Freelance Writer and Intern
- FMA
- The Fabricator
- FABTECH
- Canadian Metalworking
Categories
- Additive Manufacturing
- Aluminum Welding
- Arc Welding
- Assembly and Joining
- Automation and Robotics
- Bending and Forming
- Consumables
- Cutting and Weld Prep
- Electric Vehicles
- En Español
- Finishing
- Hydroforming
- Laser Cutting
- Laser Welding
- Machining
- Manufacturing Software
- Materials Handling
- Metals/Materials
- Oxyfuel Cutting
- Plasma Cutting
- Power Tools
- Punching and Other Holemaking
- Roll Forming
- Safety
- Sawing
- Shearing
- Shop Management
- Testing and Measuring
- Tube and Pipe Fabrication
- Tube and Pipe Production
- Waterjet Cutting
Industry Directory
Webcasts
Podcasts
FAB 40
Advertise
Subscribe
Account Login
Search
HPTR's past, present, and future—Part II
Capabilities and applications for the high-precision tube roller
- By Albert Nerino, Chris Nagele, John Reinhart, and Mark Deaver
- July 11, 2011
- Article
- Tube and Pipe Production
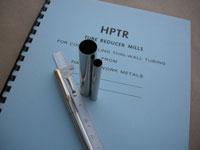
These two tubes show the range of a single HPTR mill, model 8-15. Named for final sizes of tube (in metric), the machine allows a maximum OD between 8 and 15 millimeters, while still providing great reductions in wall thickness. The brochure in the background was the original specification issued by Patent Management Inc. Both tube samples and the brochure were handed out to U.S. manufacturers to illustrate the capabilities of the new machine, which was developed in Russia during the Cold War.
Editor's Note: This article is the second of a two-part series. Part I examined the development, design, and functions of the high-precision tube roller (HPTR). Part II discusses the HPTR’s current role and modern applications.
At its creation, the high-precision tube rolling (HPTR) mill was unmatched in its ability to reduce the size of small, precise, thin-wall tubing made from exotic metals. The HPTR concept was developed at the dawn of the nuclear power era, for producing nuclear fuel cladding.
While they no longer are widely used for that purpose, HPTR mills still have a place in industry today, producing special tubes for niche applications. Their design makes them unique in their ability to reduce tubes made from difficult-to-form metals without having to resolve tricky lubrication issues. The resulting tubes have tight tolerances and excellent mechanical and textural properties, which are necessary for many medical and aerospace applications. Further-more, their low cost, low maintenance, high efficiency, and high material yield make them well-suited for lean manufacturing.
Effective and Efficient
HPTR mills have been built to turn out tubing as small as 0.156 inch and as large as 4.75 in. Model numbers usually are based on the OD range of the resulting tube measured in millimeters. The most common models are 8-15 (capable of reducing tubes to diameters from 8 to 15 mm), 15-30, 30-60, and 60-120. These aren’t the only models available; larger and smaller machines do exist.
Other than their capacities, most HPTR mills are similar. Even the 60-120, which uses four rolls to handle large tube sizes, is fundamentally the same as three-roll models.
One unique variation of the HPTR is the twin-separator mill, inspired by a machine built at the Argonne National Laboratory. Reports came from the USSR in the mid-1960s of a twin separator equipped with two sets of rolls working in tandem, the idea being that one set would begin tube reduction while the other would finish reduction and calibrate the finished tube. While it's uncertain if the Russians ever completed a working model, it is known that American tube producers did successfully create a functional twin-separator HPTR. It has two clusters of three rolls offset 120 degrees. This mill can use a tapered or curved mandrel, and can make extreme, pilger-like reductions. It also retains the ability to use cylindrical mandrels for heavy wall reductions like other HPTR mills, giving it dual-role flexibility (see Figure 1).
HPTR mills minimize waste by lowering the number of reduction and annealing cycles necessary while at the same time improving material yields dramatically. They can achieve cross-sectional reductions of up to 85 percent on a single pass through the mill and use nearly 100 percent of the original tube by weight. They do not require special precoatings, which reduces the number of additional steps needed per reduction.
HPTR mills also are capable of producing tubing in special shapes. Among the possibilities are tubes with triangular, square, and hexagonal cross sections, as well as finned tubes.
In addition, because of the mill's minimal machine interference, a single operator can run several without a significant loss in production, freeing workers for other tasks. A typical HPTR installation may include clusters of up to four machines being operated by a single worker, with multiple clusters positioned near each other. Their simplicity and relatively small footprint means they work well in physical arrangements that can minimize distance and improve the material flow of finished tubes exiting the machines. This can provide opportunities for linking quality control and other operations such as cleaning.
Although both pilgers and HPTR mills reduce tubes via compression rather than tension, the complexity of tooling design and manufacturing varies greatly between these machine types. The variable cross-sectional groove of a pilger die requires special expertise and equipment to design and build, as does the matching mandrel. By contrast, the cams, mandrels, and constant cross-sectional grooves of HPTR mill rolls are relatively simple to design and build (see Figure 2). This allows them to be produced on conventional machine tools, which gives HPTR mill owners much more flexibility on sourcing tooling and tweaking tool design.
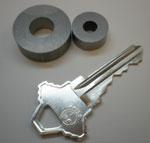
Figure 1: The reduction of a titanium tube (original size at left, reduced size at right) demonstrates a twin-separator HPTR mill’s ability to achieve a pilger-like reduction in a cross section of the tubing. In addition to reductions such as this one, the twin-separator mill is capable of the same heavy-wall, high-Q-factor reductions as a normal HPTR mill.
While HPTR mills are simpler in design and operation than pilger mills, they cannot match the output rates of pilgers. As such, modern, high-speed pilgers have largely taken over the role of HPTR mills in cladding production, as well as other products for which production speed and quantity are important. Furthermore, apart from the twin-separator variant, HPTR mills have a very limited ability to reduce tube diameter. The HPTR mill’s advantage lies in niche products. These include tubes made from high-value material in which yield is critical, as well as tubes with extreme diameter-to-wall-thickness (D/t) ratios, which in some cases can exceed 100 to 1.
Modern Applications
In terms of today’s lean manufacturing objectives, an example of applying the HPTR process to ultrathin tubes used in pressure-sensitive instrumentation illustrates its ability to reduce manufacturing steps and improve net yield of material.
These instruments required stainless steel tubes reduced to less than 0.500 in. OD, as well as an ultrathin wall of less than 1 percent of the OD. Originally, the tubes were reduced by a combination of pilgering and drawing. This method required a total of nine reduction steps. When all drawing was eliminated in favor of rolling on an HPTR mill, the number of reductions dropped to four (see Figure 3). As a result, the total number of steps—including annealing, coating, cropping, and material handling—dropped from 227 to 55, almost a 76 percent reduction. The new process also increased material yield by 110 percent and improved the mechanical qualities of the resulting tube.
Today the tubes made by HPTR mills are used in a variety of end use products. EZTM, a Russian company and manufacturer of HPTR mills, mentions “space and aircraft engineering, shipbuilding, petrochemical and chemical industries, and other sectors of machinery building” as fields that commonly use tubes from its mills. They also are used for some medical applications and nuclear instrumentation, as well as their original purpose, nuclear fuel cladding.
About the Authors
Albert Nerino
3900 Germantown Pike
Collegeville, PA 19426
610-489-5296
Chris Nagele
Manufacturing Engineer
3900 Germantown Pike
Collegeville, PA 19426
610-489-5296
John Reinhart
Manager of Product Development
3900 Germantown Pike
Collegeville, PA 19426
610-489-5296
Mark Deaver
Mechanical Engineer
3900 Germantown Pike
Collegeville, PA 19426
610-489-5296
About the Publication
Related Companies
subscribe now
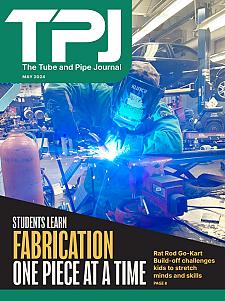
The Tube and Pipe Journal became the first magazine dedicated to serving the metal tube and pipe industry in 1990. Today, it remains the only North American publication devoted to this industry, and it has become the most trusted source of information for tube and pipe professionals.
start your free subscription- Stay connected from anywhere
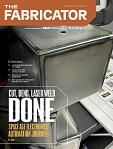
Easily access valuable industry resources now with full access to the digital edition of The Fabricator.
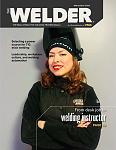
Easily access valuable industry resources now with full access to the digital edition of The Welder.
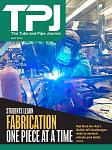
Easily access valuable industry resources now with full access to the digital edition of The Tube and Pipe Journal.
- Podcasting
- Podcast:
- The Fabricator Podcast
- Published:
- 04/16/2024
- Running Time:
- 63:29
In this episode of The Fabricator Podcast, Caleb Chamberlain, co-founder and CEO of OSH Cut, discusses his company’s...
- Trending Articles
Zekelman Industries to invest $120 million in Arkansas expansion
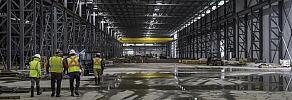
3D laser tube cutting system available in 3, 4, or 5 kW
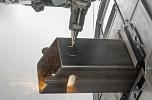
Corrosion-inhibiting coating can be peeled off after use
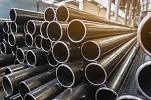
Brushless copper tubing cutter adjusts to ODs up to 2-1/8 in.
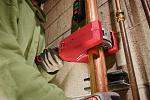
HGG Profiling Equipment names area sales manager
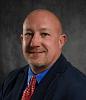
- Industry Events
16th Annual Safety Conference
- April 30 - May 1, 2024
- Elgin,
Pipe and Tube Conference
- May 21 - 22, 2024
- Omaha, NE
World-Class Roll Forming Workshop
- June 5 - 6, 2024
- Louisville, KY
Advanced Laser Application Workshop
- June 25 - 27, 2024
- Novi, MI