Independent welding consumables professional
- FMA
- The Fabricator
- FABTECH
- Canadian Metalworking
Categories
- Additive Manufacturing
- Aluminum Welding
- Arc Welding
- Assembly and Joining
- Automation and Robotics
- Bending and Forming
- Consumables
- Cutting and Weld Prep
- Electric Vehicles
- En Español
- Finishing
- Hydroforming
- Laser Cutting
- Laser Welding
- Machining
- Manufacturing Software
- Materials Handling
- Metals/Materials
- Oxyfuel Cutting
- Plasma Cutting
- Power Tools
- Punching and Other Holemaking
- Roll Forming
- Safety
- Sawing
- Shearing
- Shop Management
- Testing and Measuring
- Tube and Pipe Fabrication
- Tube and Pipe Production
- Waterjet Cutting
Industry Directory
Webcasts
Podcasts
FAB 40
Advertise
Subscribe
Account Login
Search
Consumables Corner: Before choosing filler, know your 4140
- By Nino Mascalco
- June 24, 2014
- Article
- Consumables
Q: We need to weld 4140 steel to AR 360 plate and are thinking of using an E120 electrode to try and match the strength. Is this the right electrode for our welding application?
A: Before you choose a filler metal, there are a few things you should consider for this application.
First, 4140 steel comes in many grades, which can influence filler metal type, preheat temperatures, and postweld treatments. Was the 4140 chosen for its strength or its ability to handle impact and abrasive conditions? Will the welded joints be subjected to high-impact and abrasive conditions as well? Since that information isn’t available, we will go with the best-case scenario and assume that the final product will have to withstand impact and abrasive conditions.
Because AR 360 isn't used for structural applications, there is no need to try to match tensile strength. Depending on the heat treatment of the 4140, tensile strength can be from 90 to 160 KSI. When welding these two base materials, alloy recovery will occur in the weld, which will yield improved properties; therefore, you wouldn't want or need to weld with a high-tensile-strength filler metal because this additional alloy pickup would cause the weld to crack.
Since most of your typical filler metals will not withstand abrasive environments, you will more than likely want to weld the surface with a hardfacing electrode to cover your structural supporting welds. Usually one to two layers of hardfacing weld covering the entire surface of the primary weld will do the job. These electrodes are designed to handle impact, abrasive conditions, or a combination of the two. You’ll want to select the best hardfacing electrode based on your information of the in-service condition of the weldment.
Finally, the proper filler metal can be a low-carbon E70XX or E80XX electrode with some nickel, or a stainless steel electrode such as E309. E70XX is the most cost-effective of the three choices; however, if the in-service conditions are subzero temperatures, you will want something that can handle cold temperatures, hence the nickel-based or stainless steel filler metals.
Don't forget to preheat the 4140 and slow-cool the final weldment, because it is prone to cracking. Without knowing the specific heat treatment of the 4140, I generally recommend a preheat temperature of at least 450 degrees F.
About the Author
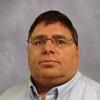
About the Publication
Related Companies
subscribe now
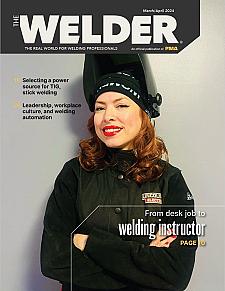
The Welder, formerly known as Practical Welding Today, is a showcase of the real people who make the products we use and work with every day. This magazine has served the welding community in North America well for more than 20 years.
start your free subscription- Stay connected from anywhere
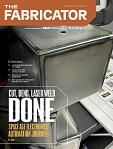
Easily access valuable industry resources now with full access to the digital edition of The Fabricator.
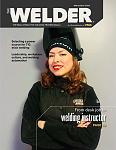
Easily access valuable industry resources now with full access to the digital edition of The Welder.
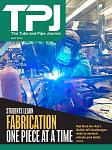
Easily access valuable industry resources now with full access to the digital edition of The Tube and Pipe Journal.
- Podcasting
- Podcast:
- The Fabricator Podcast
- Published:
- 04/16/2024
- Running Time:
- 63:29
In this episode of The Fabricator Podcast, Caleb Chamberlain, co-founder and CEO of OSH Cut, discusses his company’s...
- Industry Events
16th Annual Safety Conference
- April 30 - May 1, 2024
- Elgin,
Pipe and Tube Conference
- May 21 - 22, 2024
- Omaha, NE
World-Class Roll Forming Workshop
- June 5 - 6, 2024
- Louisville, KY
Advanced Laser Application Workshop
- June 25 - 27, 2024
- Novi, MI