events
16th Annual Safety Conference
- April 30 - May 1, 2024
- Elgin,
Pipe and Tube Conference
- May 21 - 22, 2024
- Omaha, NE
World-Class Roll Forming Workshop
- June 5 - 6, 2024
- Louisville, KY
Advanced Laser Application Workshop
- June 25 - 27, 2024
- Novi, MI
- Upcoming Webcasts
Navigating Change: The Manufacturer’s Guide to Change Management with ERP Implementation
- May 16, 2024
- Sponsored
- Presented By: ECI Software Solutions, M1