AWS CWI, CWE, NDE Level III
- FMA
- The Fabricator
- FABTECH
- Canadian Metalworking
Categories
- Additive Manufacturing
- Aluminum Welding
- Arc Welding
- Assembly and Joining
- Automation and Robotics
- Bending and Forming
- Consumables
- Cutting and Weld Prep
- Electric Vehicles
- En Español
- Finishing
- Hydroforming
- Laser Cutting
- Laser Welding
- Machining
- Manufacturing Software
- Materials Handling
- Metals/Materials
- Oxyfuel Cutting
- Plasma Cutting
- Power Tools
- Punching and Other Holemaking
- Roll Forming
- Safety
- Sawing
- Shearing
- Shop Management
- Testing and Measuring
- Tube and Pipe Fabrication
- Tube and Pipe Production
- Waterjet Cutting
Industry Directory
Webcasts
Podcasts
FAB 40
Advertise
Subscribe
Account Login
Search
Upfront welding inspection considerations
- By Professor R. Carlisle "Carl" Smith
- July 7, 2010
- Article
- Testing and Measuring
Welding inspection is not something to be taken lightly. Lives can depend on the accuracy of the inspection. Failed welds that cause the loss of life or property make the news and technical journals. These failures sometimes are blamed on the welding inspector. If the inspector had done his job properly, the harmful event could have been avoided. In some cases this claim is justifiable; inspectors make mistakes just like any other person in the fabrication chain. However, an inspector cannot inspect quality into the product. The quality of a weldment must be established at the very beginning of the project and followed through to the end. If any step in the job is not established and carried out with quality as the top priority, the possibility of failure exists.
In years past, poor welds caused many more catastrophic failures than occur today. Boilers exploded, ships sank, buildings and bridges collapsed, and pipelines blew up frequently. These disasters became far less frequent as codes and standards were established.
Which Code or Standard?
The American Society of Mechanical Engineers (ASME) worked diligently to establish rules for fabricating boilers, pressure vessels, and piping. The American Welding Society (AWS) established rules for structural fabrication and erection. The American Petroleum Institute (API) continually is quality and safety for pipelines and related facilities.
One of the first things an inspector must know is which code or standard should be used for the inspection criteria—both the code of construction and the code to qualify the welding procedures and welders. These requirements must be outlined in the job specifications. The inspector should not make assumptions or rely on his judgment to set the standard. If it is not written in the specifications or on the drawings, the inspector should not proceed without clarification.
It must be noted that the ASME Section IX is only for welding procedure and welder qualification. It may not be used as a code of construction. The AWS D1.1 code may be used for welding procedure and welder qualification and as a code of construction. The API 1104 is for welding and nondestructive testing of pipelines and related facilities.
Before any welding begins, the inspector must verify that the welding procedures are in compliance with the applicable code or standard. Sometimes a customer establishes a standard that is not referenced to a particular code. This is often the case with very large companies, such as Siemens and General Electric. In these cases, the customer standard prevails.
Each contractor or company is responsible for establishing welding procedures. No code that I am aware of allows a company to outsource a test for welding procedures. However, prequalified welding procedures are available from the AWS. The user must demonstrate that the company is able to perform to these procedures. Most companies require fabricators to establish and test their own procedures. The API 1104 code does not recognize prequalified procedures. All codes require destructive tests for the qualification of procedures, and each code has different procedure testing requirements (Figure 1).
The welding inspector must verify that the welders are qualified and certified to the proper code or standard. Welder qualification is established by testing. A welder who successfully performs a test and receives a certification document is referred to as a certified welder.
Essential and nonessential variables are listed in each of the codes. Some of the essential variables common to all the codes are position, vertical progression, weld deposit thickness, and others related to the specific process. Nonessential variables do not require requalification, but essential variables do. The inspector may require a welder to perform a demonstration for a reasonable cause, such as multiple failures and poor workmanship.
The inspector must observe the joint design to be sure that the procedures cover the type of weld specified on the drawing. If the procedures and welders are qualified only for welds with backing, then no open-root welds are permitted. If the procedures and welders are qualified for welds without backing, then welds with or without backing can be used. This variable is common to all the codes (Figure 2).
Material Information
Material traceability is an absolute necessity for all jobs. If a failure occurs and liability is involved, proof of material quality can hold the key to the cause of the failure. The inspector can only recommend certain additional tests to ensure that the material is of sufficient quality for the use. I always advise a client to require an ultrasonic examination on any material that is 1 in. thick or thicker.
If a plate has lamellar inclusions, they should be detected and reported before any work is done to the material. Material suppliers are required to replace flawed material, but it is extremely difficult to convince a supplier to pay for any work that was done before flaws were discovered.
The inspector must check the material test report (MTR) to make sure that it meets the code requirements. Usually the ASTM is referenced for AWS work, and the ASME Section II, Parts A and B, are referenced for ASME fabrications. Even when low-carbon materials are being welded, care must be taken to compare the chemical, physical, and mechanical properties to the proper standard. The API piping standard is API 5L.
The inspector may question the material selection, but may not reject the material if it meets the job specifications. The specification for material type is to be determined by the customer (usually the engineering department or an outsourced engineering firm).
Tracking the Job
The inspector should request a shop traveler—a step-by-step guide that begins when the job is designed by engineering and proceeds all the way through packaging and shipping. Used for tracking inspections in process, the guide enables the inspector to establish hold points when necessary. An inspector should sign off on each step of the fabrication. If a part is cut, bent, or rolled incorrectly, the condition must be recorded and held as nonconforming until a decision is made by the customer. The decision may be to rework, use as is, or scrap. This decision is not to be made by the inspector, but the inspector must record the matter and secure it in the permanent job records.
Inspection Tools
Inspectors use tools, such as these recommended and assembled in a kit by AWS (Figure 3). These tools, along with the inspector’s knowledge of codes, standards, materials, and processes, help determine the quality, durability, and safety of welded products and structures.
About the Author
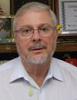
Professor R. Carlisle "Carl" Smith
Weld Inspection & Consulting
PO Box 841
St. Albans, WV 25177
304-549-5606
subscribe now
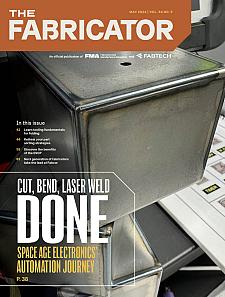
The Fabricator is North America's leading magazine for the metal forming and fabricating industry. The magazine delivers the news, technical articles, and case histories that enable fabricators to do their jobs more efficiently. The Fabricator has served the industry since 1970.
start your free subscription- Stay connected from anywhere
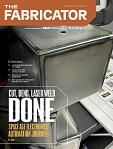
Easily access valuable industry resources now with full access to the digital edition of The Fabricator.
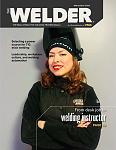
Easily access valuable industry resources now with full access to the digital edition of The Welder.
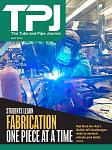
Easily access valuable industry resources now with full access to the digital edition of The Tube and Pipe Journal.
- Podcasting
- Podcast:
- The Fabricator Podcast
- Published:
- 04/16/2024
- Running Time:
- 63:29
In this episode of The Fabricator Podcast, Caleb Chamberlain, co-founder and CEO of OSH Cut, discusses his company’s...
- Industry Events
16th Annual Safety Conference
- April 30 - May 1, 2024
- Elgin,
Pipe and Tube Conference
- May 21 - 22, 2024
- Omaha, NE
World-Class Roll Forming Workshop
- June 5 - 6, 2024
- Louisville, KY
Advanced Laser Application Workshop
- June 25 - 27, 2024
- Novi, MI