President
- FMA
- The Fabricator
- FABTECH
- Canadian Metalworking
Categories
- Additive Manufacturing
- Aluminum Welding
- Arc Welding
- Assembly and Joining
- Automation and Robotics
- Bending and Forming
- Consumables
- Cutting and Weld Prep
- Electric Vehicles
- En Español
- Finishing
- Hydroforming
- Laser Cutting
- Laser Welding
- Machining
- Manufacturing Software
- Materials Handling
- Metals/Materials
- Oxyfuel Cutting
- Plasma Cutting
- Power Tools
- Punching and Other Holemaking
- Roll Forming
- Safety
- Sawing
- Shearing
- Shop Management
- Testing and Measuring
- Tube and Pipe Fabrication
- Tube and Pipe Production
- Waterjet Cutting
Industry Directory
Webcasts
Podcasts
FAB 40
Advertise
Subscribe
Account Login
Search
Relief ahead in 2006?
The answer is a two-letter word you don't want to hear
- By W.B. "Bud" Graham
- December 13, 2005
- Article
- Tube and Pipe Production
![]() |
As we approach the end of another year, anticipation builds to see what challenges and changes will emerge. Please observe I'm not complaining, but I think we're in for another difficult year.
Our industry continues to shrink in both experienced operating personnel and the number of operating entities. Industry changes and market pressures—plant closings, mergers, acquisitions, consolidations, increasing offshore competition, steel prices, and quality demands—continue and with no letup in sight. This is the future; expect more of it next year. Energy availability, conservation, and cost impact will trump materials as the major determinants of the winners in the profitability game. Expect more fallout from bankruptcy filings as companies duck their pension and benefit expenses to emerge as new entities; happy stockholders and lost talent and experience will go hand in hand.
What do you do? Hanging on and hoping for the best won't make it! We have to be the least-cost producers in tons or feet per labor-hour or all of us will end up working for Wal-Mart. Yes, keep your resume up-to-date and be prepared to bail if your company doesn't get it. Yes, work hard if your company shows loyalty in return, because no company or individual can succeed alone.
Do you know what your competitors are up to? Any company that doesn't tell its employees the real story isn't protecting itself from employee losses—instead, it's blinding the best resources that can help it adapt and grow. Get off the company premises and see what's going on in the industry. Attend every tradeshow you can get to, learn what your competitors are doing, network, and find mentors.
Don't rely on last year's skills to solve next year's problems. Try to learn something new every day. Expect to spend an hour a day honing a new skill. You will become more adept, a better contributor to your own and your company's success. Take advantage of every training avenue available. Seek out state or local funding for training and safety improvements. Local and state governments want you and your company to stay healthy and grow so the tax base will grow, so use these resources to the best of your ability.
Avoid the deadly sins:
- Remember to look upstream when a problem occurs. Wrinkled edges aren't created in the fin passes but are produced by misaligned breakdown passes.
- Don't think you're so hot that you don't have to keep records and use setup procedures. Records, not memory, always give you the fastest changeover.
- Always inspect the tools when they come off the mill. Eroded roll roots predict tool failure only if they are inspected. This is your best chance to avoid a problem on the next setup.
- Anyone can jump through hoops when problems occur. Your future will be secure only if you become a planner rather than a worker bee. Maintenance must be driven by a schedule, not breakdowns. Firefighter mode reduces real production time and reduces profits.
If you're locked into a seven-day-a-week schedule just to keep up with the smaller customer orders, and changing over so frequently you spend more time setting up the mill than running the order, stop! Fire customers that don't accept reasonable order lots. If your scrap rate is high (because of setup losses, poor forming, weld faults, and customer rejections), get help any way you can. Otherwise you're sending money down the tubes and the end is near!
Play to your strengths. If you have a quick-change mill—one that requires less than one hour prime to prime—use it to your advantage. If your equipment is more basic, do everything possible to minimize changeover times (and remember that changeover isn't just a matter of setup, but rather the total time between shutdown of the previous tube to tweaking the mill until the current tube is acceptable). Whatever the changeover time, never intentionally change over unless the cost is absorbed in the next run.
If you think a stretched piano wire is good enough for mill alignment ("We've always done it that way"), you better be running large-diameter, heavy-wall pipe because the error factor for great welds is a misalignment of no more than 5 percent of the minimum wall thickness, pass to pass, along the entire mill line. Shaft shoulders, top to bottom, must be no more than 0.002 inch out of alignment.
The future belongs to the swift, the sure, and the competent. Along with high confidence for our industry, I pray for the new year to include independence in Afghanistan and Iraq and the safe return of our soldiers.
Godspeed and Happy New Year!
About the Author
W.B. "Bud" Graham
P.O. Box 202
Doylestown, OH 44230
330-408-3447
About the Publication
subscribe now
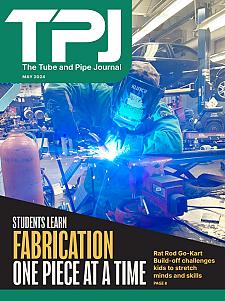
The Tube and Pipe Journal became the first magazine dedicated to serving the metal tube and pipe industry in 1990. Today, it remains the only North American publication devoted to this industry, and it has become the most trusted source of information for tube and pipe professionals.
start your free subscription- Stay connected from anywhere
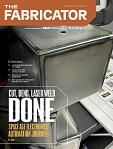
Easily access valuable industry resources now with full access to the digital edition of The Fabricator.
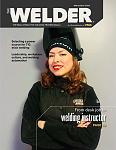
Easily access valuable industry resources now with full access to the digital edition of The Welder.
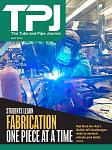
Easily access valuable industry resources now with full access to the digital edition of The Tube and Pipe Journal.
- Podcasting
- Podcast:
- The Fabricator Podcast
- Published:
- 04/16/2024
- Running Time:
- 63:29
In this episode of The Fabricator Podcast, Caleb Chamberlain, co-founder and CEO of OSH Cut, discusses his company’s...
- Trending Articles
Zekelman Industries to invest $120 million in Arkansas expansion
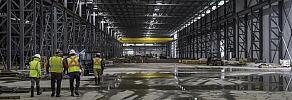
3D laser tube cutting system available in 3, 4, or 5 kW
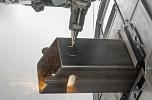
Corrosion-inhibiting coating can be peeled off after use
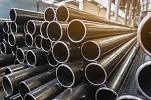
Brushless copper tubing cutter adjusts to ODs up to 2-1/8 in.
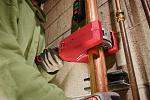
HGG Profiling Equipment names area sales manager
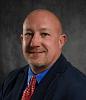
- Industry Events
16th Annual Safety Conference
- April 30 - May 1, 2024
- Elgin,
Pipe and Tube Conference
- May 21 - 22, 2024
- Omaha, NE
World-Class Roll Forming Workshop
- June 5 - 6, 2024
- Louisville, KY
Advanced Laser Application Workshop
- June 25 - 27, 2024
- Novi, MI