Contributing Writer
- FMA
- The Fabricator
- FABTECH
- Canadian Metalworking
Categories
- Additive Manufacturing
- Aluminum Welding
- Arc Welding
- Assembly and Joining
- Automation and Robotics
- Bending and Forming
- Consumables
- Cutting and Weld Prep
- Electric Vehicles
- En Español
- Finishing
- Hydroforming
- Laser Cutting
- Laser Welding
- Machining
- Manufacturing Software
- Materials Handling
- Metals/Materials
- Oxyfuel Cutting
- Plasma Cutting
- Power Tools
- Punching and Other Holemaking
- Roll Forming
- Safety
- Sawing
- Shearing
- Shop Management
- Testing and Measuring
- Tube and Pipe Fabrication
- Tube and Pipe Production
- Waterjet Cutting
Industry Directory
Webcasts
Podcasts
FAB 40
Advertise
Subscribe
Account Login
Search
Die Science: Opportunity knocks
Career options in tool and die
- By Art Hedrick
- February 24, 2017
- Article
- Bending and Forming
When you think of the tool and die industry, you often think first of tool- and diemakers—people grinding die sections, reading engineered drawings, assembling dies, and trying out tooling.
Although tool- and diemakers are critical to the diemaking process, many jobs are equally important to the tool and die industry.
Process Engineers
A process engineer determines the steps needed to change a flat sheet of metal into a finished part. Process engineers need to perform this job with a great deal of confidence and accuracy, so they must understand sheet metal behavior and know the amount of time and money it will take to design and build the tooling. They must also be able to view and assess quickly the tolerance requirements of the part to be stamped. Most process engineers have a background in either designing or building dies.
Cost is an important part of the process. If the process engineer adds unnecessary steps, the tooling cost may be excessive, and the company likely will not win the job. However, without enough steps, the die will not perform as intended. A single process error can spell failure. Many process engineers keep a detailed history of parts that were made in the past, showing how much they ended up spending to design, build, and finalize the tooling.
Forming Simulation Engineers
Many tool and die companies specializing in deep drawing and forming use some type of forming simulation computer software. This software allows virtual forming of the part to help eliminate the potential for forming failures such as splits and wrinkles.
Individuals running this advanced software must have not only good computer and solid modeling skills, but a comprehensive understanding of sheet metal properties and behaviors. They also must have a deep knowledge of how drawing and stretching dies operate. These individuals are in great demand, now more than ever.
Die Designers
Die designers are responsible for designing the tool that will execute the forming process. Die designers often also serve as process engineers. They need to understand mechanical motion, material strengths, and tool steel types, and they need to know how to operate CAD software.
Die designers often have a mechanical imagination, which helps them create and design unique methods for metal cutting and forming operations.
Machinists
Machinists cut the die components out of their respective materials to their proper dimensions. They need a comprehensive knowledge of metal cutting speeds and feeds, and they have to know how to locate and secure the tool steel to the machine.
Machinists have to be able to interpret tolerances and to operate and read precision measuring instruments. They must know different types and applications of cutters as well.
Diemakers
Diemakers are responsible for tool assembly and construction. They must try out the die to make sure that it functions properly and consistently produces an acceptable piece part. Depending on the shop, diemakers also might perform some machining and grinding on the die sections. They have to know how to interpret engineered drawing and know how the die works.
The diemaker’s role has changed dramatically in the last 40 years. For instance, the advent of computer numerically controlled technology has eliminated or at least dramatically reduced the amount of layout and drilling for which the diemaker is responsible. Blueprints are antiquated now, having been replaced for the most part with solid-model computerized images. Diemaking has slowly evolved into die assembly, and many individuals with good diemaking skills have moved into engineering or tryout roles.
Production Die Maintenance Technicians
Production die maintenance technicians maintain, repair, and troubleshoot the stamping dies. The troubleshooting alone can be a daunting task, especially in the typically chaotic shop environment.
Die maintenance technicians must know how to grind and shim worn sections, replace springs and other worn components, and resurface galled sections. They often assist in setting up the die as well.
Quality Control Technicians
Quality control technicians measure and monitor the product being stamped in the dies, and they often inspect parts for surface defects. They must understand geometric dimensioning and tolerancing and be able to interpret engineered drawings. They also have to be able to read and calibrate precision measuring instruments.
These technicians have to understand the Cartesian (rectangular) coordinate system, as well as statistics and bell curves. They also have to be able to program and run a CMM manually.
Regardless of the job one chooses in the stamping industry, one thing is clear: It is a professional career path to be proud of.
About the Author
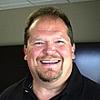
Art Hedrick
10855 Simpson Drive West Private
Greenville, MI 48838
616-894-6855
Related Companies
subscribe now
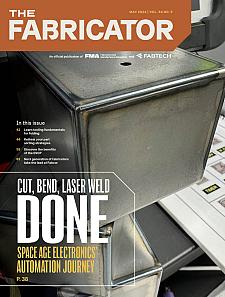
The Fabricator is North America's leading magazine for the metal forming and fabricating industry. The magazine delivers the news, technical articles, and case histories that enable fabricators to do their jobs more efficiently. The Fabricator has served the industry since 1970.
start your free subscription- Stay connected from anywhere
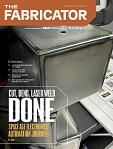
Easily access valuable industry resources now with full access to the digital edition of The Fabricator.
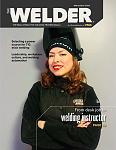
Easily access valuable industry resources now with full access to the digital edition of The Welder.
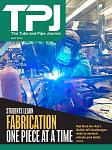
Easily access valuable industry resources now with full access to the digital edition of The Tube and Pipe Journal.
- Podcasting
- Podcast:
- The Fabricator Podcast
- Published:
- 04/16/2024
- Running Time:
- 63:29
In this episode of The Fabricator Podcast, Caleb Chamberlain, co-founder and CEO of OSH Cut, discusses his company’s...
- Industry Events
16th Annual Safety Conference
- April 30 - May 1, 2024
- Elgin,
Pipe and Tube Conference
- May 21 - 22, 2024
- Omaha, NE
World-Class Roll Forming Workshop
- June 5 - 6, 2024
- Louisville, KY
Advanced Laser Application Workshop
- June 25 - 27, 2024
- Novi, MI