Graduate Research Associate - Center for Precision Forming
- FMA
- The Fabricator
- FABTECH
- Canadian Metalworking
Categories
- Additive Manufacturing
- Aluminum Welding
- Arc Welding
- Assembly and Joining
- Automation and Robotics
- Bending and Forming
- Consumables
- Cutting and Weld Prep
- Electric Vehicles
- En Español
- Finishing
- Hydroforming
- Laser Cutting
- Laser Welding
- Machining
- Manufacturing Software
- Materials Handling
- Metals/Materials
- Oxyfuel Cutting
- Plasma Cutting
- Power Tools
- Punching and Other Holemaking
- Roll Forming
- Safety
- Sawing
- Shearing
- Shop Management
- Testing and Measuring
- Tube and Pipe Fabrication
- Tube and Pipe Production
- Waterjet Cutting
Industry Directory
Webcasts
Podcasts
FAB 40
Advertise
Subscribe
Account Login
Search
R&D Update: Lightweighting in the automotive industry using sheet metal forming, Part 1
Design considerations and materials
- By Ali Fallahiarezoodar and Taylan Altan, Ph.D.
- January 7, 2016
- Article
- Bending and Forming
Achieving weight reduction in metal parts for the automotive industry requires forming of lightweight and high-strength materials at room temperature and at elevated temperatures. This requirement presents challenges in material characterization and formability, lubrication, die materials and design, process simulation and prediction of springback, press design and operation, and quality control.
As a result, the stamping industry is faced with inconsistency of incoming material properties, fracture during forming, higher contact pressure and temperature rise at the sheet/die interface, higher die wear leading to reduced tool life, higher forming load/press capacity, and large springback leading to dimensional inaccuracy in the formed part.
Achieving light weight requires consideration of design, material selection, new processes, new lubricants, and new presses and tooling. OEMs must study several important factors (see Figure 1).
Research Into Weight Reduction in Stamping
Recent research studies at the Center for Precision Forming (CPF) at The Ohio State University have focused on achieving weight reduction in stamping. Studies have included:
- Forming of advanced high-strength steels (AHSS) (DP600, DP980, CP800, TRIP1180, DP1200) using servo-driven presses with CNC hydraulic cushions.
- Hot stamping of manganese-boron steels.
- Cold and warm forming of aluminum alloys (5xxx, 6xxx, and 7xxx series).
- Improvements in the evaluation of material properties (true stress/strain or flow stress curve) and the use of new lubricants.
Some of the new AHSS alloys (TRIP, TWIP) may replace selected hot-stamping applications. Companies around the world attempt to expand the application of very high-strength dual-phase steels. For example, DP980 and DP1200 now are used routinely in stamping.
Selected Nissan models already have B-pillars formed from DP1200 steel. In Japan, development work is in progress for forming 1,400-MPa material for structural components. As expected, low formability, springback, and tool/press deflections are issues to be considered in obtaining quality parts.
The most commonly used aluminum alloys in automotive industry are the 5xxx and 6xxx series, which are typically used to manufacture closures for doors, hoods, and trunk lids. The high-strength 7xxx alloys must be formed at elevated temperatures, and they are being investigated for cost-effective application. Figure 2 illustrates the virtual comparison of a B-pillar formed from hot-stamped boron steel and from Al 7075-T6. Results showed the same crash performance for both materials, although the aluminum part cost 40 percent less. Figure 3 illustrates a production part made from 7xxx aluminum—a door side crash beam used in the BMW i8.
Formability of Materials
The flow stress curve (true stress versus true strain) is essential for conducting finite element simulations of sheet forming operations. The viscous pressure bulge (VPB) and tensile tests are used for this purpose.
The VPB test also can be used to estimate the formability of the sheet material from when the test is conducted until the sample has fractured (see Figure 4). The height of the bulge at fracture is an indication of the material formability, even though the deformation is equibiaxial and linear; in stamping, the strain path usually is nonlinear.
Prediction of Fracture
The usual method of predicting fracture is to predict the strains in the deformed part and compare them with the calculated maximum major and minor strains given in the forming limit curve (FLC) (see Figure 5). Thus, it was possible to change the forming process and the parameters (blank shape, draw bead size and shape, blank holder force, and thickness of spacers of distance blocks located between the die and blank holder or binder).
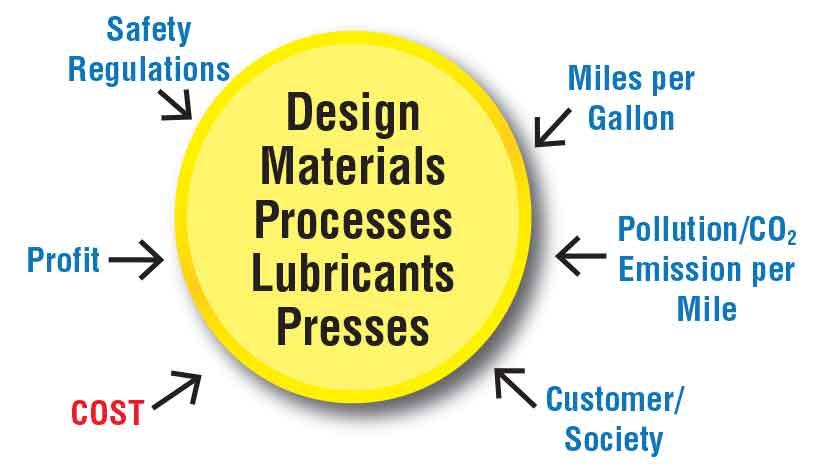
Figure 1
OEMs must consider several factors when trying to achieve light
weight in automotive design and manufacturing.
As seen in Figure 5, the determination of the FLC required a large number of samples and considerable time for experiments to evaluate one sheet material and thickness. Furthermore, variations in edge quality of the samples and interface friction between the punch and the samples used in the tests also affected the measurement of minor and major strains.
To save time and money, we can determine the FLC approximately by using three fracture points: biaxial stretching, plane strain deformation (minor strain is nearly zero), and the tensile test. The FLC determined by the simplified three-point method was in good agreement with the FLC determined using the conventional test technique for DP600 (0.96 mm thick) (see Figure 6).
The CPF is still evaluating this method for its practical validity. If the results are positive, then the three-point technique has the potential to save considerable time and costs in determining FLCs for various materials and thicknesses.
Resource
D.V. Nieuwerburgh, “Aluminum sheet developments for current and future BIW concepts,” August 2011, Aleris Europe.
About the Authors
Ali Fallahiarezoodar
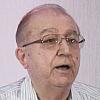
Taylan Altan, Ph.D.
Professor Emeritus and Director - Center for Precision Forming
Related Companies
subscribe now
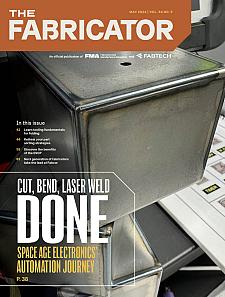
The Fabricator is North America's leading magazine for the metal forming and fabricating industry. The magazine delivers the news, technical articles, and case histories that enable fabricators to do their jobs more efficiently. The Fabricator has served the industry since 1970.
start your free subscription- Stay connected from anywhere
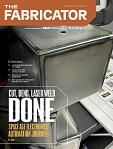
Easily access valuable industry resources now with full access to the digital edition of The Fabricator.
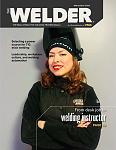
Easily access valuable industry resources now with full access to the digital edition of The Welder.
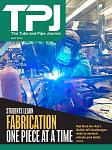
Easily access valuable industry resources now with full access to the digital edition of The Tube and Pipe Journal.
- Podcasting
- Podcast:
- The Fabricator Podcast
- Published:
- 04/16/2024
- Running Time:
- 63:29
In this episode of The Fabricator Podcast, Caleb Chamberlain, co-founder and CEO of OSH Cut, discusses his company’s...
- Trending Articles
Capturing, recording equipment inspection data for FMEA
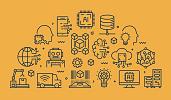
Tips for creating sheet metal tubes with perforations
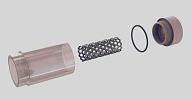
Are two heads better than one in fiber laser cutting?
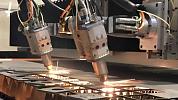
Supporting the metal fabricating industry through FMA
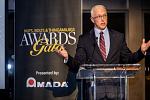
Omco Solar opens second Alabama manufacturing facility
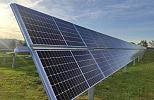
- Industry Events
16th Annual Safety Conference
- April 30 - May 1, 2024
- Elgin,
Pipe and Tube Conference
- May 21 - 22, 2024
- Omaha, NE
World-Class Roll Forming Workshop
- June 5 - 6, 2024
- Louisville, KY
Advanced Laser Application Workshop
- June 25 - 27, 2024
- Novi, MI