Director of Engineering
- FMA
- The Fabricator
- FABTECH
- Canadian Metalworking
Categories
- Additive Manufacturing
- Aluminum Welding
- Arc Welding
- Assembly and Joining
- Automation and Robotics
- Bending and Forming
- Consumables
- Cutting and Weld Prep
- Electric Vehicles
- En Español
- Finishing
- Hydroforming
- Laser Cutting
- Laser Welding
- Machining
- Manufacturing Software
- Materials Handling
- Metals/Materials
- Oxyfuel Cutting
- Plasma Cutting
- Power Tools
- Punching and Other Holemaking
- Roll Forming
- Safety
- Sawing
- Shearing
- Shop Management
- Testing and Measuring
- Tube and Pipe Fabrication
- Tube and Pipe Production
- Waterjet Cutting
Industry Directory
Webcasts
Podcasts
FAB 40
Advertise
Subscribe
Account Login
Search
Keeping hydroforming competitive
A call for improved specifications, processes
- By Klaus Hertell and Prashant Soman
- September 30, 2008
- Article
- Hydroforming
The market for hydroformed parts is substantial and diverse. Today's hydroformers make a multitude of components by forming tubes into various hollow shapes and sizes for use in the automotive, aerospace, plumbing, and appliance industries. The current North American tubular hydroforming market is estimated at $350 million per year, based on the rough calculation of 35 million parts produced per year multiplied by an average price of $10 per tubular part.
Hydroformers often face competition from the stamping industry, especially because the stamping industry has plenty of production capacity these days. In fact, recent price pressures associated with excess stamping capacity have caused a slight shift in the industry: A number of high-volume hydroformed parts have reverted to stamping, resulting in a lost market for both hydroformers and tube manufacturers.
To succeed in this competitive environment, the hydroforming industry must focus on ways to offer the marketplace products that are stronger, lighter, and less expensive than competing products. Hydroformers and tube manufacturers depend on each other, which implies opportunity for improvement if these two groups work together to investigate ways to reduce conversion costs in tube production.
This article serves as a call to the tube industry to explore the possibilities of reducing tube conversion costs by rethinking the required tube specifications. It also reviews process efficiencies from lessons learned in a commercial hydroforming production environment.
Conversion Costs at the Tube Mill
The conversion costs, which are the costs of rolling flat steel into a tube, handicap hydroformers but not stampers. Tube producers incur some costs in their efforts to produce tube that meets various standards or specifications, and incur other costs in testing the tube to verify that it does meet them. However, many tube specifications do not correspond to the requirements of the hydroforming process. Understanding what the tests determine and what the process actually needs can lead to ways to simplify the tube conversion process and reduce the cost of the tube (see Figure 1).
In other words, relaxing some of the tube mill's tolerances and requirements could make the rolling process easier and more cost-effective, while producing tubing that meets the hydroforming market's requirements.
Dimensional Requirements
ASTM A513, "Standard Specification for Electric-Resistance-Welded Carbon and Alloy Steel Mechanical Tubing," often is used as a base to specify tubes used in hydroforming. However, many of the criteria in this specification don't correspond to hydroforming requirements—some are too lax, some too stringent.
For example, consider a typical tube for hydroforming: hot-rolled 1010 steel tube that measures 2.75 inches in diameter, 0.083 in. thick, and 60 in. long. ASTM A513 calls for an OD tolerance of ±0.008 in. For hydroforming, this tolerance could be increased to almost ±0.016 in. without affecting the process. To meet this standard, tube mills use sizing rolls after welding to squeeze the oversized tubes to the correct diameter. This conversion step also work-hardens the tube material, leaving less formability available for hydroforming. Eliminating or minimizing the sizing step would provide two benefits: It would reduce tube producers' costs and improve the tube's formability.
Furthermore, the wall thickness tolerance specified in ASTM A513 is +0.004/-0.012 in. This does not always meet the process challenges of hydroforming. Tube mills typically target the lower end of the tolerance band and supply thinner tubes than those used in engineering analysis and product development. This leads to quality problems for the OEM and more scrap in the production process. The tolerance for the hydroforming process therefore should protect the minimum required wall thickness and be +0.012/-0.0 in.
Tube-end Conditions and Straightness Specs
Hydroformers often set the bar high when it comes to the end condition of the tube. They usually specify it to be cut perfectly, deburred, and in some cases chamfered. However, some tube-end sealing technologies available today eliminate the need for these expensive end-cut requirements. With an appropriate end-sealing technology, hydroformers can use tubes that are sheared only. It isn't necessary to use nick-and-shear, deburring, or chamfering processes.
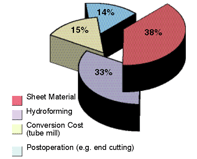
Figure 1 The cost breakdown for a typical hydroformed part reveals that tubing comprises more than 50 percent of the cost: 38 percent for sheet metal and 15 percent to convert sheet to tube.
Depending on the end application and process, such as whether the part requires bending, straightness tolerances on tubes also can be discarded.
Mechanical Properties Required for Bending and Hydroforming
The tube's formability is one of the most important concerns for hydroformers. Bending and hydroforming stretch and work-harden the material; bending usually stretches it in a uniaxial direction, while hydroforming stretches it in a biaxial direction.
ASTM A513 does not specify proper testing methods and limit values suitable for the hydroforming process. The existing standard calls for a traditional longitudinal tensile test to check material properties, as well as a flattening/flaring test to check the weld seam's quality. While the tensile test gives some indication of the amount of work-hardening during the tube rolling process, it is not necessarily an accurate predictor of the overall tube quality or formability. A burst test, which stretches the material in the biaxial direction and therefore emulates the stretching that occurs in hydroforming, would be a better match for hydroforming. Unfortunately, this method is not standardized in the industry and is limited to research and development purposes during the product development cycle. Implementing this test could greatly improve the reliability of the forming process and reduce scrap for hydroformers.
Various studies have shown that the weakest point in a tube is often next to the heat-affected zone (HAZ) near the weld seam or 180 degrees from the weld seam. Research also has revealed that tubes made from material slit from the center of a master coil perform better than those slit from the edges. These qualities cannot be measured with a single tensile test.
Careful analysis of hydroforming production processes reveals a good correlation between the n-value (work-hardening exponent) of the material and the scrap rate, which is the scrap caused by material failure (see Figure 2). The n-value is determined by a traditional tensile test and measures the formability of the material. It is found that the n-value is a better parameter for evaluating material than the more commonly used measurement of total elongation. This is because the n-value also determines the spread between the yield strength and tensile strength.
Efforts by Hydroformers to Reduce Costs
To reduce costs of the hydroforming portion of the piece price, hydroformers now are able to choose from several forming methods to produce the part (see Figure 3). Hydroformed parts which require no circumferential expansion (for example, some body-in-white parts) can be formed with a light-expansion method. Light expansion uses a low internal pressure and therefore has low requirements for tube quality, which reduces tube manufacturing costs. On the other hand, tubular parts which require high expansion, such as exhaust parts, require high pressure and tubes with stricter quality requirements.
The most critical area in reducing a hydroformed part's cost is in postprocessing (after hydroforming). The goal is to have the hydroformed part ready for assembly directly after hydroforming. Postprocessing operations such as cutting the part to length add manufacturing and material costs to the part (see Figure 1).
A new forming/sealing technology allows hydroformers to send parts cut to the correct length through the hydroforming process. This eliminates the postprocess end-cutting and uses 100 percent of the material (see Figure 4). This gives hydroforming a big advantage over stamping, which typically has a material utilization rate between 60 percent and 80 percent. This patented sealing technology does not require any special tubes and can be applied to all available methods of hydroforming—light, high, and extreme expansion.
Outlook
The growing demand for stiffer, stronger, and lighter automotive structures puts the hydroforming process in an advantageous market position. In the future, it is likely that the market for hydroformed parts will expand with more applications in automotive body-in-white structures. With increased cooperation between hydroformed part suppliers and tube manufacturers, the industry can successfully develop thinner, stronger tubes to support more hydroforming applications and grow the hydroform market together.
Klaus Hertell is general manager and Prashant Soman is a production engineer with Schuler Hydroforming Inc., 7145 Commerce Blvd., Canton, MI 48187, 734-207-7263, klaus.hertell@schulerinc.com, prashant.soman@schulerinc.com, www.schulerhydroforming.com.
About the Authors
Klaus Hertell
7145 Commerce Blvd.
Canton, MI 48187
734-207-7200
Prashant Soman
Production Engineer
7145 Commerce Blvd.
Canton, MI 48187
734-207-7263
About the Publication
Related Companies
subscribe now
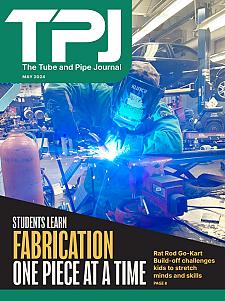
The Tube and Pipe Journal became the first magazine dedicated to serving the metal tube and pipe industry in 1990. Today, it remains the only North American publication devoted to this industry, and it has become the most trusted source of information for tube and pipe professionals.
start your free subscription- Stay connected from anywhere
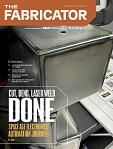
Easily access valuable industry resources now with full access to the digital edition of The Fabricator.
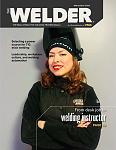
Easily access valuable industry resources now with full access to the digital edition of The Welder.
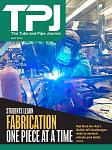
Easily access valuable industry resources now with full access to the digital edition of The Tube and Pipe Journal.
- Podcasting
- Podcast:
- The Fabricator Podcast
- Published:
- 04/16/2024
- Running Time:
- 63:29
In this episode of The Fabricator Podcast, Caleb Chamberlain, co-founder and CEO of OSH Cut, discusses his company’s...
- Trending Articles
Zekelman Industries to invest $120 million in Arkansas expansion
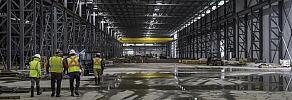
3D laser tube cutting system available in 3, 4, or 5 kW
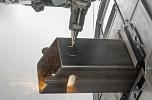
Corrosion-inhibiting coating can be peeled off after use
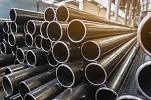
Brushless copper tubing cutter adjusts to ODs up to 2-1/8 in.
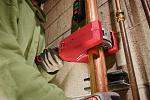
HGG Profiling Equipment names area sales manager
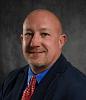
- Industry Events
16th Annual Safety Conference
- April 30 - May 1, 2024
- Elgin,
Pipe and Tube Conference
- May 21 - 22, 2024
- Omaha, NE
World-Class Roll Forming Workshop
- June 5 - 6, 2024
- Louisville, KY
Advanced Laser Application Workshop
- June 25 - 27, 2024
- Novi, MI