Contributing Writer
- FMA
- The Fabricator
- FABTECH
- Canadian Metalworking
Categories
- Additive Manufacturing
- Aluminum Welding
- Arc Welding
- Assembly and Joining
- Automation and Robotics
- Bending and Forming
- Consumables
- Cutting and Weld Prep
- Electric Vehicles
- En Español
- Finishing
- Hydroforming
- Laser Cutting
- Laser Welding
- Machining
- Manufacturing Software
- Materials Handling
- Metals/Materials
- Oxyfuel Cutting
- Plasma Cutting
- Power Tools
- Punching and Other Holemaking
- Roll Forming
- Safety
- Sawing
- Shearing
- Shop Management
- Testing and Measuring
- Tube and Pipe Fabrication
- Tube and Pipe Production
- Waterjet Cutting
Industry Directory
Webcasts
Podcasts
FAB 40
Advertise
Subscribe
Account Login
Search
Die Science: The influence of product design
- By Art Hedrick
- February 24, 2017
- Article
- Bending and Forming
I find it somewhat disheartening how often product designers fail to see the downstream effect of the decisions they make regarding the design of a stamped product. Poor tolerencing and part feature decisions cost the stampers and die builders any profit they may have realized.
While I don’t want to degrade or blame the product designers, I do want to show how their decisions can affect the cost, difficulty, and effectiveness of the die building and stamping process.
“In the Beginning …”
Sound familiar? Everything begins with an idea … in this case, an idea to make something out of sheet metal using the stamping process.
We assume that anyone designing a stamped part would have a comprehensive understanding of all of the variables that affect the stamping and die building processes. Unfortunately, that’s not always the case. In my career I have met numerous product designers who have never even seen a die or watched a press go up and down, yet nearly every decision they make sets the foundation for the entire die building and production stamping process.
The stage has been set. The basic plan has already been drawn up.
Part designers reading this might be thinking, “What does he mean by that? I haven’t made any plans about how they will make this part.” Read on.
I’m Not Responsible for That!
I chuckle when product designers say they just design parts. They say they’re not responsible for deciding how fast the parts can be run, how many stations they’ll take, which press will be used, and how much the tooling will cost.
My response is that in a basic sense, they have already made those decisions. Every dimension, tolerance, feature, and shape they incorporate into a design has inadvertently made a basic decision about the following.
Press Type, Bed Size, Speed, and Tonnage. Did the designer not choose the metal type and thickness from which to make the part? It will take a certain amount of force to cut and form that material. As a result, it will require a press with a sufficient amount of tonnage. The material’s mechanical properties affect the number of stations required, which affects the bed size. The type of metal also affects the speed at which the part can be formed.
Number of Stations. Although part designers might not determine the geometry of the stations, by designing certain features into a part, they determine the number of stations required. A part designed with a tall, small tubular feature in the center may require numerous drawing reduction stations to achieve that feature. If the designer specifies a small amount of form tolerance, the part might need restriking one or several times to achieve the desired tolerance.
Type of Tool Steel. Part designers reading this might now be thinking, “OK, Art, you’re pushing it. I certainly don’t choose the tool steel that will be used to make the die!”
Sorry to disappoint them, but although designers might not choose the exact type of tool steel, they do choose the type of metal the part will be made of. Certain metals such as 300 series stainless steel and AHSS types such as DP 790 and martensitic grades are very hard and abrasive. Some require the use of solid-carbide tools to cut and form them. Others may require CPM grades of tool steel. Some tool steel grades may require a special PVD or CVD coating to prevent excessive wear. All of these are chosen based on the metal the part is made from and the forming severity of the features to be formed. And both of those are decided by the product designer.
Type of Lubricant. “You’ve got to be kidding me! I didn’t choose the lubricant!” say the part designers. Perhaps not the specific brand, but they did predetermine that certain types of lubricants be used.
For example, if a deep-drawn part is specified with 0.080-in. HSS 70 minimum yield, we can expect a great deal of friction to be created. If the friction is too great, the tool steel will gall up. To prevent galling, a lubricant with certain heat-activated additives such as sulfur and chlorine must be used. And many of the lubricants will need to be washed off after stamping - - another added cost for which the part designer is responsible.
Amount of Material. Deep-drawn parts require more material and generate more scrap than other types of parts. Certain part features may cause the metal to gather or wrinkle during forming, in which case stretch forming or drawing must be used, and these operations use more material.
Tooling Cost. Difficult features require more stations. Tighter tolerances require greater precision. Both of these add to tooling and die cost. Every radius, every bump, every bend, every hole, and every feature added to the part has a cost associated with it.
You Set the Stage
Please understand that in no way am I attempting to “pass the buck” onto product designers. My goal is to demonstrate the importance of understanding how decisions made early in the process can and will affect the final part and tooling cost.
If you’re a product designer, don’t take your responsibility lightly. You set the stage for the entire process. Go into the shop and observe dies and presses every chance you get. Ask questions. It is only through a comprehensive understanding of the entire system that we can improve.
About the Author
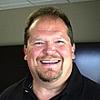
Art Hedrick
10855 Simpson Drive West Private
Greenville, MI 48838
616-894-6855
Related Companies
subscribe now
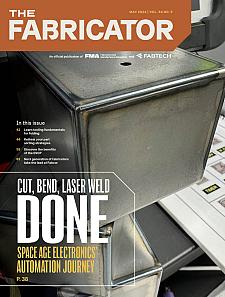
The Fabricator is North America's leading magazine for the metal forming and fabricating industry. The magazine delivers the news, technical articles, and case histories that enable fabricators to do their jobs more efficiently. The Fabricator has served the industry since 1970.
start your free subscription- Stay connected from anywhere
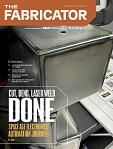
Easily access valuable industry resources now with full access to the digital edition of The Fabricator.
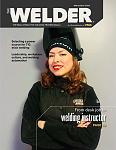
Easily access valuable industry resources now with full access to the digital edition of The Welder.
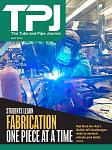
Easily access valuable industry resources now with full access to the digital edition of The Tube and Pipe Journal.
- Podcasting
- Podcast:
- The Fabricator Podcast
- Published:
- 04/16/2024
- Running Time:
- 63:29
In this episode of The Fabricator Podcast, Caleb Chamberlain, co-founder and CEO of OSH Cut, discusses his company’s...
- Trending Articles
Capturing, recording equipment inspection data for FMEA
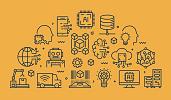
Tips for creating sheet metal tubes with perforations
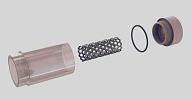
Are two heads better than one in fiber laser cutting?
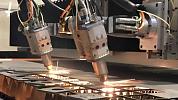
Supporting the metal fabricating industry through FMA
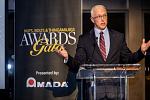
Omco Solar opens second Alabama manufacturing facility
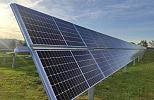
- Industry Events
16th Annual Safety Conference
- April 30 - May 1, 2024
- Elgin,
Pipe and Tube Conference
- May 21 - 22, 2024
- Omaha, NE
World-Class Roll Forming Workshop
- June 5 - 6, 2024
- Louisville, KY
Advanced Laser Application Workshop
- June 25 - 27, 2024
- Novi, MI