Contributing editor
- FMA
- The Fabricator
- FABTECH
- Canadian Metalworking
Categories
- Additive Manufacturing
- Aluminum Welding
- Arc Welding
- Assembly and Joining
- Automation and Robotics
- Bending and Forming
- Consumables
- Cutting and Weld Prep
- Electric Vehicles
- En Español
- Finishing
- Hydroforming
- Laser Cutting
- Laser Welding
- Machining
- Manufacturing Software
- Materials Handling
- Metals/Materials
- Oxyfuel Cutting
- Plasma Cutting
- Power Tools
- Punching and Other Holemaking
- Roll Forming
- Safety
- Sawing
- Shearing
- Shop Management
- Testing and Measuring
- Tube and Pipe Fabrication
- Tube and Pipe Production
- Waterjet Cutting
Industry Directory
Webcasts
Podcasts
FAB 40
Advertise
Subscribe
Account Login
Search
Appliance stamper draws on magnetic die clamping to accelerate its uptime
Reducing die changeover downtime lowers labor requirements
- By Kate Bachman
- May 5, 2010
- Article
- Bending and Forming
Situation
In the home appliance industry, designs are constantly changing and updating to meet consumer tastes and changing market demands. Modern appliances may have contoured enclosures, relocated doors, better energy efficiency, and new colors. This means production methods must cycle frequently also.
But the ability to be push-button responsive doesn’t happen without being flexible.
When an appliance-maker’s new product lines went into production, the new designs required the stamping of a toggle lock door bracket.
For the stamping supplier forming the bracket, this high production volume necessitated tripling the number of shifts. But tripling the number of shifts increased labor costs, as well as utility and material delivery costs.
The stamper looked for ways to decrease the labor-hours to resume a single-shift operation.
Resolution
After examining its die changeover process, the stamper implemented quick die changeover and installed magnetic die clamping.
One press cell served as an internal beta site. The initial baseline of the changeover, from last good part to next good part, was roughly 45 minutes. The stamper was cycling through 15 tools every three days. Accumulatively, 15 changeovers every three days at 45 minutes each consumed nearly an entire shift every week.
First, the stamper standardized all the tooling to have common 15-inch shut heights.
The company installed Tecno-magnete®’s magnetic die clamping system. The entire bolster was replaced with a new steel bolster with magnets built into it. A 1.7-in.-thick magnetic plate was added to the ram. A keyway ran right to left along the feed line. The bottoms of the dies were solid-plated with a 1-in. steel plate to maximize the metal contact with the magnet.
The press’s new bolster was equipped with roller arms to move the die. Pneumatic ball die lift rails were installed in the bolster also. The operator activates the lift balls upward, manually pushes the die onto the rollers, and a pin on each end of the die falls into the keyway. Then the operator deactivates the lift rails, brings the ram down to the bottom, and activates the magnetic system using two buttons. One magnetizes the bottom die and the other magnetizes the top.
Operators now exchange dies in less than six minutes. Each operator runs two presses at the same time in an OBI cell.
The magnetic die clamping eliminated 90 percent of the setup time, and paid for itself in five months, the company said. The stamping components supplier was able to resume a single-shift operation.
About the Author
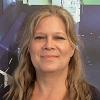
Kate Bachman
815-381-1302
Kate Bachman is a contributing editor for The FABRICATOR editor. Bachman has more than 20 years of experience as a writer and editor in the manufacturing and other industries.
subscribe now
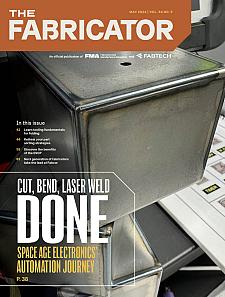
The Fabricator is North America's leading magazine for the metal forming and fabricating industry. The magazine delivers the news, technical articles, and case histories that enable fabricators to do their jobs more efficiently. The Fabricator has served the industry since 1970.
start your free subscription- Stay connected from anywhere
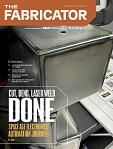
Easily access valuable industry resources now with full access to the digital edition of The Fabricator.
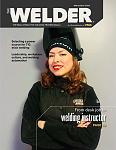
Easily access valuable industry resources now with full access to the digital edition of The Welder.
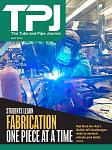
Easily access valuable industry resources now with full access to the digital edition of The Tube and Pipe Journal.
- Podcasting
- Podcast:
- The Fabricator Podcast
- Published:
- 04/16/2024
- Running Time:
- 63:29
In this episode of The Fabricator Podcast, Caleb Chamberlain, co-founder and CEO of OSH Cut, discusses his company’s...
- Trending Articles
Capturing, recording equipment inspection data for FMEA
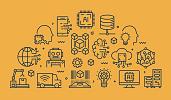
Tips for creating sheet metal tubes with perforations
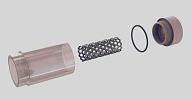
Are two heads better than one in fiber laser cutting?
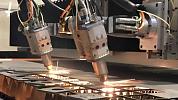
Supporting the metal fabricating industry through FMA
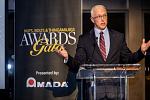
Omco Solar opens second Alabama manufacturing facility
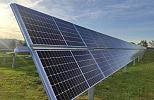
- Industry Events
16th Annual Safety Conference
- April 30 - May 1, 2024
- Elgin,
Pipe and Tube Conference
- May 21 - 22, 2024
- Omaha, NE
World-Class Roll Forming Workshop
- June 5 - 6, 2024
- Louisville, KY
Advanced Laser Application Workshop
- June 25 - 27, 2024
- Novi, MI