President
- FMA
- The Fabricator
- FABTECH
- Canadian Metalworking
Categories
- Additive Manufacturing
- Aluminum Welding
- Arc Welding
- Assembly and Joining
- Automation and Robotics
- Bending and Forming
- Consumables
- Cutting and Weld Prep
- Electric Vehicles
- En Español
- Finishing
- Hydroforming
- Laser Cutting
- Laser Welding
- Machining
- Manufacturing Software
- Materials Handling
- Metals/Materials
- Oxyfuel Cutting
- Plasma Cutting
- Power Tools
- Punching and Other Holemaking
- Roll Forming
- Safety
- Sawing
- Shearing
- Shop Management
- Testing and Measuring
- Tube and Pipe Fabrication
- Tube and Pipe Production
- Waterjet Cutting
Industry Directory
Webcasts
Podcasts
FAB 40
Advertise
Subscribe
Account Login
Search
Aluminum Workshop: Using 4043 versus 4047 filler wire
- By Frank Armao
- December 30, 2014
- Article
- Aluminum Welding
Q: I usually use 4043 filler wire for welding 6061-T6 and castings. My friend told me I should switch to 4047 because it’s stronger. Is that true? It’s more expensive than 4043. Is it worth it?
A: As you know, 4043 and 5356 are the most common aluminum filler alloys. In fact, these two alloys make up 80 percent of all aluminum welding wire sold. So it stands to reason that one of the two is the right choice for most applications. However, the two are not always interchangeable.
It may be easier to remember if we think of 4043 as being the correct choice for welding 6XXX alloys and most casting alloys. When welding most 5XXX alloys and welding 5XXX alloys to 6XXX alloys, 5356 is the correct choice. It also can be a good choice for welding most 6XXX alloys. Now let’s concentrate on those applications in which 4043 is chosen.
Regarding differences between 4043 and 4047, 4043 basically is aluminum with 5 percent silicon added, while 4047 is aluminum with 12 percent silicon added. The additional silicon has several effects.
A pure metal has one specific melting point. However, an alloy melts over a range of temperatures. On heating, it begins to melt at one temperature, called the solidus, and finishes melting at a higher temperature, called the liquidus. If you look at the alloy between these two temperatures, you will see both liquid and solid. The temperature difference between the liquidus and solidus is called the melting range. It can be shown that the resistance to weld cracking is related to the melting range. The smaller the melting range, the more crack-resistant the alloy.
The 4043 wire has a solidus temperature of 1,065 degrees F and a liquidus temperature of 1,170 degrees F, or a melting range of 105 degrees F. The 4047 wire has a solidus temperature of 1,070 degrees F and a liquidus temperature of 1,080 degrees F, or a melting range of 10 degrees F. Therefore, 4047 is more crack-resistant than 4043, which is crack-resistant in its own right. This is the real advantage of 4047 over 4043. If you are using 4043 and still have weld cracking problems, try 4047. It probably will not crack.
The 4047 wire has two other advantages over 4043 wire. First, it is a bit stronger than 4043. However, the difference is only 1,000 or 2,000 pounds per square inch, so this advantage probably is insignificant. The molten weld pool also is slightly more fluid than 4043, which can sometimes be an advantage.
However, 4047 has disadvantages too. While 5356 is stronger than 4043 and 4047, it has more ductility. The 4043 wire has limited ductility, perhaps 7 to 8 percent. The 4047 wire has very little ductility, perhaps 2 to 4 percent. Most structural designs don’t take ductility into account. However, some structures are prone to plastic deformation during their lifetimes. For instance, automobiles sometimes are crashed, in testing and in use. In designing automotive structures, I would choose 4043 over 4047 for its better ductility.
You have discovered the other disadvantage of 4047: It is considerably more expensive than 4043. Some of the extra cost is because 4047 is not sold in high volumes, so some suppliers consider it a special-order item. However, the real cost associated with producing 4047 wire is its low elongation, which means that only one or two draw reductions can be taken before the wire becomes brittle enough to break. To prevent wire breakage, the coil of wire is taken offline to a furnace and annealed. This is called an intermediate anneal. The coil of wire then is put back onto the draw bench, and one or two more draws are done. Then it’s time for another intermediate anneal. You get the idea. Because of its lower elongation, 4047 requires several more intermediate anneals than 4043 during processing. So 4047 is more expensive than 4043. This is the reason for most of the cost difference between the two wires.
So should you give up on 4043 and switch to 4047 for all your applications? No. Using 4047 is not a panacea. Use 4043 like you do now for most applications. When you have an application that shows centerline weld cracking with 4043, try 4047. I’ve even had people tell me that you can’t get a crater crack with 4047, but I think that’s stretching the truth a bit.
About the Author
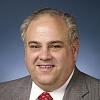
Frank Armao
Aluminum Consulting Inc.
440-479-0239
About the Publication
Related Companies
subscribe now
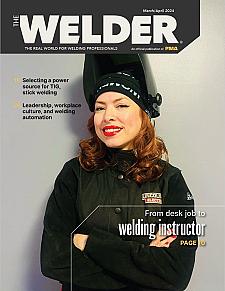
The Welder, formerly known as Practical Welding Today, is a showcase of the real people who make the products we use and work with every day. This magazine has served the welding community in North America well for more than 20 years.
start your free subscription- Stay connected from anywhere
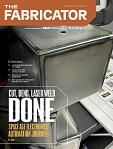
Easily access valuable industry resources now with full access to the digital edition of The Fabricator.
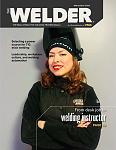
Easily access valuable industry resources now with full access to the digital edition of The Welder.
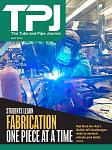
Easily access valuable industry resources now with full access to the digital edition of The Tube and Pipe Journal.
- Podcasting
- Podcast:
- The Fabricator Podcast
- Published:
- 04/16/2024
- Running Time:
- 63:29
In this episode of The Fabricator Podcast, Caleb Chamberlain, co-founder and CEO of OSH Cut, discusses his company’s...
- Industry Events
16th Annual Safety Conference
- April 30 - May 1, 2024
- Elgin,
Pipe and Tube Conference
- May 21 - 22, 2024
- Omaha, NE
World-Class Roll Forming Workshop
- June 5 - 6, 2024
- Louisville, KY
Advanced Laser Application Workshop
- June 25 - 27, 2024
- Novi, MI