Contributing editor
- FMA
- The Fabricator
- FABTECH
- Canadian Metalworking
Categories
- Additive Manufacturing
- Aluminum Welding
- Arc Welding
- Assembly and Joining
- Automation and Robotics
- Bending and Forming
- Consumables
- Cutting and Weld Prep
- Electric Vehicles
- En Español
- Finishing
- Hydroforming
- Laser Cutting
- Laser Welding
- Machining
- Manufacturing Software
- Materials Handling
- Metals/Materials
- Oxyfuel Cutting
- Plasma Cutting
- Power Tools
- Punching and Other Holemaking
- Roll Forming
- Safety
- Sawing
- Shearing
- Shop Management
- Testing and Measuring
- Tube and Pipe Fabrication
- Tube and Pipe Production
- Waterjet Cutting
Industry Directory
Webcasts
Podcasts
FAB 40
Advertise
Subscribe
Account Login
Search
Tier stamper improves mechanical press productivity with transfer retrofit
- By Kate Bachman
- September 10, 2010
- Article
- Bending and Forming
Situation
A Midwestern manufacturer sought to improve productivity on its nearly 10-year-old Verson transfer press. Although the press was in good condition, the original ETF transfer, which had endured 28 million press hits, was causing considerable maintenance costs and lost production.
Because of the transfer’s age, unexpected maintenance and repair had become more frequent, and components were sometimes difficult to replace. In addition, part mislocations in the die were becoming an issue, causing additional downtime.
The management team investigated investing in a transfer retrofit and modernization to improve the press’s productivity in terms of both throughput and uptime within a reasonable payback period.
Resolution
The stamper retrofitted the Verson transfer stamping press with a Schuler Automation AT series triaxis transfer. The transfer system is designed for the stamper’s medium-duty part production. The high-performance direct-drive system is mounted directly to the transfer rails, which improved the output rate because it reduces the system’s reciprocating mass. This provided consistent, precise, and reliable part location in the dies.
A newly developed transfer rail guide, constructed with heavy-duty steel, improves the rigidity of the transfer so it can be operated at high speeds with minimal deflection to maintain consistent quality. This made it especially suitable for production of the company’s small parts and high stroke rates.
The system also has a special transfer-rail coupling with integrated sensors for rail changeovers.
The system’s compact and flexible mounting design fits within the stamper’s existing system, and its modular design contributed to the timeliness of the installation. The retrofit was completed on time.
Since its completion, the transfer retrofit has resulted in a 10 to 40 percent improvement in cycle times for production of various parts, according to the stamper.
In addition, the press increased productivity through reduced downtime related to fewer emergency repairs and part mislocation during the transfer process.
After operating full production for one month, the operations team projected a payback of the investment of less than 2.5 years. The stamper has installed a second AT3 transfer to retrofit another Verson transfer press.
About the Author
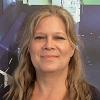
Kate Bachman
815-381-1302
Kate Bachman is a contributing editor for The FABRICATOR editor. Bachman has more than 20 years of experience as a writer and editor in the manufacturing and other industries.
Related Companies
subscribe now
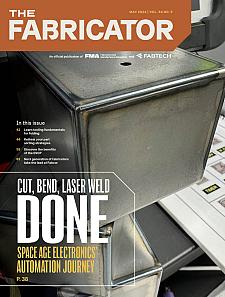
The Fabricator is North America's leading magazine for the metal forming and fabricating industry. The magazine delivers the news, technical articles, and case histories that enable fabricators to do their jobs more efficiently. The Fabricator has served the industry since 1970.
start your free subscription- Stay connected from anywhere
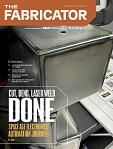
Easily access valuable industry resources now with full access to the digital edition of The Fabricator.
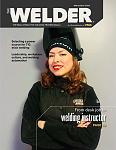
Easily access valuable industry resources now with full access to the digital edition of The Welder.
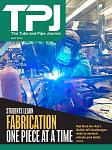
Easily access valuable industry resources now with full access to the digital edition of The Tube and Pipe Journal.
- Podcasting
- Podcast:
- The Fabricator Podcast
- Published:
- 04/16/2024
- Running Time:
- 63:29
In this episode of The Fabricator Podcast, Caleb Chamberlain, co-founder and CEO of OSH Cut, discusses his company’s...
- Industry Events
16th Annual Safety Conference
- April 30 - May 1, 2024
- Elgin,
Pipe and Tube Conference
- May 21 - 22, 2024
- Omaha, NE
World-Class Roll Forming Workshop
- June 5 - 6, 2024
- Louisville, KY
Advanced Laser Application Workshop
- June 25 - 27, 2024
- Novi, MI