- FMA
- The Fabricator
- FABTECH
- Canadian Metalworking
Categories
- Additive Manufacturing
- Aluminum Welding
- Arc Welding
- Assembly and Joining
- Automation and Robotics
- Bending and Forming
- Consumables
- Cutting and Weld Prep
- Electric Vehicles
- En Español
- Finishing
- Hydroforming
- Laser Cutting
- Laser Welding
- Machining
- Manufacturing Software
- Materials Handling
- Metals/Materials
- Oxyfuel Cutting
- Plasma Cutting
- Power Tools
- Punching and Other Holemaking
- Roll Forming
- Safety
- Sawing
- Shearing
- Shop Management
- Testing and Measuring
- Tube and Pipe Fabrication
- Tube and Pipe Production
- Waterjet Cutting
Industry Directory
Webcasts
Podcasts
FAB 40
Advertise
Subscribe
Account Login
Search
Process audits in manufacturing: Do as the accountants do
How the process audit prevents the unexpected
- By Dick Kallage
- February 10, 2016
- Article
- Shop Management
The word audit rarely drives anyone to party in the streets—unless, of course, you happen to be the auditor who is chomping at the bit to bring the cringing audited to heel. If the word is preceded by “IRS,” well, it can be positively frightening.
If you stuck around through that opening paragraph, be assured that this column has nothing to do with the IRS. You have enough to worry about. It has a lot to do with calibrating what a company actually does in the conduct of its business. It also has a lot to do with improvement.
Most of you who have spent time in operations are familiar with the annual inventory count. This is the time of year when operations are stopped while raw, work-in-process (WIP), and finished-goods inventories are counted by part number or some other identifier. The counts usually are recorded on some standard form. Normal production resumes only after the counts have been officially recorded by someone associated with the accounting function. In many cases, the counts themselves are sampled by someone other than the person doing the original count, just to check the soundness of the counting process itself. (This sampling is a form of an audit, by the way.)
While most of the readers of this column have participated in one or more of these inventory counts, relatively few know exactly why we go through this process. Most think, correctly, that it brings inventory counts that we think we have to the levels that we actually have. Fair enough. That alone would make this rather tedious process well worth it, especially if you’re not the one stuck with actually doing the counts.
But the highly orchestrated inventory count is actually part of a broader and extremely important process: the financial audit, which has the sole purpose of assuring any interested party that the financial books are substantially correct. It essentially checks the soundness of the transactional processes necessary to ensure that the company is under sufficient financial control.
The periodic inventory count is critical to this, as are examinations of other key accounts such as payroll, receipts from and payments to vendors, and other fundamental transactions. I won’t bore you with the financial audit process, but rest assured that it is necessary. It helps a company avoid a lot of unpleasantness, including an IRS audit and, even worse, running out of cash.
Everything Changes
If everyone who puts together the financial statements is honest, true, and trained, do we really need the audit? The answer is yes, and here’s why: Transactional processes tend to drift—in how the process is done, who does it, and the tools employed—and for processes done by us humans, they are inherently susceptible to variation. If this is true (and it is) for transactional processes like filling out paperwork, then it is also true for the processes involved in actually making the product.
ISO 9001 is often described by a deceptively simple phrase: State and document what you do and then faithfully do what you stated. But even without an ISO discipline, company leaders often assume that things are being done in certain defined ways. Those methods are conveyed to the people performing the process through training, usually of the on-the-job variety. Documentation can range from a formal process document to a handwritten instruction taped on a machine. So far, so good—though the handwritten, taped-on thing is definitely suspect.
Then unexpected things happen, and off we go trying to figure out what went wrong. After a lot of looking, we inevitably find out that one of three things occurred:
- The process wasn’t done like we thought it was to be done. It had somehow changed or was never implemented properly in the first place.
- The process, even when performed correctly, was inherently incapable of providing the quality of output or the consistency required. Basically, its Cpk (process capability index) was insufficient for the task.
- The process was capable, usually done properly and as expected, but a random error occurred.
The third of these is difficult or perhaps impossible to prevent entirely, especially if people are involved. But in the scheme of things, this cause is usually small potatoes compared to the first two. This begs the question, Why do we too often find that either the process wasn’t being done as prescribed, or that the process itself wasn’t capable of producing the necessary results? And why do we seem to find out only when something really bad has happened?
The answers are simple: We never checked; or we checked it out and verified it once when the process was commissioned, but never again. We have no way of detecting unfavorable process drift until something unexpected (usually bad) occurs. This is a pretty costly way of verifying process integrity.
In some cases process drift is actually favorable. For example, an operator may perform minor changes for convenience, like rearranging his workstation or using better fixturing. (Although, even in the cases of positive attempts to improve, the law of unintended consequences can raise its head.) Sadly, most drift is not favorable simply because there are far more ways for a change to be negative than positive.
So, as you can surmise, the situation is crying out for a means to ensure processes stay stable and under control. This is the role of the process audit.
Process Audits
Readers of this column know that I often cite best practices employed by outstanding companies. They use these practices for a reason: to enhance the overall economics of the organization. One practice that I haven’t featured is the process audit. It’s simply a periodic check of the methods and procedures employed to successfully operate the business.
For example, in production operations, a process audit entails a regular, detailed examination of the key processes used in physically building products. We define “key processes” as those that are both commonly used and whose integrity are critical to product quality.
Great operations go one step further and verify that the process is also capable of the throughput and uptime assumed in estimating and scheduling. As I wrote in a previous column on scheduling and on-time delivery performance, two common root causes for chronic poor delivery performance (and/or excessive overtime) is that one or more production process has lower throughput and/or uptime than planned.
An audit of the process can help detect and correct these problems. Too many companies do this only when the pain of poor performance becomes unsustainable. And they do it once and move on, only to see the pain return later.
Great companies do the audit regularly before things go south. And they do it because they believe that since they accepted an order from a customer, part of that acceptance is the promise that the processes employed in satisfying that order are indeed capable.
At the very least, process audits for key production processes should verify:
- That these procedures and methods are compatible with and reinforce the quality of the output.
- That these procedures are capable (in the quality sense) over the range of products that will be produced.
- That the operators executing these procedures are sufficiently trained and know why these procedures are critical.
- That the process is capable of producing the range of throughput expected by estimating, costing, and scheduling.
- That the process uptime is generally consistent with the data in those systems.
- That there is a means for detecting and correcting problems in the process.
- That any special considerations for an individual customer’s requirements are indeed being performed.
The process audit has two versions. The first is the baseline where the audit is done for the first time or after a process change. This sets the reference point for the second version: the integrity or maintenance audit that ensures that no significant process drift has occurred. This audit requires something to compare to, which means the process reference point has to be documented. That is a key reason for the documentation requirements in ISO and other total quality management (TQM) systems.
If you want to avoid a lot of unexpected grief in production, do what the accountants do. Audit regularly.
About the Author
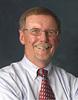
Dick Kallage
Related Companies
subscribe now
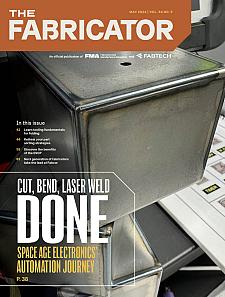
The Fabricator is North America's leading magazine for the metal forming and fabricating industry. The magazine delivers the news, technical articles, and case histories that enable fabricators to do their jobs more efficiently. The Fabricator has served the industry since 1970.
start your free subscription- Stay connected from anywhere
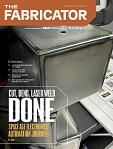
Easily access valuable industry resources now with full access to the digital edition of The Fabricator.
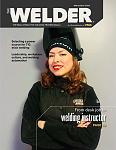
Easily access valuable industry resources now with full access to the digital edition of The Welder.
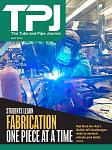
Easily access valuable industry resources now with full access to the digital edition of The Tube and Pipe Journal.
- Podcasting
- Podcast:
- The Fabricator Podcast
- Published:
- 04/16/2024
- Running Time:
- 63:29
In this episode of The Fabricator Podcast, Caleb Chamberlain, co-founder and CEO of OSH Cut, discusses his company’s...
- Industry Events
16th Annual Safety Conference
- April 30 - May 1, 2024
- Elgin,
Pipe and Tube Conference
- May 21 - 22, 2024
- Omaha, NE
World-Class Roll Forming Workshop
- June 5 - 6, 2024
- Louisville, KY
Advanced Laser Application Workshop
- June 25 - 27, 2024
- Novi, MI