- FMA
- The Fabricator
- FABTECH
- Canadian Metalworking
Our Publications
Categories
- Additive Manufacturing
- Aluminum Welding
- Arc Welding
- Assembly and Joining
- Automation and Robotics
- Bending and Forming
- Consumables
- Cutting and Weld Prep
- Electric Vehicles
- En Español
- Finishing
- Hydroforming
- Laser Cutting
- Laser Welding
- Machining
- Manufacturing Software
- Materials Handling
- Metals/Materials
- Oxyfuel Cutting
- Plasma Cutting
- Power Tools
- Punching and Other Holemaking
- Roll Forming
- Safety
- Sawing
- Shearing
- Shop Management
- Testing and Measuring
- Tube and Pipe Fabrication
- Tube and Pipe Production
- Waterjet Cutting
Industry Directory
Webcasts
Podcasts
FAB 40
Advertise
Subscribe
Account Login
Search
Bending and Forming - Page 83
-
- From The Fabricator
A virtuous feedback loop in precision sheet metal fabrication
- By Tim Heston
- Mar 6, 2019
- Blog Post
FMA Annual Meeting’s tour of Food Warming Equipment Inc. shows how important continual employee feedback and cross training have become.
-
- From The Fabricator
Material grain considerations on the press brake
- By Steve Benson
- Mar 6, 2019
- Article
If you’re bending cold-rolled steel and other anisotropic material, inconsistent grain direction can lead to inconsistencies at the press brake.
-
- From The Fabricator
SEYI America announces additions to California staff
- Mar 5, 2019
- News Release
SEYI America Inc., a press manufacturer based in Tullahoma, Tenn., and Irvine, Calif., has made additions to its California staff. The company has hired Brian Noonan as service engineering/sales manager. He has more than 20 years of experience in field service and sales in the metal stamping...
-
- From The Fabricator
Lutco launches new line of air cargo ball transfers
- Mar 4, 2019
- News Release
Lutco, a Worcester, Mass., manufacturer of custom bearings, stampings, and machined components, has launched a new product line of ball transfers for air cargo and other heavy-duty load applications. The ball transfers, which fit industry-standard holes of 1-3/4 in., allow for simplified manual...
-
- From The Fabricator
The road from turret punch press operator to guru
- By Tim Heston
- Mar 1, 2019
- Article
The best punch operators build a solid technical foundation in the process over years of experience. Some become the technical gurus who coach others and spur creative thinking.
-
- From The Fabricator
Industrial Innovations provides lubricant recycling systems to Trans-Matic
- Feb 28, 2019
- News Release
Grandville, Mich.-based Industrial Innovations has provided four Reclaim-PRO™ MSR lubrication reclamation and recycling systems to Trans-Matic, a supplier of metal stampings in Holland, Mich. The purification units use coalescing plate separators to separate the oil from coolant or water by using...
-
- From The Fabricator
Dallas Industries names new sales representatives
- Feb 27, 2019
- News Release
Dallas Industries, Troy, Mich., a manufacturer of coil handling and press feeding equipment and controls for the stamping industry, has announced the appointment of Taylor Made Solutions and Al Colby to it sales representative team. Taylor Made Solutions and its owner, Dennis Taylor, will represent...
-
- From The Fabricator
BCN offers press parts, repairs, and rebuilds to OEMs
- Feb 27, 2019
- Product Release
Part of the Schuler Group, BCN (Bliss, Clearing, and Niagara) Technical Services manufactures parts for face bridge mills, CNC lathes, CNC boring mills, surface grinders, rotary grinders, and turret lathes. The company also offers modernization services, including complete press teardown and...
-
- From The Fabricator
Kaast’s profile rolling machines bend angles from 1 to 12 in.
- Feb 22, 2019
- Product Release
Profile rolling machines from Kaast perform circular bending of metal profiles, angles, rings, and tubes. The machines operate horizontally or vertically to bend 1- to 12-in. angles, and all are suitable for bending square, flat, angle, and shaped profiles. Hydraulic (PBH) and mechanical (PBM)...
-
- From The Fabricator
Brankamp X7 in-process monitoring system from Marposs helps prevent stamping downtime
- Feb 15, 2019
- Product Release
Marposs has announced the availability of its Brankamp X7 in-process monitoring systems for cold and hot forming, thread rolling, and stamping operations. The system’s artificial intelligence capability enables quick machine monitoring setup and provides a way to control machine performance by...
-
- From The Fabricator
Boker’s celebrates 100th anniversary
- Feb 14, 2019
- News Release
Boker’s, a Minneapolis-based manufacturer of precision metal stampings, washers, spacers, and shims, celebrates its 100th anniversary in 2019. The company was founded in 1919 by Vitus Boker and his son John. The first products to be manufactured were an envelope folding machine and a small hand...
-
- From The Fabricator
IRMCO EXTREME iTransport system allows filling of lube containers as needed
- Feb 13, 2019
- Product Release
IRMCO has released the IRMCO EXTREME® iTransport system for lubricant delivery.
The system allows users to fill containers as needed without guessing if the drums are full or not. This helps reduce the inventory of excess drums and the disposal of empty drums.
-
- From The Fabricator
Tooling Tech Group appoints corporate sales executive
- Feb 13, 2019
- News Release
Tooling Tech Group (TTG), Macomb, Mich., a provider of custom tooling for stamping, die casting, and molding, has named Kelly Connors to the new position of corporate sales executive. Connors has 20 years of experience in sales and marketing. He most recently served as an account manager for...
-
- From The Fabricator
Non-Haz Hydraulic Fluids launches nonhazardous hydraulic fluid formulas
- Feb 12, 2019
- Product Release
Non-Haz Hydraulic Fluids LLC has introduced Non-Haz 32 and Non-Haz FRHF 46 hydraulic fluids with biodegradable, water-based, nonglycol formulas. Their antiwear components and heat transfer properties help increase lubricity with wear and extend pump life, reports the manufacturer. In addition,...
-
- From The Fabricator
What Is a Press Brake and Where Did the Name Come From?
- By Steve Benson
- Feb 8, 2019
- Article
What is a press brake and where did the name originate? Our experts detail how it comes from Middle English. Learn more about the press brake origin here.
subscribe now
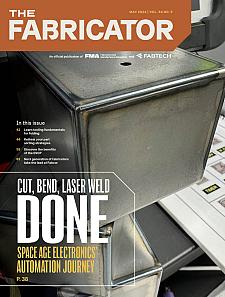
The Fabricator is North America's leading magazine for the metal forming and fabricating industry. The magazine delivers the news, technical articles, and case histories that enable fabricators to do their jobs more efficiently. The Fabricator has served the industry since 1970.
start your free subscription- Podcasting
- Podcast:
- The Fabricator Podcast
- Published:
- 04/16/2024
- Running Time:
- 63:29
In this episode of The Fabricator Podcast, Caleb Chamberlain, co-founder and CEO of OSH Cut, discusses his company’s...
- Trending Articles
Capturing, recording equipment inspection data for FMEA
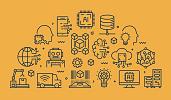
Tips for creating sheet metal tubes with perforations
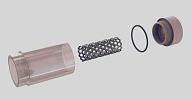
Are two heads better than one in fiber laser cutting?
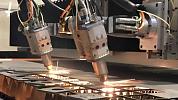
Supporting the metal fabricating industry through FMA
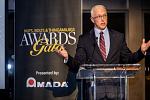
Zekelman Industries to invest $120 million in Arkansas expansion
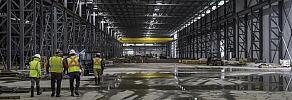
- Industry Events
16th Annual Safety Conference
- April 30 - May 1, 2024
- Elgin,
Pipe and Tube Conference
- May 21 - 22, 2024
- Omaha, NE
World-Class Roll Forming Workshop
- June 5 - 6, 2024
- Louisville, KY
Advanced Laser Application Workshop
- June 25 - 27, 2024
- Novi, MI
- Upcoming Webcasts
Navigating Change: The Manufacturer’s Guide to Change Management with ERP Implementation
- May 16, 2024
- Sponsored
- Presented By: ECI Software Solutions, M1