Contributing Writer
- FMA
- The Fabricator
- FABTECH
- Canadian Metalworking
Categories
- Additive Manufacturing
- Aluminum Welding
- Arc Welding
- Assembly and Joining
- Automation and Robotics
- Bending and Forming
- Consumables
- Cutting and Weld Prep
- Electric Vehicles
- En Español
- Finishing
- Hydroforming
- Laser Cutting
- Laser Welding
- Machining
- Manufacturing Software
- Materials Handling
- Metals/Materials
- Oxyfuel Cutting
- Plasma Cutting
- Power Tools
- Punching and Other Holemaking
- Roll Forming
- Safety
- Sawing
- Shearing
- Shop Management
- Testing and Measuring
- Tube and Pipe Fabrication
- Tube and Pipe Production
- Waterjet Cutting
Industry Directory
Webcasts
Podcasts
FAB 40
Advertise
Subscribe
Account Login
Search
End forming of square and rectangular tubing
Opportunities abound for reducing dies
- By Joe Dean
- April 15, 2002
- Article
- Tube and Pipe Fabrication
End forming applications practically are limitless. Ranging from the simple to the complex, they include reduction of the outside diameter, expansion of inside diameter, flaring, beading, and completely altering the original shape.
Square and rectangular tubing present unique challenges for end forming. Inline forming is a traditional forming method for square and rectangular shapes; however, segmented tooling has been growing in acceptance for forming these shapes.
A Conventional Approach
Inline forming is a process in which a workpiece is held in a clamping device and a tool is pushed over the workpiece to generate the desired profile. While suitable for many applications, this method has several drawbacks.
The tooling cannot be adjusted for various sizes of tubing—it is dedicated to one size only.
The length of the end form is determined by the travel of the tool and length of the tube that is not clamped by the clamping dies. This distance can cause the end form to be off-center from the original part. Off-center end forms can render the finished product unusable —for instance, a garage door track assembled from track sections with off-center ends has transitions between each section. If the transitions, or steps, between each section are too extreme, the garage door mechanism cannot travel the length of the track.
Also, tool life is a concern because of the friction forces involved and possible presence of dirt particles or metal burrs.
Segmented Tooling
Another approach for forming square or rectangular tube is to use segmented tooling. The most common application is a slip fit in which the end of one tube slips into the end of another tube.
Segmented tooling is based on four dies closing simultaneously. This action applies the work force all at once. In addition to completely altering the original shape, segmented tooling can offer a better-defined transition area with increased strength. An expanding mandrel can be used for applications with complex profiles; a simpler fixed mandrel can help direct the material flow in the desired areas.
The internal dies, which are informally called expanding fingers, can be moved into positions that define the exact internal profile of the tube. After forming they can collapse a small amount, reducing the amount of force required to remove the finished workpiece from the tooling.
In cases of a less accurate internal profile but a complex outside shape, a fixed plug can redirect the material flow to ensure correct coverage. This type of mandrel can be made from a tool steel with a highly polished surface or carbide coating to reduce wear caused by workpiece removal. The contact area is smaller than that of an expanding mandrel, and only a small surface will remain in contact at the end of cycle. Material springback is also a factor in decreasing friction.
In both cases—whether using a fixed plug or an expanding mandrel—the outside dimensions that define the type of fit in the tube can be changed easily because segmented tooling is suitable for a small range of sizes around the nominal value that it was designed for.
Segmented tooling generally is designed for universal drop-in, inside-outside (I/O) tooling in both standard and large-barrel configurations. It can accommodate tube sizes ranging from 1 by 1/4 in. to 4 by 4 in. The standard angle is 14 degrees on the cone and outside of the dies. Designing tooling around industry standards allows the use of standard tool components for new applications.
When more reduction is necessary, a larger angle can be used. This allows for a larger opening to fit the new part into the forming dies. However, dies with a custom angle require a custom cone with the same angle.
Based on the close tolerances of profiled dimensions, stringent requirements—part straightness, equal step-down from the original tube to profile on all sides (common centerlines), minimal taper condition on the formed are—create new challenges in the forming process.
Segmented tooling does present some drawbacks, however, such as tool marks made on the wall of the tube at the edges of the forming dies. Also, the amount of reduction that can be achieved is limited.
Die Design for Welded Tube. Another challenge is in the use of welded tube. One side of the rectangle contains the welded seam. Compared to the rest of the tube circumference, the weld seam has significant differences in strength, hardness, flow characteristics, and springback. The welded side and the opposite side resist the forming forces with different values, resulting in slightly different dimensions.
A die design that allows the dies some degree of axial rotation is beneficial for self-alignment for forming round parts. However, this is a drawback with nonround parts. The small gap between the dies, and their ability to rotate axially, allows the dies to close more on the side opposite the weld seam. Square and rectangular parts formed with this type of die are not symmetrical.
Another die design—one that is specifically intended for rectangular tube—has a guiding system that restricts axial rotation, helping to ensure a proper approach of all four dies at 45 degrees. The guiding system prevents axial pivoting of the dies, resulting in symmetrically formed parts.
As parts are fed manually into the machine, the dies contact the forming length while the rest of the tube is free. This condition leads to parts with deviation of the formed end toward the weld, as stress in the tube is concentrated in a pattern dependent on the weld. Assembling two or three of these sections together accentuates this deficiency. A set of dies that contact both the end formed area and some length of the unformed area help to decrease or eliminate these deviations.
Ram Forming or Segmented Tooling?
Although ram forming continues to be a viable end-forming method, use of segmented tooling is growing. In applications that have more stringent forming requirements, segmented tooling can be a suitable alternative.
About the Author
Joe Dean
2400 Southeastern Ave.
Indianapolis, IN 46201-4161
877-227-4786
About the Publication
Related Companies
subscribe now
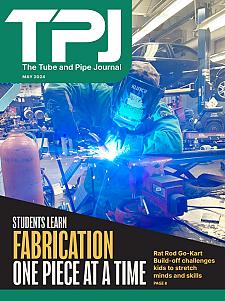
The Tube and Pipe Journal became the first magazine dedicated to serving the metal tube and pipe industry in 1990. Today, it remains the only North American publication devoted to this industry, and it has become the most trusted source of information for tube and pipe professionals.
start your free subscription- Stay connected from anywhere
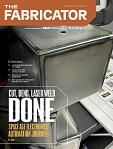
Easily access valuable industry resources now with full access to the digital edition of The Fabricator.
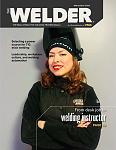
Easily access valuable industry resources now with full access to the digital edition of The Welder.
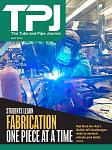
Easily access valuable industry resources now with full access to the digital edition of The Tube and Pipe Journal.
- Podcasting
- Podcast:
- The Fabricator Podcast
- Published:
- 04/16/2024
- Running Time:
- 63:29
In this episode of The Fabricator Podcast, Caleb Chamberlain, co-founder and CEO of OSH Cut, discusses his company’s...
- Trending Articles
Zekelman Industries to invest $120 million in Arkansas expansion
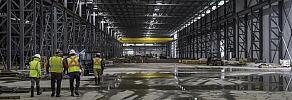
3D laser tube cutting system available in 3, 4, or 5 kW
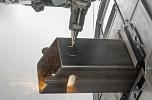
Corrosion-inhibiting coating can be peeled off after use
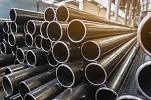
Brushless copper tubing cutter adjusts to ODs up to 2-1/8 in.
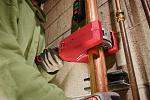
HGG Profiling Equipment names area sales manager
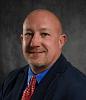
- Industry Events
16th Annual Safety Conference
- April 30 - May 1, 2024
- Elgin,
Pipe and Tube Conference
- May 21 - 22, 2024
- Omaha, NE
World-Class Roll Forming Workshop
- June 5 - 6, 2024
- Louisville, KY
Advanced Laser Application Workshop
- June 25 - 27, 2024
- Novi, MI