Editor-in-Chief
- FMA
- The Fabricator
- FABTECH
- Canadian Metalworking
Our Publications
Categories
- Additive Manufacturing
- Aluminum Welding
- Arc Welding
- Assembly and Joining
- Automation and Robotics
- Bending and Forming
- Consumables
- Cutting and Weld Prep
- Electric Vehicles
- En Español
- Finishing
- Hydroforming
- Laser Cutting
- Laser Welding
- Machining
- Manufacturing Software
- Materials Handling
- Metals/Materials
- Oxyfuel Cutting
- Plasma Cutting
- Power Tools
- Punching and Other Holemaking
- Roll Forming
- Safety
- Sawing
- Shearing
- Shop Management
- Testing and Measuring
- Tube and Pipe Fabrication
- Tube and Pipe Production
- Waterjet Cutting
Industry Directory
Webcasts
Podcasts
FAB 40
Advertise
Subscribe
Account Login
Search
Robots are on the move in manufacturing
Industrial robots, first used by a GM factory 60 years ago, are now ubiquitous throughout industry
- By Don Nelson
- April 27, 2021
Technology continuously migrates from one application to another. An example is the computer.
University of Pennsylvania researchers developed the first programmable computer in 1946. It occupied a 30- by 50-ft. space and was used to calculate military ballistic tables. Today, much, much smaller versions of the computer influence every aspect of life.
The industrial robot is another example of techno-spread. The first commercialized robot, the Unimate 1900, flexed its robotic arm at a General Motors plant in 1961.
Robotic systems find application in everything from painting to welding to 3D printing. And they’re used in industries ranging from mining to aerospace. Posted to The Additive Report website, for example, are a dozen stories about companies that use robotic systems and 3D printing technology to manufacture rockets, engines, and structures intended for off-Earth use.
Closer to home, you can find two articles in the Q2 2021 issue of AR about robots. One looks at Branch Technology, which additively manufactures building facades and other architectural structures. Its 12-ft.-high robots 3D-print one-piece structures up to 35 ft. long. The Tennessee company currently operates a fleet of 19 robots—17 for additive manufacturing and two for subtractive manufacturing. Eventually, Branch expects to operate 40 robots in its new 50,000-sq.-ft. facility.
The second article, which I wrote, looks at how medical device manufacturer Stryker uses 3D printing and robots to build knee implants and improve total knee replacement surgery. Robert Cohen, president of Stryker’s Digital, Robotics, and Enabling Technologies entity, said 42% of the primary knees the company sells to U.S. hospitals are implanted with the assistance of the company’s surgical robot. He called that percentage “unbelievable,” because Stryker introduced the robot just three years ago.
“If you look at technology transformation in marketplaces, this is one of the more rapid adoptions of a technology,” Cohen said. He expect that one day robotic surgery will be the norm for knee implantations.
During our interview, Cohen and I discussed alternative uses for Tritanium, a titanium alloy Stryker developed specifically for 3D-printing implants. The material is well-suited for making scaffolds, which promote bone/implant bonding. Limitations of space prevented inclusion of the discussion in the article, but I share it here because it relates to technology migration.
I asked Cohen if Tritanium could be used for other applications. He said yes and mentioned giant doors, like those found on aircraft carriers and the cooling towers of nuclear plants, and products that are shipped long distances. Scaffolds are used to make something light yet strong, he said, noting that a “lot of people are looking at reducing weight with scaffolds.”
Similarly, manufacturers continuously seek ways to adapt existing technologies in their effort to devise new—and better—products. Such technology migrations fuel progress.
About the Author
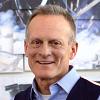
Don Nelson
2135 Point Blvd.
Elgin, IL 60123
(815)-227-8248
About the Publication
- Podcasting
- Podcast:
- The Fabricator Podcast
- Published:
- 04/16/2024
- Running Time:
- 63:29
In this episode of The Fabricator Podcast, Caleb Chamberlain, co-founder and CEO of OSH Cut, discusses his company’s...
- Trending Articles
- Industry Events
16th Annual Safety Conference
- April 30 - May 1, 2024
- Elgin,
Pipe and Tube Conference
- May 21 - 22, 2024
- Omaha, NE
World-Class Roll Forming Workshop
- June 5 - 6, 2024
- Louisville, KY
Advanced Laser Application Workshop
- June 25 - 27, 2024
- Novi, MI