- FMA
- The Fabricator
- FABTECH
- Canadian Metalworking
Our Publications
Categories
- Additive Manufacturing
- Aluminum Welding
- Arc Welding
- Assembly and Joining
- Automation and Robotics
- Bending and Forming
- Consumables
- Cutting and Weld Prep
- Electric Vehicles
- En Español
- Finishing
- Hydroforming
- Laser Cutting
- Laser Welding
- Machining
- Manufacturing Software
- Materials Handling
- Metals/Materials
- Oxyfuel Cutting
- Plasma Cutting
- Power Tools
- Punching and Other Holemaking
- Roll Forming
- Safety
- Sawing
- Shearing
- Shop Management
- Testing and Measuring
- Tube and Pipe Fabrication
- Tube and Pipe Production
- Waterjet Cutting
Industry Directory
Webcasts
Podcasts
FAB 40
Advertise
Subscribe
Account Login
Search
Laser Cutting - Page 45
-
- From The Fabricator
Technology Spotlight: “Democratized” fiber laser lowers ownership entry point
- By Kate Bachman
- Jul 17, 2017
- Article
Fabricators that want to dip theirs toes in the laser cutting machine pool without investing $1 million or so to do so may find what they seek in a new, low-entry-price point fiber laser machine launched at FABTECH with a 40-inch by 74-in. footprint that cuts both sheet metal and tube, cuts on shop air, doesn't need a chiller, and plugs into your 110-watt wall outlet.
-
- From The Welder
ICALEO 2017 opens registration
- Jul 14, 2017
- News Release
The International Congress on Applications of Lasers & Electro-Optics (ICALEO®) will be held Oct. 22–26, 2017, in Atlanta. The event will present the latest developments and technologies in laser materials processing, laser microprocessing, and nanomanufacturing. To register, visit...
-
- From The Fabricator
8-kW fiber laser uses new drive system for greater speed, accuracy
- Jul 14, 2017
- Product Release
Mazak Optonics Corp. has expanded its laser line by introducing the Optiplex Fiber III 3015 8-kW laser cutting system. The machine uses a new PreviewG control and digital drive package. The new drive system provides higher productivity through high speed and high accuracy, says the company. The...
-
- From The Fabricator
Nozzles for 2-D laser cutting machines reduce cutting gas usage 70 percent
- Jul 12, 2017
- Product Release
TRUMPF has introduced the Highspeed and Highspeed Eco nozzles, which the company says boost the feed rate by up to 100 percent for solid-state laser machines that employ fusion cutting with nitrogen. With this technology, the piercing process is faster, and laser power does not need to be...
-
- From The Fabricator
2-D laser cutting system fits in shops with limited floor space
- Jul 10, 2017
- Product Release
Mazak has designed the new Super Turbo-X 1212 2-D laser using a hybrid platform and a 4- by 4-ft. table. The fully enclosed cutting area meets FDA Class 1 safety standards. The machine incorporates a servo focus torch that helps reduce piercing time and increase productivity, according to the...
-
- From The Welder
10-kW fiber laser enables high throughput in materials processing
- Jul 4, 2017
- Product Release
Coherent has introduced the 10-kW HighLight™ FL10000 fiber laser for industrial materials processing. The system combines the output of four individual 2.5-kW laser modules into a single-output fiber. Operation is CW or pulsed, at repetition rates up to 5 kHz, for cutting, welding, and surface...
-
- From The Fabricator
Change: The new normal in manufacturing
- By Tim Heston
- Jun 26, 2017
- Blog Post
If a shop doesn't change, a competitor is bound to catch up.
-
- From The Fabricator
Kern Laser Systems expands Minnesota facility
- Jun 9, 2017
- News Release
Kern Laser Systems is adding 20,800 sq. ft. to its facility in Wadena, Minn., more than doubling its current manufacturing and R&D departments. The company plans to move into the new area by fall 2017. This expansion is the first phase of a two-phase project. The second phase, expected to begin in...
-
- From The Fabricator
Technology Spotlight: New laser cutting technology means newfound productivity
A suite of hardware, software, and control capabilities from Prima Power Laserdyne are designed to improve productivity and quality in laser processing, which should prove to be attractive to those in the automotive industry looking for productive and cost-effective fabricating equipment.
-
- From The Welder
Oscillating laser beam helps boost cutting accuracy
- May 26, 2017
- Product Release
Scanlab GmbH has developed the Weldyna scan head for cutting and welding with a high-frequency oscillating laser beam. The oscillating beam cuts through thick metal sheets and fiber-reinforced plastics. With its high wobble motion frequencies of several kilohertz and the availability of freely...
-
- From The Fabricator
LVD Strippit Mexico appoints sales engineers
- May 22, 2017
- News Release
LVD Strippit, Akron, N.Y., has announced the appointments of Belisario Antillón and Sandra Torres as sales engineers at its new office in Querétaro, Mexico. The facility offers sales and technical support for the company’s laser cutting, punching, bending, and software products. Antillón is...
-
- From The Fabricator
LAI Intl. accredited to Nadcap’s Additive Manufacturing checklist
- May 11, 2017
- News Release
LAI Intl., a contract manufacturer of precision-engineered finished parts, components, and subassemblies, has earned the first Nadcap Welding Additive Manufacturing Certification. The checklist, developed by the Nadcap Welding Task Group and used to get the Nadcap Accreditation, is based on...
-
- From The Welder
Amada Miyachi America receives ISO 9001 certification
- May 10, 2017
- News Release
Amada Miyachi America Inc., Monrovia, Calif., a manufacturer of resistance welding, laser welding, marking, cutting, and micromachining equipment and systems, has completed the ISO 9001 recertification process for its quality management system. As part of the recertification process, the company...
-
- From The Fabricator
Guide covers laser cutting machines, materials
- May 3, 2017
- Product Release
Laser Institute of America (LIA) has released the “LIA Guide to High Power Laser Cutting” for students, engineers, and scientists. Written by a team of specialists led by industry experts Dr. John Powell and Dr. Dirk Petring, this 136-page guide touches on all features of CO2 and fiber laser...
-
- From The Fabricator
Laser Mechanisms redesigns website
- Apr 26, 2017
- News Release
Laser Mechanisms Inc., Novi, Mich., has launched a newly redesigned website at www.lasermech.com. The new website offers a cleaner design, improved navigation, and a 360-degree viewer that allows the user to manipulate select products on screen in a virtual...
subscribe now
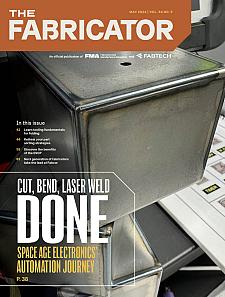
The Fabricator is North America's leading magazine for the metal forming and fabricating industry. The magazine delivers the news, technical articles, and case histories that enable fabricators to do their jobs more efficiently. The Fabricator has served the industry since 1970.
start your free subscription- Podcasting
- Podcast:
- The Fabricator Podcast
- Published:
- 05/07/2024
- Running Time:
- 67:38
Patrick Brunken, VP of Addison Machine Engineering, joins The Fabricator Podcast to talk about the tube and pipe...
- Trending Articles
How laser and TIG welding coexist in the modern job shop
Young fabricators ready to step forward at family shop
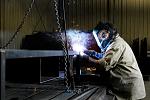
Material handling automation moves forward at MODEX
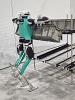
Connecticut students compete in Maritime Welding Competition
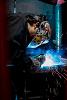
A deep dive into a bleeding-edge automation strategy in metal fabrication
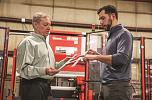
- Industry Events
World-Class Roll Forming Workshop
- June 5 - 6, 2024
- Louisville, KY
Advanced Laser Application Workshop
- June 25 - 27, 2024
- Novi, MI
Precision Press Brake Certificate Course
- July 31 - August 1, 2024
- Elgin,
- Upcoming Webcasts
Navigating Change: The Manufacturer’s Guide to Change Management with ERP Implementation
- May 16, 2024
- Sponsored
- Presented By: ECI Software Solutions, M1
Managing Dangerous Dusts from Metalworking
- June 26, 2024
- Sponsored
- Presented By: Camfil Air Pollution Control