Contributing editor
- FMA
- The Fabricator
- FABTECH
- Canadian Metalworking
Categories
- Additive Manufacturing
- Aluminum Welding
- Arc Welding
- Assembly and Joining
- Automation and Robotics
- Bending and Forming
- Consumables
- Cutting and Weld Prep
- Electric Vehicles
- En Español
- Finishing
- Hydroforming
- Laser Cutting
- Laser Welding
- Machining
- Manufacturing Software
- Materials Handling
- Metals/Materials
- Oxyfuel Cutting
- Plasma Cutting
- Power Tools
- Punching and Other Holemaking
- Roll Forming
- Safety
- Sawing
- Shearing
- Shop Management
- Testing and Measuring
- Tube and Pipe Fabrication
- Tube and Pipe Production
- Waterjet Cutting
Industry Directory
Webcasts
Podcasts
FAB 40
Advertise
Subscribe
Account Login
Search
Welding power sources trend toward user utility
What’s new with welding machines? Experts from OEMs ESAB, Miller, and Fronius weigh in
- By Kate Bachman
- July 29, 2021
- Article
- Arc Welding
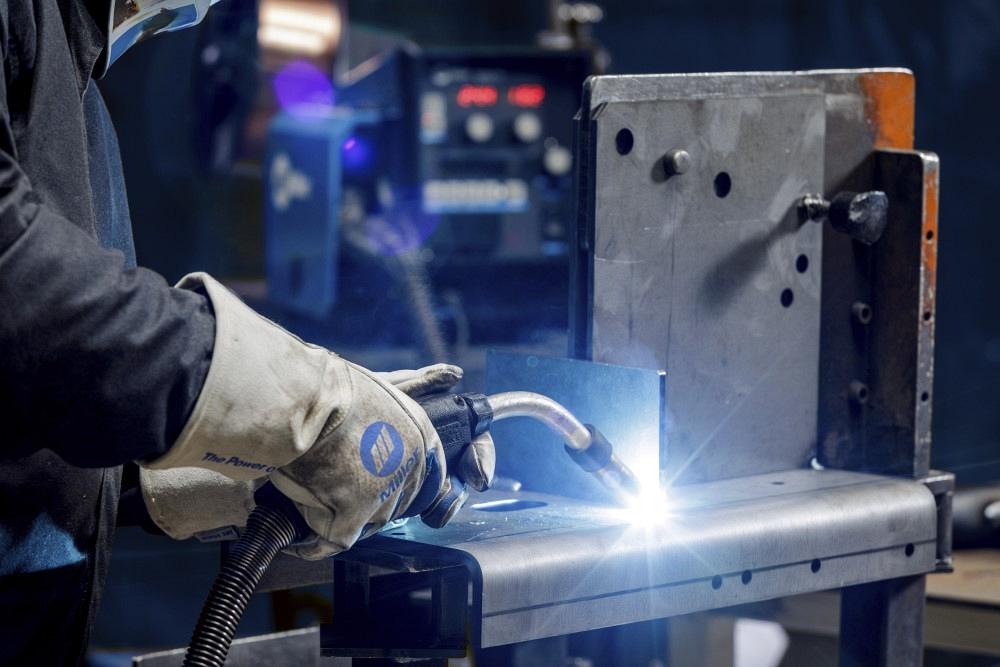
OEMs say that the lack of skilled welders results in productivity bottlenecks, poor quality, rework, and scrap. Weld repeatability, quality assurance, and data recording/traceability are key. Power source OEMs ESAB, Fronius, and Miller Electric relayed how theirs have evolved to help fabricators mitigate that challenge. Images: Miller Electric
Miles of good weld are laid down in the line of work, holding everything together. What’s power got to do with it? Nothing can happen without the power source that sends electric current to the welder’s gun. So, what’s new with welding machines?
We asked power source OEMs ESAB, Miller, and Fronius to provide updates on advances in power sources. ESAB Welding & Cutting Products North America Senior Product Manager Jeff Chittim; Miller Electric Business Development Manager, Industrial Equipment Division Jason Dunahoo; and Fronius Senior Systems Engineer Steve Zatezalo all pointed to the skilled welder shortage—finding, training, and retaining welders—as the major challenge that the industry faces.
The lack of skilled welders results in productivity bottlenecks, poor quality, rework, and scrap, they said. Weld repeatability, quality assurance, and data recording/traceability are key.
Additional challenges include equipment failures and associated downtime, as well as managing large fleets of welding equipment.
The OEMs relayed how their power sources have evolved to help fabricators mitigate those challenges.
1. What challenges are fabricators currently faced with related to arc welding power sources?
Jason Dunahoo, Miller Electric Mfg.: One of the largest problems facing fabricators today are labor issues cascading into every aspect of business. In the welding department, the lack of skilled welders manifests as quality problems and reduced productivity, resulting in higher costs and lower profitability.
As technology evolves and the workforce changes, being able to adapt will be crucial for fabricators to stay competitive.
Jeff Chittim, ESAB.: The shortage of skilled welders remains one of the industry’s most pressing challenges, and even more so at a time when U.S. manufacturing is booming. The May Purchasing Managers’ Index is at 62.1, up from 43.1 in 2020.
As a result, fabricators need to select welding systems and technologies that help them increase output per worker and identify and remove waste from their production cycles. The bottom line is that you can’t improve what you can’t measure, so we recommend that fabricators start by understanding their true production metrics, such as arc-on time.
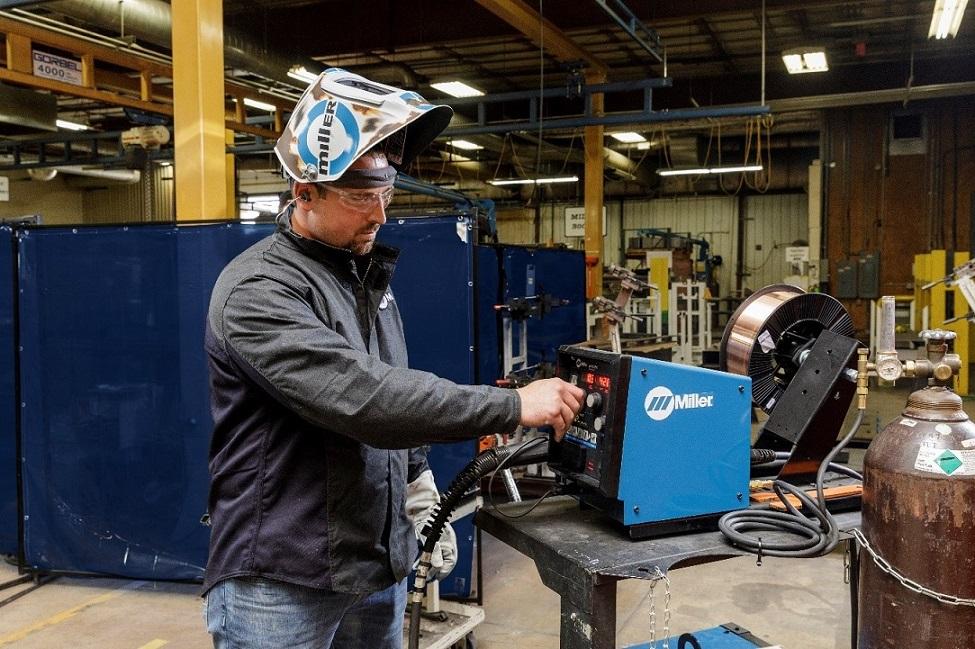
Deltaweld systems from Miller are available with Accu-Pulse technology and include EZ-Set technology, which simplifies parameter setup based on material thickness—removing complexity and reducing welder training time.
Managers typically estimate arc-on time at 25% or higher; the reality is that high-performing shops operate somewhere in the mid-teens, with an average shop at 8% to 10%. This discrepancy occurs when managers have limited visibility into the true sources of downtime or levers of productivity.
These metrics should be specific—per welding station, per shift, and for companies with multiple facilities, per shop; actual welding parameters; proof of compliance; wire consumption; and machine status.
Steve Zatezalo, Fronius: One of the biggest challenges is getting qualified welders. Not only is the current workforce getting older, but the younger generation is looking for a less laborious career. Experts are predicting a shortage of 400,000 skilled welders by 2024.
Related to this is the complexity and degree of difficulty of many fabrication jobs. It’s not enough to find someone who can weld; fab shops also need someone who is adaptive, intelligent, and creative enough to deal with the challenges of today’s welding environment.
Finally, a fear of technology exists among welders. Decision-makers aren’t as worried about the financial costs of newer equipment as they are that existing staff can’t or won’t use the new technology to take advantage of the features it offers. There is always a learning curve, and it’s hard for experienced welders to work through it if they feel that they can do the job well enough with the old machines—regardless of what the results show.
2. How are power sources/welding machines evolving to help meet these challenges?
Zatezalo, Fronius: We are seeing changes on three fronts. First, the welder interface is not only getting easier to use, it’s also able to define weld settings and procedures better. The displays allow for full text, pictures, and even videos. This really can make a difference in how the machine is ultimately used.
The second change we’re seeing is a heavier reliance on high-power, high-speed electronics. The welding arc is fast, and to modify the arc, you have to be faster than the arc. First, the welder has to detect the changes, then determine the best course of action, and finally put those actions into place. There have been massive changes to the core electronics technology in the last decade and integrated into the newer machines.
Third, software design is making a huge impact. Modern machines are taking an incredibly large number of inputs and drawing a picture of the welding arc from them. The software team must understand not only how to do the programming, but also the electronics’ capabilities and the physics of welding. The design of modern machines is only as good as the team is.
Chittim, ESAB: First, welding machines should be thought of in the context of a welding system. Nothing operates in isolation, and every component of the system contributes to productivity. To that note, one of the biggest advancements are welding power sources with communication modules that enable the power source to connect with online data management systems.
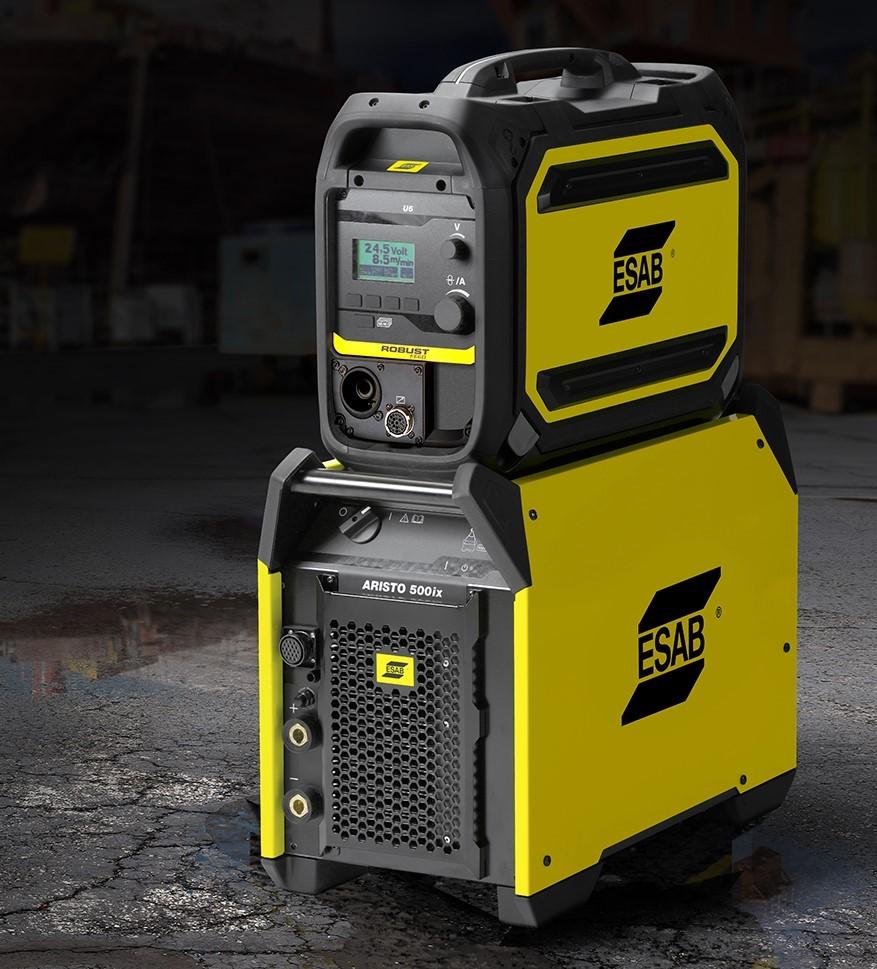
ESAB’s Aristo 500ix heavy industrial power source can connect to its WeldCloud suite of online data analytic applications via standard Wi-Fi. ESAB
If fabricators have fewer skilled welders, they need to use a more advanced control system to compensate. Advanced controls help operators focus on the fundamentals of good welding mechanics (gun angle, travel speed, manipulation, and contact-tip-to-work distance) and worry less about setting parameters and other technical details.
A first step toward consistent weld quality is linking production variables with results, such as weld quality monitoring systems. Even then, weld quality monitoring happens after a part is completed or sent down the production line. A quality assurance system based on looking in the rearview mirror is costly, especially if multiple parts have defects.
Conversely, a data monitoring system can provide the operator or manager with feedback in real time. Imagine the value of immediately identifying a weld flaw on the root pass of an inch-thick joint instead of after making the cap pass. On an automated system, the operator would be able to identify the location of a flaw on a large seam because travel speed would also be captured.
3. What have you developed with arc welding power sources that addresses these challenges.
Chittim, ESAB: ESAB’s heavy industries product series offers a host of controls that help fabricators improve weld quality, repeatability, and the welding skills of the available labor pool.
The WeldCloud Productivity app, created for production managers, improves welding productivity and traceability. It tracks arc-on time, net deposition rate, and travel speeds on each weld strike and session for each machine in a fleet and generates reports and analytic functionality. By providing visibility to actual production metrics, it can improve arc-on time by 10% to 50% during the first year.
For service and maintenance managers with large fleets of welding equipment, the WeldCloud Fleet app enables them to manage welding jobs across a fleet of equipment by viewing arc time per welding station; knowing the welding equipment’s locations via GPS; and getting support for planning, documenting, and providing reminders for service, maintenance, and calibration activities.
ESAB’s newest product with communication modules, launched in 2021, is the Aristo 500ix, a 500-amp advanced multiprocess power source for GMAW, pulsed GMAW, flux cored, lift GTAW, and carbon arc gouging. The power source, as well as other ESAB heavy industrial power sources equipped with a communication module, can connect to ESAB’s WeldCloud suite of online data analytic applications via standard Wi-Fi. These apps, which are easy to learn, intuitive to use, and work from any connected device, help fabricators address and remedy the key issues affecting the welding industry through digitization.
For any brand of welding equipment, the ESAB Universal Connector connects to the positive and negative terminals to capture basic data, including arc-on/-off time, weld session duration, and welding voltage and amperage.
ESAB achieves intelligence by pairing its industrial power sources—the Warrior CC/CV and advanced Aristo series—with a Robust Feed series wire feeder. All of the process intelligence is located at the wire feeder’s control panel.
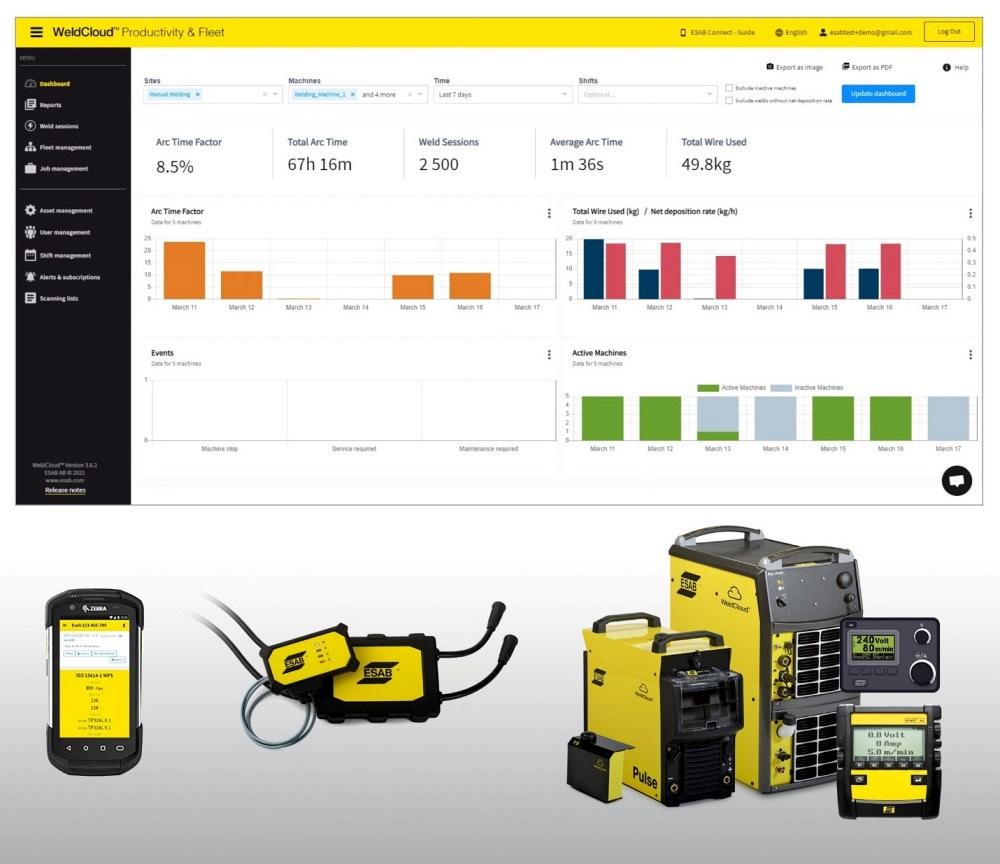
ESAB’s WeldCloud online data management applications help fabricators address and remedy the key issues affecting the welding industry through digitization. ESAB
Quality problems occur most frequently during arc starts and at the end of the weld. Advanced feeders address these problems through functions such as run-in speed control, crater fill, gas preflow and postflow, short-circuit termination, and burnback. Overall, advanced feeders help less experienced or moderately skilled welders produce better results and can transform good welders into great welders.
Run-in speed control (also called creep start) reduces the speed at which the wire approaches the plate, then ramps up to full welding speed when the system senses the arc is established. The additional time preheats the electrode, promotes a more positive arc start, reduces spatter, and promotes better fusion. Some feeders offer a hot-start function to increase total power for a few milliseconds during the start of the weld, which also helps prevent cold lap.
Wire feeders with a crater fill function ramp down parameters at the end of the weld to fill the crater at a lower wire feed speed and/or voltage level, which can prevent crater cracking and avoid melting the edges of the plate.
Gas preflow and postflow control enables the operator to set the duration of gas flow times. These functions are especially helpful in applications where gas coverage is critical, notably stainless steel.
Short-circuit termination technology sharpens the end of the solid GMAW wire at the termination of a weld to promote a positive next arc start, reduce spatter, and reduce the possibility of cold lap. SCT technology also eliminates the need for the operator to clip the wire. In an operation with numerous weld stops and starts, the time savings will quickly add up.
A burnback function controls the amount of wire that continues to feed after the operator releases the trigger, leaving an optimal wire stick-out so the operator does not need to clip the wire to length.
Very advanced feeders also offer additional functions that can immensely improve quality and consistency:
A limit function prevents the operator from welding with parameters outside of weld specifications, and a lock function prevents operators from altering the program. For example, a fabricator using an Aristo 500ix/Robust Feed U6 system could program operator access so that one setting is for spray, one for pulse, and two for gouging. This way welders can adjust the voltage and wire feed speed slightly but still stay within WPS parameters.
A function called QSet (“quick set”) automatically optimizes the short- circuit arc for the gas/wire combination installed. After a few seconds of welding, the system adapts welding parameters to match an operator’s individual welding style, notably compensating for variations in contact tip, work distance, and torch angle. This lets the operator focus on torch mechanics instead of worrying about whether they have set proper parameters.
Our preprogrammed synergic lines have optimized parameters for the wire type, wire diameter, shielding gas, and process selected. Operators can still fine-tune the arc by adjusting voltage/trim and amperage, but synergic lines get operators in the ballpark quickly, speeding setup. Synergic lines for pulsing MIG can save many hours of process development time.
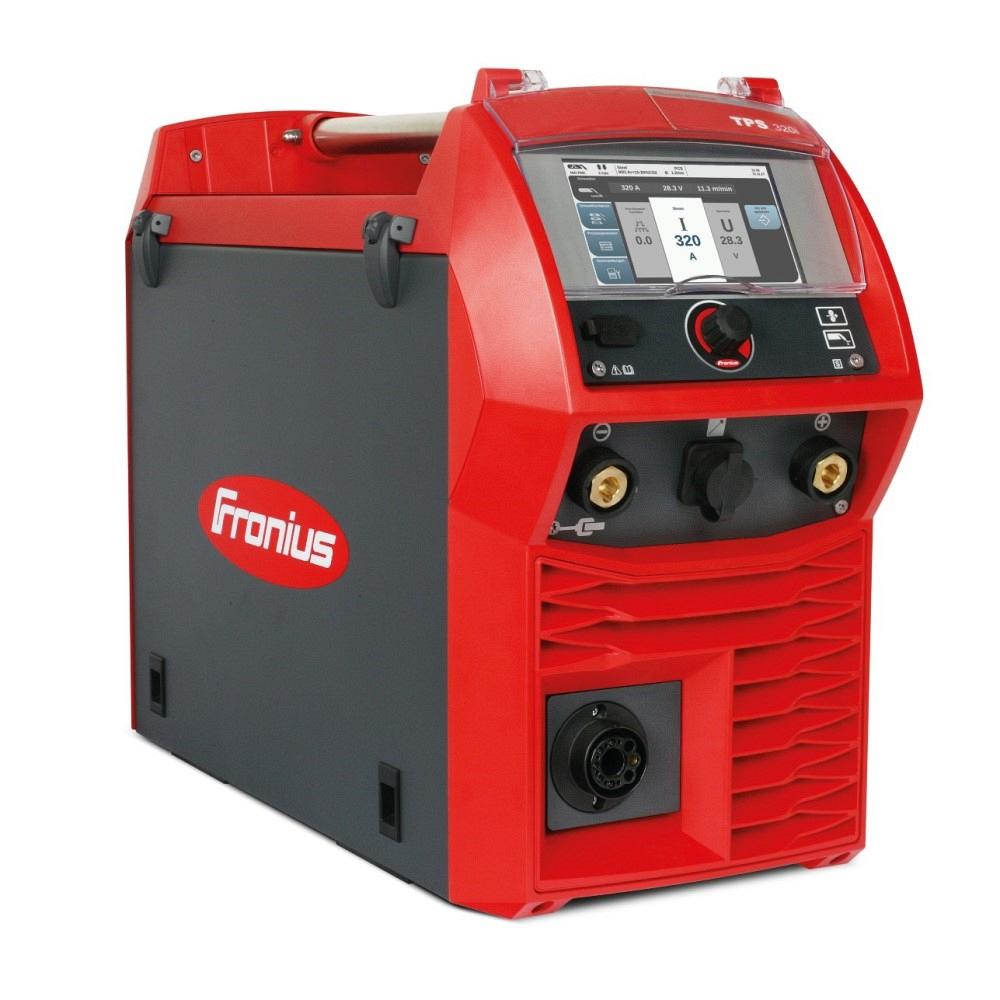
The WeldCube is Fronius’ data collection management system. WeldCube Premium, shown here, is a centralized documentation system with intelligent management, statistical, and analysis functions with graphical visualization of results. Fronius
Dunahoo, Miller: Miller Electric Mfg. LLC is evolving our welding systems to meet today’s skilled worker shortage challenge by exemplifying one of our core values: simplicity. When complexity is minimized and the user experience is simplified, operators are far less prone to execute quality errors from improper equipment configuration.
Miller EZ-Set technology helps operators find a good starting point for welding parameters without the need for hunting and testing welds.
For new-to-welding operators, maintaining proper stick-out and tip-to-work distance can be a challenge. Miller Accu-Pulse pulsed GMAW technology has a 28% wider operating window compared to typical GMAW. It can help transform new welders into more experienced welders quicker by getting them into production and producing quality welds faster.
Zatezalo, Fronius: First, we’re constantly pushing the envelope of what is possible in the electronic and welding world. Our design is focused to deliver an arc that is versatile, stable, and accurate, but also that will grow with the fabricator’s future needs. It doesn’t deter us that something has never been done before. We ask what is possible with electronics, software, and physics and deliver on it.
Take penetration as an example. Common wisdom suggests that if you move the welding torch, the penetration is likely to be uneven or lacking. We know what uneven penetration or lacking welds look like electronically. We took that idea and used our technology to ensure an even penetration even when it’s not conventionally possible.
Next, we’re conscious of the user experience. We ensure that the display/interface is clear for the user and comfortable to their experience level. Our system is designed to alter what the user sees not only for security, but also to allow them to grow with the machine. As they understand the technology, the machine allows more access to the settings, building comfort through experience.
Fronius provides multiple systems for fabricators looking to implement Industry 4.0 at their facilities. For example, WeldCube Premium is a centralized system that gathers welding data and then makes it available for third-party systems to analyze. We also offer decentralized solutions for directly collecting data from the welding equipment by implementing MQTT and OPC UA protocols in the welder to send the data directly to the company’s MES, ERP, or other third-party system for collection and analysis.
4. What are some current and critical developments you’re seeing?
Zatezalo, Fronius: Digital transformation and Industry 4.0 are transformative trends. Industry 4.0 isn’t a single piece of equipment or vendor collecting data but the gestalt of all vendors pooling the data from all the equipment responsible for producing the finished product. This helps the fabricator to fully understand and control its manufacturing process.
Manufacturers never want to see weld failures or quality issues, but if these do happen, they should be caught before they leave their floor. The shift is going from weld fault detection to the identification of the defect’s cause and rapid mitigation. This shifts production teams from reacting to an individual defect to ensuring defects don’t propagate. It is well established that part variations affect weld quality. Industry 4.0 pushes production lines to detect part variation before it even becomes a weld defect.
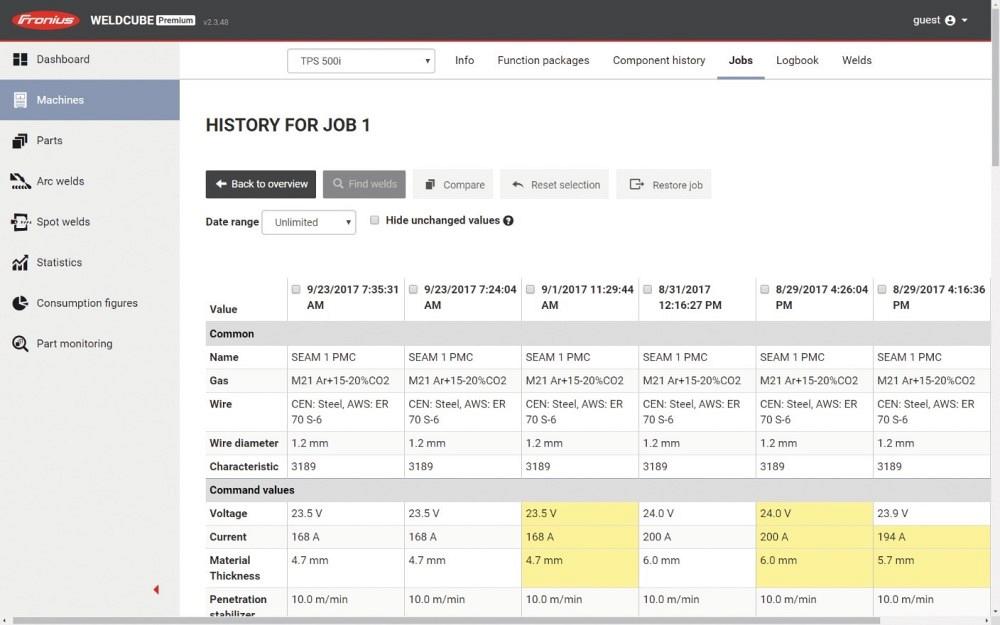
The WeldCube is Fronius’ data collection management system. WeldCube Premium, shown here, is a centralized documentation system with intelligent management, statistical, and analysis functions with graphical visualization of results. Fronius
No single technology by itself can determine the source of the defect; however, when data from the welding power supply, vision systems, stamping equipment, robots, and so forth, is combined, inconsistencies in manufacturing can be identified algorithmically. Traceability has been an important topic within Industry 4.0. This aids in detecting sources of defects before a large volume of defective parts are sent through production.
We don’t, however, think of the machine as a replacement for the welder. The welding power source should enhance the welder’s skill. The machine works hard to make the arc stable and accurate, allowing the user’s skill to produce an even better result. We’re not interested in a company replacing their skilled welders. We want our machines to make every welder better.
Chittim, ESAB: The WeldQAS quality assurance system from HKS, an ESAB brand, is an online data management system that can capture data at rates of 23 kHz and faster. By comparing measured parameters with reference curves, these systems can calculate quality marks for each weld seam and provide an instant notification when an irregularity occurs, thus providing real-time feedback. The type of faults that are detectable include poor arc ignition, porosity, burn-through, a too-short or too-long seam length, and seam interruption.
Dunahoo, Miller: As technology evolves and the workforce changes, being able to adapt is crucial for fabricators to stay competitive.
About the Author
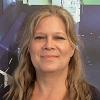
Kate Bachman
815-381-1302
Kate Bachman is a contributing editor for The FABRICATOR editor. Bachman has more than 20 years of experience as a writer and editor in the manufacturing and other industries.
Related Companies
subscribe now
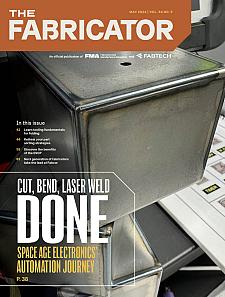
The Fabricator is North America's leading magazine for the metal forming and fabricating industry. The magazine delivers the news, technical articles, and case histories that enable fabricators to do their jobs more efficiently. The Fabricator has served the industry since 1970.
start your free subscription- Stay connected from anywhere
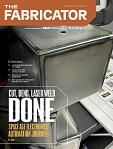
Easily access valuable industry resources now with full access to the digital edition of The Fabricator.
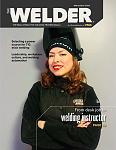
Easily access valuable industry resources now with full access to the digital edition of The Welder.
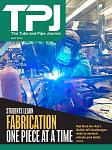
Easily access valuable industry resources now with full access to the digital edition of The Tube and Pipe Journal.
- Podcasting
- Podcast:
- The Fabricator Podcast
- Published:
- 04/16/2024
- Running Time:
- 63:29
In this episode of The Fabricator Podcast, Caleb Chamberlain, co-founder and CEO of OSH Cut, discusses his company’s...
- Trending Articles
Tips for creating sheet metal tubes with perforations
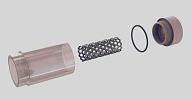
Are two heads better than one in fiber laser cutting?
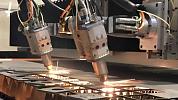
Supporting the metal fabricating industry through FMA
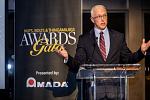
JM Steel triples capacity for solar energy projects at Pennsylvania facility
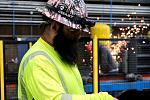
Omco Solar opens second Alabama manufacturing facility
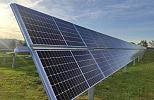
- Industry Events
16th Annual Safety Conference
- April 30 - May 1, 2024
- Elgin,
Pipe and Tube Conference
- May 21 - 22, 2024
- Omaha, NE
World-Class Roll Forming Workshop
- June 5 - 6, 2024
- Louisville, KY
Advanced Laser Application Workshop
- June 25 - 27, 2024
- Novi, MI