Contributing Writer
- FMA
- The Fabricator
- FABTECH
- Canadian Metalworking
Categories
- Additive Manufacturing
- Aluminum Welding
- Arc Welding
- Assembly and Joining
- Automation and Robotics
- Bending and Forming
- Consumables
- Cutting and Weld Prep
- Electric Vehicles
- En Español
- Finishing
- Hydroforming
- Laser Cutting
- Laser Welding
- Machining
- Manufacturing Software
- Materials Handling
- Metals/Materials
- Oxyfuel Cutting
- Plasma Cutting
- Power Tools
- Punching and Other Holemaking
- Roll Forming
- Safety
- Sawing
- Shearing
- Shop Management
- Testing and Measuring
- Tube and Pipe Fabrication
- Tube and Pipe Production
- Waterjet Cutting
Industry Directory
Webcasts
Podcasts
FAB 40
Advertise
Subscribe
Account Login
Search
Die Science: Understanding interactivity for difficult stampings
- By Art Hedrick
- February 28, 2017
- Article
- Bending and Forming
It’s no secret that the quality of a stamped part is influenced by numerous variables, including the mechanical ability of the material being stamped, the condition of the tooling and the press, the number of process steps being used, and the geometry of the dies. To truly solve a stamping-related problem, you must clearly define and correct the root cause. That might sound simple, but given the number of variables, it can be frustrating and time-consuming.
To find and solve the root cause of a stamping problem, you need to understand fully how metal behaves when subjected to forming and cutting operations in the die and the interactivity that takes place during the stamping process.
Cause-and-Effect Analysis
In a stamping operation, many types of failures can occur. To find the root cause of a stamping-related problem, you must first define the failure clearly. Many parts, especially those with features such as compression flanges, have cracking failures. However, if you don’t clearly understand the failure mode and behavior of the metal, you might define these failures as splits rather than cracking.
A split is a tensile failure resulting from too much localized stretching. A crack is a compressive failure resulting from too much localized compression and strain hardening of the metal. Although many of the same variables contribute to both of these failures, they are distinctly different. Addressing a split when the true failure is a crack can lead to more problems.
After defining the failure accurately, you must clearly define all of the potential variables associated with the failure. Only when you are aware of the variables can you define scientifically the root cause of the problem. You can lay out this cause-and-effect analysis visually using a fishbone diagram to define the interactivity problems that occur.
Example: Excessive Part Burring
Let’s say that you are having problems with excessive part burrs, and you’ve noticed that your dies need frequent sharpening and your tooling has required an excessive number of repairs. Not only do these problems affect profits, but if a burred part fails to function correctly, it could cost you a valued customer. You want to take care of this burring problem once and for all.
Define the Variables. Many variables are associated with metal cutting burrs:
•Metal type—Your decisions about the die geometry and the troubleshooting process will depend on the type of metal you are working with and its behavior. Characteristics such as thickness, tensile strength, and yield strength are important.
•Die conditions—The edge condition of the punches and dies, the tool steel they are made from, and their hardness and toughness all are important. The rigidity of the cutting sections, the die guidance accuracy, and the cutting clearance between the punches and dies also make a difference.
•Press conditions—The press can contribute to die and cutting failures. Be sure you know and understand the deflection rate and ram-to-bolster parallelism.
•Lubricant—The type of lubri-cant and application method will affect both punch life and the amount of excessive burrs.
Find the Root Cause. Could any single one of these variables be the root cause of all three problems (excessive burring, frequent sharpening, and excessive repairs)? If you understand sheet metal physics and the metal cutting process as a whole, you can answer that question with aconfident “Yes!”
In this case, the likely root cause is insufficient cutting clearance. To combat this problem, you need to increase the force required to cut the metal. Very quickly, the interactivity of problems in the die becomes highly evident, as increased cutting force leads to:
- More press deflection, which leads to poor alignment between cutting components, which leads to larger cutting burrs. Greater deflection also leads to more punch breakage, which leads to more die repair.
- More wear on punches and dies, which leads to a greater load on the punches, which leads to more punch edge breakdown, which leads to larger cutting burrs.
- Greater punch stripping force requirements, which lead to a greater probability of a stripper pad sticking, which leads to die repair. Increased punch stripping force also leads to greater wear and breakdown of the sides of the punches, which lead to more friction during stripping because of the erosion of the punch surface, which leads to greater friction, which leads to pad sticking, which leads to more die repair.
Increasing the cutting clearance is still your best solution. You just need to keep in mind that doing so can result in other interactive problems that you’ll need to address.
Just One Variable?
Can every stamping die problem be traced back to a single variable? No. In fact, most are caused by more than one variable. The key is to understand how changing a single factor, such as the cutting clearance, can influence many other problems.
About the Author
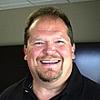
Art Hedrick
10855 Simpson Drive West Private
Greenville, MI 48838
616-894-6855
Related Companies
subscribe now
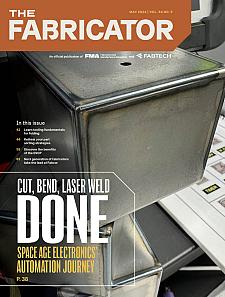
The Fabricator is North America's leading magazine for the metal forming and fabricating industry. The magazine delivers the news, technical articles, and case histories that enable fabricators to do their jobs more efficiently. The Fabricator has served the industry since 1970.
start your free subscription- Stay connected from anywhere
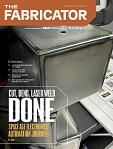
Easily access valuable industry resources now with full access to the digital edition of The Fabricator.
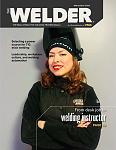
Easily access valuable industry resources now with full access to the digital edition of The Welder.
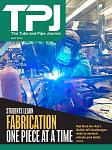
Easily access valuable industry resources now with full access to the digital edition of The Tube and Pipe Journal.
- Podcasting
- Podcast:
- The Fabricator Podcast
- Published:
- 04/16/2024
- Running Time:
- 63:29
In this episode of The Fabricator Podcast, Caleb Chamberlain, co-founder and CEO of OSH Cut, discusses his company’s...
- Industry Events
16th Annual Safety Conference
- April 30 - May 1, 2024
- Elgin,
Pipe and Tube Conference
- May 21 - 22, 2024
- Omaha, NE
World-Class Roll Forming Workshop
- June 5 - 6, 2024
- Louisville, KY
Advanced Laser Application Workshop
- June 25 - 27, 2024
- Novi, MI