AWS CWI, CWE, NDE Level III
- FMA
- The Fabricator
- FABTECH
- Canadian Metalworking
Categories
- Additive Manufacturing
- Aluminum Welding
- Arc Welding
- Assembly and Joining
- Automation and Robotics
- Bending and Forming
- Consumables
- Cutting and Weld Prep
- Electric Vehicles
- En Español
- Finishing
- Hydroforming
- Laser Cutting
- Laser Welding
- Machining
- Manufacturing Software
- Materials Handling
- Metals/Materials
- Oxyfuel Cutting
- Plasma Cutting
- Power Tools
- Punching and Other Holemaking
- Roll Forming
- Safety
- Sawing
- Shearing
- Shop Management
- Testing and Measuring
- Tube and Pipe Fabrication
- Tube and Pipe Production
- Waterjet Cutting
Industry Directory
Webcasts
Podcasts
FAB 40
Advertise
Subscribe
Account Login
Search
Welding technician and welding technologist—what’s the difference?
- By Professor R. Carlisle "Carl" Smith
- February 12, 2015
- Article
- Shop Management
The duties, training, and educational requirements for welding technicians and welding technologists can be described in many ways. AWS committees have been and currently are debating these subjects. So far they have been unable to differentiate the definitions of a welding technician and a welding technologist. Having observed and served in both fields for 50+ years, I feel that I am qualified to define each title holder.
Welding Technician
A technician is defined in the American Heritage Dictionary as an expert in a specific subject or professional area. I tend to agree with this definition, but I think the more correct definition would be specialist, rather than expert. Those of us who are a bit modest shy away from the title of expert.
The welding technician term was defined several years ago by a gentleman named Louis DeFreitas, who was a welding instructor in California. In my opinion, his definition was perhaps the most accurate: "A welding technician is the most important connection" between the engineering department and the welding shop.
Educational Requirements. A welding technician must receive a general education in practical math, English, written and oral communication, and now in computer literacy. Beyond these requirements, the technician must be trained in draftsmanship, metallurgy, and hands-on welding and cutting.
The technician also must be able to establish, prepare, and test welding and cutting procedures for the various code requirements. Welding and cutting today are quite different from the time when carbon steel was used almost exclusively in fabrication. Technicians must learn how to handle high-nickel alloys (Sam Kiser, the nickel man, said, "Cleanliness is next to godliness" when welding the high-nickel alloys). The joint designs for nickel alloys and other materials differ from those for plain carbon steel.
Training for these tasks can be obtained from schools like the Hobart Institute of Welding Technology and various seminars that are available from both welding and base material producers.
Knowledge of Codes and Standards. Technicians must be well-versed in all of the codes and standards that pertain to a particular project. For structures, such as bridges and buildings, AWS D1.1 provides the needed information. For pressure vessels and piping, ASME Section IX is the proper code. For pipelines and related facilities, API 1104 is the leading standard.
Many other codes and standards stipulate helpful and mandatory welding information. Code clinics are available, both online and in person. The cost of these clinics often is covered by the employer, but even if the cost isn't covered, technicians should participate in as many sessions as possible.
The Nickel Institute (Nickel Development Institute) provides some extremely valuable informational seminars related to high-nickel and stainless steel materials.
The AWS standard for certification of a welding technician requires a minimum of five years' experience in the fabrication field, plus related education. A few community and technical colleges offer this type of training, including Edison State Community College in Ohio, West Virginia University at the Parkersburg Campus, and two new programs being launched in West Virginia—Eastern West Virginia Community and Technical College, Moorefield, and Pierpont Community and Technical College in Fairmont.
The new BridgeValley Community and Technical College in South Charleston, W.V., also is in the beginning stages of offering this type of training and has already purchased some fairly sophisticated equipment. This school has an exceptional, brand-new, state-of-the art facility that will lend itself to training both the technician and the technologist.
Responsibilities. In many cases, the engineering department is not aware of the difficulties that vague drawings and instructions cause. Although most engineers are well-versed in making drawings that include notes that describe the parts to be fabricated, they sometimes are unaware of the shop's assembly practices. Some of the specified joints may be impossible to make with the available equipment.
The welding technician often determines the cutting, fitting, and welding sequence. The particular equipment in the fab shop sometimes is the determining factor. Cutting the material with the proper method or process is an extremely important element in the overall fabrication.
Some shops have a waterjet, precision cutting equipment that produces a surface comparable to a machined finish. Other shops use plasma cutting, which causes a slight bevel rather than a straight 90-degree cut on the edge. This process, like the oxyfuel cutting process, requires grinding to remove the dross and straighten the cut edges.
So what does all this have to do with the technician? When the engineer specifies the length and width of a certain plate or other shape, the cutting kerf's effect on the overall length and width must be taken into account. (The kerf is the space between parts to be assembled caused by the cutting or grinding.) The technician has the task of informing the engineering department that a particular allowance must be made to minimize the kerf (Figure 1).
Other important factors pertaining to the reduction of the overall length and width are the welding process and the welding sequencing. Some welding processes, such as gas metal arc welding (GMAW/MIG) and flux-cored arc welding (FCAW), produce a rapid heat input that minimizes material shrinkage and distortion. On the other hand, gas tungsten arc welding (GTAW/TIG) produces a very slow heat input and therefore causes more shrinkage in the part.
The technician must always be conscious of the significance of shall (mandatory) and should (suggestion) in codes and standards. AWS D1.1 issues a mandatory directive for weld progression. "The direction of the general progression in welding on a member shall be from points where parts are relatively fixed in position with respect to each other, toward points having a greater relative freedom of movement."
AWS D1.1 also suggests that "in assemblies, joints expected to have significant shrinkage should usually be welded before joints expected to have lesser shrinkage. They should also be welded with as little restraint as possible." The reason for limiting the restraint is that residual stresses may build up in the assembly and cause delayed or immediate cracking.
The technician also determines the amount of preheat required for the related thickness and amount of restraint. Preheat is an excellent method for preventing distortion and shrinkage in any weldment, structural or otherwise. The technician or a designee must monitor the temperature of the weld area at all times.
AWS D1.1 includes a preheat chart for materials and thicknesses. It is up to the technician to establish the amount of preheat to apply to a highly restrained section of the weldment. This is one of the times that the technician might consult the technologist, who should be able to calculate the amount of restraint involved. The technician is aware that the weld reaches its ultimate yield strength upon solidification and that transverse intersecting welds are the most highly restrained.
The real difference between the technician and the technologist is that the technician divides time between the engineer and technologist and the welding shop. The technician is more involved in the practical, hands-on welding, while the technologist actually performs some engineering department functions.
Welding Technologist
The technologist,bydefinition, is engaged in the research and development area of welding. He or she is responsible for determining the proper metallurgical compatibility between the base material and the welding material and establishing which materials are best-suited for the fabricated product's end use.
Educational Requirements. Educational requirements for a technologist are much more in-depth and diversified than those for a technician. R&D often requires a deep understanding of metallurgy and the chemistry that goes along with it. The periodic table of elements can always be found in the technologist's office, and the elements and their uses are embedded in the technologist's mind. Practice in the chemistry laboratory is an important training component.
The technologist must be familiar with both the mechanical and physical properties of metal.
Technical writing also is a must. A technologist must be able to convey the results of the R&D to the technician in a manner that is easily understood. The technician then deciphers how and how much of the information needs to be relayed to the welding foreman and the welders.
In some cases, the technologist is required to make oral presentations to his own company or to the customer the project is being built for. This requires some form of oral communication training, either interpersonal or public speaking.
The math educational requirements are much more in-depth than those necessary for the technician. Calculus and structures of mathematics are part of everyday tasks for the technologist, who also must be taught material strength formulae.
Responsibilities. For structural projects, the technologist must consider whether the components involved must be rigid or need to flex under load. A material's ductility often is determined by proof tests, in which the material (often including the welded portion) is placed in a machine and flexed multiple times until failure occurs. This is referred to as a fatigue test.
In some cases, the ductility test is used to determine the amount that hardness increases in the base material, the weld, and the heat-affected zone, especially if the material is high in manganese or other elements that may cause work hardening or embrittlement. The technologist must decide which tests are necessary for producing a product that will not fail in service.
With high-nickel and stainless steel alloys, corrosion most often is the factor that must be addressed. The technologist must determine which alloys are the most corrosion-resistant for the medium (acid, chlorine, halogen) to be used. This task often requires extensive research and testing.
Figure 2 is an actual test performed by a company involved in building a scrubber for a power plant. When this material was welded with nickel wire (ERNiCrMo-3), no corrosion was in the weld area. When it was welded with ER-2209 welding wire, the corrosion was worse in the weld area, especially in the HAZ, than in the base material.
This is just one of the tasks a technologist performs. He or she might also conduct tensile, low-mu (for magnetic permeability), and other physical and mechanical tests when specifications are not provided by the customer.
Both the technician and technologist roles are very important in the welding industry, especially when a welding engineer is unavailable. Welding engineers are scarce. With only a few in the U.S. and only one recognized welding engineering program, it is not likely the number will increase anytime soon. Most companies rely on the technician and the technologist to get the job done.
About the Author
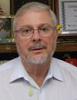
Professor R. Carlisle "Carl" Smith
Weld Inspection & Consulting
PO Box 841
St. Albans, WV 25177
304-549-5606
subscribe now
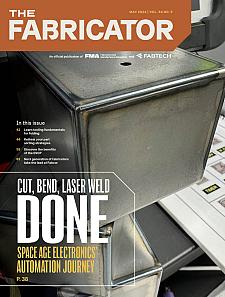
The Fabricator is North America's leading magazine for the metal forming and fabricating industry. The magazine delivers the news, technical articles, and case histories that enable fabricators to do their jobs more efficiently. The Fabricator has served the industry since 1970.
start your free subscription- Stay connected from anywhere
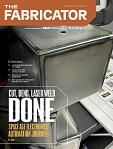
Easily access valuable industry resources now with full access to the digital edition of The Fabricator.
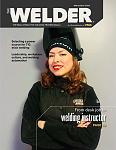
Easily access valuable industry resources now with full access to the digital edition of The Welder.
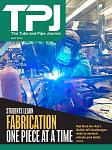
Easily access valuable industry resources now with full access to the digital edition of The Tube and Pipe Journal.
- Podcasting
- Podcast:
- The Fabricator Podcast
- Published:
- 04/16/2024
- Running Time:
- 63:29
In this episode of The Fabricator Podcast, Caleb Chamberlain, co-founder and CEO of OSH Cut, discusses his company’s...
- Industry Events
16th Annual Safety Conference
- April 30 - May 1, 2024
- Elgin,
Pipe and Tube Conference
- May 21 - 22, 2024
- Omaha, NE
World-Class Roll Forming Workshop
- June 5 - 6, 2024
- Louisville, KY
Advanced Laser Application Workshop
- June 25 - 27, 2024
- Novi, MI