Independent welding consumables professional
- FMA
- The Fabricator
- FABTECH
- Canadian Metalworking
Categories
- Additive Manufacturing
- Aluminum Welding
- Arc Welding
- Assembly and Joining
- Automation and Robotics
- Bending and Forming
- Consumables
- Cutting and Weld Prep
- Electric Vehicles
- En Español
- Finishing
- Hydroforming
- Laser Cutting
- Laser Welding
- Machining
- Manufacturing Software
- Materials Handling
- Metals/Materials
- Oxyfuel Cutting
- Plasma Cutting
- Power Tools
- Punching and Other Holemaking
- Roll Forming
- Safety
- Sawing
- Shearing
- Shop Management
- Testing and Measuring
- Tube and Pipe Fabrication
- Tube and Pipe Production
- Waterjet Cutting
Industry Directory
Webcasts
Podcasts
FAB 40
Advertise
Subscribe
Account Login
Search
Consumables Corner: Defining current density
- By Nino Mascalco, Rob Koltz, and Steve Sigler
- June 5, 2014
- Article
- Consumables
Q: Our company manufactures cylindrical structures, including tanks and smokestacks made from A36 or A572 material. The material is burned to size on a plasma table and mechanically beveled. Process limitations cause gaps in the joints during fit-up. We use a 0.045-in.-dia. solid wire with a 75 percent Ar/25 percent CO2 shielding gas. The welders struggle with filling the gaps, which takes a considerable amount of time. They spend additional time backgouging or grinding the opposite side because of burn-through and other issues. It was suggested that we switch to a metal-cored wire because the current density is higher. Should we consider making this switch? Would a higher current density burn through easier?
A: It appears that your overall goal is to reduce additional joint preparation time and increase throughput. There are a number of ways to accomplish this goal.
Switching to a metal-cored wire is one option. And you’re right, there is a higher current density with cored wire. Current density is the amount of amps per cross-sectional area of the effective wire diameter. In cored wires such as metal-cored or flux-cored, no current passes through the powdered cores of the wires. Instead, all of the current passes through the outer portion or sheath of the filler metal. This means for a 0.045-in.-dia. cored wire versus a solid wire of the same diameter and at the same wire feed speeds, the cored wire will have a less effective cross-sectional area and therefore higher current density. In short, at the same wire feed speed, the cored wire will have lower overall amperage and may fill joint gaps more easily.
Since amperage is associated with penetration, lower amperage means less penetration or greater ability to fill gaps. Conversely, turning up the wire feed speed to match the amperage value with that of the solid wire will produce higher deposition rates, typically in the form of travel speed. This will reduce the likelihood of burning through.
Metal-cored wires are similar to solid wires in that they are both high-efficiency wires. Depending on shielding gas and weld parameters, typical efficiencies are from 92 to 99 percent. In comparison, the efficiency of flux-cored wire is in the lower to middle 80 percent range. The initial downside of cored wires is the higher cost to manufacture them, which makes them more expensive. However, if a filler metal cost increase can be offset by the time gained through reducing joint prep, backgouging, and ultrasonic testing (UT) failures, then it may be the fastest, most economical method to attain your goals.
Other options include improving joint fit-up. This could be done with a high-definition plasma that has a multiaccess head to perform plate beveling. However, this would be a significant investment for which you may want to calculate an ROI. Depending on your company’s capital budget, such an investment would be an ideal solution for the long run.
About the Authors
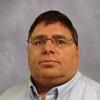
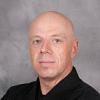
Rob Koltz
Application Engineer
411 S. Ebenezer Rd.
Florence, 29501
636-485-2253
Steve Sigler
Application Engineer
411 S. Ebenezer Rd.
Florence, South Carolina 29501
636-485-2253
About the Publication
Related Companies
subscribe now
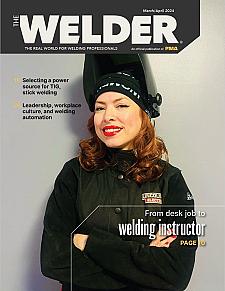
The Welder, formerly known as Practical Welding Today, is a showcase of the real people who make the products we use and work with every day. This magazine has served the welding community in North America well for more than 20 years.
start your free subscription- Stay connected from anywhere
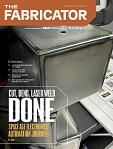
Easily access valuable industry resources now with full access to the digital edition of The Fabricator.
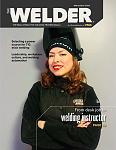
Easily access valuable industry resources now with full access to the digital edition of The Welder.
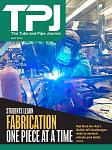
Easily access valuable industry resources now with full access to the digital edition of The Tube and Pipe Journal.
- Podcasting
- Podcast:
- The Fabricator Podcast
- Published:
- 04/16/2024
- Running Time:
- 63:29
In this episode of The Fabricator Podcast, Caleb Chamberlain, co-founder and CEO of OSH Cut, discusses his company’s...
- Trending Articles
Sheffield Forgemasters makes global leap in welding technology
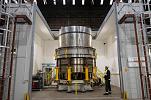
ESAB unveils Texas facility renovation
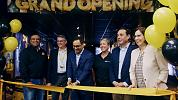
Engine-driven welding machines include integrated air compressors
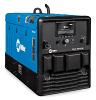
The impact of sine and square waves in aluminum AC welding, Part I
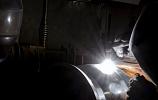
How welders can stay safe during grinding
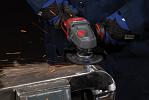
- Industry Events
16th Annual Safety Conference
- April 30 - May 1, 2024
- Elgin,
Pipe and Tube Conference
- May 21 - 22, 2024
- Omaha, NE
World-Class Roll Forming Workshop
- June 5 - 6, 2024
- Louisville, KY
Advanced Laser Application Workshop
- June 25 - 27, 2024
- Novi, MI