Contributing Writer
- FMA
- The Fabricator
- FABTECH
- Canadian Metalworking
Categories
- Additive Manufacturing
- Aluminum Welding
- Arc Welding
- Assembly and Joining
- Automation and Robotics
- Bending and Forming
- Consumables
- Cutting and Weld Prep
- Electric Vehicles
- En Español
- Finishing
- Hydroforming
- Laser Cutting
- Laser Welding
- Machining
- Manufacturing Software
- Materials Handling
- Metals/Materials
- Oxyfuel Cutting
- Plasma Cutting
- Power Tools
- Punching and Other Holemaking
- Roll Forming
- Safety
- Sawing
- Shearing
- Shop Management
- Testing and Measuring
- Tube and Pipe Fabrication
- Tube and Pipe Production
- Waterjet Cutting
Industry Directory
Webcasts
Podcasts
FAB 40
Advertise
Subscribe
Account Login
Search
Die Science: Reducing lead-times and tooling cost, Part I
- By Art Hedrick
- June 22, 2017
- Article
- Bending and Forming
Ideal with many tool and die building shops in western Michigan and surrounding areas. Last year most of them managed to weather the storm and endure the financial hardships that resulted from the drastic downturn in the U.S economy, but they’re still looking for ways to become more competitive in the global marketplace.
One common thread, especially among larger shops, is they spend way too much time engineering parts and not enough time engineering the dies. Unfortunately, they rarely are compensated for those extra engineering services. It’s important to understand the constraints that drive up tooling cost and extend delivery times and to know how to reduce those cost and lead-times.
Die Quoting Reality
A lot of demands are placed on quoting engineers. For instance, I recently received a 3-D part file via e-mail. Shortly afterward, I received a phone call from the person who wanted this part to be made using the metal stamping process. He had the following questions for me:
- Can it be made as designed?
- How much will the die cost?
- How many operations will be needed?
- How fast will it run?
- Can I use my press to make the part?
- How long will it take to get the tooling made?
- Can you get me a tooling quote by this afternoon?
Here is the part data he provided:
- Part to be made on a 200-ton gap-frame press
- Part to be made out of “some kind of formable steel”
- Metal thickness and volume to be determined
He didn’t indicate a part function , because the design was proprietary, and he gave no die building standards, no tolerancing, and no volume.
Welcome to a typical day in the life of a process engineer. Trying to establish a realistic quote for this tool is a crapshoot.
To quote a tool like this, you need more data from the product designer. If you can’t get that information, one option is to quote the tool using data you think is suited for product design. Include with your quote several disclaimers starting that if the part is not made out of metal X and a thickness of Y, the quote is null and void.
The Question of Part Design
Keep in mind that even if all the necessary part and press data is provided, somebody must take the time to sit down and come up with steps necessary to make this part. Depending on the part’s geometry, this may be a simple o ra very time-consuming process. Keeping in mind that many request for quotes are nothing more than an attempt to get a free process for making the part.
The big question is: Are you a die builder, or are you a free part engineer/designer? I’m sure I’ve opened up a big can of worms with this question. Put simply, the part designer i step person who is compensated to design or redesign the part. This might be the original product designer, or it might be the die building shop, Problem begin when the die shop assumes that the product designer has engineered the products so that it can be made in the allotted number of operations from the material that it is designed for.
Prototype Parts
One common assumption is that if a prototype shop made the part successfully, it can be made using hard tooling. Remember that the main function of a prototype shop is to produce only a few parts, and the shop is not limited in the number of operations or methods it can use to produce the parts. Many prototype parts are formed after heating the metal or using many more steps that can be used in the production tooling.
Unless the prototype shop has followed the actual intended production process, the part itself cannot be used as evidence that it can be made in the hard tooling. However, a prototype shop that adheres to the intended production process can prove to be a valuable processing asset when it comes time to build the production tooling.A Typical Costly Struggle in 20 Steps
How doe tooling design and production get so expensive? Consider a common series of events.
- The product designer designs a deep-formed part out of advanced high-strength steel (AHSS) ,
- This part may or may not be prototyped.
- The part design get tested and approved to be tooled.
- Many die shops quote the tooling, and one is awarded the job.
- The chosen shop’s process engineer determines the best way to form the part, estimating i will require eight operations.
- The costumer says that because of press capacity, only six operations will be allowed.
- After several days or weeks of re-engineering the process, the die building shop comes up with a process to make the part in six operations, but the product design will need to be alternated. The request is submitted to increase four part radii from 3mm to 10mm.
- After reviewing the request, the product designer seeks approval from his superior to make the part design changes.
- The part changes are rejected because the part might have to be re-prototyped and tested.
- The customer encourages the die shop to make further process changes to see if there is any other way to make this part in six stations.
- The die shop spends several more weeks attempting to produce the part in six stations, and several more conducting numerous forming simulations iterations unsuccessfully.
- The customer tells the die shop how the part can be made in six stations.
- Not wanting to destroy its relationship with the customer, the die shop spends many more days trying to make the part using the customer-driven process.
- After excessive engineering time has elapsed, the customer is finally convinced that the part cannot be made as designed in six stations. Sixty-five percent of the die design and building time has been spent in engineering.
- The customer redesigns the part with the larger radii, as previously recommended.
- The shop designs the tooling and then orders the die-building materials.
- The shop machines the components and details, and builds and assembles the tooling.
- The customer sends tryout stock to the die shop.
- The shop spends many hours fitting and spotting the forming dies.
- The shop finally makes an acceptable part, six weeks late and way over budget.
Avoiding This Scenario
So what is the root cause of this problem? Did the die shop fail? Was it a poor product design? Was the tooling quoted too low? Was the process engineer inexperienced?
While any one of these may be a factor, none is the root cause of the problem. Instead, 99.9 percent of all problems are the result of one or combination of serval root causes: ignorance, lack of effective communication, and lack of planning.
Until next time… Best of luck!
About the Author
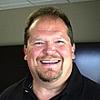
Art Hedrick
10855 Simpson Drive West Private
Greenville, MI 48838
616-894-6855
Related Companies
subscribe now
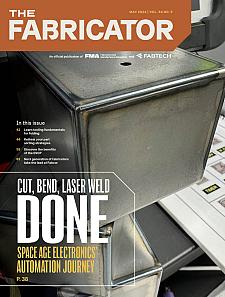
The Fabricator is North America's leading magazine for the metal forming and fabricating industry. The magazine delivers the news, technical articles, and case histories that enable fabricators to do their jobs more efficiently. The Fabricator has served the industry since 1970.
start your free subscription- Stay connected from anywhere
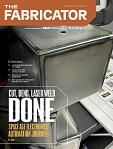
Easily access valuable industry resources now with full access to the digital edition of The Fabricator.
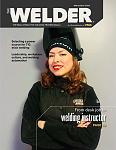
Easily access valuable industry resources now with full access to the digital edition of The Welder.
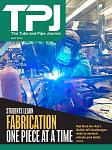
Easily access valuable industry resources now with full access to the digital edition of The Tube and Pipe Journal.
- Podcasting
- Podcast:
- The Fabricator Podcast
- Published:
- 04/16/2024
- Running Time:
- 63:29
In this episode of The Fabricator Podcast, Caleb Chamberlain, co-founder and CEO of OSH Cut, discusses his company’s...
- Industry Events
16th Annual Safety Conference
- April 30 - May 1, 2024
- Elgin,
Pipe and Tube Conference
- May 21 - 22, 2024
- Omaha, NE
World-Class Roll Forming Workshop
- June 5 - 6, 2024
- Louisville, KY
Advanced Laser Application Workshop
- June 25 - 27, 2024
- Novi, MI