- FMA
- The Fabricator
- FABTECH
- Canadian Metalworking
Our Publications
Categories
- Additive Manufacturing
- Aluminum Welding
- Arc Welding
- Assembly and Joining
- Automation and Robotics
- Bending and Forming
- Consumables
- Cutting and Weld Prep
- Electric Vehicles
- En Español
- Finishing
- Hydroforming
- Laser Cutting
- Laser Welding
- Machining
- Manufacturing Software
- Materials Handling
- Metals/Materials
- Oxyfuel Cutting
- Plasma Cutting
- Power Tools
- Punching and Other Holemaking
- Roll Forming
- Safety
- Sawing
- Shearing
- Shop Management
- Testing and Measuring
- Tube and Pipe Fabrication
- Tube and Pipe Production
- Waterjet Cutting
Industry Directory
Webcasts
Podcasts
FAB 40
Advertise
Subscribe
Account Login
Search
Bending and Forming - Page 25
-
- From The Fabricator
AP&T receives order from Mercedes-Benz for partial press hardening system
- Apr 6, 2022
- News Release
AP&T in Germany has received an order for its TemperBox partial press hardening system from Mercedes-Benz in Sindelfingen, Germany. The order also includes AP&T’s multilayer furnace, automation equipment, control system, and integration.
-
- From The Fabricator
Ask the Stamping Expert: Are we taking the best approach to meeting statistical capability on a die set?
- By Thomas Vacca
- Apr 5, 2022
- Article
Ask the Stamping Expert columnist Tom Vacca discusses the practicalities of meeting statistical capability on a die set.
-
- From The Fabricator
SAF adds machine for bending complex metal profiles
- Apr 4, 2022
- News Release
Atlanta-based SAF, a global metals distributor, fabricator, and finisher, has invested in a new double bending machine to augment its fabrication capabilities.
-
- From The Fabricator
New bending technology helps custom fabricator increase throughput on low-volume press brake jobs
- Apr 4, 2022
- News Release
With American precision style tooling and the Maglock magnetic safety system from Mate Precision Technologies, Bilan Metalworks increased throughput on its low-volume press brake jobs.
-
- From The Fabricator
Improved semiconductor supply drives market share gains for GM
- Apr 1, 2022
- News Release
General Motors has announced higher production and market share in key truck segments in Q1 2022, giving partial credit for the increases to improved semiconductor supplies.
-
- From The Fabricator
Staff additions announced at AIDA-America
- Mar 31, 2022
- News Release
AIDA-America, metal stamping press manufacturer in Dayton, Ohio, has hired Dawn Reed as accounts payable/payroll specialist and Krista Matsumoto as sales administrator.
-
- From The Fabricator
Talkin' Shop with Metal Shop Masters: Episode 4, Seven Bailey
- By The Fabricator editors
- Mar 30, 2022
- Blog Post
In episode No. 4 of Talkin' Shop with Metal Shop Masters, we speak with Minneapolis-based Seven Bailey about their 20-plus-year career as a metal fabricator, AWS certified welder, welding inspector, educator, and artist.
-
- From The Fabricator
Auto/Steel Partnership to offer AHSS formability training course
- Mar 25, 2022
- News Release
Auto/Steel Partnership will present an online training course for stamping suppliers, “AHSS Formability 101,” on April 14, 2022, from 9:00 a.m.-12:00 p.m.
-
- From The Fabricator
Coe Press Equipment expands service network
- Mar 25, 2022
- News Release
Coe Press Equipment, Sterling Heights, Mich., a provider of coil processing equipment to the metal stamping and fabrication industries, has announced the expansion of its service offerings with the establishment of two new regional service hubs.
-
- From The Fabricator
Toyota to invest $27 million to expand TABC’s manufacturing capabilities
- Mar 24, 2022
- News Release
Toyota Motor North America (TMNA) has announced it will make a $27 million investment in its Toyota Auto Body Co. (TABC) operation in Long Beach, Calif., to support an increase in production capabilities.
-
- From The Fabricator
Grain direction’s effect on sheet metal bending
- By Steve Benson
- Mar 24, 2022
- Article
If press brake operators bend a small radius with the material grain—that is, the bend line runs parallel to the material grain direction, they should watch out for cracking.
-
- From The Fabricator
BMW to create 200 jobs with $200 million investment in South Carolina
- Mar 18, 2022
- News Release
BMW has announced it is expanding its Plant Spartanburg campus in South Carolina with the construction of a new press shop. The $200 million investment will create 200 new jobs.
-
- From The Fabricator
GM names 2021 Supplier Award winners
- Mar 18, 2022
- News Release
General Motors has recognized 134 suppliers from 16 countries with its Supplier of the Year Award.
-
- From The Fabricator
Snell Mfg. appoints president/CEO
- Mar 17, 2022
- News Release
Snell Mfg., a Nashville-based family of industrial companies, has hired Charles “Chuck” Banker as president/CEO to lead the company’s three holdings in its next phase of development.
-
- From The Fabricator
Okay Industries names engineering manager
- Mar 15, 2022
- News Release
New Britain, Conn.-based Okay Industries Inc., a contract manufacturer of components and subassemblies for global medical device OEMs, has promoted Mario Chaves Jr. to engineering manager.
subscribe now
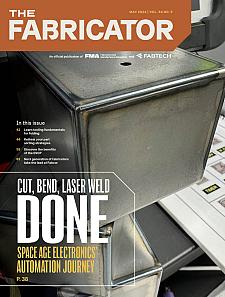
The Fabricator is North America's leading magazine for the metal forming and fabricating industry. The magazine delivers the news, technical articles, and case histories that enable fabricators to do their jobs more efficiently. The Fabricator has served the industry since 1970.
start your free subscription- Podcasting
- Podcast:
- The Fabricator Podcast
- Published:
- 05/07/2024
- Running Time:
- 67:38
Patrick Brunken, VP of Addison Machine Engineering, joins The Fabricator Podcast to talk about the tube and pipe...
- Trending Articles
How laser and TIG welding coexist in the modern job shop
Young fabricators ready to step forward at family shop
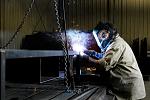
Material handling automation moves forward at MODEX
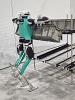
Connecticut students compete in Maritime Welding Competition
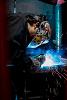
A deep dive into a bleeding-edge automation strategy in metal fabrication
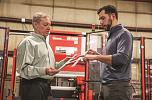
- Industry Events
World-Class Roll Forming Workshop
- June 5 - 6, 2024
- Louisville, KY
Advanced Laser Application Workshop
- June 25 - 27, 2024
- Novi, MI
Precision Press Brake Certificate Course
- July 31 - August 1, 2024
- Elgin,
- Upcoming Webcasts
Navigating Change: The Manufacturer’s Guide to Change Management with ERP Implementation
- May 16, 2024
- Sponsored
- Presented By: ECI Software Solutions, M1
Managing Dangerous Dusts from Metalworking
- June 26, 2024
- Sponsored
- Presented By: Camfil Air Pollution Control